Ankur Seth
Head Of Supply Chain Management at Trouw Nutrition India- Claim this Profile
Click to upgrade to our gold package
for the full feature experience.
Topline Score
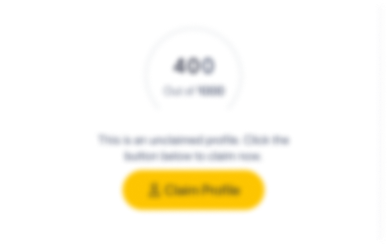
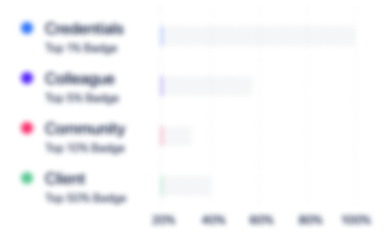
Bio


Credentials
-
Supply Chain Management
INTERNATIONAL ACADEMY FOR CERTIFICATION AND TRAININGNov, 2019- Oct, 2024 -
Bread and Bakery Technology
National Skill Development Corporation
Experience
-
Trouw Nutrition India
-
India
-
Food and Beverage Manufacturing
-
1 - 100 Employee
-
Head Of Supply Chain Management
-
Mar 2020 - Present
-
-
-
Jubilant FoodWorks Ltd.
-
India
-
Food & Beverages
-
700 & Above Employee
-
Manager
-
Apr 2019 - Mar 2020
-
-
Assistant Manager Supply Chain
-
Jul 2017 - Mar 2020
• Publishing KPIs for Global Supply Chain Council• Leading multi-functional teams at various levels.• Ensuring that all projects run smoothly and without problem.• Carrying out Fleet Management projects, to ensure optimization of the resources• Ensuring No delay in dispatches due to product unavailability/production short fall• Ensuring Safety of whole commissary, • Leading the Food Safety team,• Maintain SAP working of all operations• Carrying out periodic stock checks• Budget management and cost tracking• Monitoring freight costs, negotiating prices for supply chain services.• Keeping accurate records of all distribution that takes place.• Scheduling appropriate modes of transportation for goods• Customer care help desk query resolution• Calculating total supply chain and logistical costs.• Planning in detail the movement of goods from one point to another.• Lean Manufacturing Process & Implementation • TPM & TQM Implementation• 6 Sigma Implementation• Visual Management Implementation @ SCC• Compliance with all statutory rules and regulations as per respective state /central government regulations • Asset Protection (Trays, Inventory, machines, dough trolley)• Ensure minimal deviations in audits / inspections and timely closure of all gaps• Ensure no major findings in Internal audits• Saving in cost against the budget with optimizing the resources• Carrying out projects for Optimization of Resources• Automation of plant • Wastage control• OEE & USLE Tracking • Capability Mapping and SCFx roll out• Develop culture of Quality Assurance at Supply Chain Center• No Food Safety complaints• HACCP and FSMS implementation • TPM/TQM/Lean manufacturing• Ensuring Temperature compliance • DPI International audit score target +90%• Redefine Skill Levels, Enhance Organization Capability• Multi-skilling of peoples & job rotation
-
-
-
Top N Town
-
India
-
Food and Beverage Services
-
1 - 100 Employee
-
Factory Manager
-
Jun 2015 - Jun 2017
• To ensure the proper running of factory operations • New product development for bakery plant i.e.; flavors application and recipes development of all types of bread and bakery products. eg; Buns, Breads, Rusk/Toast, Dry Cakes, Muffins, Brownies, Bar Cakes, Cream Cakes, Themed Desserts etc., • Setting up the factory techno-commercially. • Inventory controlling, BOM making, tracking product distribution etc. • Setting up the market by helping market team by initiating new projects, product trials and many other promotional activities planning.
-
-
-
Parle Products Pvt. Ltd
-
India
-
Food and Beverage Services
-
700 & Above Employee
-
Business Development Executive
-
Aug 2011 - May 2015
• Developed and standardized the Parle Rusk in co-ordination with the QA department, • Closely Monitor Day Wise and Weekly Production on prorate Basis. • Ensuring the proper deliveries of materials and fulfilments of demands • Check and sign documents related to all techno-commercial working. • Closely monitor all testing in Lab, and Ensure working of FST, • Critical process parameter through check sheet. • Up to date Regular HACCP Implementation Activity through meeting and report. • Inventory of raw material & packaging to be controlled, • Daily Stock & Value of raw and packing material and finished product to be checked • Surveying market and make the correctives at unit end if any problems found. • Making Preventive list on Weekly Basis in order for smooth working in plant. • Physical and Mental Involvement on shop floor. • Completing paperwork relating to the export of goods to foreign countries. • Managing contractor and subcontractor activities. • Booking transport through preferred suppliers.
-
-
Education
-
Uttar Pradesh Technical University
Bachelor of Technology - BTech, Biotechnology
Community
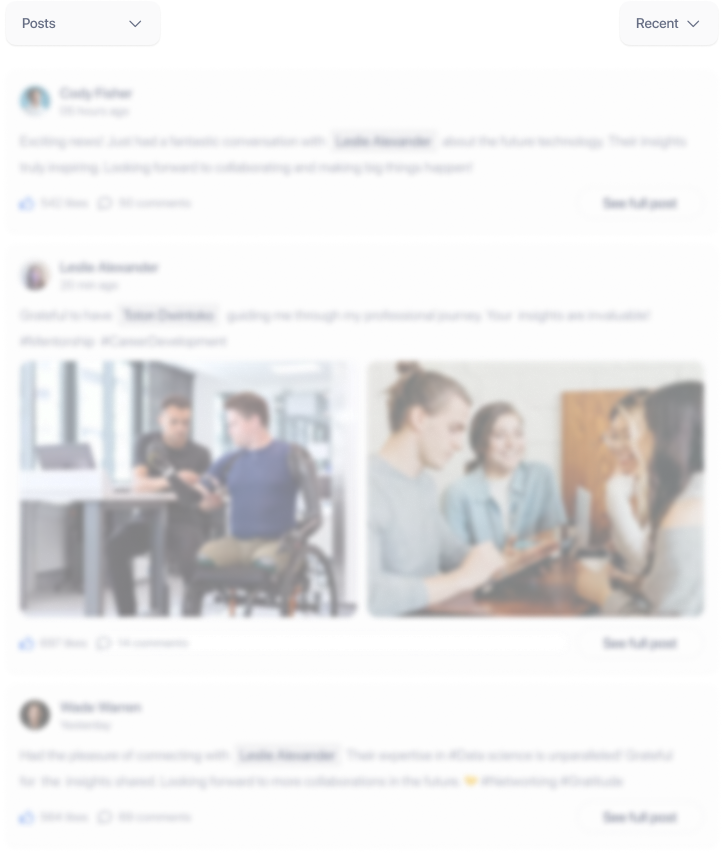