Arlynn R.
Director Program Management at Zentech Manufacturing- Claim this Profile
Click to upgrade to our gold package
for the full feature experience.
Topline Score
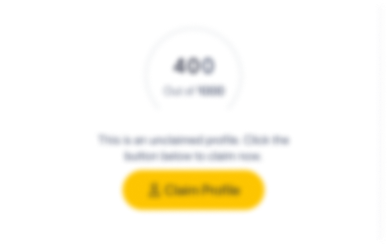
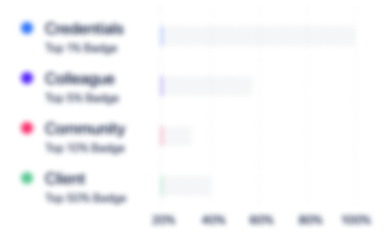
Bio


Experience
-
Zentech Manufacturing
-
United States
-
Appliances, Electrical, and Electronics Manufacturing
-
1 - 100 Employee
-
Director Program Management
-
Oct 2021 - Present
Washington DC-Baltimore Area
-
-
-
-
Human Services Specialist
-
Jan 2016 - Present
Phoenix, Arizona Summary of Experience: State Government & Private Industry Staff Leadership and Management •Directed work activity for factory managers, engineers, technicians, buyers, EHS, facilities, and program managers. •Established a continuous improvement culture and defined LEAN Manufacturing strategies for all team members. •Developed the 1st OEM defense customer using FAR/DAR requirements to define contract management capabilities. •Organized union contract negotiation strategy and… Show more Summary of Experience: State Government & Private Industry Staff Leadership and Management •Directed work activity for factory managers, engineers, technicians, buyers, EHS, facilities, and program managers. •Established a continuous improvement culture and defined LEAN Manufacturing strategies for all team members. •Developed the 1st OEM defense customer using FAR/DAR requirements to define contract management capabilities. •Organized union contract negotiation strategy and reorganization efforts to drive KPI improvement. Project and Process Administration •Implemented business operations management training curriculum and Food Safety Manager Certification. •Evaluated DoD contract requirements and proposed analysis for impact to program with recommendations. •Developed and maintain comprehensive training manuals, program quality plans, and supplier KPI’s. • Lead factory cost reduction activities to implement LEAN process principles in solving problems. Communication •Champion all site-wide communications including conducting lunch and learn training seminars. •Lead community youth motivation efforts by attending high school career counseling events to encourage youth to pursue careers in Science, Technology, Engineering, and Math (STEM). Show less
-
-
-
Smiths Detection
-
United Kingdom
-
Security Systems Services
-
700 & Above Employee
-
Director of Operations / Site Manager
-
Mar 2012 - Sep 2015
Edgewood, Md § Establish a culture of continuous improvement is in place and lead all activities to establish Lean manufacturing at all levels within the operations team. § Continuously train and develop the operations team at all levels to ensure that the workforce is fit to meet the demands of the market. - Implemented the daily whiteboard meeting process with the specific flow down communication from Focused Factory Managers to direct reports. § Lead management representative for all Bargaining… Show more § Establish a culture of continuous improvement is in place and lead all activities to establish Lean manufacturing at all levels within the operations team. § Continuously train and develop the operations team at all levels to ensure that the workforce is fit to meet the demands of the market. - Implemented the daily whiteboard meeting process with the specific flow down communication from Focused Factory Managers to direct reports. § Lead management representative for all Bargaining Unit interactions associated with grievances, mediations, and arbitrations. § Provide input and guidance to executive staff on all union interaction and activity. o Participated in the successful negotiation of several mediation strategies to reduce company liability for union grievances without moving to arbitration as the next step. § Communications champion for all site-wide communications including conducting lunch and learn training seminars. o Administered the first-ever monthly lunch and learn sessions to educate staff on business initiatives which included financial planning for retirement, preparing for tax submittals and benefits of 401k participation, health, and wellness fairs focusing on healthy living. § High-level management accountability for manufacturing engineering, facilities, maintenance, radiation safety, trade compliance, environmental health and safety, and video/graphics activity across a 249k square foot facility. o Using Lean principles and concepts successfully implemented vehicle factory re-layout to reduce overall footprint and lean process flow reducing overall production time against standard. Show less
-
-
-
Suntron Corporation
-
Appliances, Electrical, and Electronics Manufacturing
-
100 - 200 Employee
-
Plant Manager
-
Nov 2010 - Mar 2012
Sugar Land Texas Represent the company before vendors, employees, customers, Board of Directors, and its other various constituencies to present information on the site and realize the company’s current operations and future objectives. o Successfully hosted several onsite transitions and new customer meet and greet conferences for continued business development opportunities. o New customers won for the alternative site include Medical Device and Avionics OEMs. Develop and maintain manufacturing… Show more Represent the company before vendors, employees, customers, Board of Directors, and its other various constituencies to present information on the site and realize the company’s current operations and future objectives. o Successfully hosted several onsite transitions and new customer meet and greet conferences for continued business development opportunities. o New customers won for the alternative site include Medical Device and Avionics OEMs. Develop and maintain manufacturing operations business plans to include all program requirements, labor hours, production costs, and throughput. o Providing guidance to the development of a manufacturing process plan, including personnel requirements, material needs, subcontract requirements, facility needs, tooling & equipment needs. Ensuring all established costs, safety, quality, and delivery commitments are met. o Reduced the quantity of outsourced 3rd party facilities contractors by bringing the activity in-house thus increasing the bench strength of the facilities team. o Implemented square footage usage reduction from 260k sq. ft. to 105k sq. ft. to allow businesses to seek other tenant opportunities to support cost savings opportunities Show less
-
-
-
Honeywell
-
United States
-
Appliances, Electrical, and Electronics Manufacturing
-
700 & Above Employee
-
Customer Business Mgr. /Capital Planning Mgr. /Manufacturing Mgr. /HR Business Partner
-
Feb 1997 - May 2007
Phoenix, Arizona Area •Responsible for financial performance to an annual operating plan of $21M and execution of customer commitments by directing activities of account reps in order entry and maintenance. •Create and deploy robust process management activities of Capital Coordinators from 46 global Aerospace Repair and Overhaul businesses responsible for a $20M capital appropriations budget. •Organized and directed the work activity of 9-17 manufacturing supervisors in deploying Lean Manufacturing concepts… Show more •Responsible for financial performance to an annual operating plan of $21M and execution of customer commitments by directing activities of account reps in order entry and maintenance. •Create and deploy robust process management activities of Capital Coordinators from 46 global Aerospace Repair and Overhaul businesses responsible for a $20M capital appropriations budget. •Organized and directed the work activity of 9-17 manufacturing supervisors in deploying Lean Manufacturing concepts and 5S strategies across a three-shift operation. •Implement and ensure execution of various HR programs such as dispute resolution, succession planning, advanced leadership training, organizational development, and performance management. Show less
-
-
-
Suntron Corporation
-
Appliances, Electrical, and Electronics Manufacturing
-
100 - 200 Employee
-
Director, Customer Business Management
-
Sep 1999 - May 2005
Phoenix, Arizona Area Responsible for maintaining close contact with the customer organization to ensure the highest possible level of customer satisfaction is provided with the appropriate customer representatives to maintain a high level of program status awareness, provide timely recognition and resolution of problems, identify follow-on business opportunities, and prevent surprises. o Direct program management responsibility for the site 1st defense OEM o Coordinated customer meetings with several… Show more Responsible for maintaining close contact with the customer organization to ensure the highest possible level of customer satisfaction is provided with the appropriate customer representatives to maintain a high level of program status awareness, provide timely recognition and resolution of problems, identify follow-on business opportunities, and prevent surprises. o Direct program management responsibility for the site 1st defense OEM o Coordinated customer meetings with several avionics OEMs of which three long term supplier contract were awarded. Participate in follow-on business development of existing customers’ contract strategy, development, review and negotiations for programs in concert with Contracts and site Plant Manager. Show less
-
-
Education
-
Grand Canyon University
Master of Public Administration - MPA, Government and Policy -
Ottawa University-Phoenix
BA, Business Management
Community
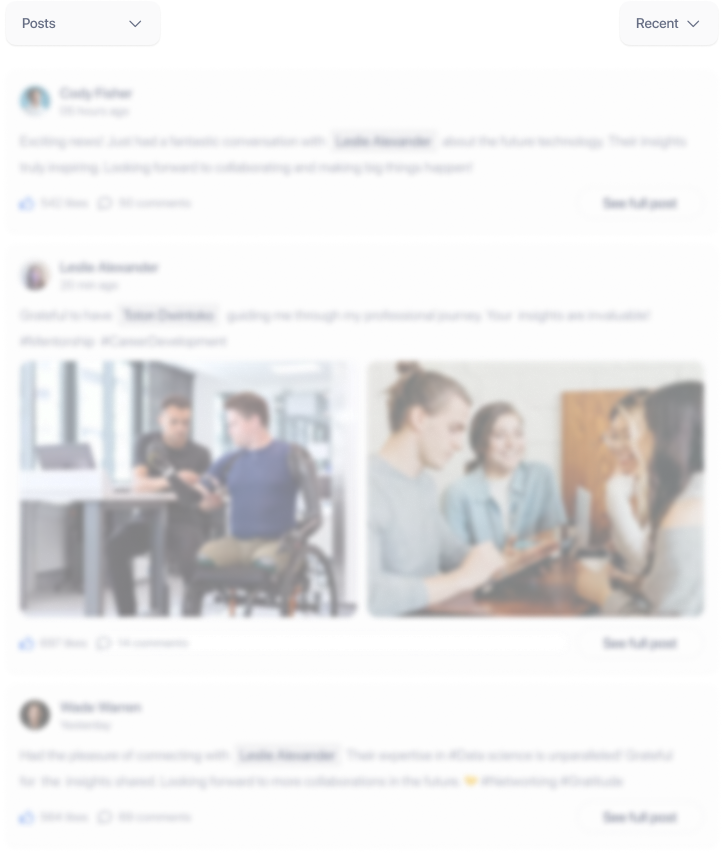