Barbara Parsons
Retired at Self Employed- Claim this Profile
Click to upgrade to our gold package
for the full feature experience.
-
English -
Topline Score
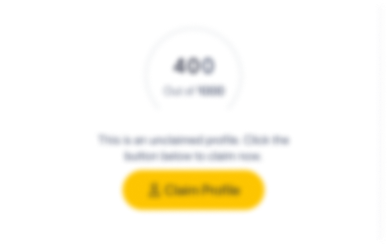
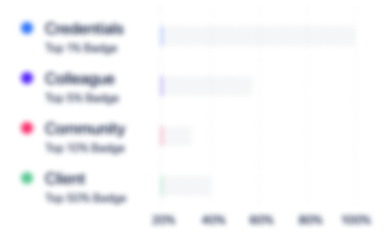
Bio


Credentials
-
IAQG–Sanctioned Aerospace Auditor Transition Training 9110
IAQG - International Aerospace Quality GroupSep, 2011- Nov, 2024 -
Internal Auditor
American Society of QualityDec, 2010- Nov, 2024 -
Quality Technician
American Society of Quality -
Six Sigma Black Belt
National Graduate School of Quality Management
Experience
-
Self Employed
-
Online Audio and Video Media
-
700 & Above Employee
-
Retired
-
Jun 2021 - Present
-
-
-
-
Retired
-
Jun 2021 - Nov 2021
-
-
-
BSI
-
United Kingdom
-
International Trade and Development
-
700 & Above Employee
-
Client Manager - Lead Auditor
-
Feb 2018 - Nov 2021
KEY DUTIES / RESPONSIBILITIES: • Undertake assessments in accordance with BSI requirements. • Prepare assessment reports and deliver findings to clients to ensure client understanding of the assessment decision and clear direction to particular items of corrective action where appropriate. • Recommend the issue, re-issue or withdrawal of certificates, and report recommendations in accordance with BSI policy, procedures and prescribed time frame. • Lead assessment teams as required • Establish and develop an effective partnership• Provide accurate and prompt information to support services, working closely with them t. • Plan/schedule workloads to make best use of own time and maximize revenue-earning activity. • Coach colleagues as appropriate especially where those members are inexperienced assessors or unfamiliar with clients' business/technology and assist in the induction and coaching of new colleagues as requested. • Maintain and develop assessment skills and technical and management system standards knowledge. Specializing in ISO9001:2015 auditing. Show less
-
-
-
Arrow Electronics
-
United States
-
Technology, Information and Internet
-
700 & Above Employee
-
Senior Quality Assurance Engineer
-
Jun 2015 - Feb 2018
• Lead Internal Auditor for AS9100, ISO9001, ISO13485, TL9000 as well as representative for External visitor audits • Primary quality representative for our east coast customer’s accounts. • Provide support in the ongoing development and administration of the Quality System through the use of statistical analysis and systems ownership. • Responds to complaints from internal and external customers; Monitoring and reporting of containment and corrective action deadlines. • Collect, Analyze and Report on internal and external quality data using statistical tools and techniques to determine trends and make recommendations for improvement. • Maintain the Internal Corrective Action program through the issuance, follow up and reporting of Internal Process quality. • Develop and maintain proactive working relationships with the Sales Organization. Show less
-
-
-
Honeywell
-
United States
-
Appliances, Electrical, and Electronics Manufacturing
-
700 & Above Employee
-
Senior Quality Engineer
-
Aug 2011 - Apr 2015
Provide leadership in deploying and enforcing the Honeywell quality system. Drive robust and effective Root Cause and Corrective Action across organization. Facilitated Corrective Action Board for Aerospace Engineering Analysis of data utilizing MS excel and pivot tables. Contribute to the effectiveness and maturity of the quality system at the site through the following by improving performance by analyzing current processes, making recommendations, and facilitating the implementation of tools and techniques to reduce process variation. Project Manager for Quality engagements with Customers, Suppliers, Integrated Supply Chain and Engineering Center Of Excellence to drive the flow down of technical and quality requirements. Network auditor for AS9100 and AS9115 (ISO 9000) specifications. Show less
-
-
-
Hamilton Sundstrand
-
United States
-
Aviation and Aerospace Component Manufacturing
-
700 & Above Employee
-
Quality Engineer/AS9100 Auditor
-
May 2005 - Jan 2011
Established, generated criteria and review of inspection requirements, instructions; metric charts; product traceability/part configuration records. Project leader of all First Article Inspections (FAI) activities. Received United Technologies (UTC) Level II Award. •Streamlined the FAI process reducing queue and preparation time plus establishing paperless system resulting in a cost savings of over $100K/year. •Implemented and redesigned FAI Excel spreadsheets with embedded blueprints for easy reference resulting in 75% turnaround reduction time. Interfaced with Customer for product presentations and process improvement. Process mapping, Lean Manufacturing, 5S, Safety. Generated final inspection work instructions and approval of production work instructions. Received UTC Level II award for commitment of on-time customer delivery dates. •Lead team project for the reduction of configuration errors from production to quality preventing erroneous delivery to customer. Reducing rework/teardown time and COPQ. Projected savings of over $200K/year (Black Belt Project). AS9100 – Lead Internal auditor for site. Program Lead and Trainer for Foreign Object (FOD) and Electro Static Discharge (ESD). Provided quality training and quality orientation. Show less
-
-
-
EaglePicher Technologies
-
United States
-
Defense and Space Manufacturing
-
300 - 400 Employee
-
Quality Engineer
-
2004 - 2005
Transfer of ISO systems to new automated start-up location in AZ. Facilitator/Manager for ISO 9000, Auditing; Document and Data Control, Receiving Inspection, Calibration, Technical Procedure/Policy Writing. Implemented Training program. Quality Customer interface representative. •Achieved ISO certification for new facility in only a three-month period with zero non-conformances. Transfer of ISO systems to new automated start-up location in AZ. Facilitator/Manager for ISO 9000, Auditing; Document and Data Control, Receiving Inspection, Calibration, Technical Procedure/Policy Writing. Implemented Training program. Quality Customer interface representative. •Achieved ISO certification for new facility in only a three-month period with zero non-conformances.
-
-
-
Edwards Vacuum
-
United Kingdom
-
Semiconductor Manufacturing
-
700 & Above Employee
-
Quality Engineer
-
2002 - 2003
Managed and implemented complete ISO 9000:2000 quality system. Supervised inspection team. •Lead company to successful certification of ISO throughout three domestic and one European facility. •Implemented: Quality Auditing program; Document and Data Control system; Critical Dimension Inspection; Calibration program; and Supplier Quality Program. Provided training to all sites for quality programs. Managed and implemented complete ISO 9000:2000 quality system. Supervised inspection team. •Lead company to successful certification of ISO throughout three domestic and one European facility. •Implemented: Quality Auditing program; Document and Data Control system; Critical Dimension Inspection; Calibration program; and Supplier Quality Program. Provided training to all sites for quality programs.
-
-
-
Pacific Scientific Energetic Materials Company
-
United States
-
Defense and Space Manufacturing
-
400 - 500 Employee
-
Quality Engineer
-
Jan 2001 - Jan 2002
Manufacturer of explosives used as stand-alone devices or as part of an ordnance system. Quality planning and requirements flow-down on military and commercial specifications programs in accordance with company and government procedures. Implementation of systems defining, monitoring, reducing cost, and enhancing delivery of products. Manufacturer of explosives used as stand-alone devices or as part of an ordnance system. Quality planning and requirements flow-down on military and commercial specifications programs in accordance with company and government procedures. Implementation of systems defining, monitoring, reducing cost, and enhancing delivery of products.
-
-
-
-
Quality Manager
-
Jan 1998 - Jan 2001
Manufacturer of probe cards and package test solutions used for semiconductor test integration. Corporate quality manager of quality services organization. Managed the following departments: ISO 9000, Corporate Quality Auditing; Technical Writing; Document and Data Control; Corporate Training; Receiving Inspection; Material Review Board and Supplier Quality. Implemented Corporate-wide Quality Auditing, Policy, and Procedure Programs. Reorganized Inspection area to reach goal of material turnover by 20%. Show less
-
-
-
-
Quality Assurance Manager
-
Jan 1996 - Jan 1998
Manufacturer and designs point-of-sales products for the commercial industry. Implemented, developed and managed all quality system programs and personnel. Established standards for product quality conformance and supporting documentation. Organized and trained inspection and manufacturing staff in disciplines required for product reliability. Participated in verification of design, budget development, manufacturing processes, and vendor compliance. Reorganized inspection departments, and devised new strategies for inspection methods. Show less
-
-
-
-
Quality Engineer
-
Jan 1995 - Jan 1996
Manufacturer of lapping machines/polishing machines used for precision stock removal and fine surface finishing. Project leader for Quality Systems documentation. Facilitator and leader for company-wide quality assessment improvement project. Developed and documented corrective/preventative action program, auditing system, Material Review Board process, calibration system, and training program. Pioneered and implemented the Quality System documentation program, writing over 75 procedures while providing training and guidance company-wide. Received the President's employee award for leadership in the company-wide quality assessment improvement program leading to ISO 9000 compliance. Show less
-
-
-
-
Production Manager/Supervisor
-
Jan 1994 - Jan 1995
Manufacturer of semi-finished mass lamination multilayer specialty printed wiring boards Managed over 50 employees in all phases of circuit board fabrication. Evaluate employee performance; provide training; maintain employee records and determine production needs. Promote teamwork and employee motivation. Organized "team module" concept for 5 departments increasing production 20% while reducing defects by 15% Manufacturer of semi-finished mass lamination multilayer specialty printed wiring boards Managed over 50 employees in all phases of circuit board fabrication. Evaluate employee performance; provide training; maintain employee records and determine production needs. Promote teamwork and employee motivation. Organized "team module" concept for 5 departments increasing production 20% while reducing defects by 15%
-
-
-
-
Quality Engineer/Inspection/Production Supervisor
-
Jan 1992 - Jan 1994
Manufacturer of semi-finished mass lamination multilayer printed wiring boards Supervised 50 employees performing circuit board functions including pre-preg fabrication; multilayer fabrication; lay-up; lamination; etching; photo-print; inspection, x-ray; plating and auditing. Performed Material Review Board duties; solved supplier/customer quality problems; assisted in ISO-9000 preparation. Implemented a cross-training program with emphasis in inter-department knowledge. Streamlined audit process and instituted audit program. Show less
-
-
Education
-
Ottawa University
Master of Education, School Counseling -
The National Graduate School of Quality Management (NGS)
Masters of Science, Quality Management -
University of Phoenix
Master of Arts, Organizational Management -
Ottawa University
Bachelor of Arts, Business Management
Community
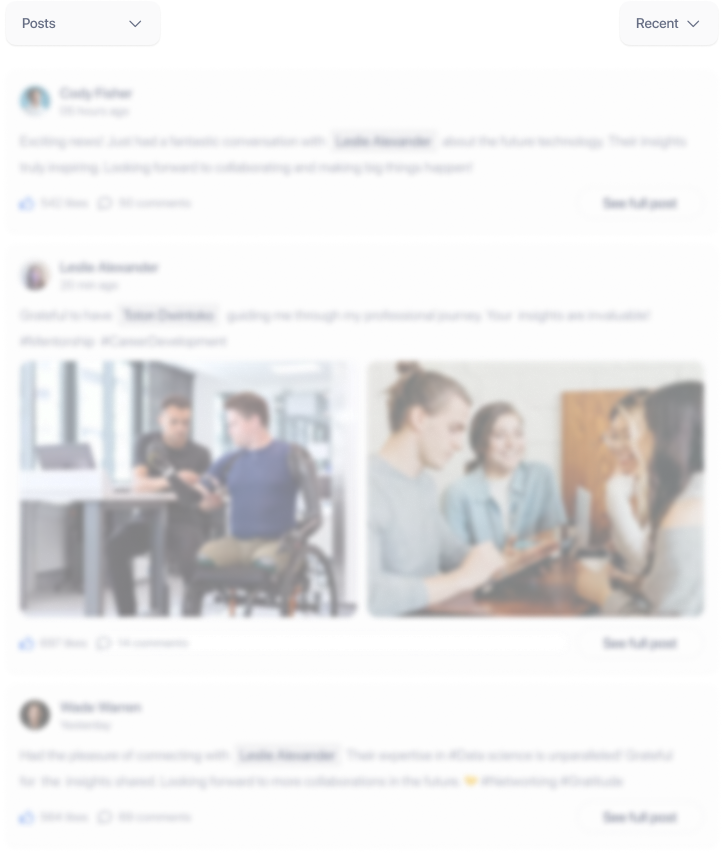