Boris Snitgaard
Plant Manager at Arctic Filet AS- Claim this Profile
Click to upgrade to our gold package
for the full feature experience.
-
English Professional working proficiency
-
German Professional working proficiency
-
Polsk Limited working proficiency
Topline Score
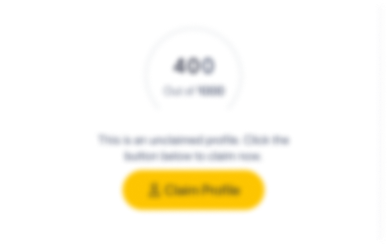
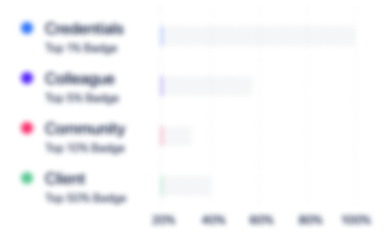
Bio


Credentials
-
Six Sigma Master Black Belt
COMPASS AkademiDec, 2019- Nov, 2024 -
Iso 9001 og Iso 22000
-
Experience
-
Arctic Filet AS
-
Norway
-
Food and Beverage Manufacturing
-
1 - 100 Employee
-
Plant Manager
-
Sep 2021 - Present
-
-
-
A. Espersen A/S
-
Denmark
-
Food and Beverage Manufacturing
-
100 - 200 Employee
-
PLANT MANAGER
-
2018 - Sep 2021
Leads all all plant operations for a 24/7 250 employee food manufacturing operation. Managing nine direct reports protects all operations by ensuring adherence and compliance to policies and procedures in the working environment and with all food safety regulations including HSE, BRC, FDA, IFS, and HACCP. Responsibilities include managing the entire supply chain and logistics for 16,500 tons of production output across three production lines. Also carries full P&L responsibility for over 300 million PLN while leading optimization and investment projects and serving as a board member on the management board. Cultivated a lean, high-performance culture of quality-focused leaders and staff by leading training and development efforts and by monitoring and managing KPIs including security, complaints, employee absences, stop time, delivery security, and stock binding of raw materials and finished products. ▪ Increased productivity 19% by conducting regular meetings and executive proper planning.▪ Increased profitability 8% by staff restructuring. ▪ Improved on time deliveries from 95% to 99.2% through improved planning and scheduling. ▪ Reduced downtime 44% by implementing a preventive maintenance program.▪ Contributed 3% in raw material savings through vendor and inventory management combined with improved packaging. ▪ Enabled 20% increase by adding 1 production line and moving to a 24/7 operation. Show less
-
-
INTERIM HEAD OF DIVISION
-
2017 - 2018
-
-
-
RPC Group Limited
-
United Kingdom
-
Plastics Manufacturing
-
300 - 400 Employee
-
PLANT MANAGER
-
2016 - 2017
As the Plant Manger reporting to the General Manager I was responsible for the P&L for the facility. Overseeing twenty-six bottle/can production lines I was tasked with identifying cost reductions, implementing safety, environmental and compliance policies, while also developing a complete preventative maintenance program for all equipment. While transforming the environment into a high performance and lean culture I was responsible for employee engagement, training and development. ▪ Improved EBITDA, from PLN -6.5M to PLN 1.2M, by leading continuous improvements with lean management to enhance operational performance. ▪ Saved over PLN 50K by reducing occupational accidents from seven to four per year ▪ Reduced waste by over 50% Show less
-
-
-
Stryhns Gruppen
-
Denmark
-
Food and Beverage Manufacturing
-
100 - 200 Employee
-
PLANT MANAGER
-
2008 - 2016
As the Plant Manager I led the daily operations of three food production lines. Reporting to the Production Director I was tasked with ensuring safety and compliance standards were followed and adhered to. Managing the full P&L with four direct reports I developed and implemented new ISO and HSE standards and guidelines. Additionally I was responsible for reducing and then monitoring production costs while assuring all budgets were met while production increased. Part of this encompassed the development of a complete maintenance program. ▪ Reduced waste 64% while increasing profitability PLN 1M by implementing 5S and SMED. ▪ Increased productivity an average of 3.5% each year through strategic planning and LEAN manufacturing. ▪ Improved on time deliveries, from 94.5% to 98% over tenure, by utilizing optimum scheduling and planning tools. ▪ Lowered absenteeism, from 11% to 3.5%, by holding employees accountable for their own objectives and goals. ▪ No recordable lost time accidents in three years. Show less
-
-
Education
-
Compass Akademi
Lean Six Sigma Master Black Belt, Master -
Aabenraa
high school
Community
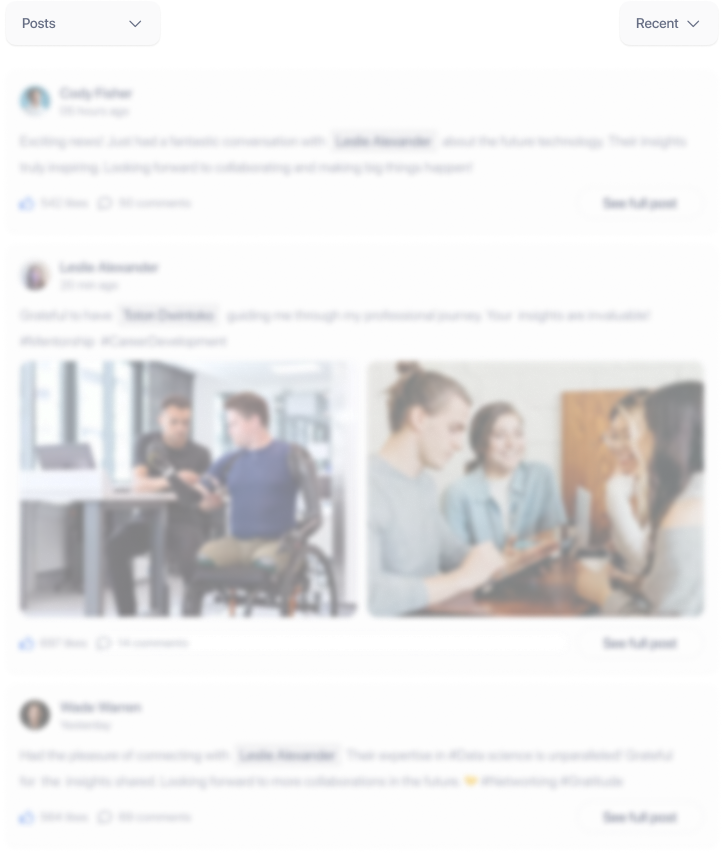