Atakan Ortagedik
Quality Manager at Response Ortho- Claim this Profile
Click to upgrade to our gold package
for the full feature experience.
Topline Score
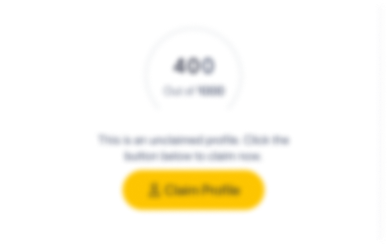
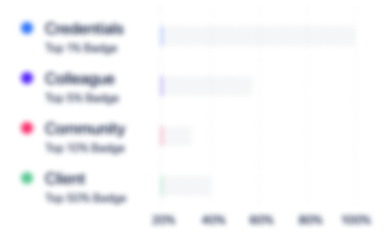
Bio


Experience
-
Response Ortho
-
Türkiye
-
Medical Equipment Manufacturing
-
1 - 100 Employee
-
Quality Manager
-
Dec 2020 - Present
I transferred to Wishbone Medical Company, a US company, in order to accelerate international work and career development. I am the Quality Control Manager at Response Ortho, a US company, Wisbone Medical Turkey production factory. Response Ortho company produces medical parts with machining method. Basically, I work on improving the approval files of the products according to the quality requirements and monitoring and improving the quality control activities for the company. I do documentation and process improvement studies such as DHR, FAI, DFMEA, Kaizen,Gemba and continuous improvement
-
-
-
NETA Elektronik AS
-
Türkiye
-
Telecommunications
-
1 - 100 Employee
-
Quality Manager
-
Sep 2019 - Dec 2020
I transferred to Neta Elektronik company in order to create a new step in my career. As the Quality Manager at Neta Elektronik, I was responsible for managing the defense industry quality processes and completing the quality processes of products according to customer requests such as Baykar, Aselsan and Roketansan. I transferred to Neta Elektronik company in order to create a new step in my career. As the Quality Manager at Neta Elektronik, I was responsible for managing the defense industry quality processes and completing the quality processes of products according to customer requests such as Baykar, Aselsan and Roketansan.
-
-
-
ARaymond Network
-
France
-
Manufacturing
-
700 & Above Employee
-
Quality and Laboratory Engineer-Leader
-
Mar 2017 - Sep 2019
I transferred to ARaymond as Project Quality Leader. In my team; There were 1 project quality engineer, 1 PPAP responsible engineer, 3 laboratory specialists, 3 quality operators. I was responsible for the process from the start of the project to the mass production of the part. My main processes are; TS 16949 / AIAG, ISO 9001, OHSAS 18001, ISO 14001, customer audits, supplier selection and audits, 8D, tier 1s and PPAP by OEMs. Team development and training plan, quality plan, laboratory activities, FMEA, sub-supplier issue, incoming inspection and storage, quality assurance with all procedures, quality procedure preparation, MSA, SPC, Cpk requirements, control gauges and fixtures, equipment usage, monitoring and coordination of processes I was providing. In summary, I had good experiences with automation requirements such as TS16949 / AIAG, VDA 6.3, FMEA, PPAP, MSA, SPC, 8D, control plans, customer portfolio utilization, team management, team planning, investment planning, customer satisfaction, laboratory activities. Supplier issues, internal documentation, process audit, internal audit, quality procedure preparation, customer audits, R@R process, support proposal preparation, negotiating with customers and suppliers on all issues, quality KPIs, team KPIs. I have a lot of time connection and good communication with Tier1s, Ford, Toyota, Daimler, Fiat, Reanult, GM, JLR, Volvo, VW, BMW. I visited the locations of suppliers and customers many times, including Portugal twice, Bulgaria twice, Italy twice, Germany once, Japan once, and France four times. I have many problem solving and transfer authorities in the international arena.
-
-
-
Yazaki Europe
-
Germany
-
Motor Vehicle Manufacturing
-
700 & Above Employee
-
Quality Leader
-
Jun 2013 - Mar 2017
> SQA Leader for Toyota, Daimler, Ford, Fiat > Customer Quality and Resident Engineer Leader for Ford OEM My automotive career started in Yazaki as a Supplier Quality Engineer and I had a team of 5 quality operators, 1 expert in the incoming inspection department. I was responsible for problem solving communication with over 100 suppliers, supplier audit and approval, PPAP preparation and approval, quality related to weekly and monthly reports. About 8 months later, I took over the position of Ford Customer Quality Leader and thus received the title of Quality Leader. In my responsibility; There were 1 customer quality engineer, 1 quality specialist, 1 resident engineer, 25 quality technicians. I have experience in teamwork and management, project management and quality tools, and quality negotiations with the OEM. I was responsible for IATF16946 / AIAG, ISO 9001, OHSAH 18001, ISO 14001, internal audit, team training, quality planning and client auditing.
-
-
Education
-
Sakarya Üniversitesi
2,47, Metallurgy and Material Engineer
Community
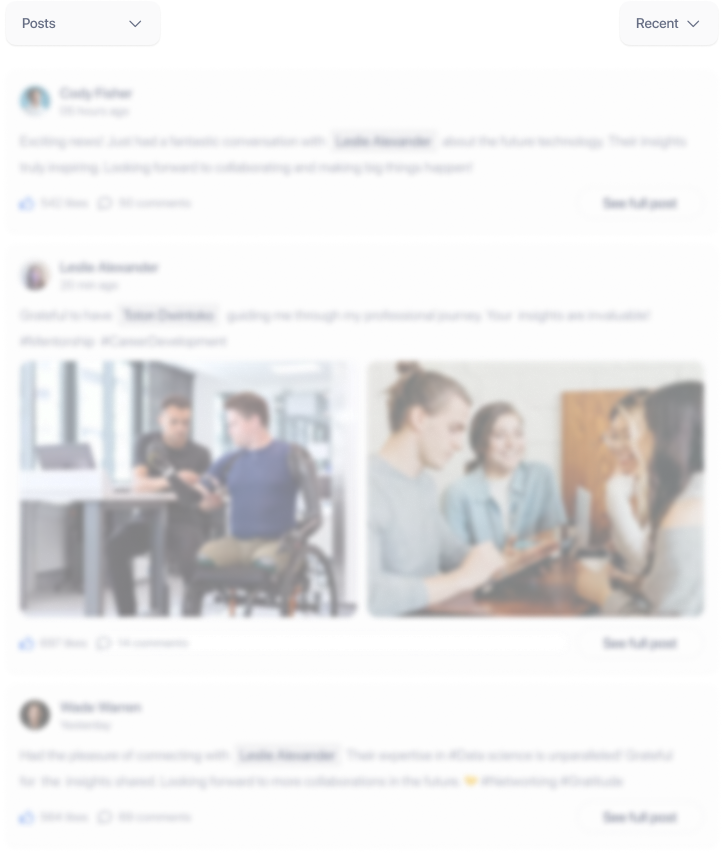