Ben Yanko
Head of Operations at Rekah Pharmaceutical Industries Ltd.- Claim this Profile
Click to upgrade to our gold package
for the full feature experience.
Topline Score
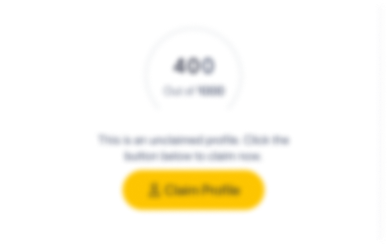
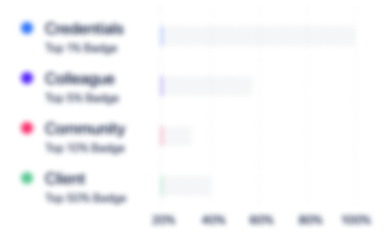
Bio
0
/5.0 / Based on 0 ratingsFilter reviews by:
Experience
-
Rekah Pharmaceutical Industries Ltd.
-
Israel
-
Pharmaceutical Manufacturing
-
1 - 100 Employee
-
Head of Operations
-
Apr 2022 - Present
-
-
-
-
Chief Operating Officer
-
May 2020 - Apr 2022
Overall responsibility for all operational aspects in the company- engineering and technology, safety, quality, production, supply chain (in Israel and abroad), human resources. Partnership in building development plans and submitting applications to the innovation authority. • Acting CEO in his absence on multiple trips abroad. • Managing company’s operational budgets – controlling variable and fixed operating costs and execution of operations and projects to reduce them. • Implementation of manufacturing excellence methodologies in the company (Lean, TPM, WCM, Industry 4.0). • Management of company’s export and import activity. • Responsible for liaison with all regulatory bodies – MOH, MOL, MOE etc. • Managing teams and operational and logistical processes in Israel and abroad. • Management of emergency events. • Streamlining processes, suppliers and subcontractors. • Responsible for issuing procurement tenders for equipment and executing procurement of equipment, machinery and production lines. • Leading projects in various fields- construction, environment etc. Show less
-
-
-
Unilever
-
United Kingdom
-
Manufacturing
-
700 & Above Employee
-
Engineering And Maintenance Manager
-
Jul 2015 - May 2020
Technological Performance: •Manages and coordinates all technical issues of the plant •Consultation and recommendation for the management and others in technical issues •Manages CAPEX annual budget according to plant plans •Observation and acceptance of new equipment •Serves as knowledge resource for all technical issues •Project management according to UL and plant policies •Manages a continuous improvement on tools' performance. Maintenance: • Maintenance cost budgeting, tracking and forecast preparing. • Guarantee the expected machines and equipment reliability on production areas to meet the requested production capacity and accordingly with the budget. •Manages technical team to meet tools capacity and availability targets •Initiates new technical procedures of machine’s maintenance. •Manufacturing Excellence-professional maintenance pillar leader Safety & Quality policies and procedures: • Implementation of Safety & Quality tools, methods & procedures in line with Unilever's global policy People Management & Organizational Culture: •Build management team in order to have the most capable and skilled people •Improve technical team capabilities and proficiency •Enable and promote communication at all levels in compliance with UL mission and culture Show less
-
-
-
Dexcel Pharma
-
Israel
-
Pharmaceutical Manufacturing
-
300 - 400 Employee
-
Technical Manager
-
Apr 2007 - Jul 2015
• Managing of plant wide maintenance activities and the maintenance team. • Direct management of Maintenance team persons including their professional development. • Leading and implementation of planned and breakdown activates including investigative and corrective actions implementation as maintenance instructions, and long term predictive and preventive maintenance • Managing and supervision of plant utilities including energy, water ,HVAC and more. • Managing technology handover of new production systems projects including maintenance training Preparing spare part stock and planned maintenance instructions. • Engineering support to production and R&D departments and assistance preparing efficient process. • Preparing long term annual and multi yearly maintenance work plans and budget, review revenues and costs relative to budget, established further action plans.. • Direct contact responsibility to variety of suppliers and contractors for plant services. • Leading and supporting engineering plant projects including production expansion ,new systems and equipment’s. • Preparing user requirement specifications including suppliers locating, bidding comparison and supporting up to hand over. • Direct working with engineering design offices and contractors and assistance to Dexcel legal department issuing work contracts. • Managing and maintaining work quality standards per company QA and safety policies. • Presentation of plant wide technical activities to FDA and local authorities. • Direct contact and responsibility to local authorities including Labor Ministry , Fire & Rescue Authority , Environmental Protection authority and hold company poison supervisor position. Show less
-
-
-
Precise Engineering
-
United States
-
Industrial Machinery Manufacturing
-
1 - 100 Employee
-
Project Manager
-
Jan 2005 - Mar 2007
Experience in clean room environment design with energy efficient system Experience with design and build of clean rooms including HVAC and control system. Preparing validation protocols and design basis (BOD , OQ , IQ , RFQ) including project site supervision. Experience in clean room environment design with energy efficient system Experience with design and build of clean rooms including HVAC and control system. Preparing validation protocols and design basis (BOD , OQ , IQ , RFQ) including project site supervision.
-
-
Education
-
Ariel University
Bachelor of Science - BSc, Mechanical Engineering
Community
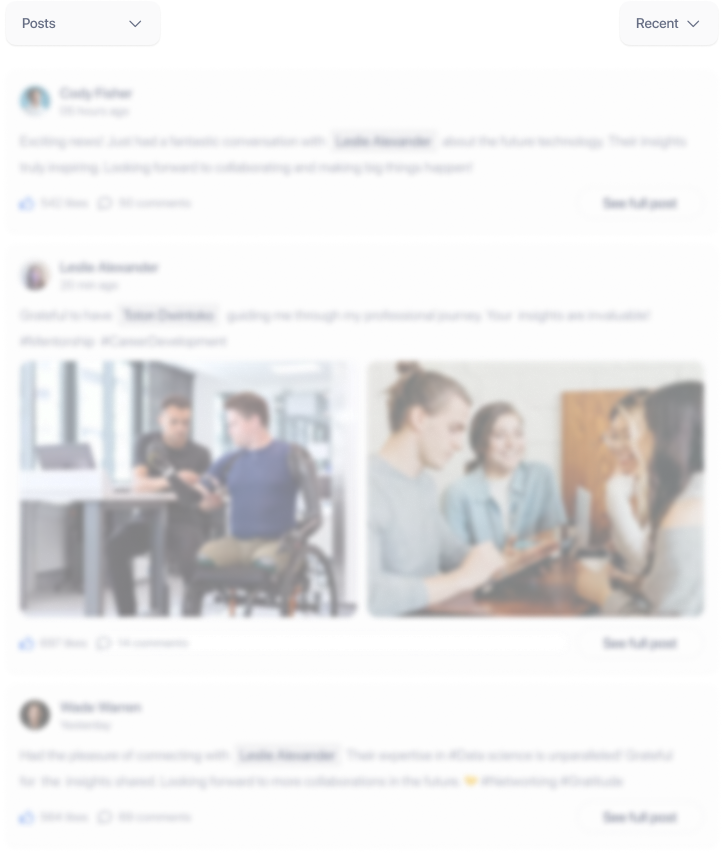