Batsheva Bain
Sr. Director, Quality at Vyera Pharmaceuticals, LLC- Claim this Profile
Click to upgrade to our gold package
for the full feature experience.
-
English Native or bilingual proficiency
-
Hebrew Native or bilingual proficiency
Topline Score
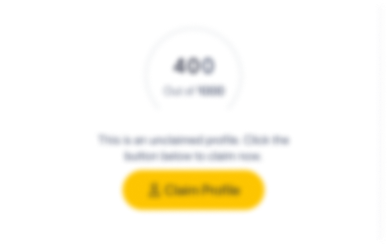
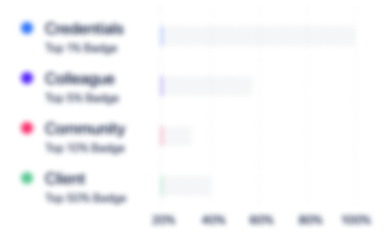
Bio

LinkedIn User
BatSheva is very professional and knowledgeable in global compliance. She is a positive influence, a strong team member and has an ability to create focus to drive issues to successful completion.

LinkedIn User
BatSheva is very professional and knowledgeable in global compliance. She is a positive influence, a strong team member and has an ability to create focus to drive issues to successful completion.

LinkedIn User
BatSheva is very professional and knowledgeable in global compliance. She is a positive influence, a strong team member and has an ability to create focus to drive issues to successful completion.

LinkedIn User
BatSheva is very professional and knowledgeable in global compliance. She is a positive influence, a strong team member and has an ability to create focus to drive issues to successful completion.

Experience
-
Vyera Pharmaceuticals, LLC
-
United States
-
Pharmaceutical Manufacturing
-
1 - 100 Employee
-
Sr. Director, Quality
-
Sep 2017 - Present
-
-
-
-
Associate Director, Quality
-
Mar 2015 - Aug 2017
-
-
-
Excel at Work Limited
-
New Zealand
-
IT Services and IT Consulting
-
1 - 100 Employee
-
Principal
-
Mar 2013 - Mar 2015
-
-
-
-
Director, Supplier Quality and Regulatory Compliance
-
2008 - 2013
• Managed all - front to end - Quality and Regulatory compliance aspects of DS and DP manufacturing. • Assisted in the writing, coordination and preparation of documentation intended to support all post-approval CMC activities. • Wrote CMC section for Annual Report. Wrote applicable supplements (CBEs, PAS). Authored, reviewed and revised various CMC sections to NDA, sNDA. • Worked closely with CMOs regulatory groups to devise regulatory strategy and ensure clear communication of requirements to support post approval activities including change controls, ARs and DMF and NDA supplements. • Worked with regulatory staff worldwide (EU/CA/Israel/AU/NZ/SA) to communicate, coordinate and track all the required documentation to support post-approval CMC activities. • Provided interpretation of regulations and guidances to internal project teams and external teams. • Addressed FDA queries. • Quality Lead for all life cycle-related projects. • Interacted with FDA, Regulatory partners/QPs in EU to resolve relevant Regulatory bodies’ compliance questions. Created applicable risk assessments to support product release/distribution for all major markets (US/EU/CA). • Provided Quality Systems support to QS group at MDCO; author SOPs; internal audit support. • Strong negotiation and conflict resolution skills to achieve win-win results. Show less
-
-
-
-
Senior Manager, Quality Assurance
-
2007 - 2008
• Quality Assurance Lead for the site Quality Assurance Team • Created integrated Quality Systems including Documentation management, SOP system, Change Control, Deviations, Investigations, and Training. • Managed quality oversight of CMOs (front to end). • Led internal and external audits (Suppliers, Contract Manufacturers and Contract Labs). • Represented QA for Tech Transfers. • Key contributor for Phase 1-3 Clinical trial support. QA consultant to clinical sites. • Quality Assurance Lead for the site Quality Assurance Team • Created integrated Quality Systems including Documentation management, SOP system, Change Control, Deviations, Investigations, and Training. • Managed quality oversight of CMOs (front to end). • Led internal and external audits (Suppliers, Contract Manufacturers and Contract Labs). • Represented QA for Tech Transfers. • Key contributor for Phase 1-3 Clinical trial support. QA consultant to clinical sites.
-
-
-
-
Senior Manager, Change Control
-
2005 - 2007
• Created a centralized change control system for the 10 US & Canada s-a sites and CMOs (post merger). •Reduced manpower demands by 25% by designing and implementing an electronic change control system. • Created a centralized change control system for the 10 US & Canada s-a sites and CMOs (post merger). •Reduced manpower demands by 25% by designing and implementing an electronic change control system.
-
-
-
-
Manager - Change Control
-
2003 - 2005
• Saved $250K by streamlining the Change Control process to assure cGMP compliance. • Managed the routine and non-routine functions of the system audit files and develop metrics. • Advisory board member to Pharmaceutical Training Institute (PTi) and speaker at two industry-wide conferences. • Saved $250K by streamlining the Change Control process to assure cGMP compliance. • Managed the routine and non-routine functions of the system audit files and develop metrics. • Advisory board member to Pharmaceutical Training Institute (PTi) and speaker at two industry-wide conferences.
-
-
-
-
Supervisor, Documentation and Change Control
-
2000 - 2003
• Increased compliance by designing and implementing a Documentation System that supports the review and approval process of all site master documents by applying consistent cGMP standards to the process. • Designed and implemented a Documentation Filing System that supports QA needs and adheres to cGMPs. • Increased department efficiency by developing documentation KPIs for the department. • Standardized the document review process by centralizing the knowledge of cGMPs and general document issues to assure that the review is completed in a single review cycle. • Reviewed and approved all documents for Sanofi-Synthelabo, QA (including but not limited to: Validation protocols, Master Production Documents, Test Methods, Specifications and Stability Protocols). • Created, designed and implemented a cGMP Training function for the QA group at Sanofi-Synthelabo, which was rolled out later company wide. • Participated in site audits of Sanofi-Synthelabo contract manufacturers and suppliers. • Coached, mentored and trained new employees. Show less
-
-
-
Pfizer
-
United States
-
Pharmaceutical Manufacturing
-
700 & Above Employee
-
Analyst
-
1991 - 2000
Operations Planning Analyst – Technical Services Department, (1997-2000) • Reduced calculation errors by designing and implementing a method of data collection to assure the accuracy of information in cleaning validation supplements. • Saved time and money by combining two reports into one thus reducing cycle time for task completion. Information collected from various sources was streamlined and calculations combined to eliminate duplication and error. • Prepared, updated validation supplements. Wrote cleaning validation task reports and protocols. • Team Leader for the Change Team of the Work Environment Initiative. Operations Planning Analyst – Materials Department, (1994-1997) • Prepared, updated and maintained site manufacturing and packaging master documents as well as site Dosage Form Monographs. Assured that these documents meet internal specifications and adhere to cGMPs. Lab Analyst – Quality Control Laboratories, (1991-1994) • Executed chemical, biological and micro testing for a variety of dosage forms. These include ID tests, dosage uniformity, dissolution testing, release rate testing, HPLC, TLC, turbidimetric and plate assays for antibiotics, air and water testing, identification of microorganisms in raw materials, selective media preparations and growth promotion tests. Show less
-
-
Education
-
Long Island University
M.Sc, Pharmacology/Toxicology
Community
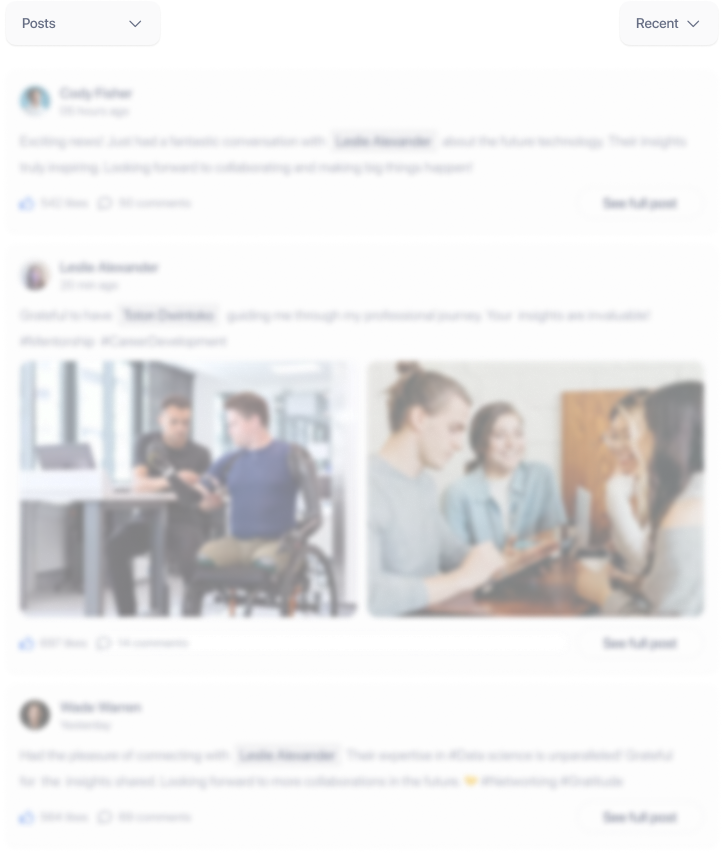