Bob Wallbridge
Inventory/Purchasing Associate at TDL Gentek Inc.- Claim this Profile
Click to upgrade to our gold package
for the full feature experience.
Topline Score
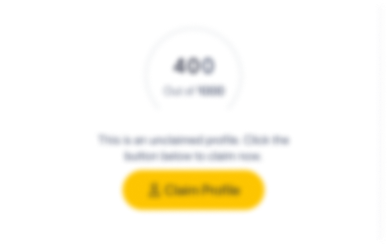
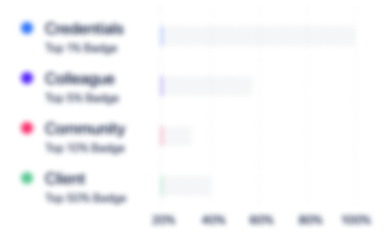
Bio
0
/5.0 / Based on 0 ratingsFilter reviews by:
Experience
-
TDL Gentek Inc.
-
Canada
-
IT Services and IT Consulting
-
1 - 100 Employee
-
Inventory/Purchasing Associate
-
Nov 2022 - Present
-
-
-
Unemployed at this time
-
Industrial Machinery Manufacturing
-
700 & Above Employee
-
Unemployed
-
Dec 2021 - Present
-
-
-
JDS Express Inc
-
Canada
-
Truck Transportation
-
1 - 100 Employee
-
Operations Manager
-
Apr 2021 - Dec 2021
• Responsible for the day of the operations of the 3rd party delivery service business. • Supervise freight drivers delivering pharmaceuticals and commercial freight. • Supervise customer service personal. • Supervise warehouse staff. • Plan warehouse storage facility to optimize building layout and maximize thru flow of all material. • Increase inventory turns from 4 to 12 and eliminated undeliverable freight due missing delivery time. • Created systems to assist Customer Service staff perform functions. • Liaison with freight provide to feedback on improvements to their systems. • Report and follow up with freight providers s on day to delivery issues. • Responsible for inventory audits as required. Show less
-
-
-
Team Quality Services
-
United States
-
Motor Vehicle Manufacturing
-
1 - 100 Employee
-
Inspection Supervisor
-
Jan 2020 - Apr 2021
• Responsible for direct coordination and supervision of inspection projects. • Available and on-call and travel to project locations. • Manage job site and crews, and coordinate projects with necessary departments. • Set-up and establish project work flow. • Ensure required tools and supplies for the project are on-site. • Perform on the job training. • Prepare, review and submit necessary paperwork. • Schedule project crews for subsequent projects and assignment. • Communicate changes in project procedures and/or requirements to necessary departments. • Act as primary contact on the job site, including but not limited to progress, concerns, and potential issues. • Maintain required certifications and authorizations as required. • Maintain working knowledge of TQS policies and procedures. • Maintain a professional and Ethical work environment/behavior. • Recommendations for disciplinary action with the Project Associates. Show less
-
-
-
-
Delivery Driver
-
Nov 2019 - Jan 2020
• Execute the delivery to the customers according to the delivery route order as determined by customer needs. • Loading and unloading of truck. • Responsible for ensuring product in truck is loaded in a safe manner prior to vehicle movement. • Complete inspection of the truck, performing circle check of truck on a daily basis and notify supervisor of any problem. • Complete all the necessary delivery documents according to the establish procedures, controls data for certain reports and remits them to his immediate supervisor (delivery run sheets etc.). • Responsible to follow safe driving practices and follow all Ministry of Transportation regulations. • Maintain security of product and vehicle. • On occasion, puts away stock warehouse or the yard in the appropriate location. Show less
-
-
-
-
Route Driver
-
Jan 2019 - Sep 2019
• Responsible for transporting and delivering various bread products to small stores and large chains stores in safe and responsible manner. • Assisting with loading and unloading items from truck to store floor and merchandising if required. • Reviewing orders with manager before delivery to ensure that the orders are complete and the customer is satisfied. • Providing excellent customer service and answering concerns form clients. • Adhering to assigned routes and following time schedules. • Abiding by all transportation laws and maintaining a safe driving record. • Ensure the warehouse and delivery truck are kept in a clean and orderly condition Show less
-
-
-
PM Industries
-
Tunisia
-
Automotive
-
1 - 100 Employee
-
Independent Business Owner
-
Oct 2016 - Oct 2018
Manufacturing custom displays, badges, vinyl lettering signs, silk screen sign for commercial and industrial applications. Manufacturing custom displays, badges, vinyl lettering signs, silk screen sign for commercial and industrial applications.
-
-
-
HGC Management Inc
-
Canada
-
Investment Management
-
1 - 100 Employee
-
Collections Operations Manager
-
Feb 2016 - Jul 2016
Organize and schedule all necessary resources required to accomplish activities. Coordinate daily operational needs with Maintenance. Plan, distribute, monitor, and follow-up daily route assignments to ensure customers are serviced per company standards and agreements. Manage the end-of-day check-in process, capturing and communicating key service, safety, and equipment issues. Monitor driver time, attendance, and minimize overtime. Sets and monitors productivity, service, and safety targets for each route and driver. Promote and maintain collaborative relations with union. Work with functional groups to resolve employee relations and labor relations issues. Conduct Root Cause Investigations for all injuries and incidents, ensuring consistent discipline and retraining. Visit customers and customer sites to evaluate and resolve service issues, seeking service alternatives where appropriate. Establish and maintain a clean, safe work environment in compliance with Company/Occupational Safety and Health Act. Document problem fixes and provide instructions should problems occur/recur. Communicate problems at customer site, and safety issues reported by drivers. Ensure missed pickups are resolved, and the resolution reported. Document and maintain records required by all regulatory agencies (i.e.; Ministry of Transportation Ministry of Labor etc.). Review and audit documentation related to route operations on a daily basis (e.g., pre and post trip inspections, driver time and attendance, open tickets), following-up where appropriate. Responsible for employee performance reviews and feedback, scheduling time off, employee grievances or complaints, and job responsibilities. Show less
-
-
-
Blommer Chocolate Company
-
United States
-
Food Production
-
300 - 400 Employee
-
Supply Chain Manager
-
Jun 2014 - Jun 2015
Strategically plan and acquire all raw materials, packaging and transportation requirements to support the manufacturing process. Reducing inventory holding cost by 10% while maintaining, service, quality and quantity. Redesign MRP and set min/max control levels to maintain efficient levels to obtain 0 stock outs. Completed first 3PW inventory and established monthly inventory verification geared to 97% accuracy Increase inventory turns from 5 for 12 with a continuous improvement plan in place. Establish landed costs of model for raw material. Maintain Vendor Program, including review of supplier performance to 98% conformance. Process Purchase Orders from the point of purchase; receipt thru to Accounts Payable to verify 100% billing accuracy. Reduce freight cost by 12% by implementing regulated fuel surcharge program. Ensure 100 % customs compliance, through implementation of policies; procedures and staff training. Improve and maintain collaborative, honest, professional relationships with suppliers. Establish open door policy with management team, production and quality control. Conduct performance evaluations of the direct and indirect team members using Taleo system to ensure that cooperate and departmental objectives are being met. Provide coaching and resources to employees with respect to career development, compensation, staffing initiatives, performance management, and employee relations. Assist in the development and implementation of programs that will increase employee satisfaction and commitment levels. Increased employee retention by 2% Comply with (and play a lead role with respect to) all requirements of the Ontario Health and Safety Act & Regulations and Blommer Health & Safety policies and procedures. Develop, implement, and maintain written policies and procedures. Direct and coordinate activities of personnel engaged in Warehouse and Customer Service functions. Show less
-
-
-
-
Distribution Center Operations Manager
-
May 2013 - Jul 2013
Management of all aspects of the day to day operations. This included capacity planning for daily DC operation, as well as management and capacity planning of production. Obtained a 99% order fill rate was achieved by introducing pick to order in place of batch and les then full case storage locations. The continuation of self-directed teams in production maintained 100% of a daily output targets. Review of internal and customer policies and procedures to ensure 100% compliance of product and logistical quality standards. Reporting of operational KPI’s and financials to the corporate level to target 98% efficiency. Deployed corrective action to any substandard performance criteria by using Failure, Mode and Effect Analysis (F.M.E.A.). Participate in monthly North American and International KPI’s webinar reviews, to ensure 100% of KPI’s were answered to, corrective actions were being deployed, and best practises were being shared and implemented. Developed the order fulfilment process which included the mapping for system programing. This produced a 20% efficiency improvement in order picking. Manage cycle count program to 98% accuracy rating. 5% efficiency improvement in warehousing and production by championing and deploying 5S program. Management chair for the Joint Health and Safety Committee which achieved a 0.1% lost time annual average. Coach and counsel staff of 47 union team members and 3 supervisors through performance expectations, development, and problem resolution. Obtained a 0% turnover rate and 0 union grievances. Show less
-
-
Process Manager
-
Aug 2011 - May 2013
Completed a review and bench mark of all DC processes and procedures and developed a computer based format for all policies and procedures. Management and capacity planning of production. By introducing production to “self-directed team work practises, the output was maintained at 100 efficiency% Develop the process flow for dock to stock put away which included the mapping for system programing. This produced a 15% efficiency improvement in stock put away time. Develop and deployed a cycle count program, including the process flow for the system program. This moved inventory accuracy to 98%. Designed planning tools to monitor seasonal fluctuating warehouse layout and staff scheduling. This improved temporary labour requirement during peak seasons by 5%. Managed 3rd party warehouse during peak seasons to allow for 50% increase in revenue flow. Introduced Cross Functional team strategies to bring floor team members into the planning process and gain buy in for critical changes. 10% efficiency improvement in warehousing and production by championing and deploying 5S program. Collection of forecast data for building expansion planning submission to Corporate HQ, back plans for a building expansion. This building expansion provided a 25% overhead cost reduction during peak seasons. Reporting of operational KPI’s and financials to the corporate. Deployed corrective action to any criteria below 98% efficiency by using Failure, Mode and Effect Analysis (F.M.E.A.). Participate in monthly North American and International KPI’s webinar reviews, to ensure 100% of KPI’s were answered to, corrective actions were being deployed, and best practises were being shared and implemented. Management chair for the Joint Health and Safety Committee. This included working with the city Fire Marshall to provide a required evacuation plan and facilitating the required changes to meet 100% of the building ordinance requirements Show less
-
-
-
-
Purchasing and Logistics Coordinator
-
Sep 2009 - Sep 2010
Monitor customer requirements on a daily basis and schedule production to ensure all orders/stock throughout the supply chain were filled to support 100% on time delivery to the field. Daily review of all inventory levels and coordinate monthly cycle counts to ensure 98 % inventory accuracies. Develop landed cost models to enable supply chain solutions. Develop plant/production launch system to ensure 100% on time market readiness. Reduced inventory by $1.2 million dollars. Negotiation of freight contract with 3rd party transportation provide to ensure budget target of 5.2% cost of goods sold (COG). Achieved a 25% reduction in bottom line freight costs. Review and authorize payment of all freight and customs invoicing ensuring 100% billing accuracy. Negotiation of Customs Broker contract to ensure efficient and cost effective border clearance. Responsible for all customs activity including annual NAFTA certification. Support all departments with logistically analysis to assist in business planning and critical decisions. Show less
-
-
-
Choice Refer Systems
-
Canada
-
Truck Transportation
-
1 - 100 Employee
-
Warehouse Manager
-
Oct 2008 - Feb 2009
Supervised staff of 12 through the day to day operations of all aspects of shipping, receiving, inventory, warehousing, and safety, in a frozen and refrigerated cross dock environment. Developed and maintained staffing schedules, detailed job instructions (D.J.I.), policies and procedures relating to all aspects of the warehouse and logistics network. Initiated best practices shipping methods. Developing matrix's to monitor warehouse staff performance on shipping accuracies, receiving accuracies, SKU location and safety. Developed and administered forklift training for all staff. Coached and counselled warehouse staff through performance issues. Coordinated with customer service and operations manager to ensure 100% on time deliver to Canada wide customer base. Responsible to provide delivery instruction to transport drivers. Show less
-
-
-
-
Logistics Coordinator, Warehouse Operations Supervisor, Material Handling Leadhand
-
Jan 1989 - Jan 2007
• Reduce the inbound freight budget from 3.0% COG sold to 2.2 % by analyzing data, developing carrier RFQ, negotiating contracts, and route design/redesign. • Led the M.P.& L. cost reduction team to a $1.5 million reduction in departmental operating costs by using LEAN principals for manufacturing and warehouse operations • Preparation of the annual logistics budget. • Monitored the monthly budget verses actual and accruals on all warehouse and logistics activities. • Responsible for all logistics related ISO and QS9000 documentation. • Coached and counselled 32 warehouse staff through performance issues. • Maintained a 98% 5S rating throughout all warehouse by monitoring the facilities and developing corrective actions. • Developed and maintained staffing schedules, and detailed job instructions (D.J.I.) to ensure 100% cross training compliance. • Developed matrix's to monitor warehouse staff performance on shipping accuracies, receiving accuracies, SKU location and safety. • Achieved a departmental 0 accident rate by developing and administering safety training programs. • Achieved a 99.5% customer rating as leader of the Material Management Operations Guidelines team, by ensuring all MRP business policies and procedures were documented in detail. • Led advance launch team site visits to customer locations. • Achieved 100% on time delivery rating from customers by establishing and maintaining dock schedule in conjunction with their 3PL's. • Supported purchasing, marketing, and engineering departments with logistics models for customer and supply base, to achieved 100% on time new product launch. • 100 % compliance to Canadian and international customs requirements. • Maintained customer owned packaging inventory and repair. • Received a joint $1,000.00 award for a $500,000.00 saving for a packaging design. • Met budget requirements in the design and building layouts for two warehouse facilities. • Member of the Health and Safety Ergonomics Committee. Show less
-
-
Education
-
Schulich School of Business - York University
Export and International Trade -
Linda McGill Group (Ministry of Labor)
Joint Health and Safety Certification -
Loyalist College
Fork Lift Operator Training (Class # 1, 4, 5 and Counter Balance Sit-down trucks) -
PIC Group
Problem Solving Using the 8D Model -
Peter Vasos & Associates
Coaching On The Job -
Rockhurst University
Microsoft Excel -
Ontario Management Development Program (OMDP)
Training in the Workplace -
Rockhurst University
Highly Effective Criticism & Discipline for Managers -
Industrial Accident Prevention Association
Safety Health and The Law -
Loyalist College – Learning Development
The 3-A's of Leadership and Authority -
Ontario Management Development Program (OMDP)
Management for Results -
Automotive Industry Action Group (A.I.A.G.)
Certificate, HTS Harmonized Tariff Schedule Overview -
Loyalist College – Learning Development
Dealing With Difficult Situations in the Workplace -
Loyalist College – Learning Development
Dealing With Difficult Situations -
Lean Enterprising Institute
Value Stream Mapping – Lean Systems -
Automotive Industry Action Group (A.I.A.G.)
Certificate, NAFTA Content Reporting -
Biztech
Microsoft Project -
Loyalist College
Time Management -
Schulich School of Business - York University
Logistics Management -
Ford Development Centre (Q1, Q2, and Q3 Modules)
Quality Concepts, Quality by Process Flow, Process Instructions -
Workers Health & Safety Centre
Joint Health and Safety Certification Level 1 Training Program -
Ford Development Centre
Failure Effect Mode Analysis (F.E.M.A.) -
Loyalist College
Excel and Word for Windows Basic -
Workers Health & Safety Centre
Joint Health and Safety Instructor Certification -
International Material Management Society
Associate's Degree, Material Management -
Loyalist College
Advanced Electronic Engineering -
Quinte Secondary School
Diploma, Technical
Community
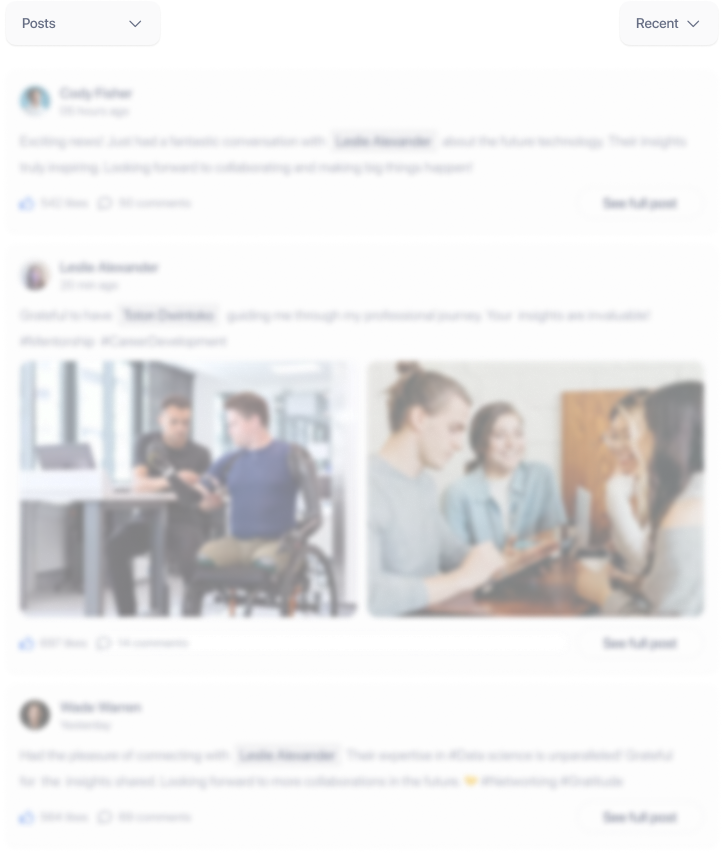