August Spencer
CFO & COO at INDEXX- Claim this Profile
Click to upgrade to our gold package
for the full feature experience.
Topline Score
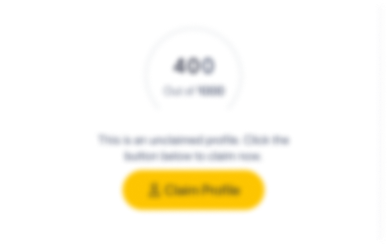
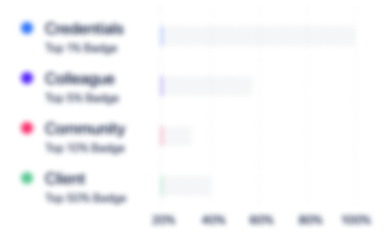
Bio


Experience
-
INDEXX
-
United States
-
Printing Services
-
1 - 100 Employee
-
CFO & COO
-
Sep 2019 - Present
Greenville, South Carolina Area - INDEXX Commercial Printing INDEXX prides itself on being the best commercial printer in the Upstate of South Carolina. Based in Greenville, SC, we offer everything from offset and digital printing to design, binding, mailing, and fulfillment services. Recognized by both the printing industry and our clients for the quality of our work, INDEXX has been the top choice for printing and customer service since 1993.
-
-
-
Hubbell Lighting
-
United States
-
Appliances, Electrical, and Electronics Manufacturing
-
300 - 400 Employee
-
Hubbell Lighting Controller
-
Apr 2007 - Oct 2016
Greenville, South Carolina Area - Responsible for all aspects of general accounting, operational accounting, accounts payable, accounts receivable, and fixed assets for this $930M platform. - Manage 4 direct reports and 54 professionals across the above mentioned areas. - Over an 18 month period, consolidated the accounting practices of 4 businesses into a single and common view of GAAP. This allowed for the introduction of a single methodology concept to be used by all brands and businesses (accrual calculations and… Show more - Responsible for all aspects of general accounting, operational accounting, accounts payable, accounts receivable, and fixed assets for this $930M platform. - Manage 4 direct reports and 54 professionals across the above mentioned areas. - Over an 18 month period, consolidated the accounting practices of 4 businesses into a single and common view of GAAP. This allowed for the introduction of a single methodology concept to be used by all brands and businesses (accrual calculations and methodologies for freight, bad debt, utilities, excess and obsolete inventories, warranty, A/R deductions, etc). - Centralized the general accounting, accounts payable, fixed assets, and accounts receivables functions in one central area. Migrated from “generalist” to “specialists” in each of the functional areas which lead to more efficient and consistent results. - Segregated and separated the functions from General Accounting, Operational Accounting, and Financial Planning & Analysis such that each group has their own areas of expertise and responsibilities. Segregation of duties assured accurate and timely financial results being reported. - Developed (and partnered with the VP of Operations) financial models that lead to the transfers or closures of 7 operating locations that are yielding over $19M in annual operating profits. - Rolled in and absorbed the accounting practices of 8 unique acquired businesses over a 6 year period. Once converted into SAP, all of the financial functions at the remote locations were absorbed (supporting the centralized model) with the exception of cost accounting. - Reduced the financial closing cycle from 4 long days to 2 normal days over a 2 year period. - Conduct monthly plant reviews with plant managers and plant cost managers to analyze the closed month performance and review current month forecast. Show less
-
-
-
Ingersoll Rand
-
United States
-
Industrial Machinery Manufacturing
-
700 & Above Employee
-
Oracle Implementation Finance Lead
-
Nov 2004 - Apr 2007
Davidson, NC - Designed a Multi-Org Financial model and built a Global Reference Model to be used by 26 manufacturing locations, 55 Service Centers, and 12 Sales and Marketing Offices for the Industrial Technologies Sector Oracle Conversion Project. - Responsible for directing, coordinating, testing and implementing accounting related modules and activities associated with implementing at pilot location (Unicov, Czech Republic). - Responsible to reviewing all business processes that affect… Show more - Designed a Multi-Org Financial model and built a Global Reference Model to be used by 26 manufacturing locations, 55 Service Centers, and 12 Sales and Marketing Offices for the Industrial Technologies Sector Oracle Conversion Project. - Responsible for directing, coordinating, testing and implementing accounting related modules and activities associated with implementing at pilot location (Unicov, Czech Republic). - Responsible to reviewing all business processes that affect accounting in an effort to accomplish 3 main objectives: Standardize, Simplify, and Centralize as many functions as possible to attain maximum benefits from implementing Oracle. General Accounting, Accounts Payable, Credit and Collections, and Cash Applications were modified to be managed from a single location for the USA. - Introduced a complete redesign of the sector’s general ledger account structure (segments, values, and a common chart of accounts), consolidated 19 entities into 3 reporting entities in the USA, and provided a comprehensive Oracle Instance capable of handling all current and future needs for a world wide consolidation at the sector level. Consolidations can be performed vertically or horizontally. - Modules reviewed and or implemented: General Ledger, Accounts Receivable (cash applications and Credit Management), Accounts Payable, Fixed Assets, Project Accounting, Costing, Inventory costing, Distributor Net Costing (DN), Customer Master, Order Management, Manufacturing Shop floor, and Materials/Procurement. - Planed, coordinated, and lead the execution of the migration of the North America IR Corporate Oracle Instance to the Industrial Technologies Oracle Instance.
-
-
Division Operations Controller
-
May 2002 - Oct 2004
Annandale, NJ - Assisted in the development of a global manufacturing strategy that consolidated the organization structure across 6 manufacturing facilities that reduced operating costs by $46M in a 5 year period. Tasks ranging from analyzing outsourcing of non core processes, re-sourcing and localization of material purchases, plant closure costs, moving costs, severance calculations, and several other financial and operational reviews. - Assisted in the creation and analysis of the division’s Plant… Show more - Assisted in the development of a global manufacturing strategy that consolidated the organization structure across 6 manufacturing facilities that reduced operating costs by $46M in a 5 year period. Tasks ranging from analyzing outsourcing of non core processes, re-sourcing and localization of material purchases, plant closure costs, moving costs, severance calculations, and several other financial and operational reviews. - Assisted in the creation and analysis of the division’s Plant Rationalization plan. The plan was presented and subsequently approved by the Board of Directors. CEO, Herb Henkel, stated that the presentation was the best, well thought out, detailed, presented plan he had ever seen. - Footprint project executed trough 2005 realized $28M in annual savings through the closure of 3 plants and transfers of 6 manufacturing lines within the division. - Responsible for formulating, establishing, rolling out, and reviewing Monthly and Quarterly results from a common set of Operational and Financial reports for the Productivity Solutions Division. Reports included: Plant Score card (49 different data points), Plant Expenses and Absorption review, Production Volume and Mix Changes, Direct and Indirect Material Productivity, and Inventory Changes to name a few. These reports were intended for tracking all 11 manufacturing facilities and 3 Distribution Centers world wide. My responsibilities included the consolidation, review, analysis, and recommendations for improving performance across the division. Published summary reporting of the performance of the division on a monthly and quarterly basis. Quarterly reviews were conducted with the Division President, Division CFO, and Plant Managers from all locations. - Assisted the two China manufacturing locations migrate from an actual costing methodology to the corporate approved Standard Costing method (Guilin and Jintan, China locations).
-
-
Distribution & Global Logistics Center Controller
-
Jun 1999 - Apr 2002
White House, TN - Responsible for general accounting, inventory control, cash applications, claims, and facility departments (4 direct reports, 22 total headcount). - Responsible for all financial reporting for the White House distribution center operations ($145 million) as well as consolidation and reporting Revenue and COGS for all USA manufacturing locations ($320 million total Revenue). - Coordinated and corrected 3 independent databases within the division. Corrections included proper mapping of… Show more - Responsible for general accounting, inventory control, cash applications, claims, and facility departments (4 direct reports, 22 total headcount). - Responsible for all financial reporting for the White House distribution center operations ($145 million) as well as consolidation and reporting Revenue and COGS for all USA manufacturing locations ($320 million total Revenue). - Coordinated and corrected 3 independent databases within the division. Corrections included proper mapping of all process driven transactions in a manufacturing operation that posts to the general ledger. Corrections resulted in OI recognition of over $1.2 million within twelve months. - Introduced and implemented sound accounting practices that allowed for proper GAAP compliance as well as timely and accurate financial reporting for the division. - Responsible for cash applications for division’s domestic sales. - Responsible for processing all A/R adjustments for the Productivity Solutions Division emanating from customer returns, claims, and warranty complaints ($13 million in credits per year). - Improved inventory accuracy to 99.996% by establishing sound procedures associated with the Cycle Counting Program . - Cleaned and reconciled all balance sheet accounts as well as all intercompany accounts receivable and payable within a one-year period. All accounts are currently reconciled within 30 days after each month end closing. Corrections resulted in OP recognition of an additional $2.1 million. - Responsible for coordinating, maintaining, and changing standard costs for all items in the division’s main database (over 95,000 active part numbers, 155,000 in total) for all 6 USA division locations. Transfer pricing for Europe, Asia, and Latin American for division is coordinated through the White House location.
-
-
-
-
Plant Controller
-
Mar 1998 - May 1999
Knoxville, TN - Responsible for all financial reporting for the Knoxville manufacturing and distribution operations ($106 million), which includes the distribution of fully assembled transmission units for the “Lineset” operation for Navistar in the USA and Canada, Freightliner, Mack and other customers. - Upgraded all accounting and operational systems. Convert from a semi-manual process to a fully automated and integrated accounting and manufacturing system. Upgrade was conducted from an earlier… Show more - Responsible for all financial reporting for the Knoxville manufacturing and distribution operations ($106 million), which includes the distribution of fully assembled transmission units for the “Lineset” operation for Navistar in the USA and Canada, Freightliner, Mack and other customers. - Upgraded all accounting and operational systems. Convert from a semi-manual process to a fully automated and integrated accounting and manufacturing system. Upgrade was conducted from an earlier version of QAD, Manufacturing PRO (7.3) to the most recent release (8.5) that was Y2K compliant. - Introduced departmental costing system for future use in an ABC costing environment. - Introduced improved costing accounting systems, modified existing routings and conducted new time studies to reflect more accurate manufacturing costs for more than 900 manufactured, sub-assembled, and finished assembled goods. These parts range from a single conversion of a raw component to a bill of material with over 100 components with multiple subassemblies (5 levels). - Created new corporate chart of accounts that was implemented at all SPICER-DANA manufacturing and distribution plants. New format allows for faster and consistent financial reporting. The change in chart of accounts was the 2nd change in less than a year, which presented added challenges in the upgrade implementation process. Show less
-
-
-
MAHLE
-
Germany
-
Motor Vehicle Manufacturing
-
700 & Above Employee
-
AR Manager, Systems Analyst, Internal Auditor
-
Jan 1994 - Mar 1998
Morristown, TN - Responsible for all trade and inter-company receivable ($250 million). Directed complete change of accounting procedures related to the billing and recording of corporate trade receivable, inter-company receivable, and customer service order entry activities. Wrote policies and procedures to support new methods. - Developed and designed a Cost Recovery System and a Return Authorization System. Responsibilities included implementing the new systems, training all personnel involved in… Show more - Responsible for all trade and inter-company receivable ($250 million). Directed complete change of accounting procedures related to the billing and recording of corporate trade receivable, inter-company receivable, and customer service order entry activities. Wrote policies and procedures to support new methods. - Developed and designed a Cost Recovery System and a Return Authorization System. Responsibilities included implementing the new systems, training all personnel involved in the process, and the written documentation of the policies and procedures. - QS9000 operational auditor. Shop floor and office audits. - Internal auditor responsibilities included auditing our Headquarters location in Morristown TN, and our subsidiary location in Saltillo, Mexico. Audit scope included finished goods, work-in-process inventories, inventory turnover and valuations, cash and cash equivalents, accounts receivable, accounts payable, and payroll. - General Ledger maintenance, closing entries, and reconciliation of sales and distributions, accounts receivable, fixed assets and other current asset accounts. - Supervise all accounting personnel under the Treasurer: responsibilities include direction and support concerning operations management, audits, month end closings, accounts receivable, system integration, security and recommendations to improve internal controls. - Maintain knowledge of new data processing concepts and techniques to support sound conceptual thinking in relation to all aspects of accounting, treasury and operations management. Show less
-
-
-
The R.A. Siegel Company
-
United States
-
Wholesale
-
1 - 100 Employee
-
Credit and Collections Manager
-
Sep 1990 - Jan 1993
Atlanta, GA - Responsible for over 400 accounts in assigned territory with $15 million annual sales. - Improved aging reports from 68% to 93% current while helping increase sales in assigned territory in a 1 year period. - Maintained the lowest bad debt write off of less than 0.15% of sales for the Knoxville, Chattanooga, Dalton and Tennessee Tri-Cities area. - Nominated and awarded "Employee of the Quarter" in the third quarter in 1992. - Conducted credit and collection seminars to customers… Show more - Responsible for over 400 accounts in assigned territory with $15 million annual sales. - Improved aging reports from 68% to 93% current while helping increase sales in assigned territory in a 1 year period. - Maintained the lowest bad debt write off of less than 0.15% of sales for the Knoxville, Chattanooga, Dalton and Tennessee Tri-Cities area. - Nominated and awarded "Employee of the Quarter" in the third quarter in 1992. - Conducted credit and collection seminars to customers of the R.A Siegel Company. Seminar locations included Atlanta, Dalton, Macon, Knoxville, Nashville, and Chattanooga. Show less
-
-
Education
-
The University of Tennessee at Chattanooga
Masters, Manufacturing Operations -
University of Tennessee, Knoxville
BA, Accounting -
University of Tennessee, Knoxville
BA, Finance
Community
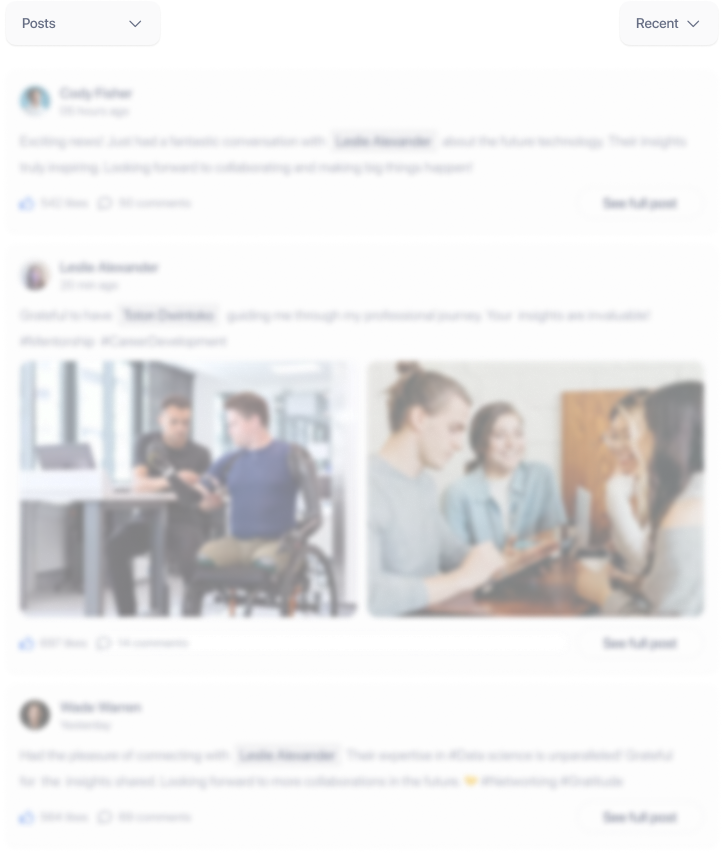