Bradley Stroka
Quality Manager at C-P Flexible Packaging- Claim this Profile
Click to upgrade to our gold package
for the full feature experience.
Topline Score
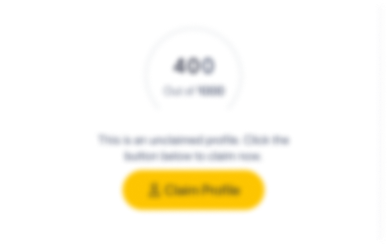
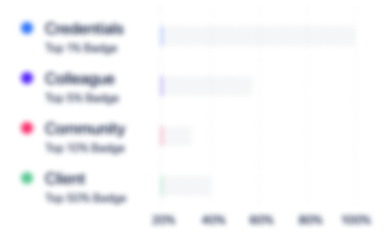
Bio


Credentials
-
HACCP Plan Development
HydriteMay, 2022- Nov, 2024 -
ISO 14001:2015 Internal Auditor
University at BuffaloMay, 2017- Nov, 2024 -
ISO 9001:2015 Internal Auditor
University at BuffaloMay, 2017- Nov, 2024 -
OHSAS 18001:2007 Internal Auditor
University at BuffaloMay, 2017- Nov, 2024 -
AS9100 Rev D Training
Bureau Veritas GroupMar, 2017- Nov, 2024 -
Oxygen Hazards & Fire Risk Analysis – Level 4
WHA International, Inc.Mar, 2017- Nov, 2024 -
Key Person Leadership Development Program
University at Buffalo School of Management, The State University of New YorkDec, 2013- Nov, 2024 -
Supervisory Skills
University at Buffalo School of Management, The State University of New YorkDec, 2012- Nov, 2024 -
Knowledge-Driven New Product Development
University at BuffaloNov, 2012- Nov, 2024
Experience
-
C-P Flexible Packaging
-
United States
-
Packaging & Containers
-
100 - 200 Employee
-
Quality Manager
-
Jun 2021 - Present
- Managed Quality department comprised of Quality Supervisor and three Quality Technicians across three shifts. - Maintained AIB GMP and BRC Food Safety programs across multiple sites (Buffalo, NY; Fond du Lac, WI; Lakeville, MN). - Traveled to Fond du Lac and Lakeville sites to lead annual external audits. - Developed Gemba Walk, GMP, Quality Compliance, and Behavior Based Safety (BBS) audit programs to identify and address compliance gaps with all personnel. - Implemented QCBD Quality Management system to centralize all customer claim, internal hold, and Corrective Action data. - Updated site policies and procedures in preparation for BRC Food Safety program certification. - Conducted quality and food safety training for all employees. - Coordinated all activities related to customer claims, including customer communications, containment, product evaluation, and Corrective Action requests. - Worked closely with Production Supervisors and Operators to troubleshoot product defects and implement Corrective Actions. - Reviewed non-conforming materials to recommend disposition based on internal and customer specifications. - Generated and analyzed weekly performance reports (Customer Credits, Internal Discards, Quality Compliance) to distribute to local management and corporate VP of Quality. Show less
-
-
-
HDM Hydraulics, a Ligon Company
-
Machinery Manufacturing
-
1 - 100 Employee
-
Quality Manager
-
Aug 2020 - Jun 2021
- Managed Quality department comprised of Quality Technician and Warranty Coordinator. - Organized Material Review Board (MRB) meeting to ensure timely review of all non-conforming materials on a daily basis by all Production supervisors and Quality personnel. - Designed and implemented new Return Material Authorization (RMA) tracking system to improve visibility of workload distribution and enable accurate reporting of daily and monthly metrics. - Acted as the primary point-of-contact for all customer rejections, coordinated internal containment activities, and managed responses to customers including Corrective Action Requests. - Created and presented Root Cause Analysis and Corrective Action training program to all Production supervisors to improve process effectiveness. Show less
-
-
-
Safran
-
France
-
Aviation and Aerospace Component Manufacturing
-
700 & Above Employee
-
Quality Manager (AVOX Systems)
-
Jul 2018 - May 2020
- Managed Quality Assurance department comprised of Audit Manager, Auditor, Program Quality Engineer, and Administrative Assistant.- Responsible for training, mentoring, and performance management of all direct reports, as well as supporting all site Quality personnel.- Designed and implemented Cost of Quality metric to identify improvement opportunities and drive cost reductions- Responded to and resolved customer complaints and rejections, including coordinating activities for completing Corrective Action reports.- Managed all major investigations into product failures and escapes, including customer Notice of Escapes and disclosures to the Federal Aviation Administration (FAA).- Completed and submitted monthly reports to local and corporate management to summarize Quality metrics, including Quality escape parts per million (PPM) and supplier performance.- Maintained AS9100 quality management system to ensure compliance to regulatory, customer, and industry standards, including surveillance and re-certification audits from all customers and registrars.- Designed and implemented new Customer Scorecard to improve tracking and analysis of customer satisfaction for both Quality and On-Time Delivery.- Organized and managed weekly site meeting to establish and track action plans to resolve all major customer and supplier quality issues, including representation from all supporting departments and product Value Streams. Show less
-
-
Quality Engineer (AVOX Systems)
-
Jun 2016 - Jul 2018
- Evaluated and dispositioned non-conforming materials and assemblies at Receiving Inspection, during the assembly process, and for customer returns.- Issued, reviewed, and approved supplier Corrective Actions for non-conforming materials.- Reviewed and approved AS9102 First Article Inspection reports for incoming and outgoing product.- Performed product line spot audits and internal quality management system audits in accordance with audit schedule.- Coordinated cross-functional Process Failure Mode and Effects Analysis (PFMEA) meetings to identify and mitigate risks on multiple regulator assembly lines.- Initiated project to define and implement new Return Material Authorization (RMA) process to manage customer returns; reduced overall process time, improved communication between process stakeholders, implemented system into ERP software, and improved data analysis capabilities. Show less
-
-
-
Switzer
-
United States
-
Appliances, Electrical, and Electronics Manufacturing
-
1 - 100 Employee
-
Quality Engineer
-
Jan 2016 - Jun 2016
- Managed Quality Assurance department comprised of Quality Technicians responsible for dimensional sampling of all outgoing product.- Maintained ISO 9001:2008 quality system, including document management and Corrective/Preventative Actions.- Led cross-department teams for two core 2016 initiatives; redefining all manufacturing procedures and establishing a fully integrated quality system across both manufacturing facilities.
-
-
Engineer 2
-
Nov 2014 - Jan 2016
- Performed process capability studies and statistical analysis to ensure compliance to customer specifications.- Created Value Stream Map of all manufacturing processes to identify bottlenecks and improve process efficiency.
-
-
Engineering Manager
-
Sep 2012 - Nov 2014
- Managed Engineering department comprised of cost estimating, tooling generation, and Chemical Engineering functions.- Established and maintained baseline process capabilities and throughput for all steps of the photo-chemical etching process.- Designed and implemented a paperless cost estimating and file management system for the entire organization.- Created control charts and trained operators for statistical monitoring of manufacturing process parameters.
-
-
Product and Process Engineer
-
Oct 2011 - Sep 2012
- Established customer relationships and took the lead to develop multiple product lines from prototype to production volumes, one of which was a Top 3 customer for 2014.- Supported Production department on a daily basis and provided expertise in solving problems related to manufacturing parts.
-
-
Engineering Technician
-
Apr 2010 - Oct 2011
- Completed customer quotations including estimating labor times, sourcing raw materials, and working with the Purchasing department to obtain secondary service quotes.- Created and maintained sequence of operations and process instructions for incoming customer orders using VISUAL ERP system.-Provided back-up capability for tooling design and generation.
-
-
Education
-
Rochester Institute of Technology
Bachelor of Science - BS, Industrial and Systems Engineering
Community
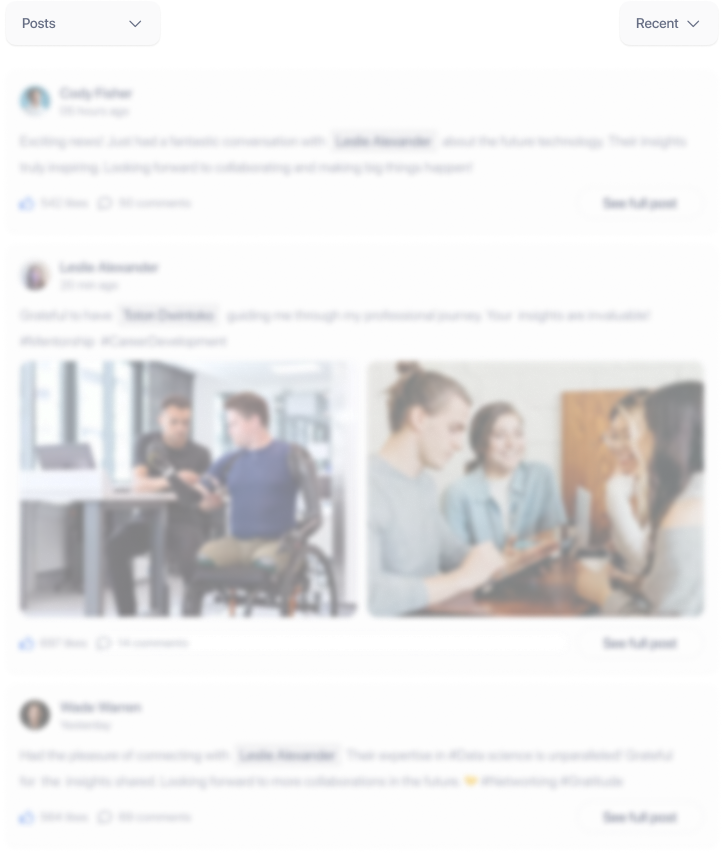