Ann Sommerfeldt
Plant Director at Advantek- Claim this Profile
Click to upgrade to our gold package
for the full feature experience.
Topline Score
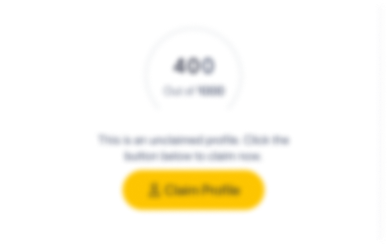
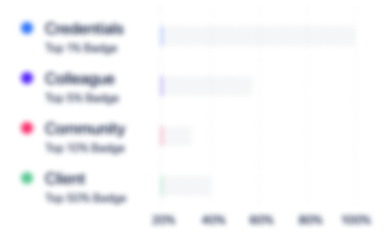
Bio


Credentials
-
Certified Supply Chain Professional (CSCP)
APICS -
Certified in Production and Inventory Management (CPIM)
APICS
Experience
-
Advantek
-
United States
-
Semiconductor Manufacturing
-
100 - 200 Employee
-
Plant Director
-
Jul 2019 - Present
-
-
Supply Chain Manager
-
Aug 2017 - Jul 2019
-
-
-
Dynamic Fitness & Strength
-
United States
-
Wellness and Fitness Services
-
1 - 100 Employee
-
Master Production Scheduler
-
Jul 2016 - Aug 2017
-
-
-
Neenah Enterprises, Inc.
-
United States
-
Manufacturing
-
200 - 300 Employee
-
Planning and Scheduling Manager
-
Aug 2014 - Jul 2016
--Track and provide management with daily statistics pertaining to on-time delivery, customer orders, inventory levels and returns costs --Work with Sales and Customer Service departments to ensure customers are aware of delivery status and strive to avoid any delay in delivery --Work with scheduling clerks to reduce Work in Progress (WIP) inventory levels, create and ensure appropriate lead times and develop a master scheduling system/ process that meets the vision of senior leadership --Review appropriate production and operational reports to establish and monitor proper plant capacity based upon machine capability, manufacturing processes and procedures --Monitor and measure employee performance and development, providing necessary coaching and feedback to subordinate employees that reinforces the Company’s customer service expectations and enables success for subordinate employees --Train new employees on the proper scheduling procedures, the use of computer systems, appropriate safety protocol and company products to ensure compliance with standard company practices --Initiate and process personnel actions involving transfers, promotions, performance evaluations, salary increases, and disciplinary actions Show less
-
-
-
Rexnord
-
United States
-
Machinery Manufacturing
-
700 & Above Employee
-
Senior Materials Analyst
-
Mar 2012 - Aug 2014
--Materials planning – monitor all inventory levels to ensure timely delivery and maintain all metrics for performance --Coordinate/Schedule all orders that are poured in the foundry and all orders that route through the machine shop --Work with engineering to determine the resources needed to meet project schedules --Schedule all Foundry Technical Services and Patter Shop Operations --Provide optimal level of customer service and ensure all material and product availability for customers --Lead SAP Contact for Mill Products – main resource through new implementation, testing and training rollout --Receive project plans and information from other departments and use this information to determine what materials will be needed and when --Create a smooth flow of goods within the organization by working with Material Manager and other departments to ensure On Time Delivery of Products Show less
-
-
-
Mercury Marine
-
United States
-
Manufacturing
-
700 & Above Employee
-
US Outboard Demand Planning Analyst
-
Nov 2009 - Mar 2012
--Coordinate overall US Demand Planning activities, including Statistical Forecasts, Macro- economic plans, Sales and Marketing Market Intelligence, Customer Collaboration, Financial Plans and New Product Development--Develop demand forecasts at multiple levels of aggregation for multiple time horizons--Interact with sales, marketing and customer finance to understand demand forecast drivers--Lead and/or participate in US Demand Planning cross-functional meetings in the SIOP Process--Accountable for the analysis and development of the US Outboard Demand Plan with associated measurements of forecast accuracy and bias--Provide input to the Supply Planning organization in developing inventory strategies on existing items, new products and product phase outs--Prepare and maintain relevant reports pertaining to the demand planning process--Drive US Forecast Accuracy Improvements--Maintain demand planning systems and software, enter and modify data and ensure correctness of product hierarchy--Manage multiple projects and utilize lean six sigma methodology Show less
-
-
Buyer/Planner
-
Nov 2007 - Dec 2009
--Evaluate potential suppliers based on their product quality, cost, delivery times and customer service--Negotiate contracts that specify price, payment terms and delivery schedules--Second source strategic commodities as needed to mitigate risk--Review open requirements, monitoring vendor performance, and expediting where necessary.--Assure that problems relating to delivery, quality or pricing are promptly conveyed to the vendor and resolved in a timely manner per standard procedures--Manage the amount of inventory needed to produce the company’s products and make sure that quality and pricing is adhered to for profitability and customer satisfaction--Create and manage purchase orders and request for quotes to include technical documents, pricing, delivery, and key milestones to ensure on-time receipt of materials for manufacturing operations--Maintain the integrity of MRP parameters (lot/order size, lead time, and safety stock)--Analyze/adjust inventory levels to coincide with lead time changes Show less
-
-
Education
-
UW Oshkosh MBA Program
Master of Business Administration - MBA, 3.7 GPA -
University of Wisconsin Oshkosh
Operations Management
Community
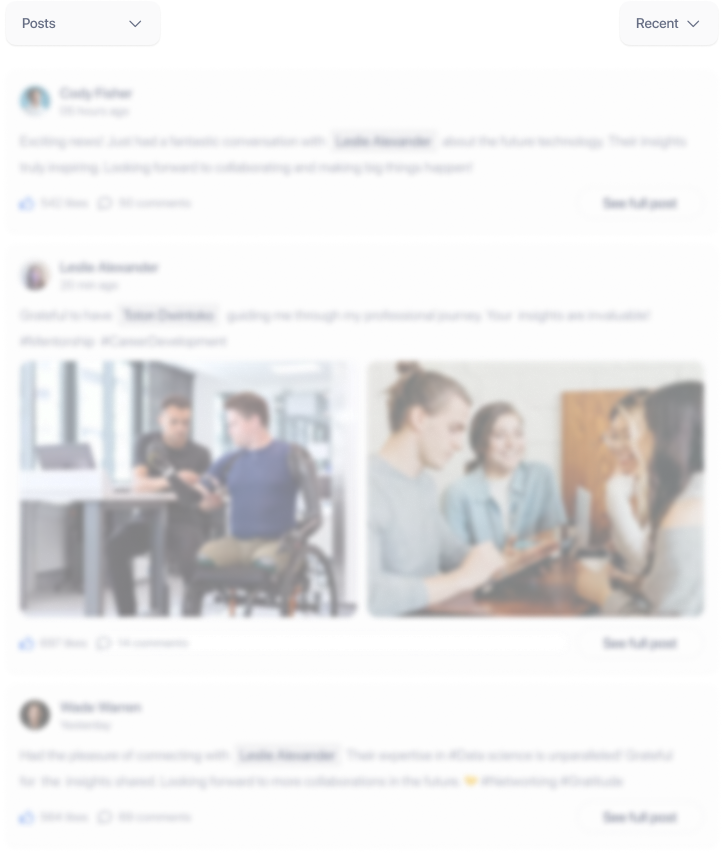