
Anthony Dulan
Vice President Operations at Boombox Beverage LLC- Claim this Profile
Click to upgrade to our gold package
for the full feature experience.
Topline Score
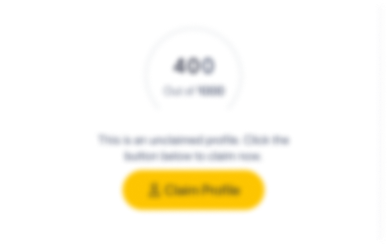
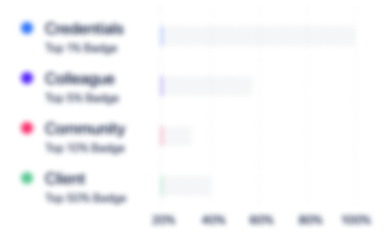
Bio
0
/5.0 / Based on 0 ratingsFilter reviews by:
Experience
-
Boombox Beverage LLC
-
United States
-
Food and Beverage Services
-
1 - 100 Employee
-
Vice President Operations
-
Oct 2019 - Present
Responsibilities:Set the vision, strategic direction, expectations, annual and long-term objectives for business developmentOwn new product development from concept through production to retailOptimize own manufacturing and supply chain strategy and development for new product lines.Work with cross-functional teams on execution operations strategyCreate and strategically adjust departments' activities, policies and practices to meet and/or exceed key performance metrics and… Responsibilities:Set the vision, strategic direction, expectations, annual and long-term objectives for business developmentOwn new product development from concept through production to retailOptimize own manufacturing and supply chain strategy and development for new product lines.Work with cross-functional teams on execution operations strategyCreate and strategically adjust departments' activities, policies and practices to meet and/or exceed key performance metrics and customer satisfaction goals.Champion efficiency ideas, cost reduction measures and assist with implementation of changes within areas of responsibilityManage partner relationships and contract negotiations for new business growth.Optimize systems for beverage retail management and operations.Implement cost reduction strategies in all aspects of the organizations supply chain transactions and activitiesKeep employees informed as to company/department plans and progressEnsure full Safety and OSHA rules are in place and followed in accordance with company goalsMaintain compliance for all regulatory requirements throughout company. Show more Show less
-
-
-
-
Director Of Plant Operations
-
Mar 2019 - Nov 2019
Building a manufacturing plant to help reduce gun violence in the city of Chicago. By creating true opportunities for individuals to learn key manufacturing functions within a working environment.Arine Duncan the former secretary of education of the United States Of America has selected a few key team members to help start a other faze of his vision thru Chicago Cred. , he continues to think outside the box to develop new and exciting was to provide opportunities to change people's… Building a manufacturing plant to help reduce gun violence in the city of Chicago. By creating true opportunities for individuals to learn key manufacturing functions within a working environment.Arine Duncan the former secretary of education of the United States Of America has selected a few key team members to help start a other faze of his vision thru Chicago Cred. , he continues to think outside the box to develop new and exciting was to provide opportunities to change people's lives. Chicagocred.com Show more Show less
-
-
-
-
Plant Manager
-
2016 - 20182 years
Responsible for the P&L of a 300,000 square foot production facility with 168 employees, 400 million in production annually.Lead a team across multiple functional areas by using lean manufacturing technics while delivering superior customer service. Coach, train and develop leaders within our organization to successfully staff and empower team to deliver against established standards, goals and profit objectives.Foster open lines of communication and teamwork while producing… Responsible for the P&L of a 300,000 square foot production facility with 168 employees, 400 million in production annually.Lead a team across multiple functional areas by using lean manufacturing technics while delivering superior customer service. Coach, train and develop leaders within our organization to successfully staff and empower team to deliver against established standards, goals and profit objectives.Foster open lines of communication and teamwork while producing best-in-class results and business practices.In first year exceeded overall throughput of cases produce while managing multiple capex projects to help make plant run efficient.Reduce OSHA recordables down by improving plant awareness with all team member Second year Implemented several accounting improvements for 6 departments, MTD expense summaries and standardized plan files for direct expenses and labor cost.Compiled month-end and year end financials to review with outside vendors.Direct the plant financial reporting and control system using ERP and SAPFocus on leadership program and high preforming management teams to help set goals and generate an overall improve production plan.Established KPI and objective for the plant through Lean manufacturing principles, Drive tree charts, 5s and burst kaizen techniques for all salary employees.Reduce operation downtime by 5%Reduce line bottle necks by line balancing by 15%Automated water system to help reduce QC check time 10%Installation of high speed automated labeler for bottling line with an improve of 25% Show more Show less
-
-
-
Weetabix North America / Barbara's Bakery Inc.
-
United States
-
Food and Beverage Manufacturing
-
1 - 100 Employee
-
North America Engineering and Mainteance Manager
-
2014 - 20162 years
Overseeing six facilities Accomplish organization goals by accepting ownership for accomplishing new and different requests; exploring opportunities to add value to job accomplishments.Monitor multiple programs within each department to ensure that milestones and deliverables are achieved according to the quality standards and Key Performance Indicators.Drive initiatives in the management team and organizationally that contribute to long-term operational excellence that will… Overseeing six facilities Accomplish organization goals by accepting ownership for accomplishing new and different requests; exploring opportunities to add value to job accomplishments.Monitor multiple programs within each department to ensure that milestones and deliverables are achieved according to the quality standards and Key Performance Indicators.Drive initiatives in the management team and organizationally that contribute to long-term operational excellence that will allow for scalable growth.Support long-term strategy by trending OEE and MOH.Expected to provide analysis of trends and forecasting.Recognition of potential business issues and prioritization as applicable.Approve and maintain internal Standard Operating Procedures (SOPs).Track plant performance, manage client, projects management and R&D teams.Strong Knowledge in handling CAPEX projects for multiple facilities. Initiate and manages analytical and operational excellence efforts to improve overall productivity and efficiency within all plants by using lean management practices.Manages the personnel, process flows and budget of the assigned functional areas.Monitors and safeguards the quality of the assigned areas.Cut waste by 4% by implementing new manufacturing design to current equipment with total cost saving of 2 million dollars. Show more Show less
-
-
-
-
Operations Superintendent
-
2006 - 20137 years
Direct production of 600 employees in a pork processing plant, quality, maintenance and sanitation duties for a union plant ensuring corporate goals are achieved.Review production orders to make decisions concerning inventory and staffing requirements, work procedures and assignments, impacting budgetary limitations and time constraints.Develop or implement production tracking or quality control systems, analyzing production, quality control, maintenance, or other operational… Direct production of 600 employees in a pork processing plant, quality, maintenance and sanitation duties for a union plant ensuring corporate goals are achieved.Review production orders to make decisions concerning inventory and staffing requirements, work procedures and assignments, impacting budgetary limitations and time constraints.Develop or implement production tracking or quality control systems, analyzing production, quality control, maintenance, or other operational processes to detect production problems.Assess operations and confer with Production Supervisors to resolve production or processing problems.Set and monitor product standards, examining samples of raw products or directing testing during processing, to ensure finished products are of prescribed quality.Prepare and maintain production reports or personnel records.Coordinate and recommend procedures for facility and equipment maintenance and modification, including the replacement of machines.Ensure plant follows USDA, EPA and OSHA regulations to ensure plant maintains compliance.Train, evaluate, discharge staff, and resolve personnel grievances. Show more Show less
-
-
-
CICI Pizza
-
United States
-
Restaurants
-
Regional Manager
-
Jan 2000 - Dec 2004
-
-
-
-
Plant Manager
-
Aug 1989 - Dec 1999
-
-
Education
-
Kansas University
-
Americomp
-
Washburn Institute of Technology
Community
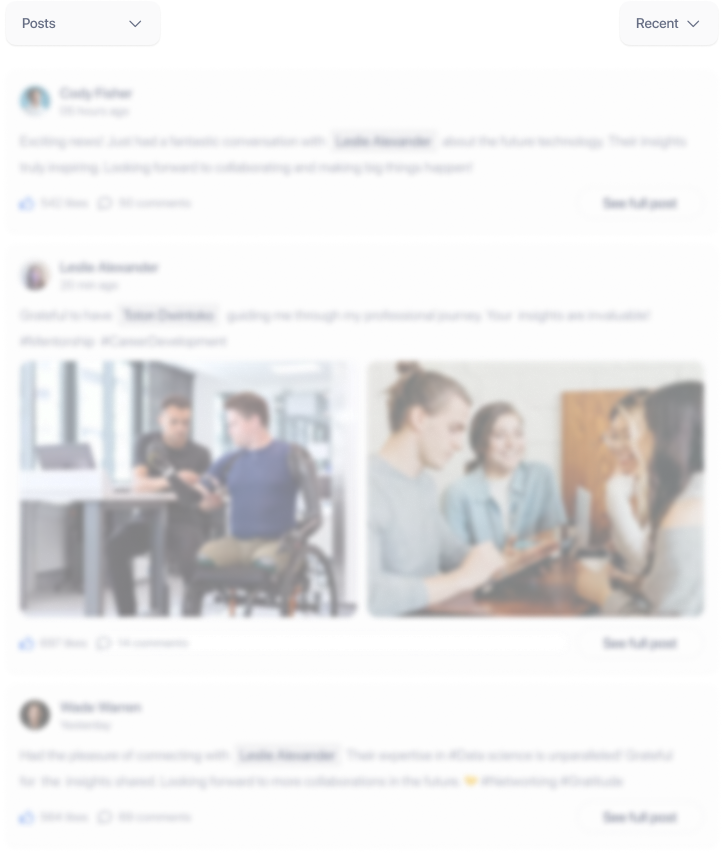