Bob Kelley
Director of Supply Chain & Planning at Stimlabs at StimLabs- Claim this Profile
Click to upgrade to our gold package
for the full feature experience.
Topline Score
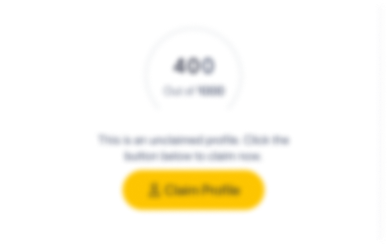
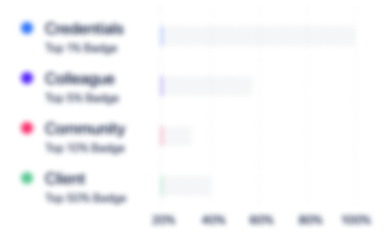
Bio

Brandon W. Phillips
Bob is very diligent and dedicated to his work. I had the pleasure of working under Bob at Femasys Inc. for over two years. Bob’s leadership style focused on nurturing the strengths of the team members and encouraging us to expand these strengths by learning new skills. His greatest strength is his ability to create and manage cross-functional teams in order to meet company objectives. Bob would be a true asset for any positions requiring strategic leadership and this comes with my heartfelt recommendation.

Mary Tyler(she/her)
I worked with and for Bob Kelley. Bob is very knowledgeable in supply chain and logistics. Bob was good at building cross functional teams along with developing the skills of his direct reports. He has a forward thinking mindset that allows him to see how changes affect not only him and his group, but the organization as a whole. Bob was a pleasure to work with, and I hope to get the chance to work with him again in the future.

Brandon W. Phillips
Bob is very diligent and dedicated to his work. I had the pleasure of working under Bob at Femasys Inc. for over two years. Bob’s leadership style focused on nurturing the strengths of the team members and encouraging us to expand these strengths by learning new skills. His greatest strength is his ability to create and manage cross-functional teams in order to meet company objectives. Bob would be a true asset for any positions requiring strategic leadership and this comes with my heartfelt recommendation.

Mary Tyler(she/her)
I worked with and for Bob Kelley. Bob is very knowledgeable in supply chain and logistics. Bob was good at building cross functional teams along with developing the skills of his direct reports. He has a forward thinking mindset that allows him to see how changes affect not only him and his group, but the organization as a whole. Bob was a pleasure to work with, and I hope to get the chance to work with him again in the future.

Brandon W. Phillips
Bob is very diligent and dedicated to his work. I had the pleasure of working under Bob at Femasys Inc. for over two years. Bob’s leadership style focused on nurturing the strengths of the team members and encouraging us to expand these strengths by learning new skills. His greatest strength is his ability to create and manage cross-functional teams in order to meet company objectives. Bob would be a true asset for any positions requiring strategic leadership and this comes with my heartfelt recommendation.

Mary Tyler(she/her)
I worked with and for Bob Kelley. Bob is very knowledgeable in supply chain and logistics. Bob was good at building cross functional teams along with developing the skills of his direct reports. He has a forward thinking mindset that allows him to see how changes affect not only him and his group, but the organization as a whole. Bob was a pleasure to work with, and I hope to get the chance to work with him again in the future.

Brandon W. Phillips
Bob is very diligent and dedicated to his work. I had the pleasure of working under Bob at Femasys Inc. for over two years. Bob’s leadership style focused on nurturing the strengths of the team members and encouraging us to expand these strengths by learning new skills. His greatest strength is his ability to create and manage cross-functional teams in order to meet company objectives. Bob would be a true asset for any positions requiring strategic leadership and this comes with my heartfelt recommendation.

Mary Tyler(she/her)
I worked with and for Bob Kelley. Bob is very knowledgeable in supply chain and logistics. Bob was good at building cross functional teams along with developing the skills of his direct reports. He has a forward thinking mindset that allows him to see how changes affect not only him and his group, but the organization as a whole. Bob was a pleasure to work with, and I hope to get the chance to work with him again in the future.

Experience
-
StimLabs
-
United States
-
Medical Equipment Manufacturing
-
100 - 200 Employee
-
Director of Supply Chain & Planning at Stimlabs
-
Apr 2021 - Present
-
-
-
VERO Biotech
-
United States
-
Pharmaceutical Manufacturing
-
100 - 200 Employee
-
Senior Supply Chain Manager
-
Apr 2020 - Apr 2021
-
-
-
Femasys Inc.
-
United States
-
Medical Equipment Manufacturing
-
1 - 100 Employee
-
Director Supply Chain Management
-
Jul 2017 - Mar 2020
Medical Device manufacturer of minimally invasive devices for women’s health. Director of Supply Chain and Facilities - Managed production & material planning functions from raw material to finished goods. Managed all material warehousing, control, movement, accuracy and costing. Responsible for all Purchasing and Supplier Management functions. Managed Product and Clinical fulfillment/distribution functions. Oversaw Customer Service function to meet all commercial and clinical requirements. Coordinate all facility and maintenance requirements as they arise. Responsible for maintaining and updating all Master Data in ERP. • Led effort to implement INFOR Syteline ERP for all Inventory Control, Distribution, Planning, Scheduling, Purchasing, Supplier Management, and Master Data Management. • Led effort to consolidate all data from manual systems to meet above functions in ERP. • Led effort to write all SOPs and Work Instructions to carry out above business processes. • Led effort for migration of material specifications and business processes in eQMS. • Led effort to set up all business processes to manage suppliers through eQMS.
-
-
-
Immucor, Inc.
-
United States
-
Medical Device
-
700 & Above Employee
-
Senior Manager, Materials Management
-
Nov 2014 - Jul 2017
Large Medical Device manufacturer of blood screening equipment and reagents for determining compatibility for blood transfusions, tissue, and organ transplants. Company with $400 million in annual sales. Sr. Manager, Materials Management – Responsible for purchasing, planning, inventory control, warehousing, manufacturing scheduling, and master scheduling of manufacturing at Immucor’s corporate location in Norcross Georgia. 6 direct reports. Developed and implemented integrated manufacturing scheduling system that tracks products through 6 manufacturing departments. Process increased productivity by 48% in six months by coordinating resources through each department.
-
-
-
A & M INSTRUMENTS LIMITED
-
United Kingdom
-
Hospitals and Health Care
-
Operations Manager
-
Jun 2013 - Nov 2014
Small Medical Device company that manufactures diamond coated dental burs. Operations Manager – Responsible for Purchasing, Planning, Inspection. Functioned as Quality Representative responsible for the implementation of ISO 13485. • Carried out all purchasing for machining, painting, and plating operations. • Conducted receiving inspection for all direct materials. • Responsible for complete implementation of the Quality Management System, ISO 13485, ISO 9001, CE Marking, MDD, and CMDR certification. Wrote Quality Manual and all procedures, work instructions and forms for carrying out the day to day operations in an ISO compliant environment.
-
-
-
Aderans Research Institute
-
Biotechnology
-
1 - 100 Employee
-
Materials Manager
-
Jan 2007 - Apr 2013
Start-up Biotech company dedicated to developing a cell based solution for hair regeneration Materials Manager – Responsible for 3 direct reports and all supply chain and logistics of materials and products for the Company. • Created rolling Master Schedule with cross functional team to increase efficiency and reduce scrap in production of perishable subassembly products and reduce stock levels of raw materials. • Created production schedule for reagent and media compounding to meet all interdepartmental requirements, reduce redundant efforts in departments and to allow lab technicians to focus on areas of expertise.. • Conducted all material planning through a combination of demand planning and MRP which resulted in on average 18 inventory turns per year. • Implemented GMP compliant purchasing process for sourcing materials and managing suppliers. • Implemented GMP compliant inventory management system with processes for material movement through kanban cards, expiration management, and cycle counting. • Managed the ingress and egress of temperature controlled and time sensitive human tissue and cell product through established carrier and courier services between ARI and clinical sites. Primary point of contact for transportation exceptions 24 hours per day 7 days per week. • Negotiated contracts and pricing that resulted in less than 2% increases yearly on sole sourced products. • Managed subcontract manufacture of 510k device used in conjunction with cell product. • Team Leader in developing business processes and implementing ERP system to meet supply chain requirements in preparation for clinical trial. o Hired and managed consultants for IT and software validation and implementation. o Led team in developing business processes, procedures, and IQ/OQ/PQ documentation for implementation. o Assembled data from manual process system to be loaded in ERP System.
-
-
-
Novoste Corporation
-
Norcross Georiga
-
Project Specialist
-
Sep 2000 - Jan 2003
Start-up manufacturer of brachytherapy catheters Document Control Supervisor/ Engineering Services – Manage projects associated with the quality services department. Supervise the day to day operations of engineering services. • Team Leader for company wide implementation of Agile Software System. • Developed and implemented plan to migrate 7000 documents from manual hard copy system to online Agile system. • Assembled cross functional team to develop business process. • Led team to implement bridging program for transfer of master data, bill of materials data, router data from Agile to MSG Pro (QAD) automatically upon approval and release in Agile. Eliminating the dual entry system. • Implementation of system resulted in a reduction of change processing time from 10 days to 2 hours. • Developed and conducted training for entire organization in the use of Agile. • Hired and trained employees to conduct change management process. • Functioned as System Administrator and point person for Agile system.
-
-
-
Boston Scientific
-
United States
-
Medical Equipment Manufacturing
-
700 & Above Employee
-
Sr. Production Manager
-
Oct 1990 - May 1998
Manufacturer of Electro physiology Catheters and Ultrasound Vascular Imaging Catheters. Senior Manager, Manufacturing – Three direct reports leading a department of over 400 employees, producing over 18,000 units monthly. • Transferred three product lines and technology from Massachusetts Division to the San Jose site and incorporated them into the daily production. • Ultrasound Catheter productivity climbed from 3,000 to over 11,000 units. • Member of SAP implementation team at San Jose site, as part of a corporate plan to implement into all 22 BSC sites, domestic and international. Manager Manufacturing, Electro physiology Catheters – Three direct reports leading a department of over 150 employees. • Managed Manufacturing Department through 500% volume ramp up as a result of PMA approval on Therapeutic Catheters while improving catheter yields. • Manufacturing Department participated in month long FDA inspection with no infractions documented against the department. • Increased catheter yields from 90% to 97.5%. • Created yearly budgets for department and tracked adherence to that budget. Supervisor Manufacturing – Led department in conversion from R&D line to clinical manufacturing line. • Increased yields from 70% to 90% by driving a series of process improvements and design changes. • Set up continuous flow line that was flexible enough to accommodate seven different product families. • Set up basic Medical Device Manufacturing infrastructure to allow organization to build a safe and effective medical device in a cost effective manner. • Developed and implemented Training and Training Documentation System. • Set up Manufacturing Documentation System. • Set up job descriptions, reporting structure, etc. for Manufacturing Department. • Assumed responsibility of R&D/Pilot Line with 11 assemblers to build into Manufacturing Line. • Increased catheter builds from 100 to 1,000 per month to support Clinical Studies and International Sales.
-
-
Education
-
North Georgia College and State University
BS, Social Science Teacher Education
Community
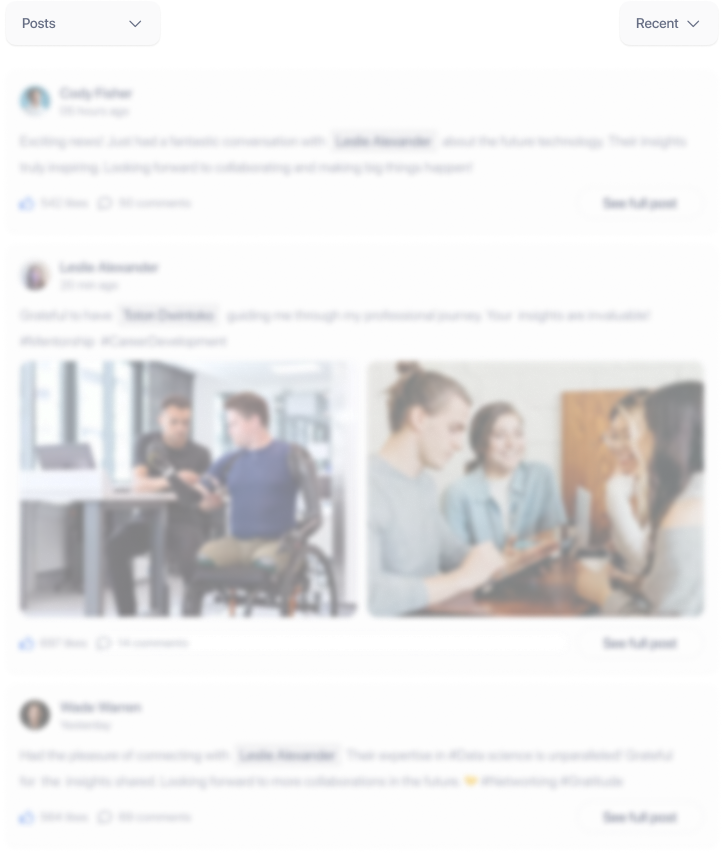