Berelize Isabel Anes Medina
Supply Chain Planner at Lyre's Spirit Co- Claim this Profile
Click to upgrade to our gold package
for the full feature experience.
Topline Score
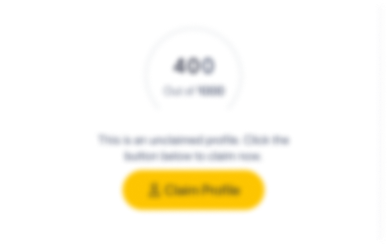
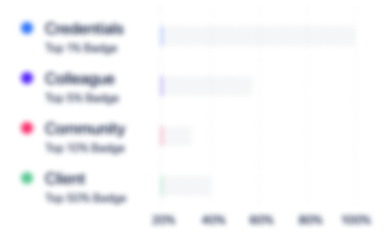
Bio


Experience
-
Lyre's Spirit Co
-
Australia
-
Food and Beverage Services
-
1 - 100 Employee
-
Supply Chain Planner
-
Nov 2020 - Present
• Development and implementation of “best in class” forecasting and planning processes, including the following elements: o Demand Forecasting o Inventory Plan o Manufacturing Plan • Development and communication of forecasts as part of the S&OP process. • Use of statistical and other forecasting methods for planning forecasts/orders. • Analysis of sales trends and influencing factors and appropriate incorporation into the demand plan. • Analysis and insights into forecast accuracy drivers and actions required to address them. • Management of master data and processes for set-up and maintenance. • Development of exception based management processes to continually drive productivity and accuracy. • Inventory optimisation whilst delivering high forecast accuracy and increased sales. • Business stakeholder engagement to clear/quit excess stock in channel. • Develop relationships with 3PL, suppliers and logistics providers in all markets and countries. • Participation in sales and marketing improvement projects with a focus on forecasting and manufacturing planning. • Knowledge of different markets compliance and regulatory requirements Show less
-
-
-
DLT OPERATIONS PTY LTD
-
Sydney, Australia
-
Sales and Operation Planning Analyst (S&OP)
-
May 2018 - Nov 2020
S&OP: drive Sales & Operations Planning process to achieve optimal demand management performance. Collaboratively lead S&OP meetings, engage and communicate with stakeholders, fostering internal business partnerships and cross-functional collaboration to optimise the demand planning process, improving forecast accuracy and reducing bias to drive best business outcomes. Reports: establish and maintain forecast performance measurement through timely and accurate creation of reports shared to stakeholders in Customer Service, Finance Marketing and Sales, Production and Management. Operation: support program management and the execution of strategic optimization across functions. Process: develop Key Process Indicators (KPI) and metrics and measure improvements. Data: develop data sets and dashboard format to support S&OP meetings to align planning across functions to meet company objectives and improve performance. Provide visibility on trends based on data analysis and make recommendations that will drive business metrics. Inventory: provide insight into inventory trends using operational KPI’s. Support in building, optimizing and maintaining Inventory Policies. Manage demand planning and inventory management process for sourcing SKU’s to ensure meeting set service level targets. Optimization and continuous improvement: assist in continuous improvement initiatives or analyses related to semi-finished goods and finished goods inventory management. Show less
-
-
-
Langfield Management PTY LTD
-
Sydney, Australia
-
Supply Planner
-
Apr 2017 - Oct 2017
Inventory: analyse stock levels to identify potential stockout as well as obsolete and excessive inventory to be communicated through the S&OP process for resolution and mitigation of financial and customer service exposure. Ensuring inventory levels are optimized against production plans, forecast and warehouse capacity with no supply interruptions. Process: work collaboratively with the team and liaise proactively with Sales, Marketing, Operations, and Strategic Accounts to ensure forecast accuracy and successful inventory management. Procurement and purchase: plan and execute procurement of materials and finished goods from global manufacturers and continuous follow up on Purchase Orders to ensure supply requirements are fulfilled. Optimization and continuous improvement: Lead initiatives that drive lead time reductions, cost savings and service levels improvements. Innovation launch execution: support forecasts to boost new product launches, special promotions and sales volume increases using historical data, consumer trends, and marketing/sales input. Supplier evaluation and improvement: examining supplier’s capacities, technological resources, delivery strategies, and general business practices to reinforce relationships. Show less
-
-
-
Empresas Polar
-
Venezuela
-
Food and Beverage Services
-
700 & Above Employee
-
-
May 2015 - Aug 2016
Manufacturing process control: track and analysis of metrics to establish and implement action plans to be monitored for weekly operational meetings. Operations: define Operational System Controls based on critical variables.S&OP: analyse, maintain and review statistical forecasts and propose and execute changes to assign the best fit S&OP demand forecast model.Project Management: support multifunctional teams in 12 factories around the country to achieve goals and meet success criteria at a specified time. Create teams, action plans and managing budgets.Report: create and implement the Report Procedure of the organisation to guarantee the data accuracy and on-time availability for S&OP meetings.Optimization and continuous improvement: lead cross-functional teams in 12 manufacturing facilities to identify improvement opportunities. Create, implement and follow up respective action plans.Logistic: lead the creation and implementation of a Management Simulator of CO2 that allows the integration and automatization of forecasts, consumption and management of this critical material applied in different departments to guarantee the operational continuity of the organisation. Show less
-
-
-
Feb 2013 - Apr 2015
Production: use of demand forecast to assist in the creation of production plan activities.Inventory: perform audits of inventory and production transactions to ensure accuracy. Ensure that appropriate inventory control procedures are implemented and followed by staff.Process: assist with plant scheduling to allocate plant and machinery resources, plan human resources, plan production processes and purchase materials.Data: develop and implement KPI’s and metric systems. Measure, review and reassess action plans to control any deviations from the set metrics.Optimization and continuous improvement: identify improvement and optimization opportunities in the production line using data analytical tools and root cause.Documentation: develop departmental manuals and production reports.Audit: Good Manufacturing Practices (GMP) and Hazard Analysis and Critical Control Point (HACCP).Environmental: develop and implement the Environmental Management System based on ISO 14000. Show less
-
-
-
Nov 2012 - Feb 2013
Logistic: Support managers in ensuring the supply and demand strategies for new products to be launched and products to be discontinued are handled appropriately.Operation: compile customer orders into truckloads and plan efficient delivery routes for the transportation fleet. Coordinate warehouse/transportation-fleet assets to fulfill customers’ orders in line with the company’s service promise.Process: monitor of operational indicators.
-
-
-
Bridgestone Americas
-
United States
-
Motor Vehicle Manufacturing
-
700 & Above Employee
-
Training Engineer of Continuous Improvement Processes
-
Feb 2012 - Aug 2012
Standard: develop Training Programs based on ISO 9001:2008 Standard. Data: establish, implement and control training indicators. Process: develop and update Production Standard Procedures and implemented operational improvements in production lines. Standard: develop Training Programs based on ISO 9001:2008 Standard. Data: establish, implement and control training indicators. Process: develop and update Production Standard Procedures and implemented operational improvements in production lines.
-
-
Education
-
Australian Pacific College
Leadership and Management, Business Administration and Management, General -
Australian Pacific College
Project Management, Project Management -
Universidad Nacional Experimental Politécnica 'Antonio José de Sucre'
Industrial Engineer, Engineer -
IESA
Logistic Operations Management Diploma, Logistics, Materials, and Supply Chain Management -
Universidad Católica Andrés Bello
Diploma in Environmental Management, Management System
Community
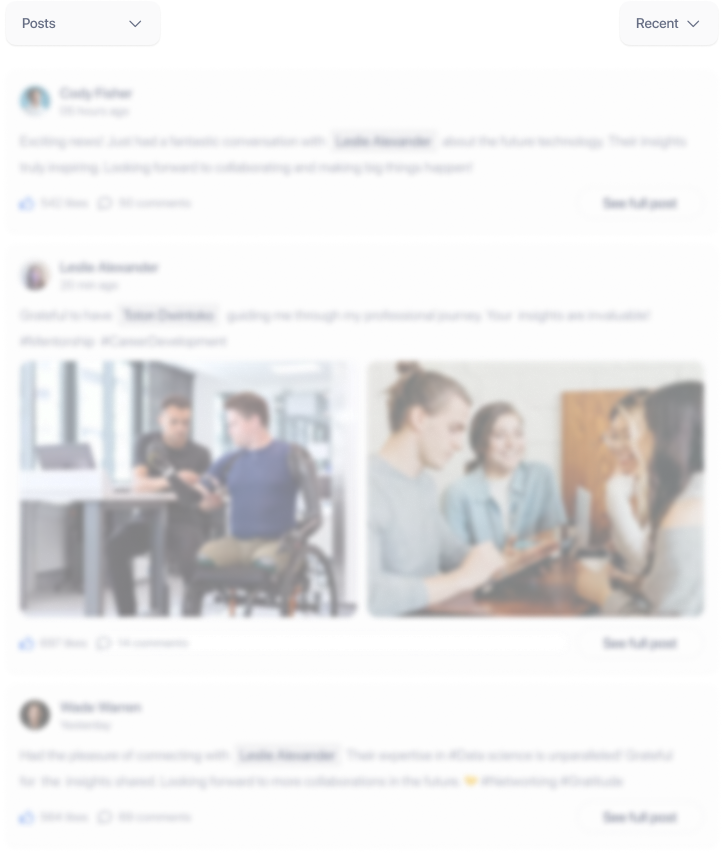