
Robert Arthur
Composite Fitter at Mercedes-AMG Petronas Formula One Team- Claim this Profile
Click to upgrade to our gold package
for the full feature experience.
-
German -
Topline Score
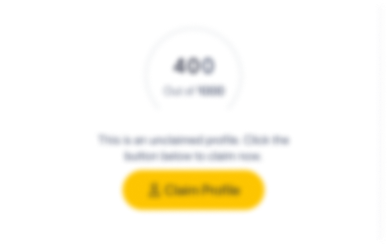
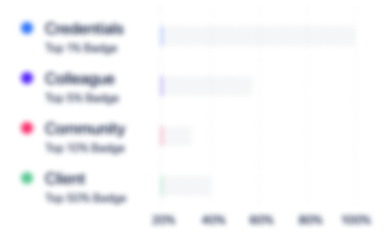
Bio


Experience
-
Mercedes-AMG PETRONAS Formula One Team
-
United Kingdom
-
Spectator Sports
-
700 & Above Employee
-
Composite Fitter
-
Jun 2020 - Present
-
-
-
-
Senior Model Maker
-
Jan 2014 - Jun 2020
Carrying out many of the tasks as at Force India. As a senior model maker my role would be to take charge of the production and assembly of parts for an area of the car, working with the designers and aerodynamicists of this group to ensure all parts were ready, pre fitted and built up for the test to ensure smooth and efficient tests giving feedback and improvements to maximise testing time with the tight deadlines of the department. My skills used on a day to day basis would consist of composite component manufacture from tooling all the way through to part finishing and fitting to the model. Machining using both manual and cnc machines, Full model builds from complete sub assembly builds (wheel corner assemblies to diffuser and rear wing assemblies) and carrying out R&D projects consisting or composite, mechanical and Sla components and builds. Building and testing scale and full size aero rakes and testing at the wind tunnel and going to the track to assist in testing.
-
-
Model Maker
-
Oct 2009 - Jan 2014
Prepare and produce scale parts to fit to the tunnel model. Ensuring pre-fitting and trimming of parts when possible. Also carrying out model changes in the tunnel along with other model makers and wind tunnel technicians. Giving feedback and advice to aeros and designers on how to improve quality of parts and improving change times and general fitting.
-
-
-
-
Model Maker
-
Jan 2008 - Sep 2009
As a model maker my day to day job role consists of preparing, fixing and modifying SLA resin, carbon fibre and pattern block parts for the wind tunnel models. I also carried out essential pre-fitting of parts to maximise efficiency in the tunnel, using jigs and pre-fit models to within tight tolerances. I was also tasked to laminate wind tunnel components and carrying out trimming tasks following technical drawings using machinery, air and hand tools. Also my job role involves working in the wind tunnel carrying out parts changes on the model to tight deadlines and making sure parts are fitted correctly using accurate measuring equipment. Towards the end of my time at the team I worked at the main factory composites department in the trimming and fitting section and also attended as composite support to a car test with the test team.
-
-
-
-
Composite Technician/ Apprentice
-
Aug 2006 - Jan 2008
I started at super aguri as an apprentice composite technician laminating parts for the cars using various materials and techniques. Which also moved onto trimming and assembling the finished parts on jigs and onto the cars using different fixings and adhesives where required. Also carrying modifications to parts already assembled on the cars and any other composite components where needed. I started at super aguri as an apprentice composite technician laminating parts for the cars using various materials and techniques. Which also moved onto trimming and assembling the finished parts on jigs and onto the cars using different fixings and adhesives where required. Also carrying modifications to parts already assembled on the cars and any other composite components where needed.
-
-
Education
-
OCVC motorsport engineering course
AVCE -
OCVC
Advanced Modern Apprenticeship, Composites -
Cooper School Bicester
Community
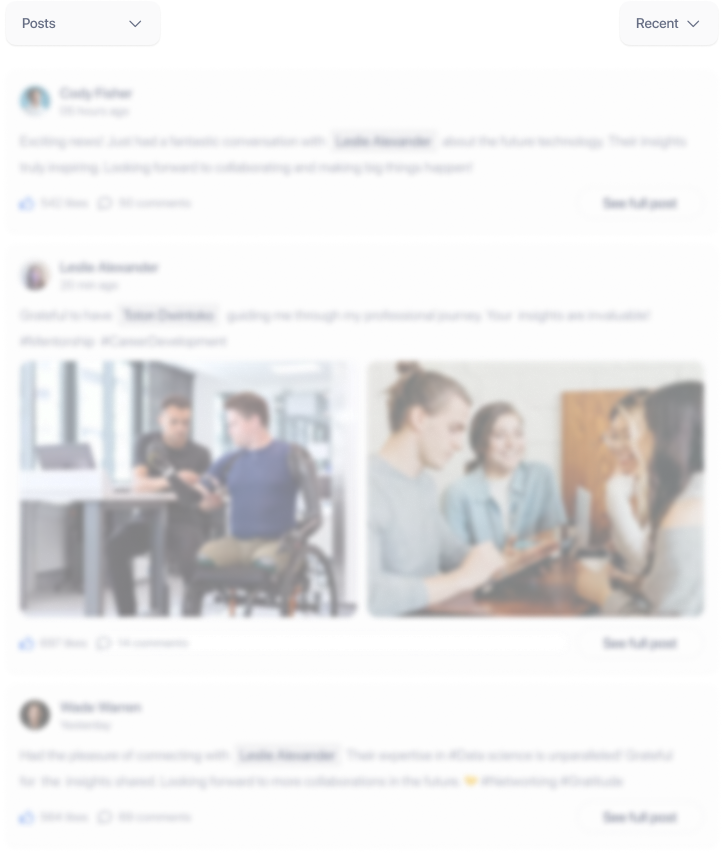