Ashish Ingole
HR Manager at Catalydd Engineering and Consulting- Claim this Profile
Click to upgrade to our gold package
for the full feature experience.
Topline Score
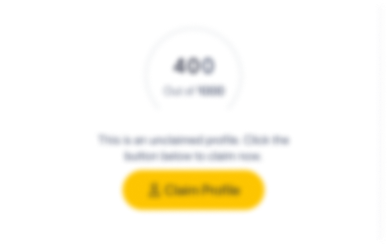
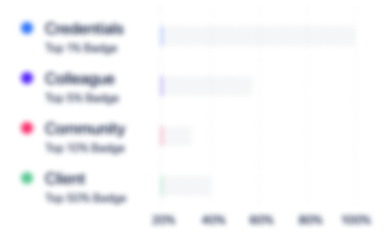
Bio


Credentials
-
Certified Internal Auditor (CIA) for IATF 16949:2016
Formel D India Pvt. Ltd.Apr, 2020- Nov, 2024 -
Certified Internal Auditor (CIA) for ISO 9001:2015
Formel D India Pvt. Ltd.Mar, 2020- Nov, 2024 -
Lean Six Sigma Green Belt
Benchmark Six SigmaJan, 2018- Nov, 2024 -
Lean Six Sigma Yellow Belt
Benchmark Six SigmaJan, 2018- Nov, 2024
Experience
-
Catalydd
-
India
-
Engineering Services
-
1 - 100 Employee
-
HR Manager
-
Oct 2022 - Present
Catalydd "Engineering" Division Is Engaged In Providing Quality Management Services Across Automotive & Engineering Sectors . Catalydd "Consulting" Division Helps Overseas Companies To Manage Their Business In India & Supports Start-ups,SMES For their Business/Transformation Journey.Catalydd "Engineering" Division Is Engaged In Providing Quality Management Services Across Automotive & Engineering Sectors . Catalydd "Consulting" Division Helps Overseas Companies To Manage Their Business In India… Show more Catalydd "Engineering" Division Is Engaged In Providing Quality Management Services Across Automotive & Engineering Sectors . Catalydd "Consulting" Division Helps Overseas Companies To Manage Their Business In India & Supports Start-ups,SMES For their Business/Transformation Journey.Catalydd "Engineering" Division Is Engaged In Providing Quality Management Services Across Automotive & Engineering Sectors . Catalydd "Consulting" Division Helps Overseas Companies To Manage Their Business In India & Supports Start-ups,SMES For their Business/Transformation Journey. Skills: Human Relationship Management · Operation Management · Quality Management · Leadership · Project Management Show less Catalydd "Engineering" Division Is Engaged In Providing Quality Management Services Across Automotive & Engineering Sectors . Catalydd "Consulting" Division Helps Overseas Companies To Manage Their Business In India & Supports Start-ups,SMES For their Business/Transformation Journey.Catalydd "Engineering" Division Is Engaged In Providing Quality Management Services Across Automotive & Engineering Sectors . Catalydd "Consulting" Division Helps Overseas Companies To Manage Their Business In India… Show more Catalydd "Engineering" Division Is Engaged In Providing Quality Management Services Across Automotive & Engineering Sectors . Catalydd "Consulting" Division Helps Overseas Companies To Manage Their Business In India & Supports Start-ups,SMES For their Business/Transformation Journey.Catalydd "Engineering" Division Is Engaged In Providing Quality Management Services Across Automotive & Engineering Sectors . Catalydd "Consulting" Division Helps Overseas Companies To Manage Their Business In India & Supports Start-ups,SMES For their Business/Transformation Journey. Skills: Human Relationship Management · Operation Management · Quality Management · Leadership · Project Management Show less
-
-
-
Formel D India Pvt. Ltd.
-
Pune/Pimpri-Chinchwad Area
-
Engineer
-
Jan 2018 - Aug 2020
Project 3: Supplier Development for Foundation Brakes Manufacturing Ltd. Jalgaon. Reporting to Project Manager & working as Project Coordinator. Maintaining and monitoring project plans, project schedules, work hours, budgets and expenditures. Preparing necessary Monthly Audit Performance presentation for meetings. Ensuring projects adhere to frameworks and all documentation is maintained appropriately. Create a project management calendar for fulfilling each goal and… Show more Project 3: Supplier Development for Foundation Brakes Manufacturing Ltd. Jalgaon. Reporting to Project Manager & working as Project Coordinator. Maintaining and monitoring project plans, project schedules, work hours, budgets and expenditures. Preparing necessary Monthly Audit Performance presentation for meetings. Ensuring projects adhere to frameworks and all documentation is maintained appropriately. Create a project management calendar for fulfilling each goal and objective. Co-ordinating with Supplier, SQA of Customer & Formel D Auditor. Uploading the Audit reports on the Customer Portal. Follow up for root cause analysis & corrective actions against the observed NC’s during VDA 6.3 Audit with evidences. Project 2: Customer Relationship Management for Mahle Filter System India Ltd. Pune Reporting to Project Manager & heading team of 4 people. Preparation of Customer Visit Plan and interaction with customer on weekly/monthly basis. Receipt of Customer Complaints, review with CFT, provide instant suitable solution & implement CAPA with the help of Why-Why Analysis through 8D. Process Audit for assembly processes. Product Audit (Layout inspection, SST, Ash Content Test, GSM, Performance Test etc.) Customer Complaint updates on the Mahle Portal. Prepare & submit PPAP for customer i.e. Bajaj Auto Ltd. & Force Motors Ltd. for level 3. Sustenance Audit for the taken each corrective & preventive actions. Project 1: Product & Process Quality Improvement for Dana India Pvt. Ltd. Pune. Reporting to Project Manager & heading team of 15 people. Verification of process needed for QMS are established, implemented & maintained. Shift scheduling, manpower handling, training & guidance to inspector & auditors. Preparing and reviewing the Standard Operating Procedures, Working Instruction, PDI Check sheets & Dock Audit Check sheets. Review of Control Plan, Process Flow Diagram, PFMEA, Quality Alerts, and One Point Lesson. Show less Project 3: Supplier Development for Foundation Brakes Manufacturing Ltd. Jalgaon. Reporting to Project Manager & working as Project Coordinator. Maintaining and monitoring project plans, project schedules, work hours, budgets and expenditures. Preparing necessary Monthly Audit Performance presentation for meetings. Ensuring projects adhere to frameworks and all documentation is maintained appropriately. Create a project management calendar for fulfilling each goal and… Show more Project 3: Supplier Development for Foundation Brakes Manufacturing Ltd. Jalgaon. Reporting to Project Manager & working as Project Coordinator. Maintaining and monitoring project plans, project schedules, work hours, budgets and expenditures. Preparing necessary Monthly Audit Performance presentation for meetings. Ensuring projects adhere to frameworks and all documentation is maintained appropriately. Create a project management calendar for fulfilling each goal and objective. Co-ordinating with Supplier, SQA of Customer & Formel D Auditor. Uploading the Audit reports on the Customer Portal. Follow up for root cause analysis & corrective actions against the observed NC’s during VDA 6.3 Audit with evidences. Project 2: Customer Relationship Management for Mahle Filter System India Ltd. Pune Reporting to Project Manager & heading team of 4 people. Preparation of Customer Visit Plan and interaction with customer on weekly/monthly basis. Receipt of Customer Complaints, review with CFT, provide instant suitable solution & implement CAPA with the help of Why-Why Analysis through 8D. Process Audit for assembly processes. Product Audit (Layout inspection, SST, Ash Content Test, GSM, Performance Test etc.) Customer Complaint updates on the Mahle Portal. Prepare & submit PPAP for customer i.e. Bajaj Auto Ltd. & Force Motors Ltd. for level 3. Sustenance Audit for the taken each corrective & preventive actions. Project 1: Product & Process Quality Improvement for Dana India Pvt. Ltd. Pune. Reporting to Project Manager & heading team of 15 people. Verification of process needed for QMS are established, implemented & maintained. Shift scheduling, manpower handling, training & guidance to inspector & auditors. Preparing and reviewing the Standard Operating Procedures, Working Instruction, PDI Check sheets & Dock Audit Check sheets. Review of Control Plan, Process Flow Diagram, PFMEA, Quality Alerts, and One Point Lesson. Show less
-
-
-
Falco eMotors Inc.
-
United States
-
Electrical Equipment Manufacturing
-
1 - 100 Employee
-
Head of Operations
-
Jun 2014 - Oct 2017
• Reporting to CEO & General Manager. • Review of received work order, production planning, manpower planning according to requirement, interaction with Mechanical, Hardware & Software Design team for requirement finalization. • Material requirement planning, interaction with vendor for quantity, quality & price negotiation, identification & preparation of purchase orders for shortages. • Inward inspection, in process inspection and final inspection of parts received from vendor for… Show more • Reporting to CEO & General Manager. • Review of received work order, production planning, manpower planning according to requirement, interaction with Mechanical, Hardware & Software Design team for requirement finalization. • Material requirement planning, interaction with vendor for quantity, quality & price negotiation, identification & preparation of purchase orders for shortages. • Inward inspection, in process inspection and final inspection of parts received from vendor for invoice clearance as well as manufactured sub assembly / assembly for final quality approval. • Existing and New Vendor Development by showing analysis report from the collected data using quality tools. (Electronics & Mechanical). • Troubleshooting of all PCB’s, sub-assemblies, assemblies and Product’s. • Software & GUI functional testing & validation as per customer requirements with preparation of reports for the same. • Resolving non-conformance by taking appropriate Corrective Action and Preventive Action after identification of the root cause using Quality Tools with maintaining records for the same. • Implementation of KAIZEN and focus on cost reduction with improvement in quality. • Audit for Calibration of all equipment’s, 5S maintenance, Quality Management System and dispatch. • Preparing and reviewing the Standard Operating Procedures, Working Instruction, Quality Alerts, and One Point Lesson. • Training to the personnel to improve skill & productivity with proper documentation. • Receipt of customer complaints, review with concern departments, take appropriate CAPA, provide instant suitable solution & keeping records for the same. Show less • Reporting to CEO & General Manager. • Review of received work order, production planning, manpower planning according to requirement, interaction with Mechanical, Hardware & Software Design team for requirement finalization. • Material requirement planning, interaction with vendor for quantity, quality & price negotiation, identification & preparation of purchase orders for shortages. • Inward inspection, in process inspection and final inspection of parts received from vendor for… Show more • Reporting to CEO & General Manager. • Review of received work order, production planning, manpower planning according to requirement, interaction with Mechanical, Hardware & Software Design team for requirement finalization. • Material requirement planning, interaction with vendor for quantity, quality & price negotiation, identification & preparation of purchase orders for shortages. • Inward inspection, in process inspection and final inspection of parts received from vendor for invoice clearance as well as manufactured sub assembly / assembly for final quality approval. • Existing and New Vendor Development by showing analysis report from the collected data using quality tools. (Electronics & Mechanical). • Troubleshooting of all PCB’s, sub-assemblies, assemblies and Product’s. • Software & GUI functional testing & validation as per customer requirements with preparation of reports for the same. • Resolving non-conformance by taking appropriate Corrective Action and Preventive Action after identification of the root cause using Quality Tools with maintaining records for the same. • Implementation of KAIZEN and focus on cost reduction with improvement in quality. • Audit for Calibration of all equipment’s, 5S maintenance, Quality Management System and dispatch. • Preparing and reviewing the Standard Operating Procedures, Working Instruction, Quality Alerts, and One Point Lesson. • Training to the personnel to improve skill & productivity with proper documentation. • Receipt of customer complaints, review with concern departments, take appropriate CAPA, provide instant suitable solution & keeping records for the same. Show less
-
-
-
Minda Stoneridge Instruments Limited
-
Wellness and Fitness Services
-
100 - 200 Employee
-
Trainee Analyst Electronics
-
Aug 2011 - May 2012
• Reporting to HOD of Quality Assurance Department. • Receipt of line & warranty rejections, separation of rejection as per Customer name, tagging & storage of material in bin properly and maintain records for the same. • Review of customer wise rejection, separation of rejection depends on old & new issues, review of history for old issues with taken CAPA. • Implementation of CAPA to resolve the new quality issues with the help of Data Analysis, Why-Why Analysis and 8D. • Implement… Show more • Reporting to HOD of Quality Assurance Department. • Receipt of line & warranty rejections, separation of rejection as per Customer name, tagging & storage of material in bin properly and maintain records for the same. • Review of customer wise rejection, separation of rejection depends on old & new issues, review of history for old issues with taken CAPA. • Implementation of CAPA to resolve the new quality issues with the help of Data Analysis, Why-Why Analysis and 8D. • Implement 8D to find root cause of a problem, devise a short term fix and implement long term solution. • Audit for Calibration of all equipment’s, instruments, gauges & soldering stations. • Study for the improvement in ON going products & implementation through Kaizen. • Resolving the issues by adopting the systematic approach using the standard problem solving techniques. • Skillful document control and maintenance. Show less • Reporting to HOD of Quality Assurance Department. • Receipt of line & warranty rejections, separation of rejection as per Customer name, tagging & storage of material in bin properly and maintain records for the same. • Review of customer wise rejection, separation of rejection depends on old & new issues, review of history for old issues with taken CAPA. • Implementation of CAPA to resolve the new quality issues with the help of Data Analysis, Why-Why Analysis and 8D. • Implement… Show more • Reporting to HOD of Quality Assurance Department. • Receipt of line & warranty rejections, separation of rejection as per Customer name, tagging & storage of material in bin properly and maintain records for the same. • Review of customer wise rejection, separation of rejection depends on old & new issues, review of history for old issues with taken CAPA. • Implementation of CAPA to resolve the new quality issues with the help of Data Analysis, Why-Why Analysis and 8D. • Implement 8D to find root cause of a problem, devise a short term fix and implement long term solution. • Audit for Calibration of all equipment’s, instruments, gauges & soldering stations. • Study for the improvement in ON going products & implementation through Kaizen. • Resolving the issues by adopting the systematic approach using the standard problem solving techniques. • Skillful document control and maintenance. Show less
-
-
-
Intelux Electronics Pvt. Ltd.
-
India
-
Telecommunications
-
100 - 200 Employee
-
QA Engineer
-
Oct 2008 - Aug 2011
• Reporting to Plant In charge. • Supervise the Quality Assurance Department. • Co-ordinate with Design & Development, Customer Support Cell, Production, In process QA & Testing department for NPD. • All types of Product Testing & validation with preparation of records for the same. • Troubleshooting of all PCB’s and Product’s. • Audit for Calibration of all equipment, instruments, gauges & soldering instruments. • To plan, organize and lead various functions of quality… Show more • Reporting to Plant In charge. • Supervise the Quality Assurance Department. • Co-ordinate with Design & Development, Customer Support Cell, Production, In process QA & Testing department for NPD. • All types of Product Testing & validation with preparation of records for the same. • Troubleshooting of all PCB’s and Product’s. • Audit for Calibration of all equipment, instruments, gauges & soldering instruments. • To plan, organize and lead various functions of quality control and assurance to ensure compliance with outgoing quality standard specification and total customer satisfaction. • Continual improvements in Production related activities. • Arrange for dispatch of products/material as per PO. • Study for the improvement in ON going products & implementation. • Making sure that the quality related complaints are investigated and resolved. • Documentation for ISO 9001:2008. Show less • Reporting to Plant In charge. • Supervise the Quality Assurance Department. • Co-ordinate with Design & Development, Customer Support Cell, Production, In process QA & Testing department for NPD. • All types of Product Testing & validation with preparation of records for the same. • Troubleshooting of all PCB’s and Product’s. • Audit for Calibration of all equipment, instruments, gauges & soldering instruments. • To plan, organize and lead various functions of quality… Show more • Reporting to Plant In charge. • Supervise the Quality Assurance Department. • Co-ordinate with Design & Development, Customer Support Cell, Production, In process QA & Testing department for NPD. • All types of Product Testing & validation with preparation of records for the same. • Troubleshooting of all PCB’s and Product’s. • Audit for Calibration of all equipment, instruments, gauges & soldering instruments. • To plan, organize and lead various functions of quality control and assurance to ensure compliance with outgoing quality standard specification and total customer satisfaction. • Continual improvements in Production related activities. • Arrange for dispatch of products/material as per PO. • Study for the improvement in ON going products & implementation. • Making sure that the quality related complaints are investigated and resolved. • Documentation for ISO 9001:2008. Show less
-
-
Education
-
Dnyanganga Institute Of Career Empowerment and Research
Master of Business Administration - MBA, Production and Material Management -
Shri Sant Gajanan Maharaj College Of Engineering, Shegaon
B.E., Electronics & Telecommunication Engineering
Community
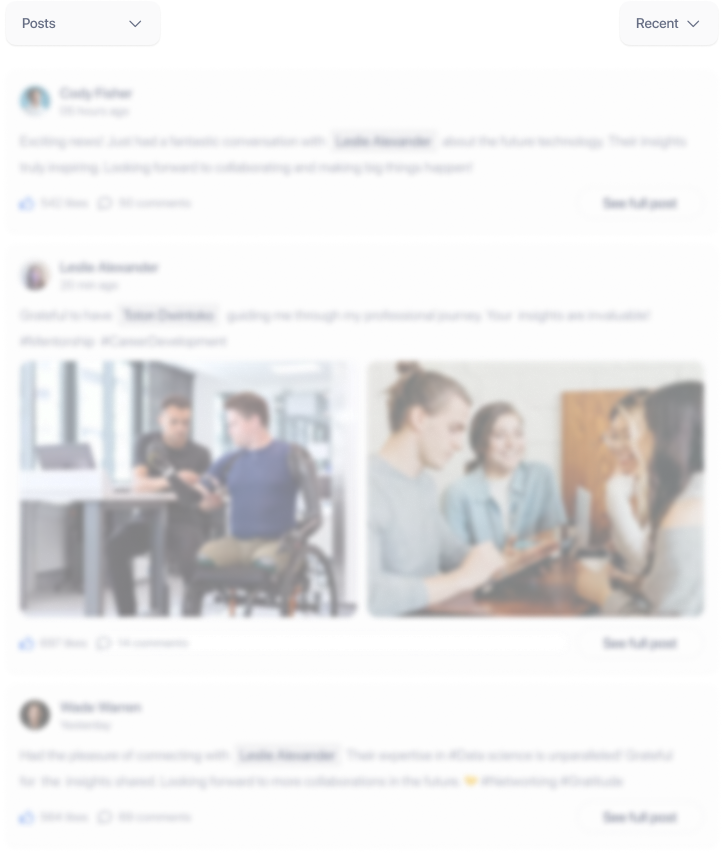