Bharat Raval
Quality Manager at Dove Die & Stamping- Claim this Profile
Click to upgrade to our gold package
for the full feature experience.
Topline Score
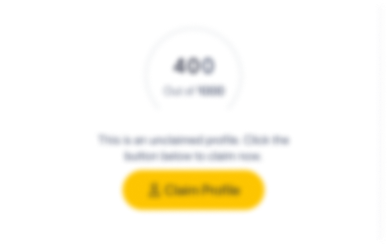
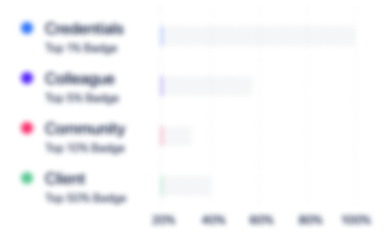
Bio


Experience
-
Dove Die & Stamping
-
United States
-
Metalworking Machinery Manufacturing
-
1 - 100 Employee
-
Quality Manager
-
Jan 2017 - Present
• Plan short and long term goals of the Quality department through interactions on all levels of the organization and leading by example. • Provide leadership to the Quality department through interactions on all levels of the organization. • Leading the development and implementation of continuous improvement initiatives related to systems, processes and procedures. • Train, motivate, and empower the Quality department and others. • Hands-on and willing to take initiative in an ever-changing manufacturing environment. • Root cause analysis for complex problems in a fast paced environment. • Manage inspection and testing of product, which includes raw material, purchased components, sample inspection, first-piece inspection, all production, final inspection, layout inspection, outside processing and sorting. • Manage gage calibration, SPC activities, APPQP, PPAP, and ISIR submissions. • Initiate 8D, 5 WHY Corrective Action process. • Ensure standards for ISO/IATF systems are in compliance. • Responsible for all other related duties and responsibilities to facilitate a successful department in a metal stamping environment.
-
-
-
Cleveland Die & Manufacturing
-
United States
-
Motor Vehicle Manufacturing
-
1 - 100 Employee
-
Quality Manager
-
Jan 2010 - Dec 2017
• Assist Management Representative and Internal auditor for company’s TS 16949 Quality Management system. • Organize successful launch of new products including prototypes and its related APQP/PPAP activities according to the time line of the project. • Work with Engineering in the design concept of strip layout including gage design per GD&T features. • Responsible for Product Qualification (PPAPs, layout inspection of first piece Samples, Control plan, PFMEA’s, SPC and Gage R&R, CMM, Calibration, In process inspection, final audit. • Organize and support customers and suppliers in PPAP activities. • Responsible for Root Cause analysis & Corrective action internal, customer and supplier rejection in a timely manner. • Lead ongoing continuous improvement projects and preventive action including 5S with cross functional team. • Responsible in maintaining quality objectives and goals through continuous improvement methodology. • Constantly monitor quarterly and improve internal and external PPM to meet goals by continuous improvement in the processes and application of root cause analysis and its elimination. • Manage and supervise 5 member, multishift quality department. Provided leadership and training for the Lean program and improvement projects.
-
-
-
Service Stampings Inc
-
United States
-
Machinery Manufacturing
-
1 - 100 Employee
-
Quality Manager
-
Jan 2005 - Dec 2010
• Develop, implement, communicate and maintain quality plan of company’s quality management system and policies into compliance with quality system requirement. • Responsible for Corrective action, Root Cause analysis, Product Qualification (PPAPs, layout inspection of first piece samples, Control plan, PFMEA’s, SPC and Gage R&R), CMM, Calibration, in process inspection, final audit, Customer returns, Customer rejects, Customer complaints, vendor rejection, in-house rejects and rework. • Developed and initiated methods and procedures for inspection, testing and evaluation on new and old jobs. • Cut quarterly customer rejects from 15% to 3% and consistently decreased number of customer complaints, vendor rejection, in-house rejects and rework by implementing corrective action and continuous improvement methods in the processes. • Develop and maintain QA objectives to ensure that targets are achieved. • Identifying relevant quality-related training needs and delivering training. • Manage and supervise 3 member in quality department.
-
-
-
-
Quality Assurance Manager
-
Jan 2002 - Dec 2005
• Management representative and lead auditor for company’s ISO 9000 quality management system. • Project task and its completion in a timely manner in launching new products from prototype phase to finished product. • Strong interface with engineering and tool room in development of new products which includes strip layout and design approval of new die, design concept and approval for building of gages per GD&T feature of the part and die tryouts. • Responsible for part inspection to the spec. and capability studies on key dimensions on parts for approval of newly built dies per customer requirement. • Responsible for APQP meetings and its documentation, Control plan, preparation of PFMEA’s, layout inspection of first piece samples through CMM, submission of PPAP’s, capability studies and Gage R&R (Attribute & Variables). • Communicate with customer’s quality/engineering dept. for any quality issues associated with products including tolerance, fit-up, comparison and capability studies. Duties often included performing engineering functions/tasks. • Analyze and investigate customer returns and initiate corrective actions as required by the ISO 9000 system. • Assisted with the reduction of internal scrap and rework rates by 5%. • Supervised two quality inspectors and one receiving inspector. • Experience with automotive and QA standards and assisting various customer QA/QC functions. • Skilled in providing coordination between quality, manufacturing, engineering and tooling. Communication is a key factor in keeping any process running efficiently.
-
-
-
Herd Manufacturing Inc
-
United States
-
Accounting
-
1 - 100 Employee
-
Quality Assurance Manager
-
Jan 1995 - Dec 2002
• Management representative and lead auditor for company’s QS 9000 quality management system. • Launching of new products from APQP phase to production phase. • Responsible for APQP, preparation of Control plan, PFMEA’s, Capability studies, layout inspection, PPAP submission and Gage R&R. • Responsible for implementation of ongoing SPC applications for new and in process jobs. • Conducted MRB meetings and supervised disposition activities. • Initiated gage calibration, scrap reporting, vendor rating system, corrective actions and inspection processes. • Development of new suppliers that includes onsite auditing for secondary operation like plating, heat treating and E-Coat. • Supervised and trained quality engineer, quality inspector and one receiving and final audit inspector.
-
-
-
-
Quality Engineer
-
Jan 1994 - Dec 1995
• Wrote Policies, Procedures and Quality Manual. • Team facilitator for process evaluation deploying statistical and problem solving techniques in order to improve quality and production standards. • Interpret engineering drawings and establish control limits per the quality plan. Also use to work on Auto-cad as and when required. • Responsible for first piece and last piece inspection per spec. and also monitor work in process after setup approval. • Responsible for receiving inspection of purchased product from outside service per control plan. • Achieved external PPM level to 50 and external PPM to 4500 by placing inspection points in in process inspections, improving the process performance and final audit instructions. • Ability to provide supervision and training for less qualified inspectors.
-
-
Education
-
Lorain County Community College
Six Sigma Black Belt -
Sardar Patel University
Bachelor of Science - BS, Mechanical Engineering -
The City University of New York
Master of Science - MS, Mechanical Engineering
Community
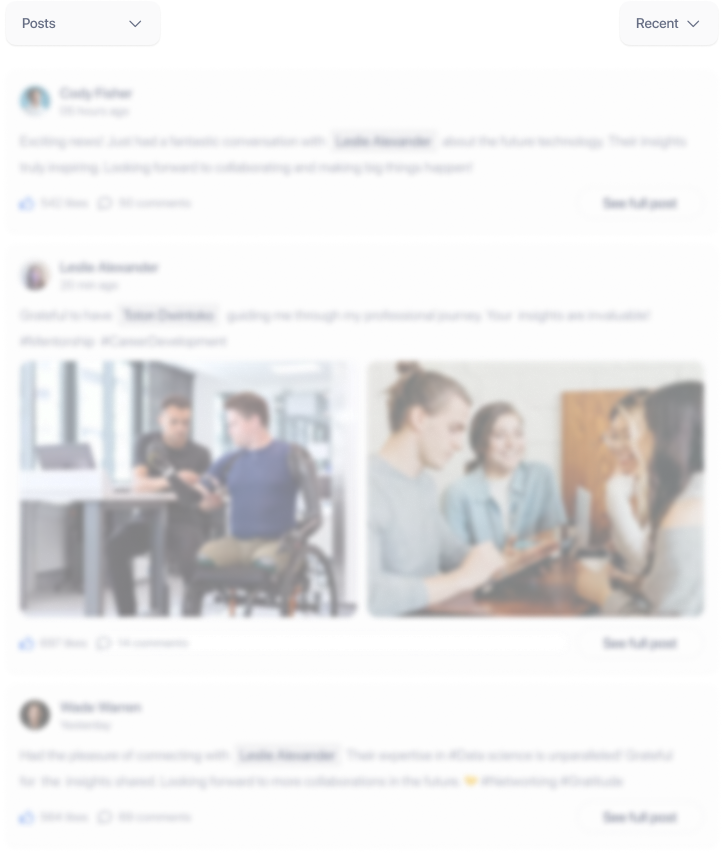