Arturo Jacobo
Production Manager at Avio Excelente- Claim this Profile
Click to upgrade to our gold package
for the full feature experience.
Topline Score
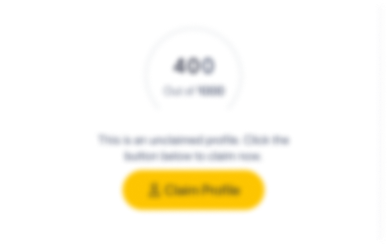
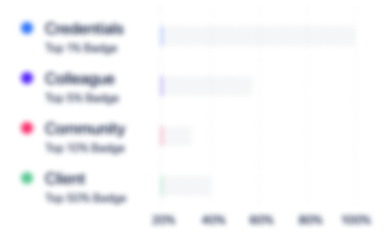
Bio


Experience
-
Avio Excelente
-
United States
-
Industrial Machinery Manufacturing
-
1 - 100 Employee
-
Production Manager
-
May 2019 - Present
Responsible of Engineering, planning and production activities Responsible of Engineering, planning and production activities
-
-
-
GE Healthcare BOP
-
GE Healthcare
-
Business Team Leader of Electronic Center
-
2005 - Present
Responsible for the direction and administration of a manufacturing operations with yearly sales of more than 800MM USD, leading the electronic boards production site and HLA for monitoring products. Responsibility includes production, scheduling, shipping, receiving, procurement, process and test engineering, quality assurance, master planners and manufacturing engineer supervision. Managing development of product, process and machinery transfers from US facilities to Mexico as project coordinator. Demonstrated leadership of Lean enterprises achieving increasing productivity, quality yield improvement, overtime reduction and optimizing process cycle time having more than 2MM dollars on savings on a yearly basis. Top Achievements • Established a material control system improving Cycle Count Accuracy from 60% to 96% reducing material adjustments from 400K to less than 50K dollars annually. • Winner of 2013 & 2014 of Best Lean Project award competing against 70 GE manufacturing plants around the world. • Reduction of inventory levels of FG (from 6MM to less than 1 MM dollars) and released of more than 40K sqf, through the implementation of proper material flow processes. • Implemented Make to Order scheme process instead of Make to Stock • More than 3K sqft saved through assembly process consolidation, 500K dollar savings on assembly processes through proficient usage of human space and equipment resources. • Reduction of more than 50% of inventory levels (from 2.6MM to less than 1.3MM dollars) through the implementation of proper materials flow procedures. • Elimination of non-conformant material (from more than 200K to 0 dollars) implementing mechanisms for the handling and disposition of the non-conformant material. • Customer Returns reduction from 7% to 1% launching lean projects focused on the elimination of root cause of recurrent quality defects by driving implementation of six sigma and effective root cause analysis. Show less
-
-
-
GE HealthCare
-
United States
-
Hospitals and Health Care
-
700 & Above Employee
-
Senior Quality Assurance Engineer
-
Dec 2003 - 2005
Implementation and day-to-day operation of procedures. Range of responsibilities includes quality improvements, GMP compliance documentation, field complaint coordination and corrective action plans. Technical supervision of process and product parameter optimization and validations, fixtures and quality instrumentation design, failure analysis of field complaints, development of technical procedures and manufacturing specifications and handling of supplier issues. • Directly interfaced with FDA inspectors during a FDA audit resulting in no observation nor 483 issuance in March 2005. • Coordinated all major efforts to achieve ISO/FDIS 13485:2003(E) certifications re designing and developing procedures and work instructions in a standardized quality system achieving company certification in February 2005. • Coordinated of manufacturing plant transfer from Denver Colorado to GE Border Operations facility such transferring process included; development of Mater Validation Plans for process and equipment being transferred, inspection plans, procedures and work instructions development. • Development of an effective visual aids system useful for manufacturing people as a support for their daily assembly activities. • Directly interfaced with FDA inspectors during a FDA audit resulting in no observation nor 483 issuances in September 2003. • Key participant of Lean Manufacturing initiatives achieving substantial work force and space savings and output improvements, coordinating one-piece flow concept implementation. • Reduced waste on material, time and workforce related, on quality assurance inspection and testing. Through inspection and testing transfer to actual production staff. • Reduced 700K rejected material in holding area through implementation of an effective Non-conforming material handling system, achieving better communication between GE and suppliers emphasizing mutual understanding of technical requirements and establishment of win / win scenario. Show less
-
-
-
Venusa LTD Cd. Juarez Mexico.
-
Juarez, Chihuahua Mexico
-
Business Unit Manager
-
2001 - 2002
Responsible for Class II and Class III manufacturing site of goals ranging; on time deliveries, quality manufacturing, engineering and supply chain. Enforcing cost saving and quality improvement programs through the use of engineering and quality tools such as FMEA, Kaisen, Pokka Yoke and Cause and Effect analysis. Responsible for all operations aspects of one manufacturing plant, with a total headcount of over 250 people. • Key member of the Total Quality Steering Committee. • Implemented over 10 engineering projects achieving more than 200K dollars in direct savings yearly, through coordination of individuals and departmental skills, emphasizing integration/cooperation and a teamwork philosophy. • Reduction of customer and field complaint rates from 7 cpm to less than 3 cpm through implementation of better root cause analysis and corrective and preventive action systems. Show less
-
-
-
-
Manufacturing Manager
-
1996 - 2001
Responsible for the direction and administration of manufacturing operations, supervised of two production sites for 800+ direct operators plus inherent technical and professional personnel. Responsibility included production, scheduling, shipping, receiving, procurement, quality assurance and customer service. Managed development of product, process and machinery transfers from US facilities to Mexico as project coordinator. • Quadrupled the size of production work force from 150 employees to 500+, expanding staff, systems and production equipment. Coordination of complete manufacturing plant transferring from US to Mexico as project manager. Hiring of operators, supervisors and engineers in a timely manner, developing an onsite training program for operators, supervisors and engineers. Scheduling process and equipment transfers and their inherent Master Validation Plans in compliance with current FDA’s Quality System Regulations. Achieving an outstanding 8 months transfer period exceeding customer expectations. • Promoted incremental systemic reduction in material waste and labor content through better industrial engineering such as; most analysis, one-piece flow and Pokka yoke system implementation.• Sustained and an external quality rate of 5 cpm and internal indicators below 750 dpm with a productivity improvement from 60% to over 90% through development and implementation of an effective self-assessment system in all manufacturing lines. As well as development and implementation of crossed functional training programs achieving an effective people involvement through recognition programs. Show less
-
-
Quality Assurance Manager
-
1991 - 1996
Skilled liaison between corporate offices and manufacturing operations, management of technical and quality projects. Directed efforts in monitoring and improving performance standards, procedures and regulatory compliance. Management of quality system development, improvement quality projects, validations, technology transfer and ISO certification. • Development and implementation of the company quality system, coordinating company configuration, writing and implementing inspection and testing specifications and procedures for in-coming, in-process and final product acceptance, standard operating procedures and work instructions for fully company compliance with FDA’s Quality System Regulations.• Coordinated all major efforts to achieve ISO 9001 and EN 46001 certification developing policies, procedures and work instructions in a standardized quality system to successfully achieved company certification on first surveillance. • Developed of operator’s certification project that included a reward program based on operation skills improvements, seniority, absenteeism, discipline and GMP regulation compliance. • Successful underwent of more than 25 extensive audits from fortune 500 companies auditing teams and implemented all corrective actions accordingly. Directly interfaced with FDA inspectors during a FDA international audits resulting in a minor observation on a 483 issuance. Show less
-
-
-
-
Quality Control Engineer
-
1990 - 1991
Managed the implementation and day to day operation of customer’s procedures for the Becton Dickinson Shelter in Elamex plant 6. Supported the validation and internal quality teams. Range of responsibilities included quality improvements; GMP compliance documentation; development of clinical samples; customer complaint coordination and corrective action plans.• Technical supervision of process and product parameter optimization; validation; fixtures and quality instrumentation design; failure analysis of field complaints; development of technical procedures and manufacturing specifications. Show less
-
-
Quality Control Supervisor
-
1988 - 1990
Supervised a production floor quality group of 10 inspectors involved in incoming, in-process and final inspection as well as compliance to product and process specifications. Maintained all quality records for a 120 employee operation.
-
-
-
Elamex, Sa de CV
-
Ciudad Juarez, Cihuahua Mexico
-
Production Supervisor
-
1987 - 1988
Supervised over 5 production lines and manufacturing cells with 56 operators, 3 group leaders and 2 material handlers. • Improved assembly efficiencies of my production cells by 25%. Supervised over 5 production lines and manufacturing cells with 56 operators, 3 group leaders and 2 material handlers. • Improved assembly efficiencies of my production cells by 25%.
-
-
Education
-
Lean Certification. Hino Japan Academy
Certification, Lean Techniques -
DALE CARNEGIE INSTITUTE
Certification, Human Resources Management -
APICS El Paso
APICS CSCP course (Certified Supply Chain Profesional)., APICS -
IPC certified body
IPC A-610 Specialist., Electronic board analist -
GE Healthcare corporate
6 Sigma Training Corporate, 6 Sigma -
Tecnológico de Monterrey
Diploma, Industrial Engineering Diploma -
Tecnológico de Monterrey
Executive Management Diploma., Business Administration and Management, General -
Instituto Tecnológico de La Laguna
Industrial Mechanical Engineer, Graduated -
GE Excellence training center. Crotonville NY.
Manager Development Course, Human Resources Management/Personnel Administration, General
Community
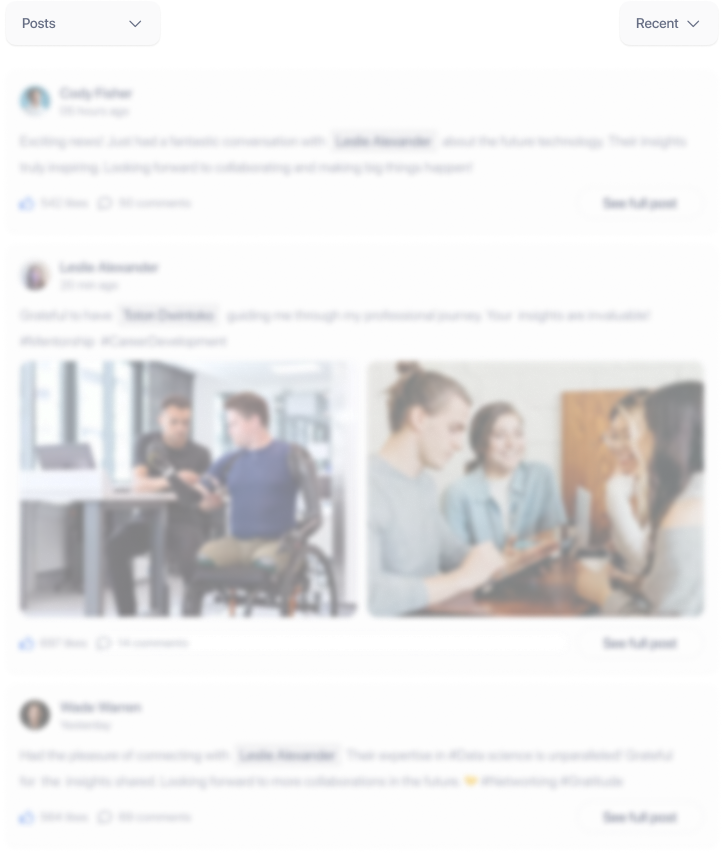