Anthony Sanford
VP, Quality and Regulatory at Gold Standard Diagnostics- Claim this Profile
Click to upgrade to our gold package
for the full feature experience.
Topline Score
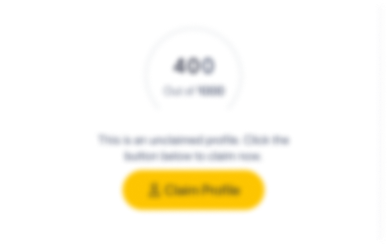
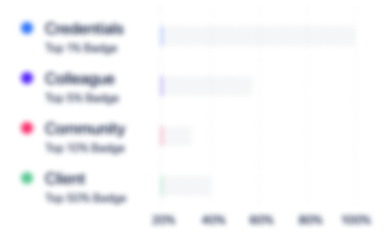
Bio

Jim Marshall, C.P.M.
I worked with Tony at Sanofi Genzyme when he was hired as a Quality Consultant to help us remediate our quality system as part of the now infamous Genyzme consent decree. Although there were some obvious gaps in our systems, Tony's experience and insight helped us to uncover and prioritize the elements that would bring us into compliance and allow us to identify what "good" and "best in class" look like from both an operational and compliance standpoint. A critical element to our team's success was Tony's ability to understand our culture and way of working, which in turn, resulted in action plans that were executable in our current environment and allowed us to meet our deadlines as prescribed in the consent decree. Even though an outside consultant, Tony was always willing to put in whatever time and effort was required to support and drive the team forward and our team never missed a single consent decree deadline to either our third-party oversight or the FDA. Tony's capabilities and performance are commendable and I would highly recommend him for any role or opportunity in the bio-pharmaceutical quality or regulatory space. In addition to all of his capabilities, he is very personable and a pleasure to work with. I was thankful for his leadership and guidance through our process.

LinkedIn User
Anthony Sanford was an excellent resource for quality systems review, management processes and supplier controls. Anthony contributed significantly as a Quality systems consultant during his time with me at Sanofi Genzyme. He has thorough knowledge of the 21 CFR820 quality requirements and ISO 13485. Anthony was able to work across the disciplines, with all levels of the organization. He was able to help our teams in the difficult task of developing compliant, operational and sustainable systems for a robust QMS. Anthony’s problem solving approach and his ability to deliver helped to keep our projects on track.

Jim Marshall, C.P.M.
I worked with Tony at Sanofi Genzyme when he was hired as a Quality Consultant to help us remediate our quality system as part of the now infamous Genyzme consent decree. Although there were some obvious gaps in our systems, Tony's experience and insight helped us to uncover and prioritize the elements that would bring us into compliance and allow us to identify what "good" and "best in class" look like from both an operational and compliance standpoint. A critical element to our team's success was Tony's ability to understand our culture and way of working, which in turn, resulted in action plans that were executable in our current environment and allowed us to meet our deadlines as prescribed in the consent decree. Even though an outside consultant, Tony was always willing to put in whatever time and effort was required to support and drive the team forward and our team never missed a single consent decree deadline to either our third-party oversight or the FDA. Tony's capabilities and performance are commendable and I would highly recommend him for any role or opportunity in the bio-pharmaceutical quality or regulatory space. In addition to all of his capabilities, he is very personable and a pleasure to work with. I was thankful for his leadership and guidance through our process.

LinkedIn User
Anthony Sanford was an excellent resource for quality systems review, management processes and supplier controls. Anthony contributed significantly as a Quality systems consultant during his time with me at Sanofi Genzyme. He has thorough knowledge of the 21 CFR820 quality requirements and ISO 13485. Anthony was able to work across the disciplines, with all levels of the organization. He was able to help our teams in the difficult task of developing compliant, operational and sustainable systems for a robust QMS. Anthony’s problem solving approach and his ability to deliver helped to keep our projects on track.

Jim Marshall, C.P.M.
I worked with Tony at Sanofi Genzyme when he was hired as a Quality Consultant to help us remediate our quality system as part of the now infamous Genyzme consent decree. Although there were some obvious gaps in our systems, Tony's experience and insight helped us to uncover and prioritize the elements that would bring us into compliance and allow us to identify what "good" and "best in class" look like from both an operational and compliance standpoint. A critical element to our team's success was Tony's ability to understand our culture and way of working, which in turn, resulted in action plans that were executable in our current environment and allowed us to meet our deadlines as prescribed in the consent decree. Even though an outside consultant, Tony was always willing to put in whatever time and effort was required to support and drive the team forward and our team never missed a single consent decree deadline to either our third-party oversight or the FDA. Tony's capabilities and performance are commendable and I would highly recommend him for any role or opportunity in the bio-pharmaceutical quality or regulatory space. In addition to all of his capabilities, he is very personable and a pleasure to work with. I was thankful for his leadership and guidance through our process.

LinkedIn User
Anthony Sanford was an excellent resource for quality systems review, management processes and supplier controls. Anthony contributed significantly as a Quality systems consultant during his time with me at Sanofi Genzyme. He has thorough knowledge of the 21 CFR820 quality requirements and ISO 13485. Anthony was able to work across the disciplines, with all levels of the organization. He was able to help our teams in the difficult task of developing compliant, operational and sustainable systems for a robust QMS. Anthony’s problem solving approach and his ability to deliver helped to keep our projects on track.

Jim Marshall, C.P.M.
I worked with Tony at Sanofi Genzyme when he was hired as a Quality Consultant to help us remediate our quality system as part of the now infamous Genyzme consent decree. Although there were some obvious gaps in our systems, Tony's experience and insight helped us to uncover and prioritize the elements that would bring us into compliance and allow us to identify what "good" and "best in class" look like from both an operational and compliance standpoint. A critical element to our team's success was Tony's ability to understand our culture and way of working, which in turn, resulted in action plans that were executable in our current environment and allowed us to meet our deadlines as prescribed in the consent decree. Even though an outside consultant, Tony was always willing to put in whatever time and effort was required to support and drive the team forward and our team never missed a single consent decree deadline to either our third-party oversight or the FDA. Tony's capabilities and performance are commendable and I would highly recommend him for any role or opportunity in the bio-pharmaceutical quality or regulatory space. In addition to all of his capabilities, he is very personable and a pleasure to work with. I was thankful for his leadership and guidance through our process.

LinkedIn User
Anthony Sanford was an excellent resource for quality systems review, management processes and supplier controls. Anthony contributed significantly as a Quality systems consultant during his time with me at Sanofi Genzyme. He has thorough knowledge of the 21 CFR820 quality requirements and ISO 13485. Anthony was able to work across the disciplines, with all levels of the organization. He was able to help our teams in the difficult task of developing compliant, operational and sustainable systems for a robust QMS. Anthony’s problem solving approach and his ability to deliver helped to keep our projects on track.

Experience
-
Gold Standard Diagnostics USA Clinical
-
United States
-
Medical Device
-
1 - 100 Employee
-
VP, Quality and Regulatory
-
Jan 2017 - Present
Responsible for leading GSD’s quality & regulatory system and team both domestically and internationally. Serve as the management representative for the Quality System, developing and implementing a best-practice approach to quality systems to create a sustainable culture of quality. Drive process improvements and cost reductions. Manage GSD’s relationships with the FDA, Notified Bodies and other external and internal quality and regulatory groups and agencies, ensuring a best practice approach to compliance; liaise with the FDA and other global regulatory agencies to ensure all quality and regulatory reporting requirements are met. Create and implement a quality vision and strategy supported by quality and regulatory compliance programs and infrastructure that sets the standard to proactively influence the design and manufacturability of GSD’s products. Provide the education and development of employees, driving their ownership of the Quality Management System (QMS). Provide direction on product design reviews and validation requirements. Align quality systems with partners and customers. Show less
-
-
-
Silara Medtech
-
United States
-
Medical Equipment Manufacturing
-
1 - 100 Employee
-
Director, Quality Systems
-
Jan 2016 - Dec 2016
• Develop internal quality systems compliant with both domestic and international regulations. • Apply and coach others on Quality System regulation requirements, implementing best practice quality organization and strategy to align with business objectives. • Revise management review process for compliance, provide leadership while managing quarterly management review. • Partner with senior management in establishment of annual quality plan, performance measurements and business metrics. • Establish and drive improvement of Quality System programs including Internal Audits, Supplier Quality, and CAPA. • Serve as Owner for QMS System, revise quality manual and related documents in alignment with ISO and QSR, schedule, conduct and manage internal and external cGMP audits. • Design, Develop and Deliver cGMP and CAPA training for all personnel. Show less
-
-
-
Gold Standard Diagnostics USA Clinical
-
United States
-
Medical Device
-
1 - 100 Employee
-
Director of Quality and Regulatory
-
Aug 2014 - Dec 2015
• Develop and implement corrective action plans in response to warning letter and 483 observations. Successful close-out of warning letter. Manage internal and external audits. • Conduct assessments of the QMS processes and procedures, implement new and revised procedures to be compliant, operational and sustainable to meet internal and external regulatory requirements. • Assist VP’s in establishment of performance measurements and business metrics, quality plan, revise and lead management review program. • Design, Develop and Deliver GMP, CAPA and Design Control training for all personnel. Show less
-
-
-
Sanford Consulting, LLC
-
Scottsdale, AZ
-
Senior Consultant
-
Jan 2011 - Jul 2015
Work with clients in the pharmaceutical, medical device and biotechnical industries to develop and implement quality processes, procedures and strategies that are operational, sustainable and compliant with FDA and MDD regulations by; • Performing system gap assessments, developing and implementing corrective action plans in response to consent decree, warning letters and 483 observations. • Conducting assessments of client processes and procedures to determine compliance with internal and regulatory requirements in preparation for FDA and regulatory agency inspections. • Developing and managing remediation plans with Operations to implement compliant Material Controls, Purchasing Controls, Handling, Storage and Distribution processes and procedures. • Developing, standardizing and implementing supplier quality management processes and procedures with supply chain. • Preforming investigations, developing and implementing comprehensive root cause and corrective action plans. Developing criteria for verification of effectiveness. • Developing and communicating standards for Supplier Quality Assurance and Supplier Qualification requirements with supply chain, quality engineering and suppliers. Show less
-
-
-
Sanofi
-
France
-
Pharmaceutical Manufacturing
-
700 & Above Employee
-
Consent Decree QA SME
-
Nov 2011 - Jul 2014
• Work with project teams to define, document and implement compliant, operational and sustainable quality systems. • Perform gap assessments on quality systems, develop implementation plans to meet company commitments to FDA. • Work with project teams to successfully implement quality systems that were verified by third party auditors. • Work with project teams to define, document and implement compliant, operational and sustainable quality systems. • Perform gap assessments on quality systems, develop implementation plans to meet company commitments to FDA. • Work with project teams to successfully implement quality systems that were verified by third party auditors.
-
-
-
Validant
-
United States
-
Business Consulting and Services
-
100 - 200 Employee
-
SME Material Controls
-
Aug 2011 - Oct 2011
• Perform gap assessments of material control quality system, develop implementation plans to meet company commitments to FDA. • Work with project team to define, document and implement a compliant quality system. • Perform gap assessments of material control quality system, develop implementation plans to meet company commitments to FDA. • Work with project team to define, document and implement a compliant quality system.
-
-
-
Medela
-
Switzerland
-
Medical Equipment Manufacturing
-
700 & Above Employee
-
Team Lead Purchasing and Material Controls
-
Jan 2011 - Aug 2011
• Conduct gap assessments of the purchasing and material control processes and procedures, implement new and revised procedures to be compliant, operational and sustainable to meet internal and regulatory requirements. • Provide leadership in root cause investigation, development of corrective action plans and development of effectiveness checks. • Conduct gap assessments of the purchasing and material control processes and procedures, implement new and revised procedures to be compliant, operational and sustainable to meet internal and regulatory requirements. • Provide leadership in root cause investigation, development of corrective action plans and development of effectiveness checks.
-
-
-
CR Bard
-
United States
-
Medical Equipment Manufacturing
-
700 & Above Employee
-
Quality Engineering Manager
-
Apr 2002 - Dec 2010
•Develop and implement supply chain management program to evaluate suppliers based on objective risk criteria. Plan, organize and lead supplier quality audit requirements and improvement initiatives. Perform failure investigations at off site manufacturing locations, identify and implement improvement. •Manage OEM product quality compliance. Coordinate investigation and approve resolution of OEM customer complaints with customers and BARD international manufacturing facilities. •Develop and implement supply chain management program to evaluate suppliers based on objective risk criteria. Plan, organize and lead supplier quality audit requirements and improvement initiatives. Perform failure investigations at off site manufacturing locations, identify and implement improvement. •Manage OEM product quality compliance. Coordinate investigation and approve resolution of OEM customer complaints with customers and BARD international manufacturing facilities.
-
-
-
Varian, Inc.
-
Biotechnology Research
-
200 - 300 Employee
-
Manager, Quality Assurance
-
1997 - 2001
• Plan and conduct supplier certification assessments and perform business reviews to strengthen supply chain. • Review processes and material requirements with project teams and suppliers to improve overall quality performance. • Organize and lead facility-wide quality system programs development and implementation in contract manufacturing. • Manage quality systems for effectiveness and compliance. Establish, forecast and manage annual budget. • Program manager for new customers introducing products into facility. Show less
-
-
Education
-
California State University, Fresno
BSIE, Industrial Engineering -
Pepperdine University
MBA Program
Community
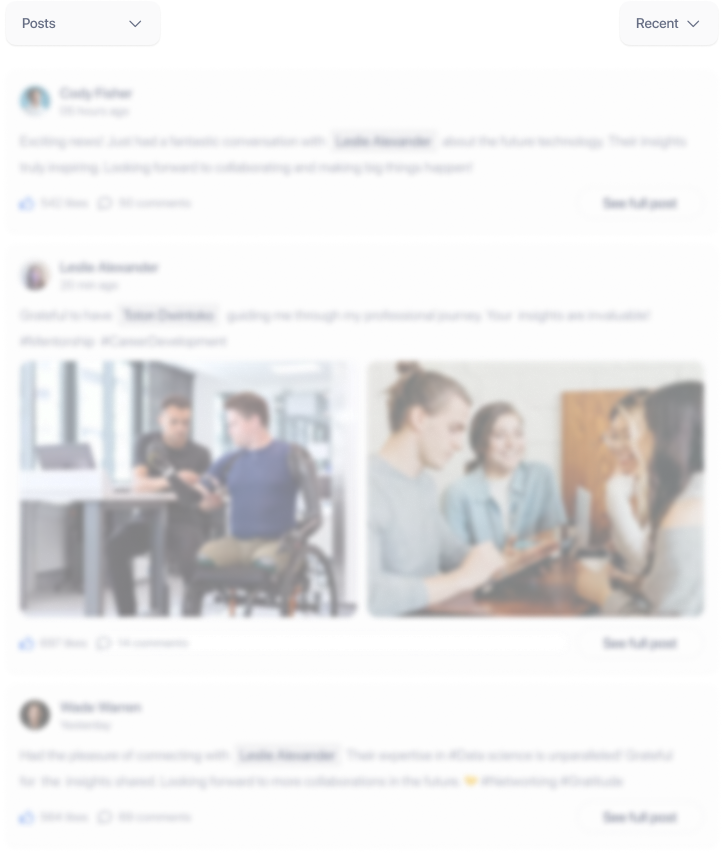