Brett Lewis
Electrotechnical Maintenance at GE Additive- Claim this Profile
Click to upgrade to our gold package
for the full feature experience.
Topline Score
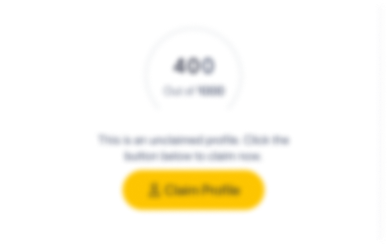
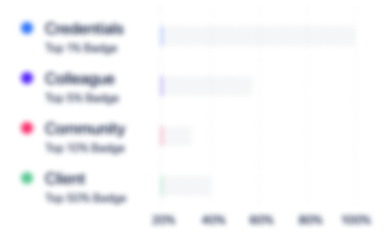
Bio


Experience
-
GE Additive
-
United States
-
Machinery Manufacturing
-
300 - 400 Employee
-
Electrotechnical Maintenance
-
Mar 2019 - Present
-
-
-
Boral
-
Australia
-
Construction
-
700 & Above Employee
-
Maintenance Lead
-
Jun 2018 - Mar 2019
-
-
-
Patheon
-
United States
-
Pharmaceutical Manufacturing
-
700 & Above Employee
-
Maintenance
-
Oct 2015 - Jun 2018
-
-
-
Metal Coaters
-
United States
-
Manufacturing
-
1 - 100 Employee
-
Maintenance Electrician
-
Oct 2014 - Jul 2015
Responsible for safely performing emergency and preventative repairs to plant machinery and infrastructure and minimizing production time losses associated with the breakdown or failure of production equipment. Responsible for the day-to-day administration of a Preventative Maintenance Program designed to establish reliability of production equipment and infrastructure. Responsible for the day-to-day administration of a Work Order System designed to establish priority and control over maintenance request from production personnel. Ensures that Work Oder (Maintenance) request are fulfilled in a timely fashion. Ensures a safe work environment by utilizing Lock-out/Tag-out procedures and reporting any unsafe condition. Responsible for the inventory of maintenance supplies. Informs the Maintenance Supervisor when supplies have been removed from stock and require replenishment. Provides ordering information for replenishment of stock. Responsible for utilizing the Work Order system both in entering work orders and completing work orders, as directed by the Maintenance Supervisor. Communicates daily with internal personnel from Production and Quality Control in order to assist in resolving problems and achieving company goals. Responsible for follow-up review of completed maintenance tasks to ensure that work is completed properly and in a safe and timely manner. Show less
-
-
-
-
Warehouse
-
Jan 2012 - Jul 2014
Monitor and maintain database on all incoming and outgoing shipments. Review all shipping documentation, such as bills of lading, invoices, and orders, to ensure proper labeling and accurate annotation. Oversee and ensure accountability of storage area containing shipping materials and supplies. Conduct regular inventory to identify depleted supplies and collaborate with external units to requisition additional materials. Operate equipment, including forklifts and bridge cranes to facilitate receiving, storage, and shipment of inventory. Conduct recurring inspections of vehicles and equipment in accordance with company policy and manufacturers’ requirements. Use Computerized Maintenance Management System to input preventive and corrective maintenance performed, to generate work orders and requisitions for repair parts, and to input general logs to record actions performed during each shift. Recognized need for, developed, and implemented fall protection system for personnel working at heights while transferring heavy objects; new system resulted in significantly improved safety. Show less
-
-
Melt Shop Electrician
-
Nov 2009 - Jan 2012
Received and responded to requests for assistance as sole Electrician on shift. Utilized ABB PLC's to maintain and troubleshoot Melt Shop equipment. Performed weekly and monthly safety inspections on bridge crane. Checked bridge and trolley brakes and couplings, magnet cables, festoon and crane cabling, deadman operations, hot rail collector shoe condition, function and travel of all hoists, and crane Motor Control Center. Planned and executed preventive and restorative maintenance on Electric Arc Furnace as well as corresponding mechanical, hydraulic, and pneumatic systems. Maintained and programmed Kuka Robot. Devised safety lockout system to prevent movement of liquid steel ladles while filling; achieved no safety incidents since system implementation while incurring no cost to the organization. Show less
-
-
Education
-
Thomas Edison State College
Bachelor’s Degree, Nuclear Engineering Technology/Technician
Community
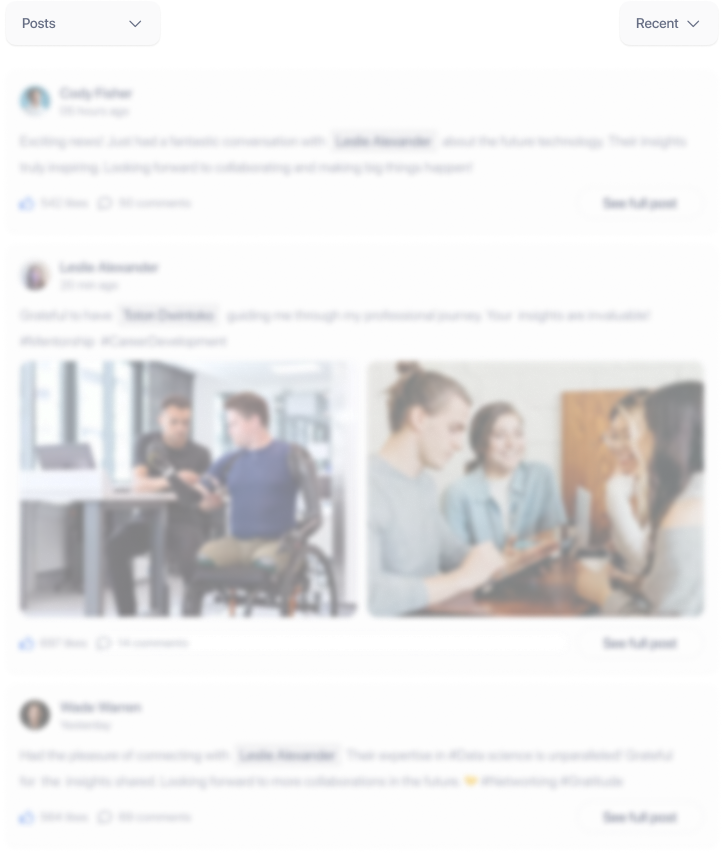