Aracely Melgar
Process Improvement Manager at PaperWorks Industries, Inc.- Claim this Profile
Click to upgrade to our gold package
for the full feature experience.
Topline Score
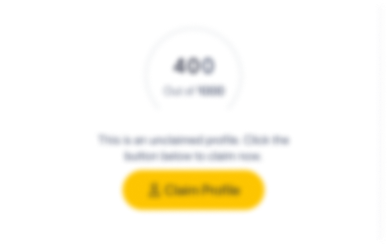
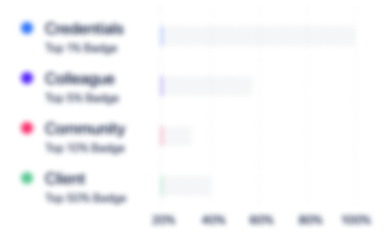
Bio

James Fournace
Aracely is an individual who has a strong knowledge of manufacturing, costs, scheduling and inventory. She is a dedicated and tireless worker, needing little supervision in order to exceed expectations. Aracely is well accepted and respected as a trusted leader amongst her peers.

James Fournace
Aracely is an individual who has a strong knowledge of manufacturing, costs, scheduling and inventory. She is a dedicated and tireless worker, needing little supervision in order to exceed expectations. Aracely is well accepted and respected as a trusted leader amongst her peers.

James Fournace
Aracely is an individual who has a strong knowledge of manufacturing, costs, scheduling and inventory. She is a dedicated and tireless worker, needing little supervision in order to exceed expectations. Aracely is well accepted and respected as a trusted leader amongst her peers.

James Fournace
Aracely is an individual who has a strong knowledge of manufacturing, costs, scheduling and inventory. She is a dedicated and tireless worker, needing little supervision in order to exceed expectations. Aracely is well accepted and respected as a trusted leader amongst her peers.
0
/5.0 / Based on 0 ratingsFilter reviews by:
Experience
-
-
Process Improvement Manager
-
Oct 2011 - Present
Identify opportunities for improvement -either through data analysis* or team brainstorming-, find solutions, define best practices and aid in the implementation of them. Evaluate progress and measure improvement. Participate in managerial decisions. Participate in initiatives of other teams: quality, safety, environmental, maintenance, etc. Work independently and call on teams as needed. * Data analysis: collect information, analyze it, draw conclusions and act upon those. Apply statistical methods to improve operations: production efficiency, job costing and waste reduction. Co-led the project to implement the ERP computer system to integrate the manufacturing operations. Co-led the project to put into practice Lean Manufacturing principles: implementation of the 5 S’s methodology, Visual Management and process flow. Leader of the project to improve the use of the ERP software through the analysis of transactions and information flow, debugging, training, database maintenance, and inventory management (product traceability and stock control). Internal auditor for ISO-9000. IT Exposure: Support daily manufacturing operations: troubleshoot and resolve problems related to software and hardware. Routine maintenance activities to IT equipment including desktops, servers, touch screen stations, and scanners. Provide training on new software to users.
-
-
-
Taylor Precision Products
-
United States
-
Manufacturing
-
1 - 100 Employee
-
Supply Chain Management Analyst
-
May 2003 - Dec 2005
Coordinate all purchasing and production scheduling activities. Inventory management: inventory control, inventory turns, excess and obsolescence, aging, Develop plans for cost reduction: define economic order quantities, supplier evaluation, optimize inventory management, Analysis of forecast and trends and adapt production capabilities as needed. Communicate with different departments. Coordinate between departments to develop solutions for process improvement: quality, engineering, shipping, etc. Develop tools to make the management of the supply chain activities more efficient.
-
-
-
Johnson Controls
-
Ireland
-
Industrial Machinery Manufacturing
-
700 & Above Employee
-
Buyer/Planner
-
Aug 2001 - May 2003
Production scheduling, capacity management, analysis of demand, production activity control, customer service. Procurement (raw materials), inventory management, analysis of materials requirement planning. Production scheduling, capacity management, analysis of demand, production activity control, customer service. Procurement (raw materials), inventory management, analysis of materials requirement planning.
-
-
Education
-
The University of Texas at El Paso
Master of Science (MS), Manufacturing Engineering -
Instituto Tecnológico de Ciudad Juárez
Bachelor of Science (BS), Industrial Engineering
Community
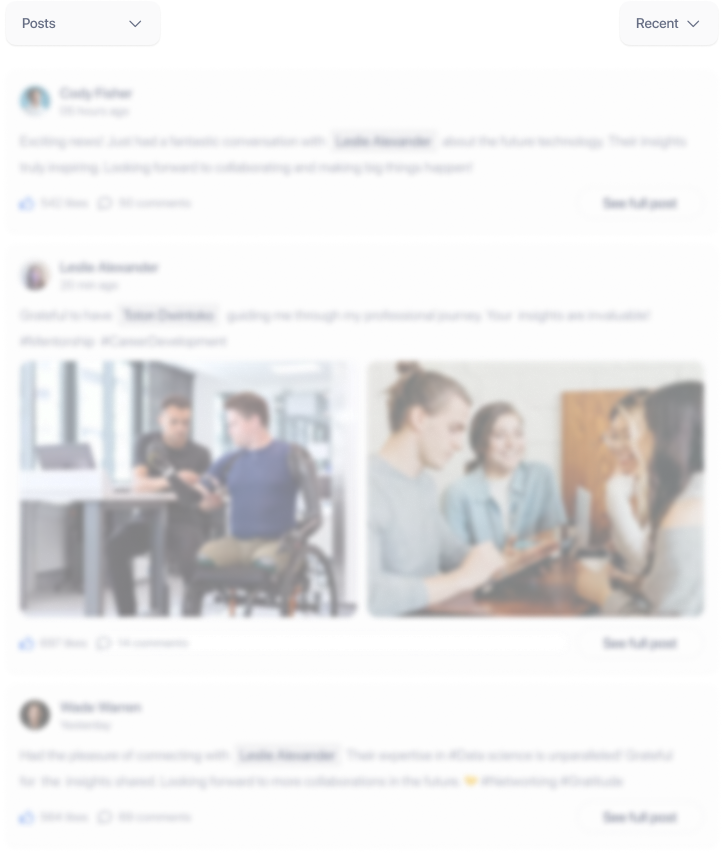