
Brian Borowiak
Program Manager at EPC- Claim this Profile
Click to upgrade to our gold package
for the full feature experience.
Topline Score
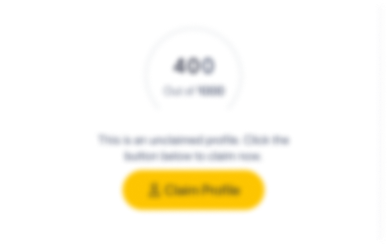
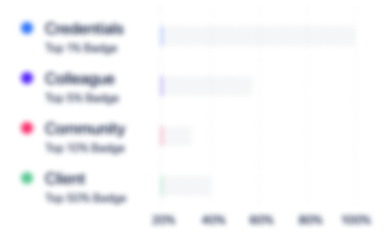
Bio


Experience
-
-
Program Manager
-
Mar 2008 - Present
(Automotive Connector business for Heavy Truck and Light vehicle. Freightliner,Paccar,Ford Fusion, Hummer)Sr. Program ManagerWork with APQP team on new project launch readiness.Utilized Six Sigma / RGJ Systematic Molding training for problem solving.Successful in setting up DOE / MSE by using the Six Sigma philosophy, which aided in product being more cost efficient for both Alcoa and Customer.Coordinated with Vendors (Tool shops, sampling houses and Machine… (Automotive Connector business for Heavy Truck and Light vehicle. Freightliner,Paccar,Ford Fusion, Hummer)Sr. Program ManagerWork with APQP team on new project launch readiness.Utilized Six Sigma / RGJ Systematic Molding training for problem solving.Successful in setting up DOE / MSE by using the Six Sigma philosophy, which aided in product being more cost efficient for both Alcoa and Customer.Coordinated with Vendors (Tool shops, sampling houses and Machine Fabricators) to verify project timing and budget cost.Worked with Plant Quality Manager and Quality Technicians to help in maintaining TS quality system.Worked directly with Ford through the SREA process in transferring tools to Mexixo.Worked directly with Chrysler through Forever Requirements process in transferring tools to Mexico.Accomplishments:Successfully launched the following platforms PACCAR (Heavy duty Truck), Light Duty Truck (P473 Light Vehicle) this involved a 45-injection molding tools, Automation equipment, Robots. Program were on time and with in budget.Successfully coordinated a 30-tool transfer from Alcoa Mattawan facility to Juarez Mexico facility Successfully coordinated a 25-tool transfer form AEES China Facility to Mattawan Facility.Successfully coordinated a Facility shut down which included the transfer of 750 tools, 85 IMM and 61 assembly machines to our Torreon and Juarez facilities.Involved in a Change control console which targets cost savings in the plant. Which resulted in cost saving of savings of $500,000. (Savings areas material)In using Six Sigma and RGJ philosophy to help gain the optimal process for new program launches. Show more Show less
-
-
-
-
Progam Manager
-
2011 - 20143 years
-
-
-
-
Engineering Manager
-
Aug 2005 - Dec 2007
(Automotive, Furniture, & Medical / Injection Molding & Assembly / Saturn Auro, Chevrolet Malibu, &Chrysler Sebring)Engineering ManagerCoordinated the design of molded parts from prototype stage to production, which included setting up APQP format.Served as a primary contact for customer needs.Work with Quality Manager to redevelop Quality system to be ready for TS certification.Work with Operations Manager to restructuring the plant floor to reduce labor… (Automotive, Furniture, & Medical / Injection Molding & Assembly / Saturn Auro, Chevrolet Malibu, &Chrysler Sebring)Engineering ManagerCoordinated the design of molded parts from prototype stage to production, which included setting up APQP format.Served as a primary contact for customer needs.Work with Quality Manager to redevelop Quality system to be ready for TS certification.Work with Operations Manager to restructuring the plant floor to reduce labor and increase productivity by 25% through automation. Coordinated with the customer on part and tool design through the use of APQP format. (Control plans. Red Line drawings, flow diagrams, work instructions, and PPAP submission package.Supervised 5 indirect personnel, to include: 3-Process Technicians, 1-Tool Supervisor, and 1-Maintenance Supervisor.Worked with Quality manage to redevelop quality system to be ready for TS certification.Trained all Quality technicians on company SOP. Trained all Process Technicians on the use automation equipment. Trained all material handlers on use of material handling equipment.Accomplishment:Work with Operations Manager to implement the use of robots, sprue pickers and material handling equipment (Wittmann, Husky, AEC) which increased productivity by 25% and reduced scrap by 10%.Met all customer expectations on time and within budget.Used RJG format along with six-sigma philosophy to show customer a potential design issues with resulted in a .75 cent/ part reduction. Show more Show less
-
-
-
-
Sr. Project Engineer
-
Aug 2002 - Jul 2005
Worked with tool shops and sampling houses to verify project timing.Work with the plants on APQP and project launch.Utilized Six Sigma / RGJ Systematic Molding training for problem solving.Successful in setting up DOE / MSE by using the Six Sigma philosophy, which aided in product being more cost efficient for both Titan and Customer.Coordinated with the customer and Titan plants on part and tool design through the use of APQP format. (Control plans. Red Line drawings, flow… Worked with tool shops and sampling houses to verify project timing.Work with the plants on APQP and project launch.Utilized Six Sigma / RGJ Systematic Molding training for problem solving.Successful in setting up DOE / MSE by using the Six Sigma philosophy, which aided in product being more cost efficient for both Titan and Customer.Coordinated with the customer and Titan plants on part and tool design through the use of APQP format. (Control plans. Red Line drawings, flow diagrams, work instructions and PPAP submission package)Coordinated with Vendors (Tool shops, sampling houses and Machine Fabricators) to verify project timing and budget cost.Worked with Plant Quality Manager and Quality Technicians to help in maintaining QS 9000 quality system.Work with Operations Manager to implement a budget cost on equipment needed to product launch.Supervised 2 direct personnel (2 Project Engineers)Successful in setting up DOE / MSE by using the Six Sigma philosophy along with RGJ which aided in product being more cost efficient for both Titan and Customer.Accomplishments:Launched a 38-tool program for Dodge Durango in Monterrey Mexico on time and within budget.Successfully coordinated a 60-tool transfer for Monterrey Mexico plant to Charlotte MI facility.In using Six Sigma and RGJ philosophy we were able to reduce the over all door cost in the HVAC for the Durango by .12 cents per door.Reason for leaving: Company Cutbacks. Show more Show less
-
-
-
-
Operations Manager
-
Aug 1999 - Jul 2002
Automotive / /Injection molding, Assembly, & Machining)Operations MangerOversaw the engineering department and Quality department on part and tool design through the use of APQP format. (Control plans, flow diagrams, work instructions and PPAP submission package)Supervised personnel: Engineering Manager, Quality Manger, & Shipping Manager.Redesigned and put forth a quoting program to in the control of product cost.Aided in preparing the Quality System for ISO… Automotive / /Injection molding, Assembly, & Machining)Operations MangerOversaw the engineering department and Quality department on part and tool design through the use of APQP format. (Control plans, flow diagrams, work instructions and PPAP submission package)Supervised personnel: Engineering Manager, Quality Manger, & Shipping Manager.Redesigned and put forth a quoting program to in the control of product cost.Aided in preparing the Quality System for ISO CertificationAccomplishments:Establish a JIT system - reduced inventory by 25%.Restructured plant floor - reduced labor cost and increased productivity by 30%·Reason for leaving: Better opportunity presented itself. Show more Show less
-
-
-
-
Sr. Project Engineer
-
Apr 1994 - Jul 1999
Automotive / Injection molding, Assembly, Machining / Cruse, break cables for; Coordinated the design of molded parts from prototype stage to production, which included setting up APQP, Sampling and PPAP submission paperwork.Served as a primary contact for a customer base of 10, with 5 being Tier 2 automotive suppliers to GM, Chrysler, Ford, Honda, and ToyotaExpedition of Molds and / or fixtures through the tool shops.Successful in setting up programs by using Microsoft office to… Automotive / Injection molding, Assembly, Machining / Cruse, break cables for; Coordinated the design of molded parts from prototype stage to production, which included setting up APQP, Sampling and PPAP submission paperwork.Served as a primary contact for a customer base of 10, with 5 being Tier 2 automotive suppliers to GM, Chrysler, Ford, Honda, and ToyotaExpedition of Molds and / or fixtures through the tool shops.Successful in setting up programs by using Microsoft office to help make engineering more efficientInvolved in setting up SOP's to aid in getting ISO approval status.Troubleshoot customer problems by part design, tool design, either at their pant or at GLM Coordinated with the customer on part and tool design through the use of APQP format. (Control plans. flow diagrams, work instructions and PPAP submission package)· Coordinated with Vendors (Tool shops, sampling houses and Machine Fabricators) to verify project timing and budget cost.Worked with Plant Quality Manager and Quality Technicians to help in maintaining ISO 9000 quality system.Work with Operations Manager to implement a budget cost on equipment needed for product launch.Accomplishments:Establish a good relationship with customer resulting in being main contact with 5 Tier 2 automotive suppliers to GM, Chrysler, Ford, Honda, and Toyota.Successful in setting up programs by using Microsoft office to help make engineering more efficient.Establishing SOP's to aid in getting ISO approval status.Reason for leaving: Plant closing. Show more Show less
-
-
-
-
Project Engineer
-
Jul 1988 - Feb 1994
Plastic Injection, Die Cast and Thermoforming molding / Injection Molding Machines & Die Cast machining); Coordinated with the customer tool design through AutoCAD.Coordinated with Vendors to verify project timing and budget cost.Work with Operations Manager to implement a budget cost on equipment and tools need to complete tool design.Accomplishments: Successful in setting up engineering department with AutoCAD.Met all customer expectations on time and under… Plastic Injection, Die Cast and Thermoforming molding / Injection Molding Machines & Die Cast machining); Coordinated with the customer tool design through AutoCAD.Coordinated with Vendors to verify project timing and budget cost.Work with Operations Manager to implement a budget cost on equipment and tools need to complete tool design.Accomplishments: Successful in setting up engineering department with AutoCAD.Met all customer expectations on time and under budget.Reason for leaving: Plant closing. Show more Show less
-
-
-
-
Tool/Design Engineer
-
Apr 1983 - Jul 1988
Plastic Injection and Die Cast / Injection molding Machines & Die Cast machining)Tool /Design Engineer Coordinated with Vendors to verify project timing and budget cost.Work with Tool room manager to implement a budget cost on equipment and tools need to complete tool construction.Accomplishments:Met all customer expectations on time and under budget.Reason for leaving: Plant closing.
-
-
Education
-
ITT TECHNICAL INSTITUTE
Community
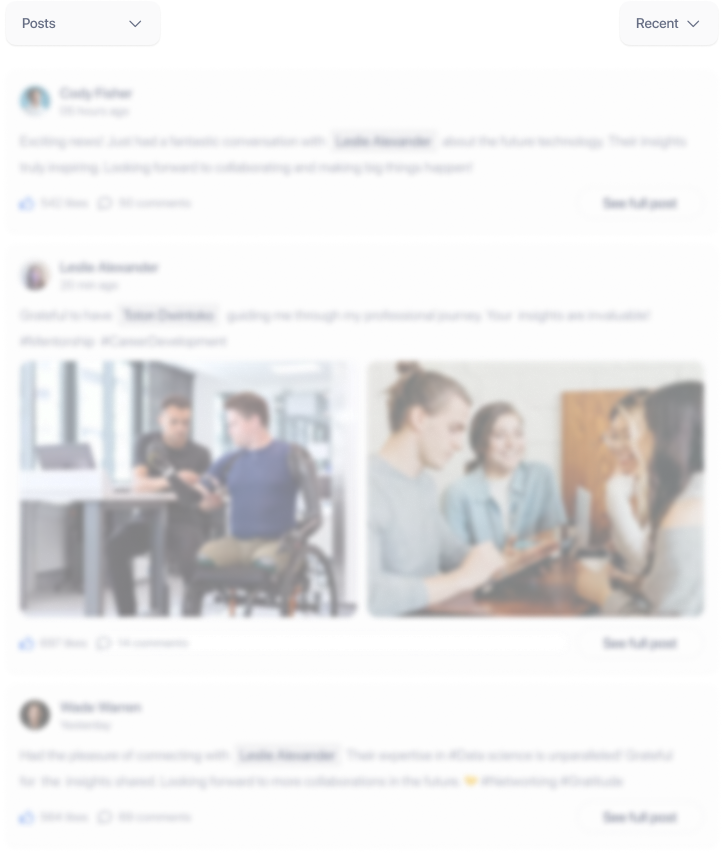