Anthony Liu
Purchasing Manager at NOVAH (Shanghai) System Technology- Claim this Profile
Click to upgrade to our gold package
for the full feature experience.
Topline Score
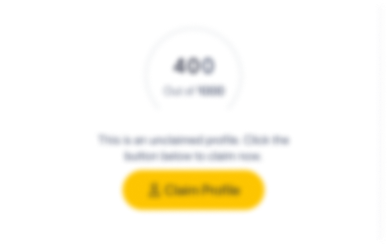
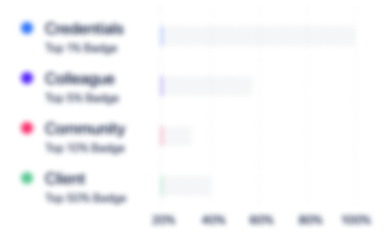
Bio


Experience
-
-
Purchasing Manager
-
Jun 2019 - Present
1. Lead two teams (raw material and finished product purchasing). Focus on managing about 20 key suppliers. The annual purchasing of raw materials is about 80 million CNY, while finished products is about 100 million CNY. The annual cost saving percentage reached 1.7% 2. Standardized the main KPI and work plan/assignments of the purchasing department. 3. Based on requirements and current situation, Established new supplier development process and supplier quarterly evaluation system. Keeps smooth running till now. 4. From requirements to bidding, to the commissioning and normal operation, three production lines with a value of 4 million have been purchased. 5. According to the historical quality data, work with the quality department to set up quality improvement objectives, includes quick-win objectives and medium/long-term objectives. 6. Support the development process of new products in supplier development, material procurement, mold manufacturing, product proofing, cost control, etc., and achieve the expected cost and quality objectives. 7. Based on the purchasing data of 2019, made 27 cost-reduction projects for standard materials, set cost saving targets and facilitate the implementation. The strategic rules of price negotiation were formulated according to the 2019 sales orders amount and bargaining experience. Show less
-
-
-
HOMAG
-
Germany
-
Machinery Manufacturing
-
700 & Above Employee
-
Strategic Sourcing Supervisor
-
May 2015 - Mar 2019
1. Lead a team of 4 people. Mainly responsible for the purchasing support of CNC equipment and automation (robot) equipment. Manage about 200 suppliers in total. The annual purchasing amount is about 250 million CNY, and the annual cost saving percentage is about 2% - 3%. 2. Participate in the process of new product development as the role of advanced purchasing. Select suppliers, Communicate and discuss technical solutions, Cost analysis and price negotiation, Sample approval, Manage projects’ schedule and cost. 3. Lead team to develop and manage suppliers of various commodity parts according to purchasing strategy. 4. Focus on the delivery time of shortage materials to defend normal production plan. Assist quality department to communicate with suppliers to solve quality problems. 5. Support global sourcing team, develop products locally and ship to each group's branches all over the world. 6. Regularly evaluate the supplier's performance in four aspects of QCDS, adjust the purchasing strategy accordingly. 7. RFQ, price comparison, cost analysis, price negotiation, determine the preferred supplier, follow up the sample quality validation process and control the progress. Support global sourcing operation. 8. Negotiate business contracts with suppliers, including General Conditions, Frame Contract, Quality Assurance and Stock Agreement, etc. 9. Focus on the annual cost saving target and measures to reduce the purchasing cost. Including but not limited to tracking the market price trend of material, price negotiation, manufacturing process optimization, change ordering methods, change suppliers and other measures. 10. Focus on the products’ localization rate. Discuss localization solutions with team and suppliers, and follow up the details and progress of sample manufacturing and quality validation. 11. According to the needs of the company, establish or optimize the relevant processes. Show less
-
-
-
Scm Group Corporate
-
Italy
-
Machinery Manufacturing
-
1 - 100 Employee
-
Purchasing Manager
-
Jul 2012 - May 2015
1. Lead a team of 5 people to be responsible for the procurement of automatic equipment parts. Manage about 50 suppliers. The annual purchasing amount is about 70 million CNY. The purchasing cost of spare parts is about 35% less than headquarters'. 2. Develop suppliers of various categories of spare parts in China, including cast parts, aluminum extrusion parts, injection molding parts, machining parts, sheet metal parts, assembly parts, electrical parts, etc. 3. Discuss with the Italian headquarters the possibility of manufacturing complete machine products and various parts in China, communicate technical details and quality standards with suppliers, RFQ, price comparison, cost analysis, follow up sample verification, and facilitate to mass production. 4. Be responsible for the export operation of global sourcing products to Italian branches and the import operation of imported parts used in Shenzhen factory. 5. Be responsible for the process quality and final inspection quality control of global sourcing products, set up inspection standards, and lead the quality team to conduct on-site inspection of products. 6. Receive the training of the whole machine to be localized in the Italian headquarters, develop all kinds of parts and components in time in China, and meet the needs of assembling the whole machine in Shenzhen factory. 7. Be responsible for the daily management of purchasing department and Quality Department of Shenzhen factory and the overall founding work of ERP system. 8. Be responsible for the purchase management of MRO materials in Shenzhen factory. Show less
-
-
-
-
Project Manager
-
Nov 2011 - Jun 2012
1. According to the requirements of the project, determine the scope of the project, select team members, establish the project team, and determine the organizational structure and responsibilities of the project, WBS. 2. Make the project schedule, review and update the project plan and project coordination table regularly to ensure that the project is completed on time 3. Implement overall quality assurance and control for the project according to the requirements of the project quality control procedure 4. Record project calendar and evaluate project performance of team members 5. Develop project risk control plan, communication rules and plan with the team 6. Coordinate all kinds of resources and problems in the process of implementation 7. Summarize project experience and lessons, update relevant standards and regulations, and commend project team members. Show less
-
-
-
-
Project Lead
-
Oct 2006 - Nov 2011
1. Responsible for the development and management of OEM products of European and American customers, from drawing communication, machine quotation, price negotiation, business terms communication, prototype production and confirmation, to the whole process follow-up of bulk orders. 2. Communicate and confirm the internal production plan of foreign orders, track the production progress and coordinate the delivery time. 3. Organize and coordinate freight forwarders and shipping companies to obtain the best shipping schedule and shipping method, and coordinate the export documents such as Bill of lading and certificate of origin. 4. Maintain daily communication and complaint handling with foreign customers. Show less
-
-
-
-
Design Engineer
-
Jul 2005 - Oct 2006
1, Components 2D/3D design 2, Components development and manufacturing. 3, Prototypes assembly and adjustment 4, Assembly process design. 5, Prototype components quality inspection and control. 6, Set components quality and inspection criteria. 1, Components 2D/3D design 2, Components development and manufacturing. 3, Prototypes assembly and adjustment 4, Assembly process design. 5, Prototype components quality inspection and control. 6, Set components quality and inspection criteria.
-
-
Education
-
Qingdao Technological University
Bachelor, Machine Design Manufacturing and Automation
Community
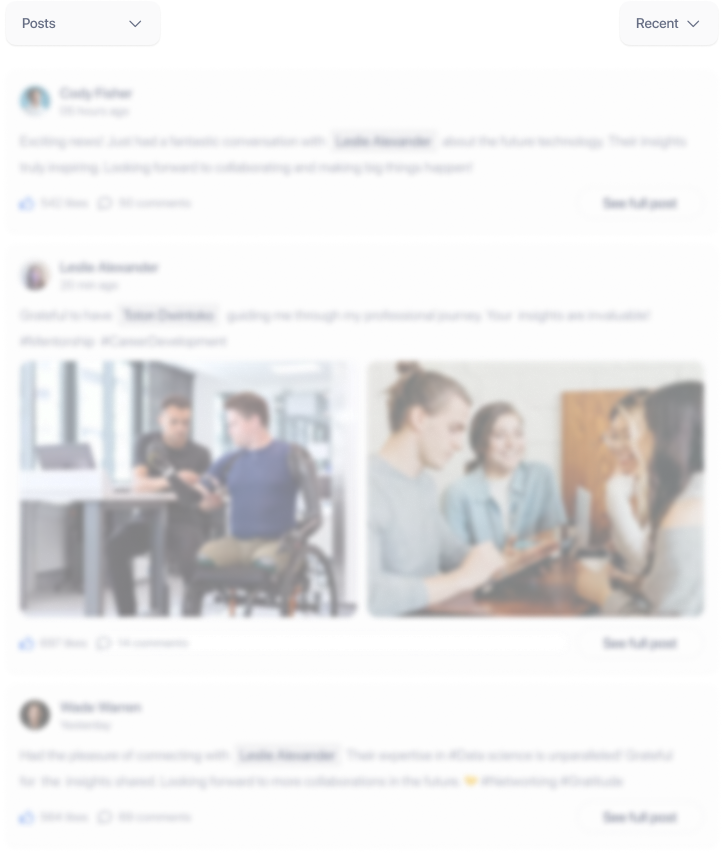