Fabián Azofeifa Trejos
After Sales Manager at Tractomotriz, S.A.- Claim this Profile
Click to upgrade to our gold package
for the full feature experience.
-
Spanish Native or bilingual proficiency
-
English Full professional proficiency
-
Italian Elementary proficiency
Topline Score
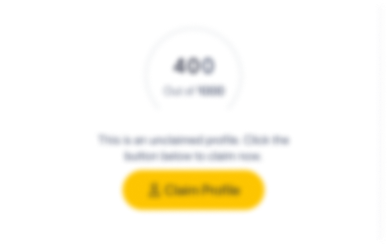
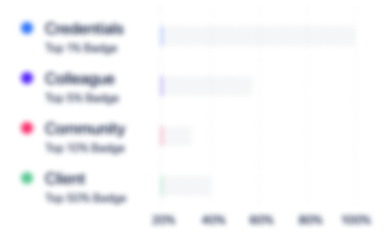
Bio


Experience
-
Tractomotriz, S.A
-
Costa Rica
-
Machinery Manufacturing
-
1 - 100 Employee
-
After Sales Manager
-
Mar 2022 - Present
In charge of the company's After Sales department, helping to guarantee excellence in the services offered in accordance with customer expectations, aligned with the policies of the represented brands meeting the highest quality standards, as well as the achievement of goals, budgets and objectives set by the organization, in coordination with all the departments involved. Likewise, foster a favorable environment of company-customer relationship that allows the represented brands to become market benchmarks, promoting an excellent service experience. Show less
-
-
-
Bioplus Care S.A
-
Costa Rica
-
Pharmaceutical Manufacturing
-
1 - 100 Employee
-
Logistics & Operations Manager
-
Aug 2021 - Oct 2021
In charge of forming the Operations and Logistics department of the company, and generating the guidelines for its optimal operation. In addition, perform the typical tasks of the area such as the coordination of imports, storage, distribution, everything that the value chain entails In charge of forming the Operations and Logistics department of the company, and generating the guidelines for its optimal operation. In addition, perform the typical tasks of the area such as the coordination of imports, storage, distribution, everything that the value chain entails
-
-
-
MPC - Comercial de Potencia y Maquinaria
-
San Jose, Costa Rica
-
Product Support Manager - After Sale Department
-
Aug 2015 - Feb 2021
As Product Support Manager I am in charge of 3 key areas of the After Sales Department: Service, Parts, and Commercial. The organization of the service facility and human resource to provide optimal customer service, the logistics of importing spare parts and maintain adequate stock and the trading strategy to increase sales of parts and services are some of my primary functions. During the time in my job the department has increased sales, improved profitability and the company has emerged as a benchmark in the industry. Show less
-
-
-
Constructora MECO
-
Construction
-
700 & Above Employee
-
Transportation Operations Manager - Strategic Business Unit - Machinery
-
Nov 2013 - Sep 2014
Within the Strategic Business Unit of Machinery of Meco Company, I was in charge of the Department of Transport. Cost control, budget execution, compliance schedules, personnel management, supplier relationship and continuous improvement are just some of the functions performed. Some of the accomplishments achieved: restructuring the department by decreasing the amount of administrative staff by unifying functions. Increased mechanical availability of the fleet by implementing preventive maintenance programs and planned corrective repairs. Budgetary compliance with the number of services rendered and operating costs. 5's program implementation in the workshop and the Fleet. Show less
-
-
-
-
Operations and Logistics Manager - Sales and Rent Department
-
Sep 2011 - Oct 2013
As Head of Operations and Logistics, I was in charge of the storage and distribution of machinery represented by the company. In logistics, ensuring timely delivery of products was vital always looking for a reduction of the costs. I was in charge of transport, inventory control, storage and delivery of equipment. Some of the accomplishments achieved: reduced inventory which generated warehousing costs reduction. Reducing costs through effective negotiations with Customs agencies in the process of importing new equipment. Improving the storage fees with bonded warehouses. Creation of a Repair Plan in conjunction with the Service Department to ensure timely delivery of equipment for both new machines and machines for rent. Improved use of own transport equipment reducing outsourcing increasing profitability in this area. Show less
-
-
Operations Manager - Service Department (John Deere Work Shop)
-
Aug 2010 - Sep 2011
As Service Operations Manager I had the responsibility of managing all activities of the Service Department for John Deere´s brand, contributing to the efficient production of services provided. Among the functions performed are the development of operational strategies. Design of new service products. Planning and control. Continuous improvement of the performance of the department. Some of the accomplishments achieved: increased sales of service through new products. Reduction of operating costs by optimizing the use of materials and spare parts. Training program for technical staff looking to increase the efficiency of work. Show less
-
-
Technical Communicator, Service Department
-
Aug 2008 - Sep 2010
As a Technical Communicator, I was responsible for solving complex problems that occur with machinery represented by the company. These complex cases were analyzed according to technical manuals and factory recommendations. The Technical Communicator maintains direct communication with the engineering department of the factory. Some of the accomplishments achieved: reduced customer complaints, increased post-sales satisfaction, and training technical staff.
-
-
-
Holcim Costa Rica
-
Limón, Costa Rica
-
Maintenance Manager - Construction Aggregates Department
-
Apr 2007 - May 2008
As Maintenance Manager, I was in charge of preventive, predictive and corrective programs of the production plant of construction aggregates. Within the functions of the position, there was the monitoring of the condition of the equipment and the elaboration of indicators concerning production. Some of the accomplishments achieved: increased mechanical equipment availability, increased productivity for both mobile and stationary equipment by incorporating predictive maintenance programs. As Maintenance Manager, I was in charge of preventive, predictive and corrective programs of the production plant of construction aggregates. Within the functions of the position, there was the monitoring of the condition of the equipment and the elaboration of indicators concerning production. Some of the accomplishments achieved: increased mechanical equipment availability, increased productivity for both mobile and stationary equipment by incorporating predictive maintenance programs.
-
-
-
Kimberly Clark de Costa RicaU
-
Heredia, Costa Rica
-
University Internship
-
Jan 2006 - Jan 2007
Internship in order to obtain the Lic degree in Industrial Maintenance engineering Evaluation and Redesign of the compressed air system of plant production of paper. Implementation of a program Reliability Centered Maintenance “RCM” in the production line of toilet paper. Achievements: The redesign of the compressed air allows energy costs for leaks and pressure drops decrease considerably and, in turn, facilitates system maintenance. The RCM maintenance program determined that the maintenance done previously was merely preventive and corrective, without an analysis of the existing failure modes to determine the causes of the failures. Show less
-
-
Education
-
Formato Educativo Escuela de Negocios
Master of Business Administration - MBA, Finance -
Universidad Latinoamericana de Ciencia y Tecnología
Master of Business Administration with emphasis in Operations Management, Business Administration and Management, General -
Instituto Tecnológico de Costa Rica
Industrial Maintenance Engineer, Engineering
Community
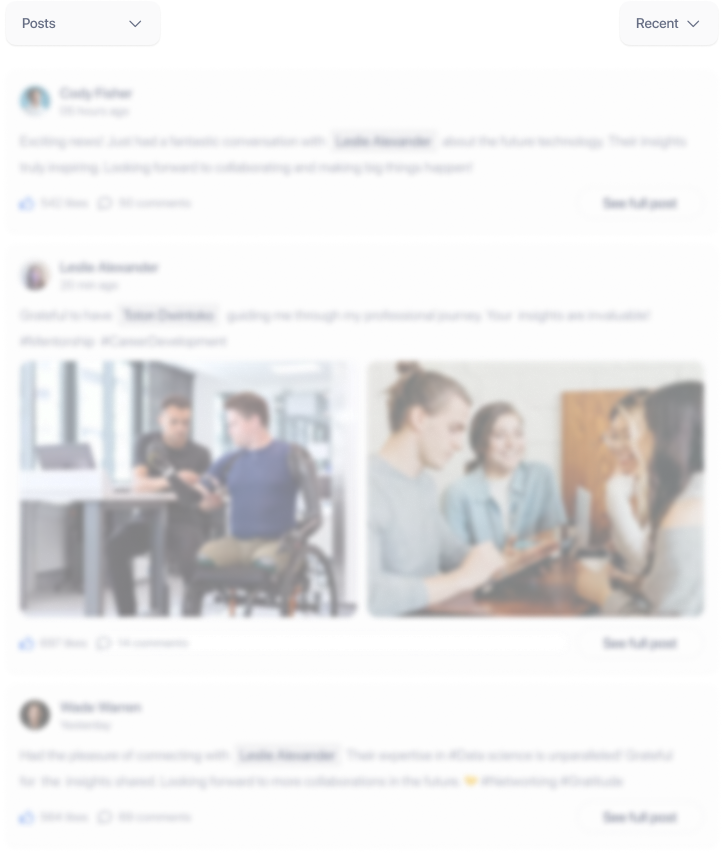