Arun kumar Muralidharan
Project industrialization manager at Alstom- Claim this Profile
Click to upgrade to our gold package
for the full feature experience.
Topline Score
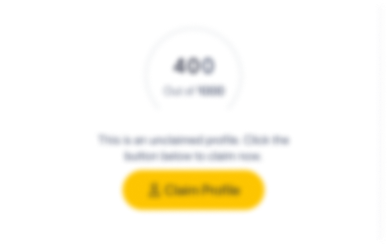
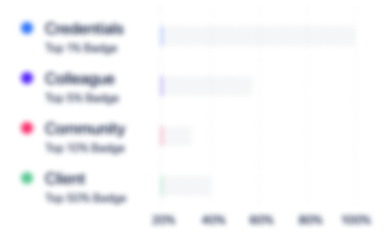
Bio


Credentials
-
Excel skills for Buisness: Intermediate I
Coursera Course CertificatesJul, 2022- Nov, 2024 -
Excel skills for Buisness:Essentials
Coursera Course CertificatesJun, 2022- Nov, 2024 -
WA white card training
The Government of Western AustraliaOct, 2021- Nov, 2024
Experience
-
Alstom
-
France
-
Rail Transportation
-
700 & Above Employee
-
Project industrialization manager
-
Oct 2022 - Present
-
-
Lead Process Engineer
-
Nov 2018 - Oct 2022
-
-
Process and methods engineer
-
Dec 2016 - Oct 2018
-
-
-
TVS Motor Company
-
India
-
Motor Vehicle Manufacturing
-
700 & Above Employee
-
Senior Process Engineer
-
Jun 2014 - Nov 2016
-
-
-
KAMAZ VECTRA MOTORS LIMITED
-
India
-
Motor Vehicle Manufacturing
-
1 - 100 Employee
-
Engineer-PED
-
Apr 2013 - Jun 2014
Organization KAMAZ VECTRA MOTORS LIMITED. Organization Background -KVML is a joint venture company between Kamaz Inc. Russia and the Vectra group. -KAMAZ Group of Companies is the largest automobile corporation of the Russian Federation. KAMAZ Inc. ranks one of the leading world heavy truck manufacturers and takes 8th place in the world by production volumes of diesel engines. Plant background -Product- Tipper Lorry. 1.6540 Kamaz-8X4 Multiaxle 280HP Euro3 Engine. 2.6520 Kamaz-6X4 Multiaxle 320HP Euro3 Engine. 3.6540 Cummins-8X4 Multiaxle 280HP Euro3 Engine. -OEM having assembly plant in SIPCOT Hosur, Tamilnadu. Designation Process Engineer Role & Responsibilities Facilities: 1. Facility Designing. 2. Plant Layout Planning. 3. Procurement of Facility & providing to manufacturing Department. 4. Procurement, installation & commissioning of Machine & Equipment. 5. Materials Storage Plan. 6. Suppiler Follow-up for quotation. Process: 1. Preparation of Technological process sheets for New process or assy. 2. Preparation of the process BOM. 3. Preparation of Work instruction for the newly procured equipment & facilities. 4. Process Establishment. 5. Monitoring the proto manufacturing process against plan. 6. Conducting Time Study. 7. Line Balancing. New Product Launch: 1. Involved in additional line establishment. 2. Created the Line layout for the additional line. 3. Planned New facilities, fixtures & tackles for additional line. Show less
-
-
-
motherson sumi systems limited,chennai
-
chennaii.
-
Manufacturing Engineer
-
Mar 2010 - Apr 2013
Product – Automotive Wiring Harness No. of lines - 4 Lines (Main, Engine Room, Body, Lead) No. of Employees - 1500 persons approx. Production per day - 600 harness/day; Safety 1. Ensure employee safety in process 2. Impart knowledge on safety to operators - significance of PPE's Quality 1. Systematic root cause analysis for Supplier defects and Customer complaints through QC tools; Quality projects to achieve best quality through systematic analysis of defects; Lead Kaizen Initiatives Implementation of Poka yokes. Delivery 1. Line balancing - Assembly & Subassembly as per Tact time 2. Scheduling production as per customer requirement 3.Lead productivity improvement projects to achieve best output in assembly line through continuous process improvements and elimination of waste 4. Maintaining 100% delivery schedule adherence Cost 1. Tact time Improvement 2. Carry out detailed process study to identify and eliminate NVA's 3. Identify cost saving opportunities through VA/VE Others 1. Resource allocation, Shift management, production planning 2. Employee Engagement in all production activities 3. Increase awareness among the operators Significant Achievements 1 Awarded the “Best Line of the Company” for consecutively three times in terms of 5S, PPM and Productivity 2 Leader of the improvement team and enhanced the productivity from 330 harness per day to 480 harness per day 3 Significantly reduced defects in Body assembly line in 3 months and sustained Zero defect for two consecutive weeks through HAI-Q project 4 Reduced the Cost per harness through VA/VE (Value Analysis/Value Engineering) 5 Single piece flow system established for the entire shop 6 Successfully coordinated ISO/TS 16949 surveillance audit and finished with Zero NC Show less
-
-
Education
-
Raja rajeswari engineering college,chennai.
B.E, electrical and electronics engineering. -
Shri natesan vidyasala mat.hr.sec.school,tambaram,chennai.
12th -
Samaskrita vidyalaya oriental high school.
10th std., High school
Community
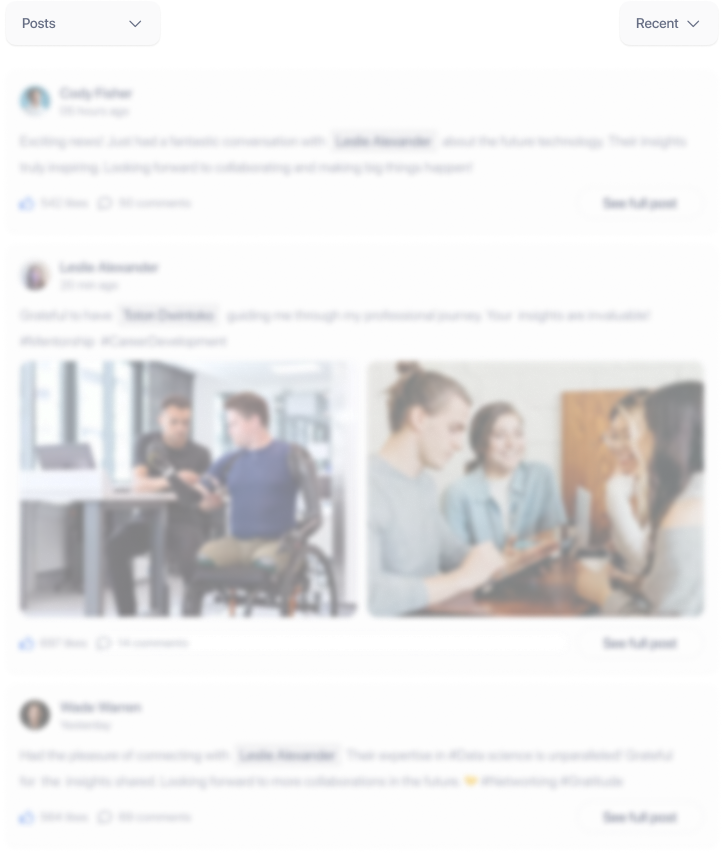