Art Oliva
Director Of Operations at Prism Logistics- Claim this Profile
Click to upgrade to our gold package
for the full feature experience.
Topline Score
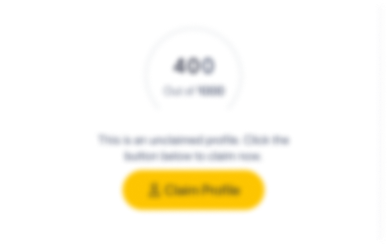
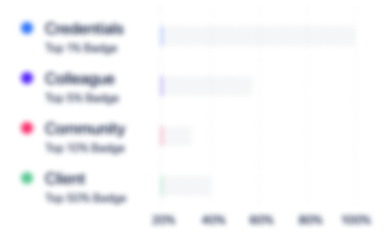
Bio


Credentials
-
CPR & First Aid
- -
Fork-lift certified
-
Experience
-
Prism Logistics
-
United States
-
Warehousing and Storage
-
1 - 100 Employee
-
Director Of Operations
-
May 2022 - Present
-
-
-
DSV - Global Transport and Logistics
-
Denmark
-
Transportation, Logistics, Supply Chain and Storage
-
700 & Above Employee
-
Operations Manager
-
Aug 2021 - Apr 2022
-
-
-
CULT GAIA
-
United States
-
Retail Apparel and Fashion
-
1 - 100 Employee
-
Warehouse Manager
-
Feb 2019 - Aug 2021
• Manage all day to day activities of the facility and staff. The fulfillment center services domestic and international customers with a wide range of big box retailers, to the small individual owned shops. The E-commerce experience must be set to an extremely high standard, along with an operation to match. • Elements of the operation include, customer service, each pick, pack functions, VAS activities, Ecommerce small parcel, wholesale, customer routing, quality control programs, and LTL shipping. • Systems- RLM (ERP apparel/footwear software) to manage a 2,500 + active SKU count, with categories in women’s fashion (garments, footwear, handbags, jewelry, swimwear, and accessories). NetSuite/WMS implementation completed on 1/04/21. Includes all major functions of a WMS, RF receiving, putaway, picking, returns, and inventory control. For the Ecommerce packing operation, Pacejet was integrated for the scan pack and carrier processing functionality. • Utilized integrated systems such as Shopify and ShipStation to process E-commerce activities. • Developed management tools to track volume trends/KPIs, contract labor expense/hours, supplies to control/compare annual spend trends, pricing and meeting budgeting expectations. • Implemented the needed SOPs across all functions, to build solid processes and a team that could be cross trained in the event of daily cross functional duties. • Built a strong foundation by way of an efficient facility layout, proper item classification slotting/re-slotting seasonal programs, efficient pick path, and strict guidelines to maintain a clean and well-organized facility. • Process improvement is one of the major parts of my day to day activities, to ensure the operation is meeting customer needs, expectations and executing to the highest level of service. • Implemented the necessary safety program/requirements so the facility would meet industry/OSHA standards. Show less
-
-
-
STG Logistics
-
United States
-
Transportation, Logistics, Supply Chain and Storage
-
400 - 500 Employee
-
Facility Manager
-
Aug 2017 - Feb 2019
• Manage day to day activities of a 210,000 sq. ft. facility. The facility consists of 34 dock doors, MHE fleet with various equipment types. Headcount is a combination of FTEs and Contract labor, totaling 55 to 100+ employees depending on seasonality and volume. • Elements of the operation included, CSRs, container devanning, carton/each pick, pick/pack functions, VAS activities, Ecommerce small parcel, customer routing, LTL and FTL shipping. • Utilize Synapse WMS to manage 400+ SKU count with 20K rack pallet position on hand inventory, with full RF capabilities. • Developed management tools to track volume trends/KPIs, VAS activity planning, contract labor expense control/compare and annual spend. • Process improvement is one of the major parts of my day to day activities, to ensure the operation is meeting customer needs, expectations and executing to the highest level of service. • Manage all facility expenditures and cost control. This is done by price comparisons, vendor negotiations and supply utilization. Also includes monthly financial reviews with executive level management. • Implemented the necessary safety program/requirements so the facility would meet industry standards. Show less
-
-
-
Expeditors
-
United States
-
Transportation, Logistics, Supply Chain and Storage
-
700 & Above Employee
-
Manager - Distribution Services
-
Mar 2016 - Jun 2017
• Managed the day to day operation activities of a 450,000 sq ft multi-client facility. Facility consisted of 15 different retail customers with various commodities, 53 dock doors, 65+ MHE fleet with various equipment types with guide wire capability. Headcount was a combination of FTEs, Interns, Contract labor and internal 3PL staff, totaling 280+ employees. • Managed a successful start-up of a 250,000 sq ft single client footwear operation. The project plan included internal facility move, construction of narrow aisle racking, installation of conveyor system, complete facility set-up, MHE and staffing. • Elements of the operation included, container devanning, carton/pair pick, pick to tote, pick/pack functions, VAS activities, ecommerce, small parcel, customer routing and LTL shipping. • Utilize Manhattan WMS to manage 30K+ SKU count with a 2 million+ pair on hand inventory, with full RF capabilities. • Developed performance management tools to justify labor needs and to validate units per hour standards. Process improvement is critical in a start-up environment, this was a huge part of my day to day activities to ensure the operation was meeting the customer needs, expectations and executing to the highest level of service. Show less
-
-
-
Incase
-
United States
-
Manufacturing
-
1 - 100 Employee
-
Director - Global Warehousing & Logistics
-
2011 - 2016
• Oversee the day to day operations of the Ecommerce Fulfillment Center - full pick/pack operation, inventory/cycle count processes, VAS activities and customer returns. Headcount, 10 to 30 employees, depending on seasonality. • Global Warehousing and Distribution - maintain the partnerships with our 3PL providers, day to day operations, validating expenses, best practices and contract negotiations. In this area I have excelled, with an overall savings of 1.3 million over the past 3 years. The Global Network consisted of 6 facilities, with a total Global footprint of 150,000 sq ft. • Global Logistics - maintain partnerships with our domestic and international freight forwarders and determine best way ship methods and rate/contract negotiations. • Key elements of accomplishments: Improved on inefficiencies with facility layout and design, which included the racks, pick line, pack line, QC and shipping stations. Developed SOPs, introduced cross training and built a strong team environment. • I took all my knowledge and tools of operating/managing a big box and utilized them to implement the required processes to effectively manage the facilities work flow, labor, inventory and financials. Introduced a cycle counting process that maintains a 98.5% inventory accuracy in a non-WMS environment, effective productivity standards/processes to hold employees accountable to the standards in a non-WMS environment. Developed operational throughput standards to tie volumes to labor expenses. Implemented a solid Safety Program company wide, the warehouse has gone over 3 years injury free. • Developed KPIs within warehousing and logistics, the tools to manage the business outputs and to provide the data to make solid financial decisions. Perform data analysis to accurately show business performance and put together the necessary monthly KPI trend reports. Show less
-
-
-
DHL Supply Chain
-
Germany
-
Transportation, Logistics, Supply Chain and Storage
-
700 & Above Employee
-
General Manager
-
2002 - 2010
• Successful facility start-up, which included facility layout and design to accommodate an 800 SKU count and a 1.2 million case inventory. Coordinated an expert team to recruit, interview and hire FTEs. Pulled together a cost effective network of vendors to ensure competitive pricing of services. Negotiated, purchased and put in place a 22 piece mixed MHE fleet to successfully run the operation. Coordinated the implementation of the Red Prairie WMS that included purchasing, installation, training and go live execution. • Drove all aspects of a 4.2 million annual revenue P&L. Executed an on time accurate month end close to include, corporate reporting, validation of journal entries, deliver a 10% operating profit margin and completion of global metrics. • Delivered a safe, clean and environmentally responsible 580,000 sq ft facility. The facility had a 26,000 pallet footprint capacity, with an average of 21,000 pallets of on hand inventory. • Drove a 98% or better inventory accuracy that exceeded the customer and company metrics. This was done with on time cycle count processes, countback process, operator accountability and effective tools to manage and track the data. • Effective performance management strategies that included the implementation and utilization of LMS to track and measure operator success, to increase productive time and decreased indirect time. Developed and effectively implemented tools to monitor day to day shift/site performance, with goal setting and effective labor planning to site performance to 103% of standard. • Produced a motivated, well trained team of 60 associates, which included management, CSRs, IC and operations teams that included temporary staffing. • Possess knowledge and success with multiple customer business operations that included Clorox-336,000 sq ft, SCJ-400,000 sq ft and Unilever-1.0 million sq ft facilities. Show less
-
-
-
MTC Distributing
-
Modesto, CA
-
Supervisor
-
1997 - 2002
• Coordinated all receiving functions that included daily scheduling of inbound receipts to meet customer/buyer order fill requirements. Delivered 100% item receipt accuracy and 100% scanned inventory. • Drove a successful and motivated inventory team. Maintained a 95% or better inventory accuracy. Day to day out of stock tracking and research to accomplish a 90% or better fill rate. Focused on item set up to ensure picking accuracy, zero pick shorts and precise flow of product throughout the pick lines. Item set up included UPC entries, item dimension entries and item pick/pack configurations were accurate. Kept an ongoing focus on FIFO/code dates of all relevant inventories to ensure proper shipping guidelines. • Developed an effective IC/receiving team that included 10 associates and a VAS team that consisted of a 100% temp work force. • Successfully delivered a 95% or better inventory accuracy with a 5 million dollar high level item category with weekly physical inventories. • Successful start-up and implementation of a 200,000 sq ft automated facility that included multi level pick modules with conveyor systems, rack storage and flow bin pick lines. Implemented an operating WMS that worked in conjunction with wrist mounted RF units for optimum pick productivity. Show less
-
-
-
Hi-Tec Sports International
-
Apparel & Fashion
-
1 - 100 Employee
-
Warehouse Supervisor
-
1992 - 1997
• Drove the main components of the facility that included scheduling all import containers, receiving of all inbound shipments with 100% accuracy. Ensured all case identification labels were properly applied to all inventory for accuracy, putaway, picking and item history. Maintained an off-load productivity standard, bench marked to 2 hours per load @ 950 cases per shipment. Drove a highly effective picking and packing operation that consisted of each pick to conveyor, packing by scan and shipping of 90% of freight by way of LTL. • Responsible to perform a 5% thorough quality inspection on every inbound shipment. Maintained data analysis to track the defect percentage per shipment and reported to overseas manufacturing with findings. • Maintained item UPCs, set-up and slotting to maximize pick flow, pick performance and packing. • Ability to motivate and drive a performing team of 25 associates, with 3% temp labor and a VAS team of 100% temp staff. • Delivered a performing facility of 200,000 sq ft that included all rack storage, one conveyor picking and packing operation. Show less
-
-
Education
-
Victor Valley College
Business Administration and Management, General -
Modesto Junior College
Criminal Justice/Law Enforcement Administration -
Al Collins Graphic Desing School
Associate of Arts (A.A.), Commercial and Advertising Art
Community
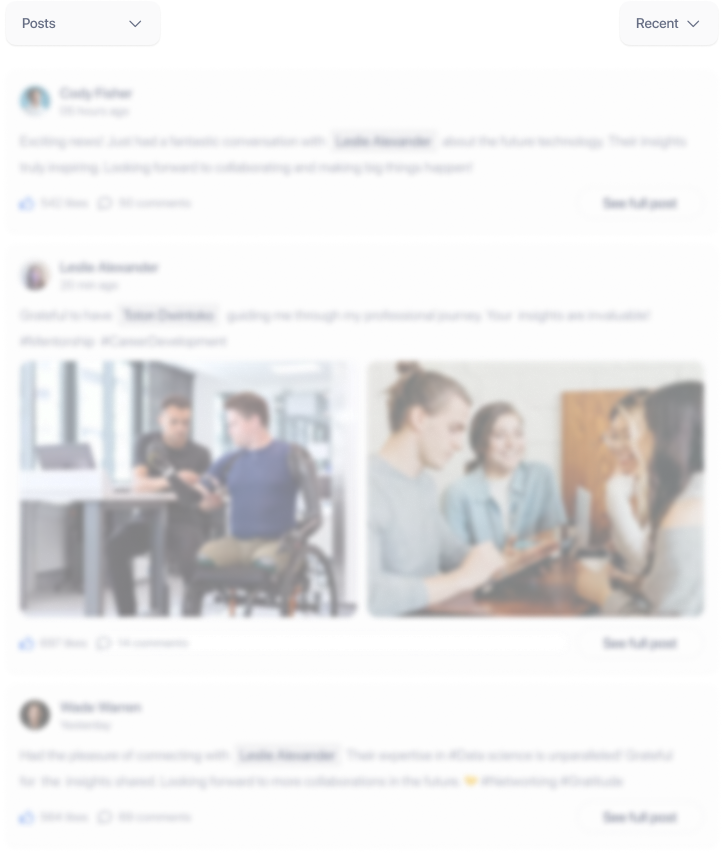