Arturo Bouwmans Martínez
at Hyperloop Supaero- Claim this Profile
Click to upgrade to our gold package
for the full feature experience.
-
Inglés Full professional proficiency
-
Francés Professional working proficiency
-
Español Native or bilingual proficiency
-
Neerlandés Elementary proficiency
Topline Score
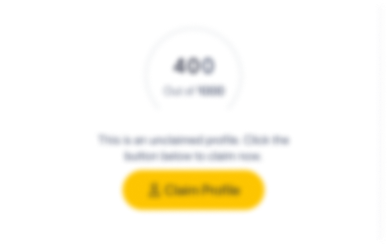
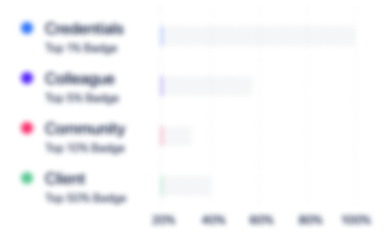
Bio


Credentials
-
Français, niveau B1
Escuela Oficial de Idiomas Fernando Lázaro CarreterJun, 2022- Nov, 2024 -
Certificate in Advanced English (CAE) Level C1 CEFR
Cambridge University Press and Assessment EnglishJan, 2022- Nov, 2024
Experience
-
Hyperloop Supaero
-
France
-
Ground Passenger Transportation
-
1 - 100 Employee
-
-
Apr 2023 - Present
-
-
-
Sep 2022 - Present
I am member of the Aerostructures Division of the Hyperloop Supaero Team. Specifically, I am responsible of the design of the guidance system.The guidance system contributes to the alignment of the vehicle with the track, which is essential for a correct propulsion. Since this is the first prototype of the team, there were no past references to take inspiration from, so research had to be done to do a smart design of the guidance system.As well as designing the guidance system, I also contributed to the design of the chassis. The chassis is the part that contains all the subsystems of the vehicle, so its shape and mechanical properties are vital to the vehicle's performance.The goal is to present the team's prototype at the European Hyperloop Week, held in Edinburgh (Scotland) this year. Show less
-
-
-
UPM Racing
-
Spain
-
Motor Vehicle Manufacturing
-
1 - 100 Employee
-
Structures Engineer
-
Sep 2021 - Aug 2022
I worked for UPMRacing as a member of the Chassis Division, responsible of providing a safe and reliable structure for a Formula type car. During the year I have worked here, we faced many problems from the monocoque that was made the previous year. We had to redesign and correct some parts of it to comply with the Formula Student competition rules. Once these problems were solved, we focused in the design and manufacturing of the next monocoque, that would have the same shape but will be lighter, thanks to the optimization of the layups of fiber. The optimization was made by simulating the structural behaviour of composite materials with Altair Hypermesh. This allowed us to reduce the number of layers of some zones of the monocoque maintaining the mechanical properties. As well as doing tasks for the Chassis Division, I also contributed to the Cost & Manufacturing Division. This division is responsible of making the bill of materials of the whole car, listing the manufacturing processes and estimating its costs, as well as thinking of ways of recycling, reducing and reusing materials. The result of the work of all the year was the qualification to the competitions of Formula Student East and Formula Student Germany, in which we participated the summer of 2022. In these competitions, we achieved the main goal of the Chassis Division, that was passing the mechanical inspections. Show less
-
-
-
Instituto Nacional de Técnica Aeroespacial «Esteban Terradas»
-
Spain
-
Aviation and Aerospace Component Manufacturing
-
100 - 200 Employee
-
Structures Engineer
-
Nov 2021 - Jul 2022
In this internship I contributed to the development of a new monocoque for a Formula type car, as well as other components of the car made of composites. It was a long process that started with the design of the layups of the different zones of the monocoque. All the different layups had to be tested to comply with the mechanical requirements given by the Formula Student competition. Once they were tested, the rolls of fiber had to be cut in patterns with the adequate shape for each zone, so the lamination could start. For the lamination, carbon fiber moulds from the previous monocoque were reused. The lamination started in July and finished at the start of 2023, resulting in a lighter monocoque, due to optimization of the layups. Overall, this internship has improved my knowledge of composite materials, their mechanical properties, and their manufacturing processes. During the internship, I have worked with carbon, glass and aramid fiber, seen its differences and understood when to use each one, depending on the application. In terms of manufacturing, I experienced the differences between a lamination with preimpregnated fibers and a wet lamination. Show less
-
-
Education
-
ISAE-SUPAERO
Master of Science - MS, Aerospace Engineering -
Universidad Politécnica de Madrid
Bachelor, Aerospace Engineering
Community
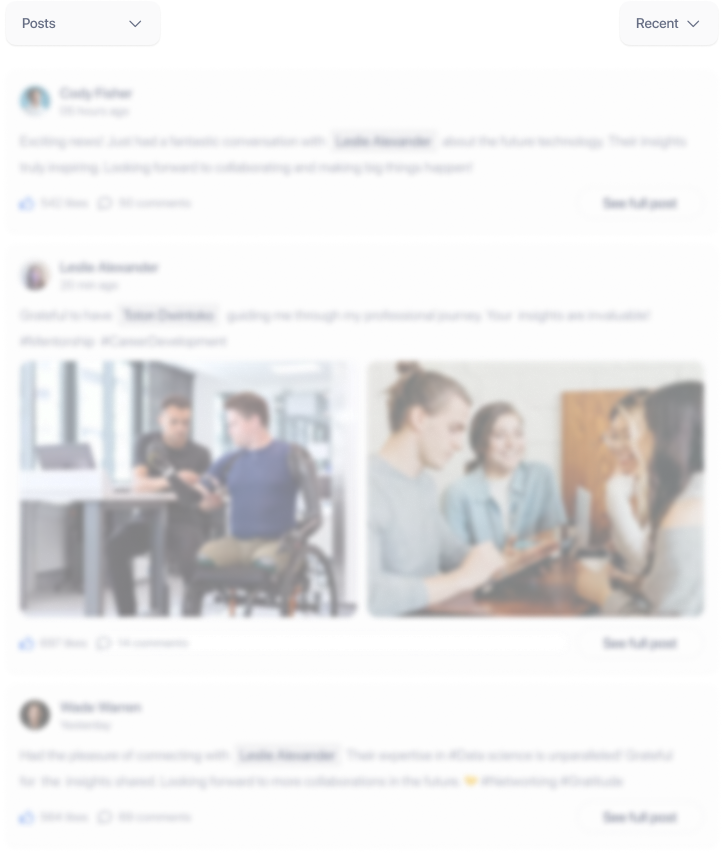