Bertha Jania Bosch
Supplier Quality & Delivery Leader at Volvo Group México- Claim this Profile
Click to upgrade to our gold package
for the full feature experience.
-
Inglés -
Topline Score
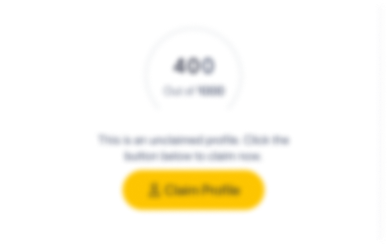
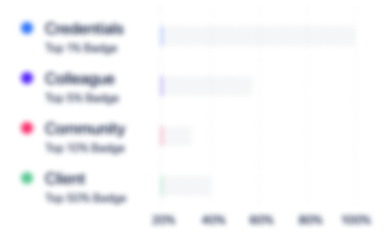
Bio

Edmundo Alvarez
Bertha is always open to listen, detect and correct weakness, emerging from processes production. Always committed to quality and improvement. Highly reliable To integrate work team with Bertha, success is a natural consequence due its professional acttitude

Vicente Orozco Flores
Quality Focus, good experience to solve claims

Edmundo Alvarez
Bertha is always open to listen, detect and correct weakness, emerging from processes production. Always committed to quality and improvement. Highly reliable To integrate work team with Bertha, success is a natural consequence due its professional acttitude

Vicente Orozco Flores
Quality Focus, good experience to solve claims

Edmundo Alvarez
Bertha is always open to listen, detect and correct weakness, emerging from processes production. Always committed to quality and improvement. Highly reliable To integrate work team with Bertha, success is a natural consequence due its professional acttitude

Vicente Orozco Flores
Quality Focus, good experience to solve claims

Edmundo Alvarez
Bertha is always open to listen, detect and correct weakness, emerging from processes production. Always committed to quality and improvement. Highly reliable To integrate work team with Bertha, success is a natural consequence due its professional acttitude

Vicente Orozco Flores
Quality Focus, good experience to solve claims

Credentials
-
Análisis y solución de problemas basado en herramientas Six Sigma - Lean
ITESM
Experience
-
Volvo Group México
-
Mexico
-
Automotive
-
1 - 100 Employee
-
Supplier Quality & Delivery Leader
-
Jan 2022 - Present
-
-
-
Volvo Group Mexico
-
Mexico
-
Automotive
-
1 - 100 Employee
-
Supplier Quality& Delivery Leader
-
Jan 2022 - Feb 2022
-
-
-
Volvo Buses México
-
Mexico
-
Motor Vehicle Manufacturing
-
1 - 100 Employee
-
Plant Supplier Quality Engineer
-
Oct 2018 - Feb 2022
-
-
-
-
Supplierf Quality Improvement Engineer
-
Nov 2013 - Feb 2022
Responsible of the Product/Project, and RT5 audit reviews representing SQD and Purchasing.I insure proper assignment and follow-up with SQE’s and Plant Product Audit Management as required to insure closure on supplier issues. Provide details, pictures, and part numbers.Report all results to the Brand Quality Account Manager and SQD Management summarizing issues across all vehicle modules weekly. I have attended Product Brand meeting as SQD representative.I Manage corporate spreadsheet of unresolved Product Audit faults of assigned local plant, and the Pr Audit Data base; update and analysis.Warranty, QJ, reliability, campaigns.I Collect the Brand requirements for current products, current and future suppliers etc. I Work with Brand Quality Account Manager to insure support is provided as needed which aligns with other commitments (SBP, mid term actions, reactivity....), for identified tasks.Local team participation as requestedSupport the investigation and closure of incoming inspection findings (IR’s). Provide follow-up as needed to insure items are written up accurately, parts are returned to the supplier and the issue is closed by the SQE.Chair bi-weekly Purchasing/Plant Quality meeting.Investigate/follow-up on daily IR floor problems which have immediate impact on Brands. Assure Brands satisfaction with sorts, containments and corrective actions.Provide support for other Brands and Plant priorities as defined by the Continental Quality Director and Brand Quality Account Manager.Assist in coordinating Plant visits by SQE’s and Suppliers; Assure Brands expectations are met and follow-up reporting provided to responsible Plant management or staff. Show less
-
-
Supplier Quality Improvement Engineer
-
2010 - 2014
Quality System audits, Customer complaints, APQP and PPAP activities, Incoming inspection and Plat Quality control.
-
-
-
Volvo México
-
Mexico
-
Automotive
-
1 - 100 Employee
-
Brand Quality Engineer
-
Oct 2010 - Nov 2013
Responsible of the Product/Project, and RT5 audit reviews representing SQD and Purchasing. I insure proper assignment and follow-up with SQE’s and Plant Product Audit Management as required to insure closure on supplier issues. Provide details, pictures, and part numbers. Report all results to the Brand Quality Account Manager and SQD Management summarizing issues across all vehicle modules weekly. I have attended Product Brand meeting as SQD representative. I Manage corporate spreadsheet of unresolved Product Audit faults of assigned local plant, and the Pr Audit Data base; update and analysis. Warranty, QJ, reliability, campaigns. I Collect the Brand requirements for current products, current and future suppliers etc. I Work with Brand Quality Account Manager to insure support is provided as needed which aligns with other commitments (SBP, mid term actions, reactivity....), for identified tasks. Local team participation as requested Support the investigation and closure of incoming inspection findings (IR’s). Provide follow-up as needed to insure items are written up accurately, parts are returned to the supplier and the issue is closed by the SQE. Chair bi-weekly Purchasing/Plant Quality meeting. Investigate/follow-up on daily IR floor problems which have immediate impact on Brands. Assure Brands satisfaction with sorts, containments and corrective actions. Provide support for other Brands and Plant priorities as defined by the Continental Quality Director and Brand Quality Account Manager. Assist in coordinating Plant visits by SQE’s and Suppliers; Assure Brands expectations are met and follow-up reporting provided to responsible Plant management or staff. Show less
-
-
-
Pulse Electronics Corporation
-
United States
-
Appliances, Electrical, and Electronics Manufacturing
-
300 - 400 Employee
-
Quality Manager
-
1995 - 2005
-
-
Quality Manager
-
1995 - 2005
-
-
Education
-
Facultad de Ingenieria UNAM
Ingeniero Mecanico Electricista, Ingeniería industrial -
ITESM
Community
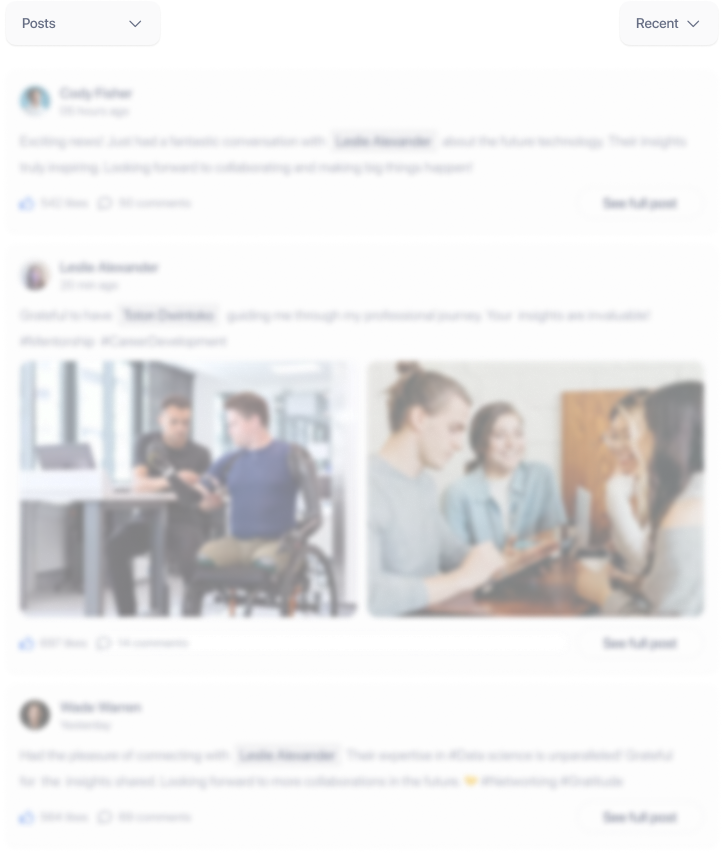