Benjamin Ruoff
Director of Maintenance and Engineering at Salm Partners, LLC- Claim this Profile
Click to upgrade to our gold package
for the full feature experience.
-
English Native or bilingual proficiency
Topline Score
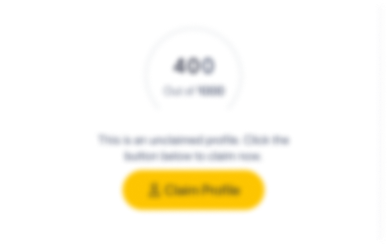
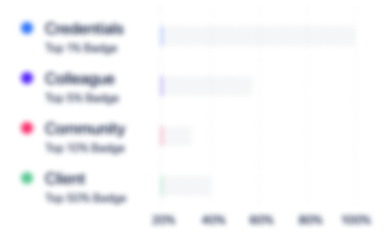
Bio


Experience
-
Salm Partners, LLC
-
United States
-
Food and Beverage Manufacturing
-
100 - 200 Employee
-
Director of Maintenance and Engineering
-
Nov 2017 - Present
-
-
Maintenance Manager
-
Jul 2016 - Nov 2017
-
-
-
PepsiCo
-
United States
-
Food and Beverage Services
-
700 & Above Employee
-
Operations Manager
-
Aug 2013 - Jul 2016
Leadership support for the processing department, 3 processing supply chain leaders, 5 coordinators, and 50 operators to deliver safety, quality, cost, and service across 8 production lines. Responsible for weekly cost forecast for the department. Prepares department productivity for the annual operating plan.● Collaborated with corporate Engineering and the Product Growth Director to develop a plan to build asset capability at the Frankfort East Plant to enable quick responses to customer demands for Organic and Non-GMO products. Led project installation and launch of Simply Organic Scoops!, the transition of Simply Tostitos from ‘Made with Organic’ to full Organic, and the launch Non-GMO Smartfood Delights Popcorn.. ● Leader of ‘Connect’ Employee Relations Group helping young professionals adjust and be successful in the corporate work place. Mentors team of 3-5 young managers to put together events that educate, engage, and empower young professionals and interns.● Key leader of PepsiCo Purdue Recruiting for Frito-Lay Supply Chain. Engaged 15 site managers in recruiting and networking events to build relations. Helped build PepsiCo presence on campus to double resume submissions over 2 years from 460 to 900+. Purdue led all of PepsiCo with highest submission and acceptance rates in the past 3 years.● Facilitated region initiative to remove 3 million annual lbs of Santitas from a co-packer and optimized run volume between the two Frankfort plants. Saved the region sales group over $500,000 in costs from co-packer and transportation; gained over $120,000 in plan efficiency between the two plants in 2015.
-
-
Receiving Manager
-
Aug 2013 - Feb 2016
Oversaw the raw material receiving department responsible for forecasting, ordering, and receiving of plant raw materials. The plant received 2.5-3MM lbs. and 270 inventory codes per week by rail and truck. Managed 1 admin and 6 material handlers in the receiving department to schedule and fulfill plant safety, quality, service, and cost goals.● Managed the production, raw materials, and record keeping to maintain Organic, Made with Organic, and Non-GMO certifications & verifications. Largest producer of organic products for Frito-Lay. Helped lead first full Organic certification for Frito-Lay and first Project Non-GMO validation audit.● Updated plant receiving documentation to F22k standards for controlled documentation to help achieve F22k certification.
-
-
Staffing Manager
-
Mar 2015 - Dec 2015
Managed team member staffing, hiring, interviewing, and job bidding of 200+ full time and 100 part time employees to reduce overtime and benefit costs. ● Led a front line staffing change plan for packaging automation of 3 departments reducing FTE head count by 20 people leveraging part time staffing with no layoffs.● Developed staffing strategy for 2015 to reduce overtime costs by $190,000 from prior year.
-
-
Sr. Operations Resource
-
Feb 2010 - Jul 2013
Led a team of 10-50 team members in processing and packing production roles across the site. Responsible for delivering safety, quality, service, and cost in plant goals. Developed teams and individuals through a continuous improvement process.● Led Productivity change plan to better utilize automated packaging assets by moving production of Baked Ruffles to the Flex Baked Lays line. Reduced employee overtime and delivered $460,000 of labor savings in 2012.● Coached a summer intern to work with a team of hourly employees in Sunchips packaging to develop a Dynamic Work Place Design (5-S leveraging LSS tools) in 2013. The process has been shared numerous times with LSS leaders and other manufacturing sites.● Led an LSS Kaizen Project to reduce breakage complaints by 65% in Baked Lays in 2012. Presented the project on national day of quality and at a networking event at headquarters.● Mentored an intern through an LSS Kaizen Project to reduce finished waste in Baked Lays delivering $160,000 in 2011.● Coached 2nd Shift Baked team to become the 1st CI (Continues Improvement) level 4 team on site. The team was recognized at annual region meeting by the Region Vice President.
-
-
Maintenance Resource
-
Jun 2008 - Jan 2010
Led a shift of 12 mechanics supporting production across the plant to deliver safety, quality, service, and cost goals. Responsible for the planning and scheduling of maintenance activates in one of the largest corn processing departments in the company consisting of 7 corn processing production lines producing 360,000 lbs. per day of Doritos, Tostitos, Fritos, and Cheetos.● Developed and rolled out a mechanic ownership process driving department ownership down to the hourly mechanics and engaging them to participate in planning, improvements, spare parts, and root cause analysis for their focus area. Helped achieve plant record downtime recording 5 consecutive months under 1% equipment downtime in 2009-2010. The process was shared as a best practice across the North division. ● Coached a cross functional team of mechanics and operators in the machine guarding safety program to help obtain the OSHA VPP Star Status for the plant. The mechanic was recognized nationally for his contribution.● Put together cross functional oven hot team to address toast oven reliability, performance, and operation. Hosted company oven expert training to build capability in the team. Supported the team traveling to other sites to share and seek out best practices. Leveraged team to gather critical data to justify oven upgrade projects to improve performance and energy efficiency.
-
-
-
FCA Fiat Chrysler Automobiles
-
United Kingdom
-
Motor Vehicle Manufacturing
-
700 & Above Employee
-
Maintenance Supervisor - Mack Engine Plant 2
-
Aug 2005 - May 2008
Responsible for leading 11-24 skilled trades and production workers across various departments in engine machining and assembly to deliver plant goals in safety, quality, cost, and morale. Responsible for leading the team through the TPM process to achieve check point 4. ● Organized the launch of a 3rd shift preventive maintenance and setup crew consisting of 24 production and maintenance team members. Worked with multiple departments across the plant to set up a routine for nightly preventive maintenance, cleaning, and production tooling setup. ● Led TPM group to create a process to improve quality on the 3.7L bedplate machining line saving over $2 million dollars in scrap costs from prior year. ● Worked with and engaged plant tradesmen to put together a plan and business proposal for setting up an in house machining spindle rebuild shop with projected annual savings of $160,000.
-
-
-
Daimler Chrysler
-
United States
-
Motor Vehicle Manufacturing
-
700 & Above Employee
-
Maintenance Supervisor - Indianapolis Foundry
-
Jan 2004 - Jul 2005
Responsible for leading a team of 34 bargaining unit skilled tradesmen employees on a nightly shutdown PM crew to achieve plant goals in safety, quality, reliability, and cost. ● Worked with production to reorganize preventive maintenance activities assigning skilled trades to work groups with a rotating down equipment schedule to help meet a department goal of 98% PM compliance and reduce downtime by 20% from prior year. ● Worked with plant and department leadership to prepare for plant closure.
-
-
Education
-
Purdue University
BSEE, Electrical Engineering
Community
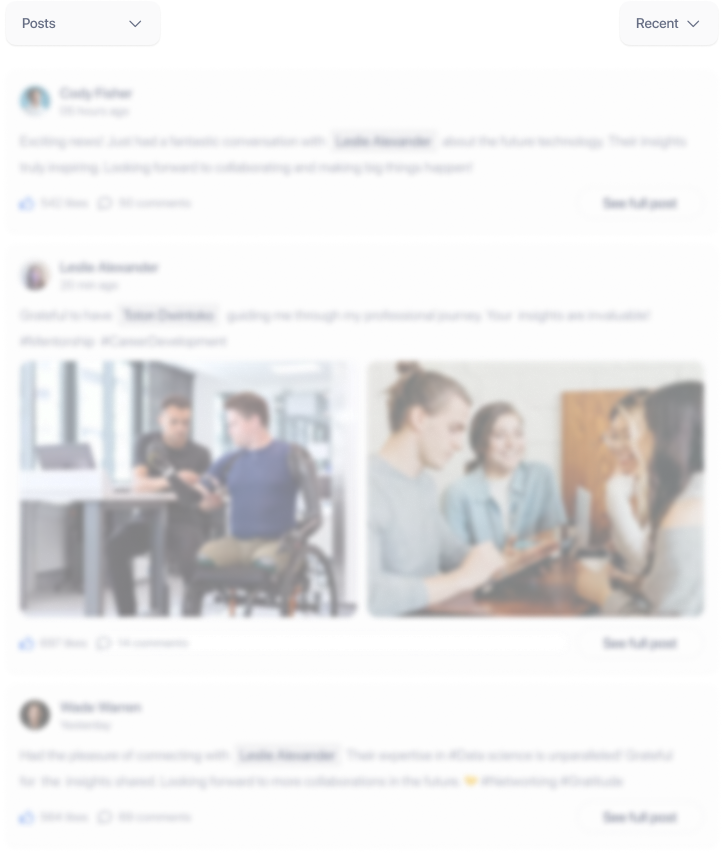