Ben T.
Sr. Process Development Engineer at VERO Biotech- Claim this Profile
Click to upgrade to our gold package
for the full feature experience.
-
Romanian -
Topline Score
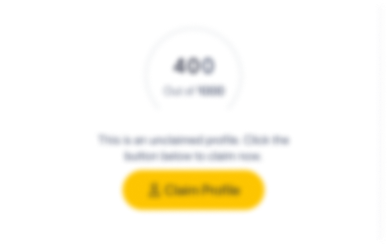
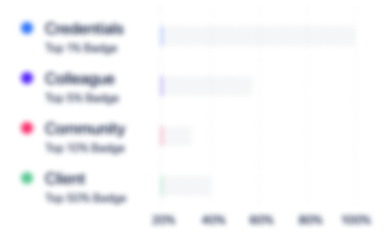
Bio


Experience
-
VERO Biotech
-
United States
-
Pharmaceutical Manufacturing
-
100 - 200 Employee
-
Sr. Process Development Engineer
-
Nov 2020 - Present
-
-
-
Avanos Medical
-
United States
-
Medical Equipment Manufacturing
-
700 & Above Employee
-
Senior Process Development Engineer
-
Jun 2018 - Nov 2020
Advanced Process Development: Supporting medical device projects with product, process, and test method development, data processing and analysis, machine design, and prototyping. Mentored co-ops and junior engineers and teaching SolidWorks. Develop electromechanical proof of principle processes as needed by various business units. Nextgen Chronic Care Oblation Probe and Kit: Developed prototype manufacturing processes, DOEs, test methods, and one/single piece flow manufacturing production equipment. Interfaced with third-party integrator to develop and build the production version equipment by providing equipment and process specifications, operator and ergonomic requirements, design reviews, timeline reviews, and as-built documentation requirements/reviews. o Subject matter expert (SME) for adhesive dispensing, UV curing, shuttle system for part handling through operator interactive one/single piece flow manufacturing stations, probe laser welding, laser marking system, Tube Kit manufacturing line. o Led tube bonding development including adhesive selection, equipment integration, curing, and curing interface design. o Designed and developed custom IV bag spike (patents pending). Nextgen Gastric Feeding Tube: Developed prototype manufacturing processes, DOEs, test methods, and one/single piece flow manufacturing production equipment. Supported Feeding Tube Project from development to LMR. LMR patient feedback is driving sales forecast increase for the MIC-KEY* SF G which is the company’s most profitable product. o SME for adhesive dispensing, UV curing, impulse sealing, automated solvent handling, machine safety, in-process testing (dimensional, leak, flow), inkjet UV cure printing and several production machines: inkjet printer, IPA cleaning, automated skiving, cuff placement vision system, RF cuff bonding, final leak tester, laser marking system, balloon burst testing, balloon cutting and vision/3d sensing error-proof kitting. Show less
-
-
-
Halyard Health
-
United States
-
Hospitals and Health Care
-
400 - 500 Employee
-
Project Scientist
-
Nov 2010 - Jun 2018
Nextgen Gastro-Jejunal Feeding Tube: 2014 – 2015 Provided support to GJ project to improve existing product and meet ISO requirements. Filled resource gap in process development team by splitting time between product & process team to leverage skillset and growth opportunities. Successfully met goals for both teams to maximize impact to project deliverables. o Provided design, fabrication, testing, test method development, test method validation and execution support for Design Freeze. o Led process development including: UV LED cure adhesive optimization, IPA cleaning optimization, valve bonding equipment, external design management, TMVs and validation protocol/execution (dimensional, concentricity, leak), pressure/leak testing equipment, FMEA/PFMEA support, data analysis automation, co-op coaching, and pilot line development and support. o SME for Suture Threader, Tungsten Filling, Skiving, adhesive dispensing and curing Invitro Gram+/- Bedside Diagnostic System: Designed and developed the fluidic system to isolate sample sputum and present it to the gram -/+ test strip for analysis while maintaining an uncontaminated bulk sample. Coordinate prototype device builds with Battelle Memorial Institute for field study and human factors studies. o Led Human Factors formative studies o Led the design coordination with internal and external customers towards final device embodiment connecting the sputum trap and fluidics, printed circuit board and test strip Paracentesis Catheter: Designed and developed exclusive valve system for integrating our bag system to only our catheter. Led Voice of Customer (VOC) reviews based on iterative designs from concept stage through DFM prototypes. o Lead customer work studies to compile customer/product/performance requirements o As technical lead, analyze technical risk, create and execute risk mitigation o Lead design/technical reviews with fellow SMEs o Coordinate engineering builds and perform design verification activities Show less
-
-
-
Kimberly-Clark
-
United States
-
Manufacturing
-
700 & Above Employee
-
Engineering Technician III
-
Jul 2008 - Nov 2010
Responsibilities: • Develop drafting standards and 3D model and print generation procedures using ANSI and K-C Corporate standards. • SCA (Site CAD Administrator) o As SCA, I advise management in the selection, implementation and training of EPDM (Enterprise Product Data Management). EPDM will replace Compliant Pro. o Provide SolidWorks training for Drafting Services. • Work with the KimVent, Bal-Cath, and Trach Solutions project teams to create new components, trouble-shoot design and quality issues as products migrate from concept phase to commercialization. Remodel and assist in the validation of legacy components being cannibalized, and create production models and drawings. Participant and contributor in multiple design review meetings. • Use Compliant Pro to create new drawing specifications across medical device component, assembly and finished good portfolios as required by the various teams and project coordinators. • Led initiative, implementing a sizing standard across the K-C gown portfolio. Coordinated with Nogales (AV3) to produce more efficient and easier to assemble gowns. These efforts led to significant reduction in scrap and maximized efficiencies of markers. • Support the Accelerated Manufacturing team in creating custom drapes as prescribed by various hospitals. • Support the Pain Management Product team in specification remediation. • Support project coordinators in maintaining all legacy product lines including Closed Suction Systems, Enteral Feeding, Facial Protection, Oral Care, Pain Management, Endoscopic and Surgical Drapes and Gowns. In support of R&E and Product Supply, I have attained a broad understanding of the K-C medical device and supply portfolios. I have experience working with K-C quality systems including; Design Control, Change Control system, Compliant- Pro, Global Packing System, and Green Folder system. Show less
-
-
-
BTD Design
-
Lawrenceville, GA
-
Consultant
-
Jul 2005 - Jul 2008
I created BTD Designs as a contract based company. I maintained relationships with customers that required outsourcing prototypes and other design needs. I created products based on design criteria required by vendors and provided 3D models, 3D/2D prints and SLA models. I created BTD Designs as a contract based company. I maintained relationships with customers that required outsourcing prototypes and other design needs. I created products based on design criteria required by vendors and provided 3D models, 3D/2D prints and SLA models.
-
-
-
Acumed
-
Medical Equipment Manufacturing
-
500 - 600 Employee
-
Product Engineer
-
Oct 1996 - Jun 2005
Responsible for managing multiple projects requiring attention from the concept phase through release to manufacturing. Responsible for creating cross-departmental teams to ensure ease of project transition through departments. • Project Management • Maintain relationships with doctors that were sponsoring the product lines and design products to meet their specifications. • Maintain relationships with vendors, outsourcing, and conduct vendor validations. • Create and maintain DHF and DMR documents including FMEA’s, Design & Development Plan, 510K documentation, validations, verifications, work instructions, drawings, and SOPs, etc. • My attention to detail helped me complete two multi-million dollar projects, both of which are now in production and sold to hospitals around the world. • During the course of these projects I had two patents approved (multiple indication bone plates). • I understand and conform to FDA, ISO 9000, and internal quality systems and requirements pertaining to Class III medical devices. • I participated in two FDA audits and conducted many internal cross-departmental audits. Duties: • Research and development of new product lines • Strict maintenance of intellectual property • Patent studies • Documentation of new product lines • Limited FEA of interfacing components • Maintaining and improving current products and procedures • Participate on regulatory team to conduct internal auditing • Complaint analysis and use CAPA if required • Maintain legacy product lines Show less
-
-
Community
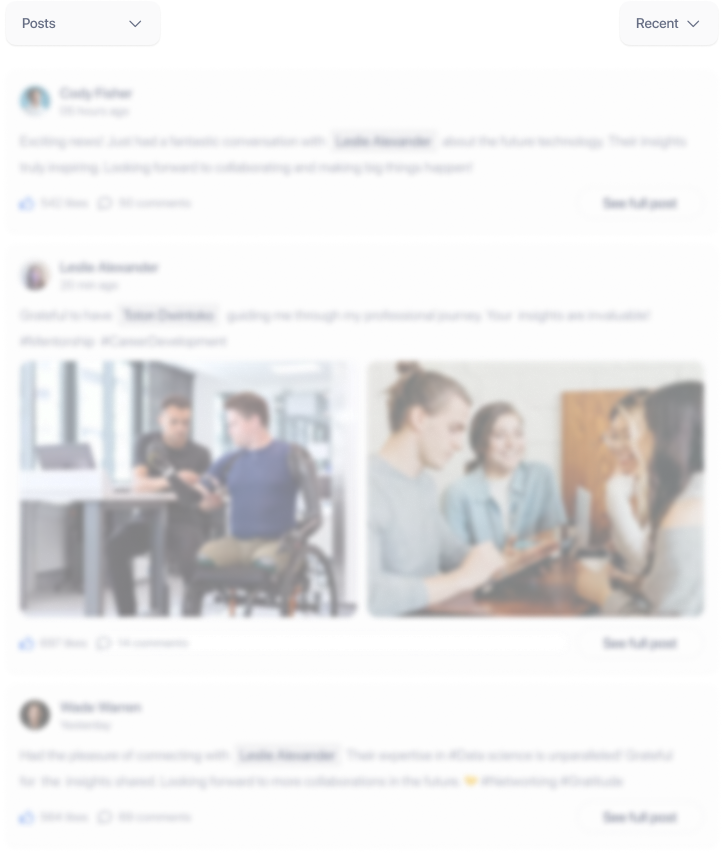