Ayhan Yunuslar
Human Resources Training Development Manager at Vatan Pres Automotive Stamping and Tooling- Claim this Profile
Click to upgrade to our gold package
for the full feature experience.
-
İngilizce Professional working proficiency
-
Türkçe Native or bilingual proficiency
Topline Score
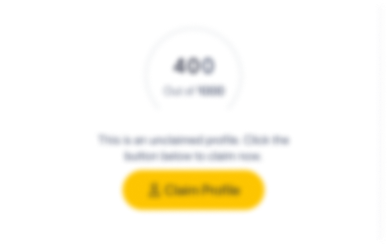
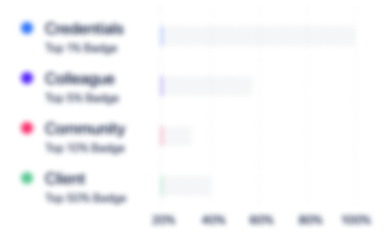
Bio


Credentials
-
Lean 6 Sigma Green Belt
Borusan HoldingFeb, 2018- Sep, 2024 -
ISO 14001 Internal Auditeur
Bureau Veritas TurkeyJan, 2018- Sep, 2024 -
ISO 50001 Internal Auditeur
SGS ConsultingNov, 2017- Sep, 2024 -
Industry 4.0
MESS Türkiye Metal Sanayicileri SendikasıSep, 2017- Sep, 2024 -
ISO 9001 Internal Auditeur
Bureau Veritas TurkeyJun, 2017- Sep, 2024 -
Coaching
MESS Türkiye Metal Sanayicileri SendikasıApr, 2017- Sep, 2024 -
Stress and Time Management
MESS Türkiye Metal Sanayicileri SendikasıApr, 2017- Sep, 2024 -
Refa Certificate
MESS Türkiye Metal Sanayicileri SendikasıApr, 2013- Sep, 2024 -
Inovation for Production
KalDer, Türkiye Kalite DerneğiApr, 2011- Sep, 2024 -
Occupational Safety Specialist A Class
T.C. Çalışma ve Sosyal Güvenlik Bakanlığı - Turkish Labour and Social Security MinistryJan, 2004- Sep, 2024 -
Trainer Training
BNB training+ consultancySep, 2010- Sep, 2024
Experience
-
Vatan Pres Automotive Stamping and Tooling
-
Türkiye
-
Automotive
-
1 - 100 Employee
-
Human Resources Training Development Manager
-
Jun 2021 - Present
Organizing Training and Development, Career Management, Performance Management, Talent Management studies. Conducting white collar recruitment studies. Monitoring of Human Resources processes. Conducting job analysis studies. Responsible for the human resources processes of the four factories in different locations. Organizing Training and Development, Career Management, Performance Management, Talent Management studies. Conducting white collar recruitment studies. Monitoring of Human Resources processes. Conducting job analysis studies. Responsible for the human resources processes of the four factories in different locations.
-
-
-
A-Plas
-
Türkiye
-
Automotive
-
100 - 200 Employee
-
Human Resources Responsible
-
Oct 2019 - Jun 2021
Carrying out all human resources processes of approximately 600 people in accordance with the labor law. White-collar, blue-collar business negotiations. Managing the recruitment and orientation process. Management of training and development activities of all personnel. Development of human resources solutions aimed at expanding the corporate culture. Management of employee satisfaction studies. Designing activities to increase employee satisfaction based on the feedback received. Managing company recognition appreciation system. Making presentations to senior management about human resources activities. Show less
-
-
-
Borusan Mannesmann
-
Türkiye
-
Mining
-
500 - 600 Employee
-
Human Resources Training Development
-
Nov 2016 - Dec 2018
Determination of training needs of employees. Creating of training plan. Taking training according to the training plan. Technical trainings, legal requirements trainings, quality trainings, lean manufacturing training organizing. Creation of talent development matrices, development of employee talents. Managing the company suggestion system. Determining, organizing and following the effects of the suggestions to the company. Cooperation with High Schools for taking intern. Besides, the management of Lean 6 sigma project as Expert Green Belt. Giving training to employees about Quality, Method, Professional and Technical issues and Personal development. Analysis of leadership characteristics of production leaders. Accordingly, determination of a personal development program. Performing necessary actions for human resources training processes in ISO 9001, ISO 14001, ISO 50001 audits. Show less
-
-
-
Beyçelik Gestamp
-
Motor Vehicle Manufacturing
-
700 & Above Employee
-
Occupational Safety Health Specialist (A Class)
-
Jun 2015 - Nov 2016
Risk analyzing in the company and determination of actions to be taken. Giving occupational health and safety training to operators. Periodic meetings of occupational safety board. Root cause analysis for work accidents and generalization of actions taken. Work on the occupational safety activities of WCM system S pillar. Risk analyzing in the company and determination of actions to be taken. Giving occupational health and safety training to operators. Periodic meetings of occupational safety board. Root cause analysis for work accidents and generalization of actions taken. Work on the occupational safety activities of WCM system S pillar.
-
-
-
-
Method Unit Responsible
-
Jun 2008 - Feb 2015
Time studies, Value Stream Mapping (VSM), Poka Yoke, JIT, SMED, Layout, Process Improvement activities, Ergonomics analysis and follow-up of actions related to this, Drawing and layout of the factory layout. He carried out line balancing, kaizen and continuous improvement works, and led the team of time studies supervisor and machine adjustment technicians. I have Refa 1 and Refa 2 international sertificate about Method and time studies. He also worked as an occupational safety specialist. Time studies, Value Stream Mapping (VSM), Poka Yoke, JIT, SMED, Layout, Process Improvement activities, Ergonomics analysis and follow-up of actions related to this, Drawing and layout of the factory layout. He carried out line balancing, kaizen and continuous improvement works, and led the team of time studies supervisor and machine adjustment technicians. I have Refa 1 and Refa 2 international sertificate about Method and time studies. He also worked as an occupational safety specialist.
-
-
-
-
Method and Production Planning Chief
-
Nov 2006 - Mar 2008
Production time measurement, time study forms to be filled. Lay Out change work. Line balancing studies. Coordinate kaizen activities on production lines. Production plan according to customer orders. Preparation of capacity reports and submission to management. Planning of production processes. He worked in production improvement works. Production time measurement, time study forms to be filled. Lay Out change work. Line balancing studies. Coordinate kaizen activities on production lines. Production plan according to customer orders. Preparation of capacity reports and submission to management. Planning of production processes. He worked in production improvement works.
-
-
Education
-
Marmara Üniversitesi
Lisans, Makine Öğretmenliği
Community
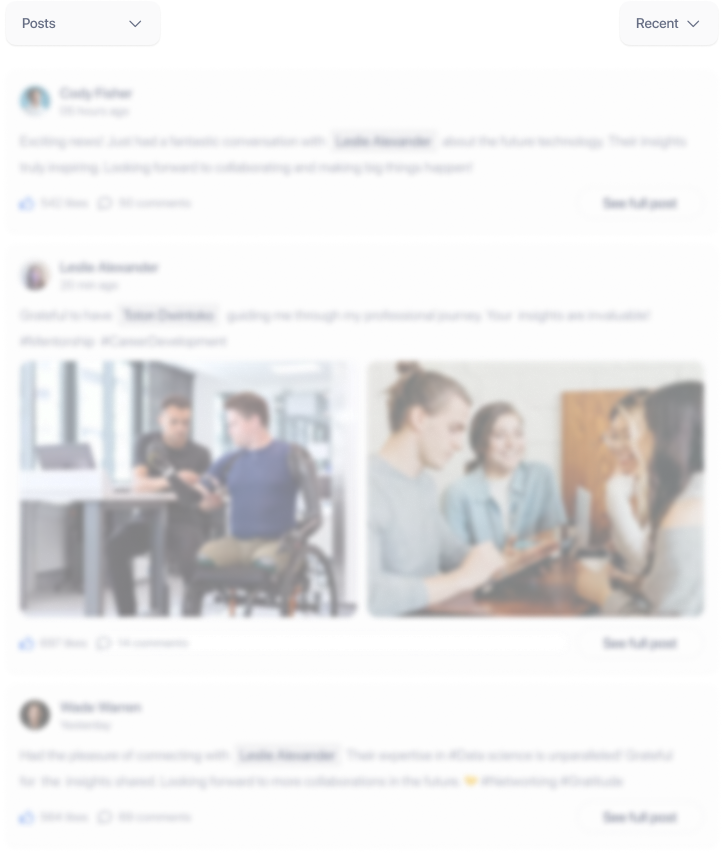