Anthony Britch
Purchaser, ERP Systems Management, Inventory & Supply Chain at Lustre Products Ltd.- Claim this Profile
Click to upgrade to our gold package
for the full feature experience.
-
English -
Topline Score
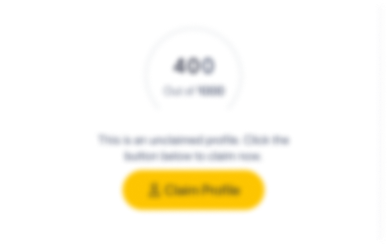
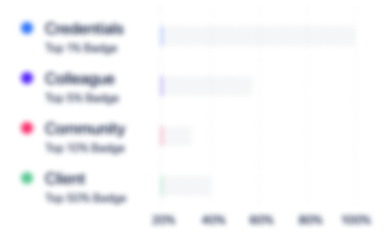
Bio

Jon Freeman
I have always found Anthony to be intelligent and knowledgeable about many topics, both work-related and general interest. He has a keen understanding of operational issues faced by manufacturers through the various roles he has held. He is insightful, detailed, and can work independently on projects or as a member of a team. He is confident in his understanding of scheduling and many other operational aspects in manufacturing but is willing to listen to others’ points of views to arrive at a general consensus for the optimum direction to take. He understands the cost/benefit choices in making decisions and can contribute positively in charting a path to success when dealing with both operational and administrative-minded staff.

Mike Olson
I worked with Anthony for 4 years at Clean Energy Compression. In that time Anthony had a variety of roles in which he performed with a high degree of knowledge and expertise. Anthony had an understanding of production scheduling, ERP system changes and process change. He became a pivotable person in our team as we enhanced our ERP system with change management. Anthony had an ability to make the processes he was reviewing to be understandable to all people. His ability to discuss items with a wide audience was invaluable. Additionally, Anthony worked well within the team environment. He worked with people remotely and internally and ensured that this communication was smooth. His ability to collaborate is excellent. I would recommend Anthony for any role which related to these three areas as he excelled in his position.

Jon Freeman
I have always found Anthony to be intelligent and knowledgeable about many topics, both work-related and general interest. He has a keen understanding of operational issues faced by manufacturers through the various roles he has held. He is insightful, detailed, and can work independently on projects or as a member of a team. He is confident in his understanding of scheduling and many other operational aspects in manufacturing but is willing to listen to others’ points of views to arrive at a general consensus for the optimum direction to take. He understands the cost/benefit choices in making decisions and can contribute positively in charting a path to success when dealing with both operational and administrative-minded staff.

Mike Olson
I worked with Anthony for 4 years at Clean Energy Compression. In that time Anthony had a variety of roles in which he performed with a high degree of knowledge and expertise. Anthony had an understanding of production scheduling, ERP system changes and process change. He became a pivotable person in our team as we enhanced our ERP system with change management. Anthony had an ability to make the processes he was reviewing to be understandable to all people. His ability to discuss items with a wide audience was invaluable. Additionally, Anthony worked well within the team environment. He worked with people remotely and internally and ensured that this communication was smooth. His ability to collaborate is excellent. I would recommend Anthony for any role which related to these three areas as he excelled in his position.

Jon Freeman
I have always found Anthony to be intelligent and knowledgeable about many topics, both work-related and general interest. He has a keen understanding of operational issues faced by manufacturers through the various roles he has held. He is insightful, detailed, and can work independently on projects or as a member of a team. He is confident in his understanding of scheduling and many other operational aspects in manufacturing but is willing to listen to others’ points of views to arrive at a general consensus for the optimum direction to take. He understands the cost/benefit choices in making decisions and can contribute positively in charting a path to success when dealing with both operational and administrative-minded staff.

Mike Olson
I worked with Anthony for 4 years at Clean Energy Compression. In that time Anthony had a variety of roles in which he performed with a high degree of knowledge and expertise. Anthony had an understanding of production scheduling, ERP system changes and process change. He became a pivotable person in our team as we enhanced our ERP system with change management. Anthony had an ability to make the processes he was reviewing to be understandable to all people. His ability to discuss items with a wide audience was invaluable. Additionally, Anthony worked well within the team environment. He worked with people remotely and internally and ensured that this communication was smooth. His ability to collaborate is excellent. I would recommend Anthony for any role which related to these three areas as he excelled in his position.

Jon Freeman
I have always found Anthony to be intelligent and knowledgeable about many topics, both work-related and general interest. He has a keen understanding of operational issues faced by manufacturers through the various roles he has held. He is insightful, detailed, and can work independently on projects or as a member of a team. He is confident in his understanding of scheduling and many other operational aspects in manufacturing but is willing to listen to others’ points of views to arrive at a general consensus for the optimum direction to take. He understands the cost/benefit choices in making decisions and can contribute positively in charting a path to success when dealing with both operational and administrative-minded staff.

Mike Olson
I worked with Anthony for 4 years at Clean Energy Compression. In that time Anthony had a variety of roles in which he performed with a high degree of knowledge and expertise. Anthony had an understanding of production scheduling, ERP system changes and process change. He became a pivotable person in our team as we enhanced our ERP system with change management. Anthony had an ability to make the processes he was reviewing to be understandable to all people. His ability to discuss items with a wide audience was invaluable. Additionally, Anthony worked well within the team environment. He worked with people remotely and internally and ensured that this communication was smooth. His ability to collaborate is excellent. I would recommend Anthony for any role which related to these three areas as he excelled in his position.

Credentials
-
Consumer Electronics
Vancouver Community College -
High School Grad
Matthew McNair Secondary School -
Journalism
Kwantlen Polytechnic University
Experience
-
Lustre Products Ltd.
-
Canada
-
Manufacturing
-
1 - 100 Employee
-
Purchaser, ERP Systems Management, Inventory & Supply Chain
-
Jan 2023 - Present
-
-
-
-
Buyer Assistant, Non-Conformance Material
-
May 2022 - Nov 2022
• Collaborating with Vendors on warranty claims through the Non-conformance report systems in Agile and Dynamics AX. • Responsible for defective part replacements through warranty or credit totaling $75,000 over two months. Manually created Purchase Orders to order replacement parts for Production and using Purchase Requisitions. • Working with Finance to solve Purchase Order/Invoice discrepancies and Warehouse/Quality to analyze and solve Inventory transaction issues. • Provided ERP interpretation of information for Individuals and reports for different departments and Management daily. • Assembled the IOM Manuals for compressor orders. Working collaboratively with Production, Engineering and Quality to complete each Manual. Extensive rewrite on Work Instruction for IOM Assembly. Show less
-
-
-
SOFTAC Systems Ltd
-
Canada
-
Appliances, Electrical, and Electronics Manufacturing
-
1 - 100 Employee
-
Materials Expeditor
-
Feb 2022 - Feb 2022
One week contract – Worked with Vendors to Expedite material to help Projects back on track. One week contract – Worked with Vendors to Expedite material to help Projects back on track.
-
-
-
-
Bill of Materials Administrator
-
May 2021 - May 2021
Three week contract - Reverse engineered landscape lighting products and created the Bill of Materials for each finished assembly. Three week contract - Reverse engineered landscape lighting products and created the Bill of Materials for each finished assembly.
-
-
-
Merit Kitchens Ltd.
-
Building Materials
-
1 - 100 Employee
-
Master Scheduler / Business Process Technician
-
Jan 2019 - Sep 2019
For over 40 years Merit Kitchens has been a leader in the design and manufacture of kitchen cabinetry. Position Duty Highlights: • Leveraged business process expertise in the design of the Dispatch Reports for Shop Floor to manage 8000+ work orders. • Created, managed Time Study on shop floor to determine data for, and setup of, Scheduling Module of the Infor Visual ERP System. • Created prototype Multi-Level BOM design to replace the Company's current flat design. • As the Project Manager I directed code changes to the auto-created work order process to work with the ERP Scheduling Module. • Designed and deployed complex Microsoft Access queries to review and maintain the data integrity of the ERP system. This was used by the Engineering/Work Order Review team who were able to close long dormant work orders, complete the issue of parts and monitor Shop Floor labour entries, all of which were not monitored previously. • As project manager, documented Business Process for rescheduling work orders and tracked project status with Microsoft Project for Executive Management. Show less
-
-
-
-
Master Scheduler / ERP Systems Specialist (Business Analyst) / 3rd Party Inspection Coordinator
-
2008 - 2018
2011-2018 Production Control Sr. Trainer & Development Business Process Analyst (ERP System Specialist) Third Party Inspection Coordinator 2008-2012 Production Control Manager Master Scheduler/ Production Planner – Assembly Production Planner/Buyer - Machine Shop/Fabrication Shop • Monitored and expedited the flow of materials, components, and production from order through receipt, production, inspection, and shipping to ensure on time delivery to the customer • Responsible for the development and implementation of material requirements, planning, and scheduling systems within the ERP system. • Schedule and plan the production and purchasing of goods, components, and raw materials to successfully meet our confirmed delivery dates, including the coordination of the production schedule with cross-functional team members • Collaborated with Management, Sales, Purchasing & Production to create, manage, and communicate the Master Schedule; the balancing of a Sales Forecast & Customer’s requested delivery with plant capacity, logistics of outside contract manufacturers and their on-time delivery. • Developed and successfully implemented the Production Control Dept.’s structure that included the determination of Planning/Purchasing positions and the creation of job descriptions. • Responsible for the training, coaching and development of planners/purchasers on methods of MRP, Production Planning/Scheduling & Supply Chain, leading to the improved flow of Work Orders in Production, the identification, resolution, and earlier reporting of critical shortages. • As a business process analyst, I was the main post-implementation support for the entire company of the AX Dynamics ERP system. I collaborated with partners and internal staff to identify, document, and lead the resolution of hundreds of process challenges across all departments . Show less
-
-
-
Rimex Supply Ltd.
-
Brazil
-
Software Development
-
Production Planner
-
2005 - 2008
RIMEX is a world leading custom manufacturer of all wheels and rims for mining, forestry, agricultural and industrial applications Positions Held Production Planner 2005-2008 (3 years) Duties: review MRP output, create/schedule Work Orders to ensure on-time delivery & meet customer demand, coordinate with Engineering dept. for Work Order Route revision, maintain Inventory by review of transaction errors, coordinated issuing of inventory to the shop floor. Reported the progress of production to Operations and Upper Management. Show less
-
-
Education
-
APICS courses CPIM program
CPIM (several courses) -
Kwantlen Polytechnic University
Certificate, Journalism -
Vancouver Community College
Diploma, Consumer Electronics -
kwantlen College
Certificate/Diploma, Journalism
Community
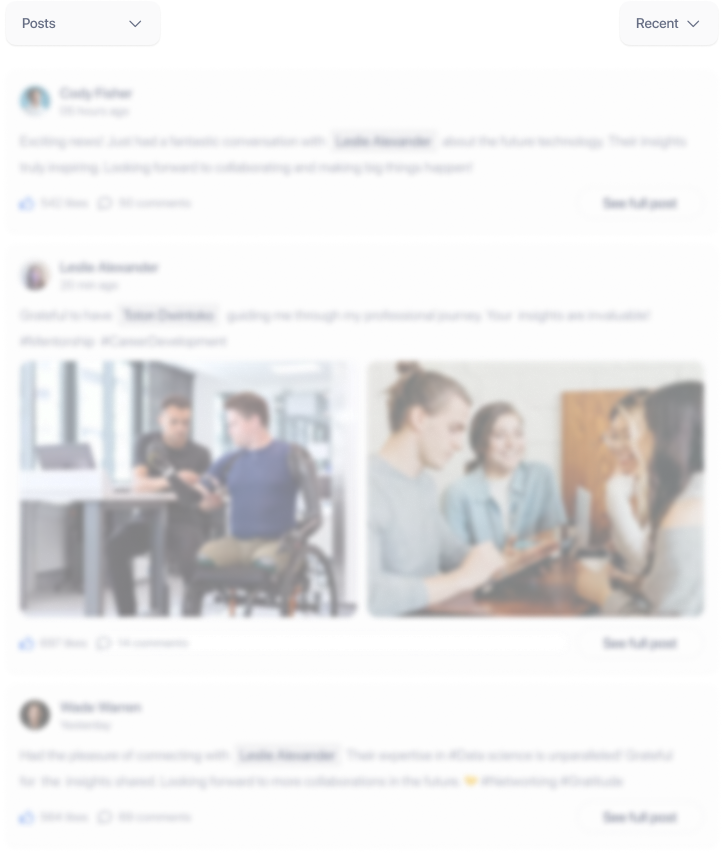