Ben Jones
Continuous Improvement and Technical Support Manager at Biocomposites- Claim this Profile
Click to upgrade to our gold package
for the full feature experience.
Topline Score
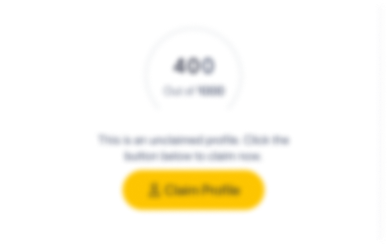
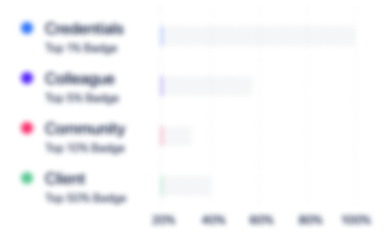
Bio


Experience
-
Biocomposites
-
United Kingdom
-
Medical Equipment Manufacturing
-
100 - 200 Employee
-
Continuous Improvement and Technical Support Manager
-
Sep 2022 - Present
· Establish a Technical Support structure and environment that will promote and implement strategy and operational models to deliver high and consistent service levels to the organization to grow revenue and improve efficiencies through Manufacturing.· Build strong relationships with the Operations team and other senior leaders to influence resource allocation and optimisation.· Develop key performance metrics and dashboards that drive the operational organisation and of the Technical Support Team· Responsible for the establishment and execution of the Technical Support Goals, KPI’s, Metrics, and objectives in alignment with the Biocomposites Goals.· Responsible for the communication and implementation of the ‘working ways and any Service Level Agreements for all Technical Support activities to stakeholders and Leadership Teams · Responsible for completion of appropriately assigned Continuous Improvement initiatives and communication to appropriate stakeholders· Responsible for Label and IFU Process from an overall ‘ownership’ perspective.· Always represent the company in a professional manner to fellow employees and subordinates as well as distributors, customers, and shareholders· Responsible for the Support to Manufacturing in terms of processing CAPA / Complaints in a ‘Rapid Response’ methodology. · Responsible for the FMEA AND Gauge R&R process, including any training aspects for the Technical Support Team· Support the Operational Team where required in the Strategic Projects and Engineering /Design Projects· Responsible for the transfer of New Products into Manufacturing, this would be through have Technical Support in the R&D phase, through design and transfer.· Support process training in Manufacturing through the ‘Standard Training’ initiative.· Responsible for the co-ordination of all the required Health & Safety requirements.
-
-
Process Improvement Manager
-
Nov 2019 - Nov 2022
-
-
-
medical Devices Company
-
Medical Equipment Manufacturing
-
1 - 100 Employee
-
Process Improvement Manager
-
Nov 2019 - Present
Identifying and delivering service improvement activities across the operations team through employment of process improvement methodologies and the application of innovative thinking. Leading and facilitating lean process improvement workshops to drive ideas and solutions. Working with key stakeholders to build a continuous improvement culture to support programmes of change. Supporting the delivery of greater value and better efficiency through the identification and elimination of unnecessary complexity within business processes and the identification of better ways of working. Identifying trends and process variation as part of establishing a continuous improvement monitoring system. Assisting and coaching other team members to be able to spot and deliver process improvement opportunities. Working cross functionally to ensure key stakeholders are aware and bought into the programme. creating monitoring systems and metrics to gauge success of initiatives. Working with other functions to ensure there is sufficient documentation in place to cover the new processes and ways of working. Ensuring that business impact and project deliverables are identified, reported on and managed at all times. Completion of after action reviews to ensure successful delivery has been achieved, documenting ad sharing of learning points.
-
-
Deputy Production Manager
-
Nov 2017 - Nov 2019
Responsible for all aspects of Production Operations.Leading teams of around 25-30 people, consisting of Controllers, Supervisors, Deputy Supervisors and Operatives.Ensuring Compliance and Regulations are followed by all to produce quality products, with the ultimate goal of patient safety. Planning production to maximise efficiency, output and Company profitability.
-
-
-
Bentley Motors
-
United Kingdom
-
Motor Vehicle Manufacturing
-
700 & Above Employee
-
Team Leader
-
Dec 2015 - Nov 2017
Production team leader in the Engine Assembly division for the Bentley Continental GT. Knowledge of BPS, Lean Manufacturing, Continuous Improvement, Waste Reduction, Line Balance, Process Reduction, Takt Change, 5's, Just In Time, Right First Time, Manpower Planning, Team Briefs & Communication, Risk Assessment, Practical Problem Solving, Plan Do Check Action, Quality Control. Production team leader in the Engine Assembly division for the Bentley Continental GT. Knowledge of BPS, Lean Manufacturing, Continuous Improvement, Waste Reduction, Line Balance, Process Reduction, Takt Change, 5's, Just In Time, Right First Time, Manpower Planning, Team Briefs & Communication, Risk Assessment, Practical Problem Solving, Plan Do Check Action, Quality Control.
-
-
-
Toyota Motor Manufacturing UK
-
United Kingdom
-
Motor Vehicle Manufacturing
-
700 & Above Employee
-
Team Leader
-
Jul 2001 - Nov 2015
Production team leader covering all aspects of TPS, Lean Manufacturing, Waste Reduction (transport, inventory, motion, waiting, over processing, over production, defects), Standardised Work, Andon, Kaizen, Kanban, TPM, Takt Time, Value Stream Mapping, Pokayoke, 4's, JIT, RFT, SYT, Risk Assessment, Project Management (Body Damage), Quality Investigation (containment & countermeasure), PPS, Visual Management, Process Diagnostics, Risk Assessment, Posture Confirmations, Manpower Planning, Colleague Training.
-
-
Education
-
Oplex Careers
Level 5, HR Management -
Six Sigma Black Belt
Black Belt, Lean Manufacturing -
TMMUK
NVQ Level 2, Business Improvement Techniques -
TMMUK
NVQ Level 3, Leadership Engineering -
Blythe Bridge High School
GCSE
Community
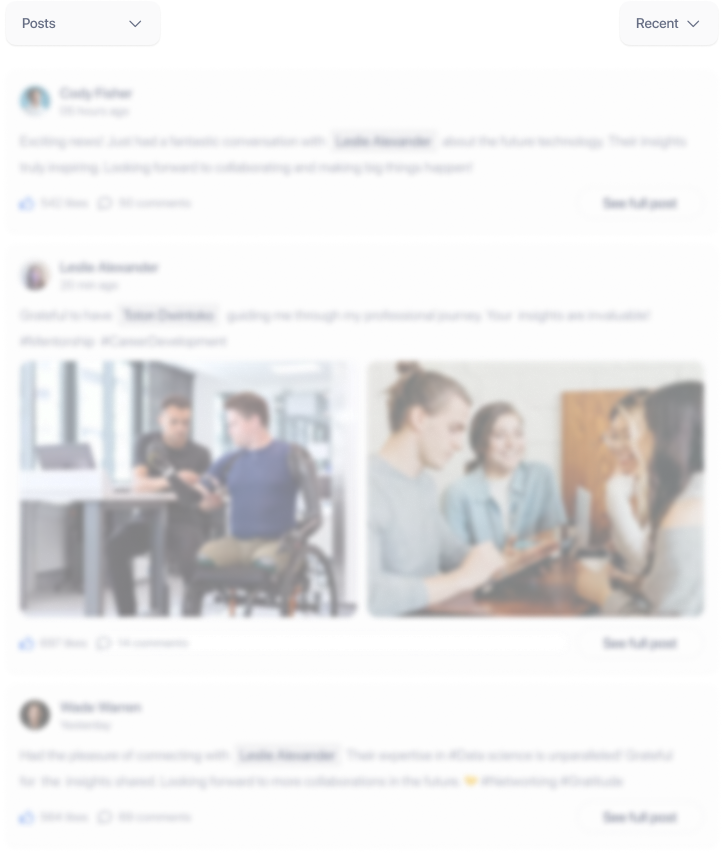