Brian Cox
Maintenance Manufacturing Manager at H&H Enterprises- Claim this Profile
Click to upgrade to our gold package
for the full feature experience.
Topline Score
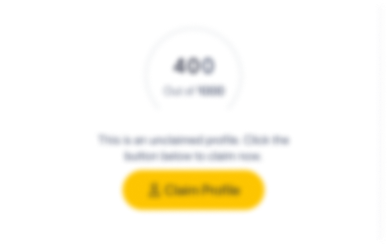
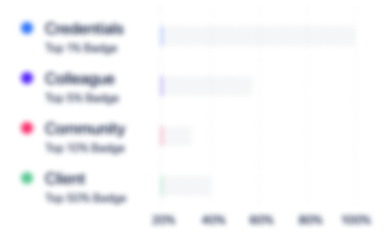
Bio


Experience
-
H&H Enterprises
-
Facilities Services
-
1 - 100 Employee
-
Maintenance Manufacturing Manager
-
May 2022 - Present
-
-
-
Clearwater Paper Corporation
-
United States
-
Paper and Forest Product Manufacturing
-
700 & Above Employee
-
Maintenance Supervisor/ Facilities Coordinator
-
Aug 2015 - Apr 2021
Responsible for coordinating process improvement and equipment reliability. Directed maintenance work prioritization including planning and execution. Reviewed the maintenance backlog and worked with maintenance planners to ensure equipment was functioning efficiently. Prepared facility operational maintenance and managed performance to meet budgeted overtime. Monitored the lines for safety violations. Organized, planned and scheduled downtime. Identified quality, production and cost improvement projects. Spent significant time on the plant floor to lead maintenance personnel in safety, quality and cost effective production utilizing checklists and accountability. Proficient in JDE workflow management. Initiated PM/SMP for nine converting lines. Facilities Coordinator included being responsible for the overall maintenance and operational functionality of the 850,000 sq ft facility, grounds and property. Served as site contact for all sub-contracted maintenance and repair services. Developed crane PMs and Dock door PMs.Notable accomplishments:• Spearheaded the effort to create strong awareness of safety with completed safety work orders on a monthly basis (improved by 48%). Set monthly goals and standardized weekly safety audits with maintenance employees. No injuries in 465+ days.• JDE Work Orders, progressively keeping the number of aged work orders at a low number.• Developed expectations for maintenance employees including daily checklists, standard work and documented sign-off training.• Built strong relationships with outside vendors to create efficient business transactions. Negotiated with vendors to give training classes for continuous improvement for maintenance employees.• Facilitated purchase at a lower cost of customized core mandrels for the rolled lines to run machines more efficiently. Resulted in a cost savings of $96,000/yr.• Unplanned maintenance for the year was 3.59% compared to a target of 3.75%, best in Clearwater Paper. Show less
-
-
Facilities Coordinator
-
Jan 2015 - Apr 2017
Responsible for the overall maintenance and operational functionality of the 300,000 sq ft facility, grounds and property. Served as site contact for all sub-contracted maintenance and repair services.Responsible for periodic (scheduled) assessments and inspections to ensure frequency of contracted service is sufficient for effective operations. Also, responsible for the contacting, monitoring and inspection of work performed by sub-contractors and for reporting any instance where performance/results have not met established standards. Show less
-
-
Process Engineer
-
May 2013 - Aug 2015
As Process Lead, I managed plant personnel and physical assets consistent with division and corporate goals and ensured that area goals of safety, quality and production were met. I managed the effort to produce or distribute safe, quality, low cost tons or cases at budgeted rates or better. Also, I lead and prioritized activities to maximize efficient use of limited resources and supplies. Always listened to employee’s safety concerns and addressed them promptly.Notable accomplishments:• Corporate cost savings – researched and negotiated purchase of wrapper sealer belts from vendor at lower cost. Cost savings was $105,000/yr between three Clearwater plants.• Upgraded Core machines with the Valco system on HHT2 and BRT2. Differences were more operator friendly, Production increase and less tonnage of core stock being wasted leading to a significant cost savings.• Facilitated purchase of core machine slitters for the rolled lines from LA Grinding out of California, which improves our lead-time, is a better quality and is only $8/slitter compared to $32/slitter previously. Cost savings of $24,000/yr.• Developed weekly cleanings improved processes and gave training.• Initiated training to provide employees correct JDE transactions and location detail for monitoring resources.• Monitored and ensured parts were available to keep downtime at a minimum.• Implemented standard work and documented sign-off training. Show less
-
-
Shift Manager
-
Jun 2011 - May 2013
In this position, I managed areas associated with shift employees on the converting and napkin lines including safety, quality and producing low cost cases. My strong qualities included organization, accountability, safety awareness and team communication. A large amount of my time was spent on the plant floor to lead personnel in safety, quality and cost effective production. I listened to employee’s safety concerns and addressed them promptly. High priority was to provide information and training on all safety policies and procedures to employees. I created training for improved work environment by listening to employee's concerns.Notable accomplishments:• Headed shift with zero safety incidents, highest production, most changeovers and least quality complaints. Achieved budget for one year.• Implemented use of centerlines on Futura rolled line.• Assessed the needs of the team members. Implemented developmental processes to continuously improve their performance and prepared them for future advancement. Show less
-
-
-
RR Donnelley
-
United States
-
Advertising Services
-
700 & Above Employee
-
Pressroom Supervisor
-
Jun 1992 - Jun 2011
While working for RR Donnelley, I ensured that production goals were met with safety as a priority, maintained quality standards per customer expectations, scheduled and sequenced jobs in manufacturing facility, coordinated crew in order to achieve production requirements, served as liaison between management, production, and customer service and provided communication of material delivery dates. While working for RR Donnelley, I ensured that production goals were met with safety as a priority, maintained quality standards per customer expectations, scheduled and sequenced jobs in manufacturing facility, coordinated crew in order to achieve production requirements, served as liaison between management, production, and customer service and provided communication of material delivery dates.
-
-
Education
-
Indiana University Southeast
Associate's degree, Business Administration and Management, General
Community
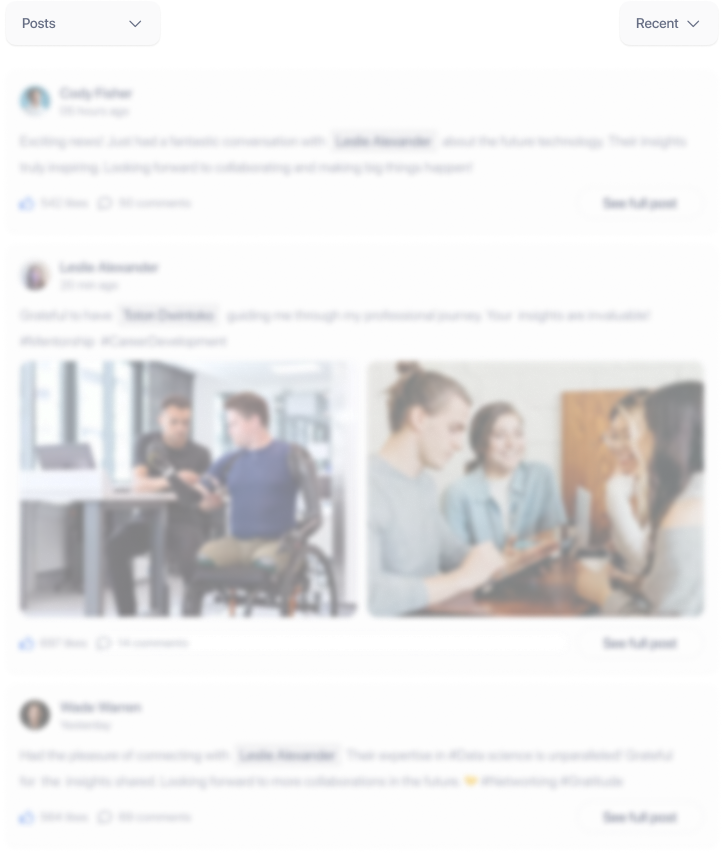