Arisbet C.
Director of Regulatory Affairs & QA at Heliae Development, LLC- Claim this Profile
Click to upgrade to our gold package
for the full feature experience.
Topline Score
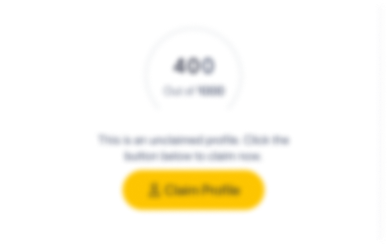
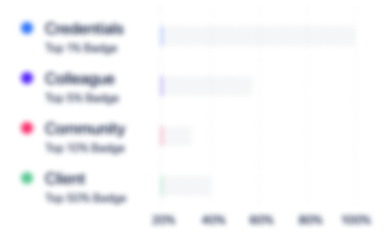
Bio


Experience
-
Heliae Development, LLC
-
United States
-
Agriculture, Construction, Mining Machinery Manufacturing
-
1 - 100 Employee
-
Director of Regulatory Affairs & QA
-
Dec 2021 - Present
United States
-
-
Quality Assurance Manager
-
Mar 2016 - Present
Arizona • Development and deployment of product quality assurance strategy, • Troubleshoots quality issues that affect quality performance of all products. • Maintains documentation/record keeping of all products. • Assist with all quality related internal and external audits including customers, and other third party audits. • Investigates customer complaints, and analyzes customer feedback to improve the quality and performance of the organization. • May have to prepare written… Show more • Development and deployment of product quality assurance strategy, • Troubleshoots quality issues that affect quality performance of all products. • Maintains documentation/record keeping of all products. • Assist with all quality related internal and external audits including customers, and other third party audits. • Investigates customer complaints, and analyzes customer feedback to improve the quality and performance of the organization. • May have to prepare written correspondence to address various concerns or issues
-
-
Assistant Quality Assurance and Regulatory Manager
-
Nov 2013 - Present
Gilbert, Arizona Primary Responsibilities; Achieves quality assurance operational objectives by contributing information and analysis to strategic plans and reviews; preparing and completing action plans; implementing production, productivity, quality, and customer-service standards; identifying and resolving problems; completing audits; determining system improvements; implementing change. Ensures that the company maintains FDA compliance with all products and processes. Develops quality assurance… Show more Primary Responsibilities; Achieves quality assurance operational objectives by contributing information and analysis to strategic plans and reviews; preparing and completing action plans; implementing production, productivity, quality, and customer-service standards; identifying and resolving problems; completing audits; determining system improvements; implementing change. Ensures that the company maintains FDA compliance with all products and processes. Develops quality assurance plans by conducting hazard analyses, identifying critical control points and preventive measures, establishing critical limits, monitoring procedures, corrective actions, and verification procedures (HACCP-HARPC), and monitoring inventories. Validates quality processes by establishing product specifications and quality attributes, measuring production, documenting evidence, determining operational and performance qualification, writing and updating quality assurance procedures. Maintains and improves product quality by employing LEAN principles and completing product, company, system, compliance, and surveillance audits; investigating customer complaints; collaborating with other members of management to develop new product and engineering designs, and manufacturing and training methods. Prepares quality documentation and reports by collecting, analyzing and summarizing information and trends including failed processes, stability studies, recalls, corrective actions, and re-validations.
-
-
-
Earthrise Nutritionals
-
United States
-
Food & Beverages
-
1 - 100 Employee
-
QMS
-
Feb 2011 - Nov 2013
Calipatria, California Establish, documented and maintain of the Earthrise Quality Management System. Management System Representative of the Earthrise Quality Management System. Member and coordinator of Management System Council meetings. Ensure compliance with the FDA/GMP requirements for Disease Control, Cleanliness, Education and Training of personnel. Supplier Qualification Process owner, as evaluator and auditor of subcontractors. Change control coordinator of standard operation procedures and… Show more Establish, documented and maintain of the Earthrise Quality Management System. Management System Representative of the Earthrise Quality Management System. Member and coordinator of Management System Council meetings. Ensure compliance with the FDA/GMP requirements for Disease Control, Cleanliness, Education and Training of personnel. Supplier Qualification Process owner, as evaluator and auditor of subcontractors. Change control coordinator of standard operation procedures and data to get management approval. Document Control and Record Keeping owner to complete the identification of obsolete documents, and traceability of the product. Internal and independent auditor of the Quality Management System, based on ISO9000 & FSSC 22000. Independently review Quality Management System suitability and effectiveness. Responsible to maintains and gets licenses and permits. (Federal, State & Locals) Trainer of QMS, GMP, Safety, and HACCP or ISO22000+PAS220 training of Earthrise personnel. (English & Spanish) Designer and creator of the training material of Quality System Management and current Good Manufacturing Practice. Responsible for establishing and manages the QMS department budget. Safety committee coordinator of Earthrise. Responsible for the Independent verification of the implementation of corrective actions of quality issue. Independently owner of nonconforming products until the quality issue is resolved. Identify adequate resources to implement Quality System Programs, like training, equipment, and literature. Show less
-
-
-
Motorola Solutions
-
United States
-
Telecommunications
-
700 & Above Employee
-
Consultant Quality
-
Aug 2001 - Feb 2011
Ciudad Juarez, Chihuahua Mexico Responsible for the identification and implementation of the Quality Management System based on ISO 9000. Sustain Certification 2005-2010. Six Sigma Green Belt Motorola certification with a 250K project in saving. Coordinator of a group of people to write down SOPs and work instructions across the organization. (Operations, Engineering, and Quality department) Internal auditor to executed audits in the annual basis, including creating audit reports, closing out audit findings and… Show more Responsible for the identification and implementation of the Quality Management System based on ISO 9000. Sustain Certification 2005-2010. Six Sigma Green Belt Motorola certification with a 250K project in saving. Coordinator of a group of people to write down SOPs and work instructions across the organization. (Operations, Engineering, and Quality department) Internal auditor to executed audits in the annual basis, including creating audit reports, closing out audit findings and determining proper corrective and preventive actions Developer and trainer of the Quality System into the organization. Developer and informer of the Key Process Indicators (KPI) to assess the effectiveness of the Quality System. Member of the investigation team of the nonconformance to ensure implementation and effectiveness of subsequent corrective and preventive actions. Coordinator of the internal and external audit, with Corporative Associates and Third-party companies. Supplier Qualification Process owner to executed supplier audits in Latin America. (Guatemala, Costa Rica, Venezuela & Panama). Established and executed training to associates on ESD, 5’s, ISO 9000, 8d’s. All these pieces of training are Quality Control and Quality Assurance disciplines to support the process improvement. Manager/Supervisor of ten quality auditors. (Recruiting, selecting, orienting, training, assigning, scheduling employees, also of the annual reviews of the quality auditors). Coordination of activities with Advocates and Customers to reduce Return Repair (warranties) rate. From 15% to 2.8% these events were coordinated between two facilities and two countries (USA-MEXICO). Owner of the corrective action program to requests and follow-ups on internal and external audits. The corrective action request used as part of the monitoring for nonconformance reports. Support of activities on Global Inventories in two different sites (Juárez Mx, El Paso, Tx) Show less
-
-
-
-
ISO 9001:2008 Consultant
-
2010 - 2010
Cd. Juarez, Chihuahua Mx Provide support in the process analysis to establish ISO9001 standard for the potable water service.
-
-
-
Antec, Inc
-
Computers and Electronics Manufacturing
-
1 - 100 Employee
-
Industrial Engineer and Document Control Spv.
-
Sep 1999 - Apr 2001
I had the project management for new product introduction , and update all relatives documentation, bill of material, standard man power, upload the cost to quote to the customer. Design new fixture, and update the work instruction as need it. Create new work instruction . Document control Supv. for all work instruction for products in the company .
-
-
-
Siemens
-
Germany
-
Automation Machinery Manufacturing
-
700 & Above Employee
-
Manufacturing Assistant -Document Control Administrator
-
Aug 1996 - Sep 1999
Ciudad Juarez Write down standard procedure as support of the Engineering Department Doer of visual aid as quality criteria for the product. Controlling all the documents (files and records) of the company and make sure that they are kept at their relevant locations so that they can be easily assessable. Routing documentation for approval. Distribution of control copies as needs it. Notification of temporary deviation dues. Entering documents to the Company Systems. Record keeper… Show more Write down standard procedure as support of the Engineering Department Doer of visual aid as quality criteria for the product. Controlling all the documents (files and records) of the company and make sure that they are kept at their relevant locations so that they can be easily assessable. Routing documentation for approval. Distribution of control copies as needs it. Notification of temporary deviation dues. Entering documents to the Company Systems. Record keeper of the Quality Department. Show less
-
-
-
Genasco
-
Appliances, Electrical, and Electronics Manufacturing
-
1 - 100 Employee
-
Industrial Technician
-
May 1994 - Aug 1996
Ciudad Juarez, Mexico Supoort to the Enginerering Department to do prototypes, establish a standard procedures and desing an electrical testing board panel of motorcycle and automotive harness. Set up a new production lines.
-
-
Education
-
Universidad Autónoma de Ciudad Juárez
Bachelor of Sciences (BS) Industrial Engineer, Operations Management and Supervision -
ITESM
Master of Business Administration (MBA), Manufacturing Engineering -
ITESM
Diploma Quality and Productivity, Manufacturing Engineering
Community
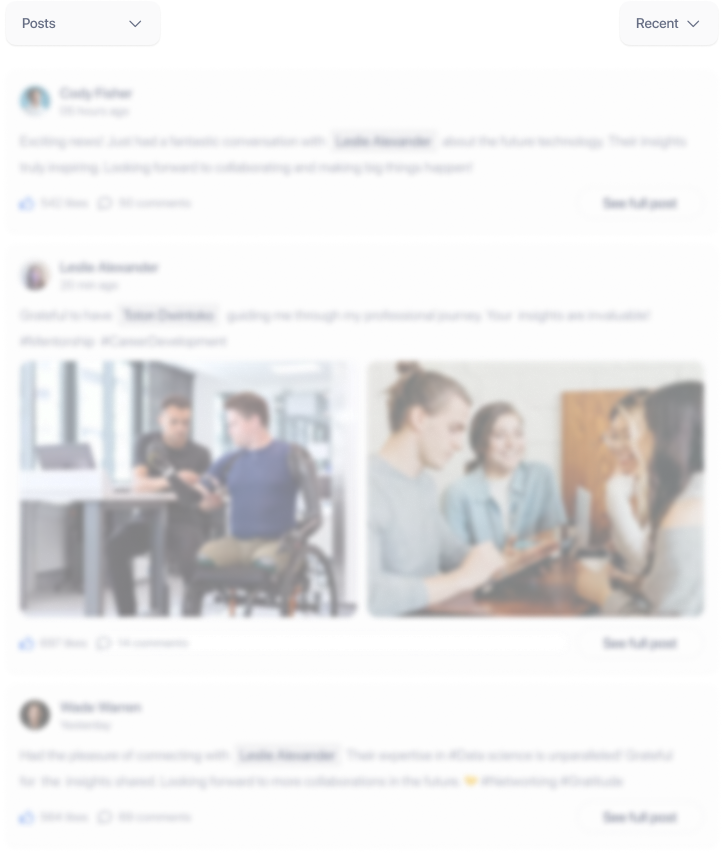