Bhanu Pratap
Sr Engg -QA at Minda Furukawa Electric (P) Ltd. Bawal- Claim this Profile
Click to upgrade to our gold package
for the full feature experience.
Topline Score
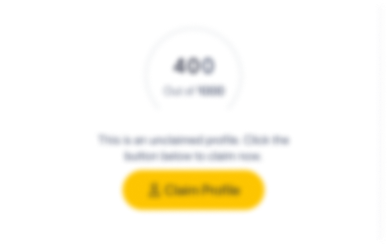
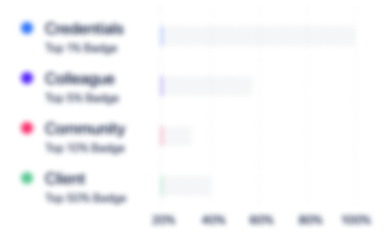
Bio


Experience
-
Minda Furukawa Electric (P) Ltd. Bawal
-
Motor Vehicle Manufacturing
-
200 - 300 Employee
-
Sr Engg -QA
-
Sep 2017 - Present
-
-
-
Supreme Treves Pvt. Ltd.
-
IMT MANESAR GURGAON
-
Sr Engineer (QA)
-
Sep 2015 - Present
• Responsible for Process Quality Assurance &.warranty Analysis. • Responsible for Final Quality Assurance. • Responsible for Inward Quality Assurance. • Responsible for PDI and Customer Quality • Responsible for calibration of welding fixture and gauges • Quality Improvement through Component & Layout Inspection. • Conducting vendor audit and process improvement • Maintain monthly rejection data. • Submit rejection summary report to top management. • Responsible for new development sample inspection • Final Inspection Defect Analysis & Monitoring. • Reduce Rejection / Rework cost by kaizen & Countermeasure Implementation. • Line problem analysis with coordination with other concerned sections. • PPM Trends Monitoring, Improvement in supplier Process by QAV-II. • Imparting training to workman about innovative techniques & new development. Quality control of manufactured parts. • Handling the process quality document PPAP,PFMEA,PQCS SPC, APQP, DFMEA, FPA, • Good knowledge about final product dispatch report. • Responsible for optimum utilization of manpower & output of line. • Responsible for reducing process trouble losses (Like Set up & adjustment time, Cycle time & defect rate). • Warranty & claim analysis at customer end, Monitoring quality systems & compliance with various standards; handling overall process. • Troubleshooting and maintaining requisite documents to ensure complete in-process quality. • To carry out Process & Product audit at Suppliers end with SQA section & look for continuous improvement based on audit findings. • Assessing variation in Process & Product characteristics, collecting data, analyzing data &making decision based on statistical output.. • Knowledge of “7-QC TOOLS “[Solving the problem by using 7QC TOOLS (Analyze the problem & 5 WHY Analysis done of Customer receiving problem in warranty & line rejection for improving Quality) Make Defect wise Pareto diagram] . Show less
-
-
-
Sunmax Auto Engineering Pvt. Ltd.
-
India
-
Motor Vehicle Manufacturing
-
100 - 200 Employee
-
QA Engineer
-
Jun 2013 - Present
-
-
Education
-
WOOD ROW SENIOR SECONDARY SCHOOL
Bachelor of Technology (B.Tech.), Mechanical Engineering
Community
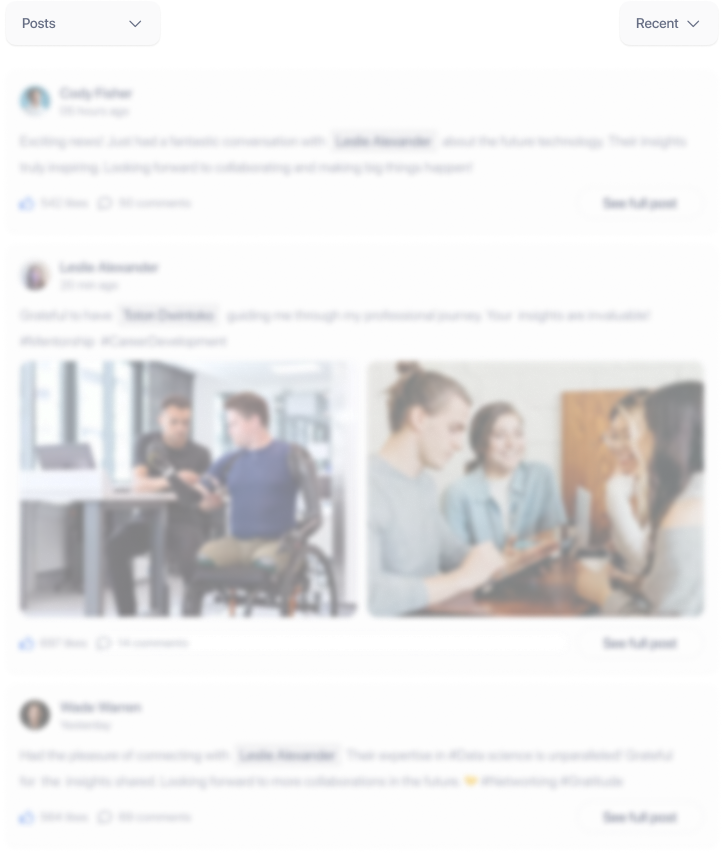