Bret Hartzell
Co-Owner and Consultant at Stenbu Design and Development LLC- Claim this Profile
Click to upgrade to our gold package
for the full feature experience.
Topline Score
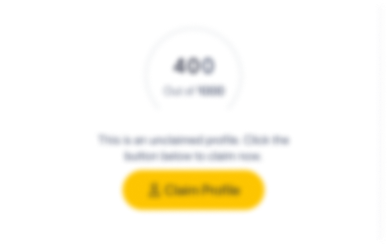
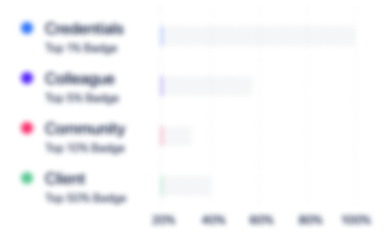
Bio


Experience
-
Stenbu Design and Development LLC
-
United States
-
Medical Equipment Manufacturing
-
1 - 100 Employee
-
Co-Owner and Consultant
-
Feb 2017 - Present
Collaborative Team Partner providing a diverse experience background in service areas of: • Product Design & Development • Cost Reduction • Design for Manufacturability • Technical Analysis • Project Management • V&V / Risk Management • Legacy Product Maintenance & Remediation Collaborative Team Partner providing a diverse experience background in service areas of: • Product Design & Development • Cost Reduction • Design for Manufacturability • Technical Analysis • Project Management • V&V / Risk Management • Legacy Product Maintenance & Remediation
-
-
-
Sole Proprietor (Orthopedics)
-
Canal Fulton, OH
-
Consultant
-
May 2016 - Jan 2017
• Contract consulting work in orthopedics, primarily focused on test protocols and reports, design history documentation. • Contract consulting work in orthopedics, primarily focused on test protocols and reports, design history documentation.
-
-
-
Career Sabbatical
-
Canal Fulton, OH
-
Career Sabbatical
-
Dec 2015 - May 2016
• A purposeful decision made to step back, reflect, find balance and refocus on the importance of life and family. • This experience changed my life and made me get back to the basics. An engineer’s mind never stops problem solving and designing. Working on our small farm during this time reminded me the value of not overcomplicating solutions, utilizing the resources I already had and spurred creativity in a cost-effective manner. • A purposeful decision made to step back, reflect, find balance and refocus on the importance of life and family. • This experience changed my life and made me get back to the basics. An engineer’s mind never stops problem solving and designing. Working on our small farm during this time reminded me the value of not overcomplicating solutions, utilizing the resources I already had and spurred creativity in a cost-effective manner.
-
-
-
NextStep Arthropedix
-
United States
-
Medical Equipment Manufacturing
-
1 - 100 Employee
-
Director of Product Development
-
Oct 2014 - Dec 2015
• Director of Product Development for a hip project at an orthopedic start-up company. • Managed 3 direct reports on the team which were primarily responsible for the development and validation of the instrumentation of a THA press-fit hip system. • Maintained the project timelines for the system and advised on implant and instrument development, prototyping, cost reduction and process improvements. • Director of Product Development for a hip project at an orthopedic start-up company. • Managed 3 direct reports on the team which were primarily responsible for the development and validation of the instrumentation of a THA press-fit hip system. • Maintained the project timelines for the system and advised on implant and instrument development, prototyping, cost reduction and process improvements.
-
-
-
Cleveland Clinic
-
United States
-
Hospitals and Health Care
-
700 & Above Employee
-
Senior Principal Research Engineer
-
Jun 2012 - Oct 2014
• Started new function (Center for Musculoskeletal Innovations) at Cleveland Clinic to encourage entrepreneurship amongst staff members by translating surgeon ideas into marketable technologies • Developed processes, tools, and templates to facilitate development of ideas from surgeon concept to licensable product/technology • Established relationships and built trust with community of over 100 surgeons, fellows, and residents to enable collaborations and idea generation • Managed over 70 new Orthopaedic and Rheumatology Institute invention disclosures through all aspects of the business development process including: o Prepared prior art searches for each technology o Drafted and submitted invention disclosures of new inventions for inventors o Develop 3D models of new technologies and products using Creo 2.0 (formerly ProE) o Collaborated with inventors through design iterations to reduce invention to practice o Conducted market analyses to determine competitive landscape, cost trends, and potential licensing partners o Prepared Product Development Fund applications and oversaw prototype production • Resulted in 8 patent applications (listed as inventor on 5 of these), 1 license agreement, 1 co-development agreement, and 3 additional technologies under licensing discussions Show less
-
-
-
Integra LifeSciences
-
United States
-
Medical Equipment Manufacturing
-
700 & Above Employee
-
Engineering Manager, Interbody
-
Aug 2011 - Jun 2012
• Engineering Manager, Product Development Engineer and Project Manager for spine interbody projects• Managed 5 direct reports on the team (located in 2 different locations) which maintained 13 existing product families and had the company’s top 3 active projects• Launched a Stand-alone ALIF interbody system.• Conducted investigations and engineering assessments of customer complaints
-
-
Engineering Team Leader, Interbody
-
Dec 2009 - Aug 2011
• Team Leader, Product Development Engineer and Project Manager for spine interbody projects• Managed 4 direct reports on the team which maintained 5 existing product families and had 7 active projects• Utilized creative approaches for rapid functional prototype production for verification/validation activities.• Development of implants, instruments, sterilization cases and post-launch systems improvements
-
-
Product Development Engineer
-
Mar 2008 - Dec 2009
• Product Development Engineer and Project Manager for spine interbody projects• Launched an ALIF interbody system and disc prep instrumentation and implemented on-going system improvements in PLIF and TILF released systems• Development of implants, instruments, sterilization cases and post-launch systems improvements
-
-
-
Orchid Orthopedic Solutions
-
United States
-
Medical Equipment Manufacturing
-
500 - 600 Employee
-
Engineering and Process Development Manager
-
Sep 2007 - Mar 2008
• Oversaw the daily activities of 8 direct reports including scheduling, die design, fabrication, and verification.• Improved die creation system to supply dies and fixtures to a rapidly increasing production demand.• Led customer issue resolutions and process improvement in the areas of scrap reduction. • Managed 5S implementation activities of Tooling Dept.
-
-
New Project Manager
-
May 2006 - Sep 2007
• Created and implemented a New Project Implementation Procedure and supporting documentation templates. Procedure was highly regarded by the ISO 13485 registrar and helped in gaining certification in 2007.• Managed new projects from quoting through production including process documentation, project plans, manufacturability / GD&T review, quality requirements, customer updates and troubleshooting. Over 125 new forging part numbers during this role.• Participated in Kaizen events and 5S implementation in support of the company’s conversion to lean manufacturing. Show less
-
-
-
Exactech
-
United States
-
Medical Equipment Manufacturing
-
700 & Above Employee
-
Product Development Engineer
-
Aug 2004 - May 2006
• Product Development Engineer and Project Manager for multiple hip and knee orthopedics projects• Launched a THA press-fit hip system and significantly contributed to the launch of a THA cemented hip system.• Development of implants, instruments, sterilization cases and post-launch systems improvements
-
-
Product Design Engineer
-
Jun 2003 - Aug 2004
• Product Design Engineer and Project Manager for multiple knee orthopedics projects• Significantly contributed to the launch of a unicondylar knee system.• Designed multiple TKA instrument enhancements in areas of ligament balancing, posterior referencing guides, and initial phases of MIS.• Additional skills highlighted from this experience: Design History documentation, legacy system maintenance, instrument refurbishment
-
-
-
Kentucky Department of Vocational Rehabilitation (Assistive Technology)
-
Louisville, Kentucky
-
Rehabilitation Engineer
-
Jul 2000 - Aug 2001
Performed client evaluation testing and reported technological recommendations to respective supervising counselor; administered $250,000 of statewide $1.2 million Rehabilitation Technology budget for Louisville and surrounding cities. • Significantly reduced budget expenditure with introduction of in-house design and fabrication. • Evaluation areas included ergonomic assessments, home and workplace modifications, and custom assistive technology. Performed client evaluation testing and reported technological recommendations to respective supervising counselor; administered $250,000 of statewide $1.2 million Rehabilitation Technology budget for Louisville and surrounding cities. • Significantly reduced budget expenditure with introduction of in-house design and fabrication. • Evaluation areas included ergonomic assessments, home and workplace modifications, and custom assistive technology.
-
-
Education
-
Wright State University
Master’s Degree, Biomedical Engineering -
Wright State University
Bachelor’s Degree, Biomedical Engineering
Community
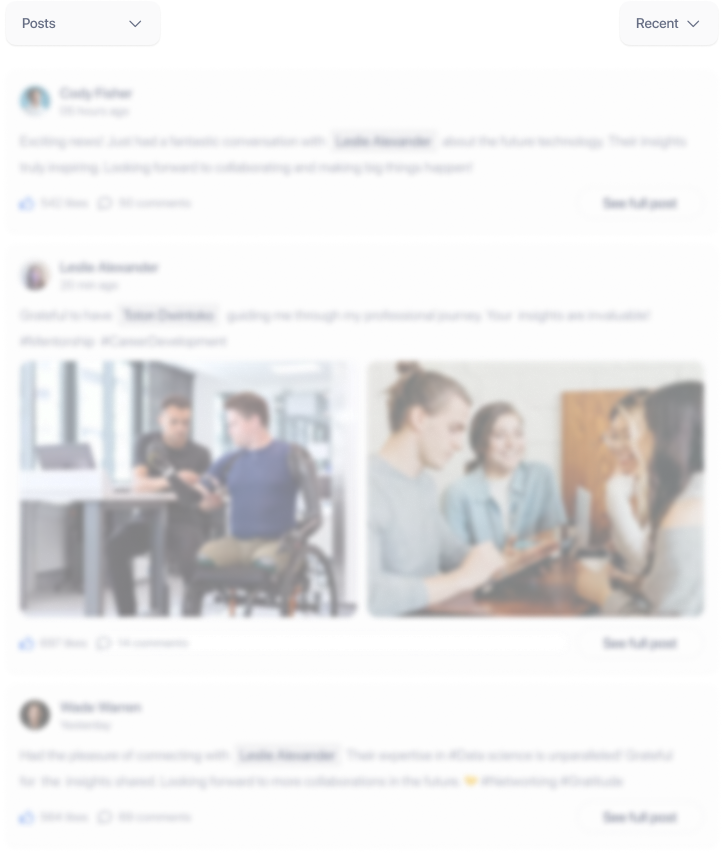