Arturo Cortinas
Project Manager at Collado Industries by Grupo Collado- Claim this Profile
Click to upgrade to our gold package
for the full feature experience.
-
Español Native or bilingual proficiency
-
Ingles Full professional proficiency
Topline Score
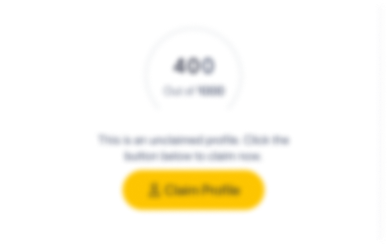
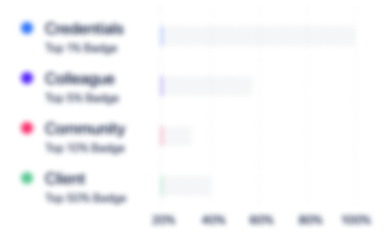
Bio


Credentials
-
Lean Six Sigma
-
Experience
-
Collado Industries by Grupo Collado
-
Mexico
-
Mining
-
300 - 400 Employee
-
Project Manager
-
Jun 2021 - Present
* Side Lead transfer receive of Planta Santa Rosa * Lead of Dematic account * Side Lead transfer receive of Planta Santa Rosa * Lead of Dematic account
-
-
-
Lenovo
-
China
-
IT Services and IT Consulting
-
700 & Above Employee
-
Manufacturing Program Manager
-
Sep 2019 - Apr 2021
• NPI laptop transfers of 47 products from China to MTY representing a business of 20 million / 93% of NPI´s on time. • Management of NPI Desktop transfer and validation and refresh of 102 products from China to MTY • Development of the validation plan for new product introduction projects (NPI) • Management and monitoring of the activities of the first parts plan until the end of validations. • Management of meetings for monitoring the plan and detection of barrers and / or risks during validations. • Coordination with the departments involved to meet the dates according to the plan. • Review and validation of Bom for families to validate • Follow-up on arrival of materials for validation. • Review of bom changes, design changes and material validation with equipment from China and Monterrey. - Lead of AQM department • Management and lead of project on Quality hold material by supply issues from 9.5 million USD to 795K USD in inventory and avoid costs of material management in Warehouse of 9K USD by month . • Management of digitalization project of the AQM system to activities tracking in real time. Show less
-
-
-
Schneider Electric
-
France
-
Automation Machinery Manufacturing
-
700 & Above Employee
-
Sr. Manufacturing and projects engineer.
-
Feb 2017 - Nov 2018
• Side leader MTY in strategic transfer plant 6 project with Schneider Electric USA • Coordination of transfer and installation of NQ1, NQ2, NF and CUSTOMER KITS lines. • Coordination and installation of CTO line. • Design and building of work station ergonomically with replenishment system to all lines. • Leader in saving project of $ 36,500 USD per year in Full Assy area and increasing capacity from 50 pcs/ day to 75 pcs /day • Implementation of Schneider Production System (TPS) • Development of equivalent units Playbook the CTO line. • Coordination of supply chain to increase of 25% of CTO line capacity after transfer project from 1000pcs to 1250 pcs per shift . • Member of CTO Business Unit • Management of budget control of project transfer over $ 400,000 USD • Leader of Kaizen Events (monthly events) under the DMAIC Methodology. • Creation of Work Instructions, Specific Aids, Staff Training. Show less
-
-
-
Prolec Energy
-
Mexico
-
Manufacturing
-
700 & Above Employee
-
Process Engineer
-
Oct 2014 - Feb 2017
• Development and implementation of standardized process Helical coils disks and work. • Development and auditing of suppliers (PPAP, APQP, FMEA). • Leader / Supervisor production of coils MPT, PT and EHV line. • Management of customer returns (SQA) and interfunctional team management to determine root cause, generating corrective actions, and solving customer problems. • Implementation of 4M's system for detecting problems in production line. • Time reduction of 33% ( 1 hr to 40min.) in reinforced molds and 45% (2.5 hrs to 1.3 hr) in mold release cycle for PT coils saving $ 11,000 USD per year and increasing capacity of 10 equivalent units. • Management cost Control Center tools and auxiliary material. • Development projects FMEA's new products. • Development Work Shop in the area of coils MPT, PT and EHV (Continuous Improvement). • Reduction VNAI (Value Added No Unnecessary) of 25% in movements and search times by auxiliary material production line. • Ensure the Process of Design and Production of the component, satisfying the needs of the Client. Show less
-
-
-
All Professional Trades
-
Toronto y alrededores, Canadá
-
Continuous Improvement Engineer
-
Nov 2013 - Mar 2014
• Reduced delivery time and material savings with 5´s implementation. • Designed system planning, Implementation Projects and Work Flow. • Coordinated work team to do projects and other services. • Reduced delivery time and material savings with 5´s implementation. • Designed system planning, Implementation Projects and Work Flow. • Coordinated work team to do projects and other services.
-
-
-
GE Transportation, a Wabtec company
-
United States
-
Truck Transportation
-
700 & Above Employee
-
Manufacturing Engineer
-
Jul 2011 - Jan 2013
• Reduced the number of defects to 32% in winding area from 15 to 5 defects per week and saving $ 32,000 USD per month • Reduced cycle time from 4 hours to 2.5 hours in Ovens and VPI (Vacuum, pressure and impregnation) area. • Created Work Flow from administration of work instruction in quality system. • Designed control system from production from use and maintenance of pneumatic tools • Developed error proofing techniques in the process production. • Elaboration of Work Instructions and Visual aids by Line process. • Ensure the Process of Design and Production of the component, satisfying the needs of the Client. Show less
-
-
-
GE
-
United States
-
Industrial Machinery Manufacturing
-
700 & Above Employee
-
Manufacturing Engineer
-
Mar 2011 - Jul 2011
• Developed and negotiated deals with suppliers for installation of production line transfer given by 10 people • Developed work instructions for a standardized process. • Was Responsible for the design of workstations. • Organized and coordinated the installation processes for production • Kaizen event reducing costs and saving $ 31,000 USD per year in wire process. • Developed and negotiated deals with suppliers for installation of production line transfer given by 10 people • Developed work instructions for a standardized process. • Was Responsible for the design of workstations. • Organized and coordinated the installation processes for production • Kaizen event reducing costs and saving $ 31,000 USD per year in wire process.
-
-
-
Instalaciones Eléctricas y Servicios CUVISA S.A. DE C.V.
-
General Escobedo y alrededores, México
-
Projects Development Engineer
-
Sep 2010 - Mar 2011
• Developed and improved proposals in production line. • Planning of new projects in electrical installations • Coordinated supply and delivery of material from projects a warehouse $20,000 Dlls. Inventory. • Developed and improved proposals in production line. • Planning of new projects in electrical installations • Coordinated supply and delivery of material from projects a warehouse $20,000 Dlls. Inventory.
-
-
Education
-
Universidad Autonoma de Nuevo Leon
Maestria en Ingenieria, Manufactura -
Universidad Autonoma de Nuevo Leon
Ingeniero en Electronica y Automatizacion, Ingeniero en Electronica y Automatizacion y Maestria en Manufactura
Community
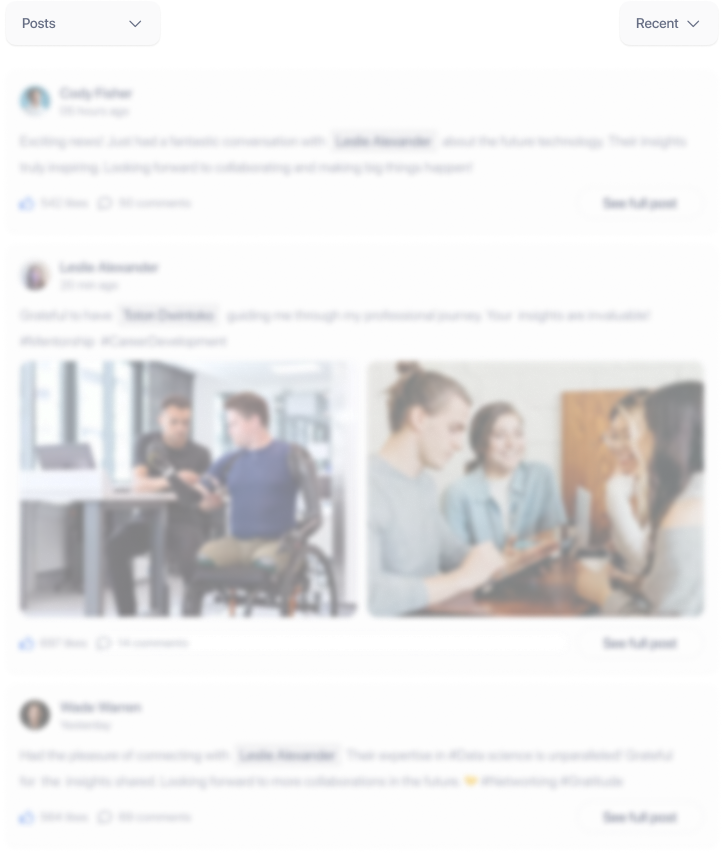