Andrew Margrie
Business Transformation Coach at Sharing In Growth UK Limited- Claim this Profile
Click to upgrade to our gold package
for the full feature experience.
Topline Score
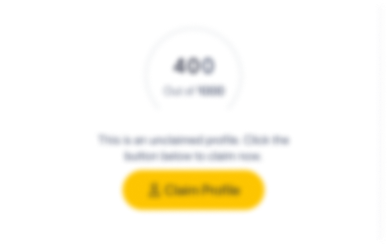
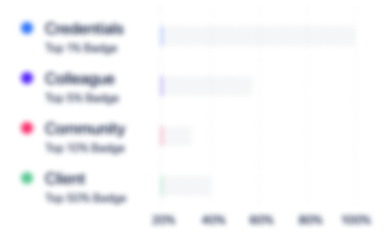
Bio

Dale Gooding
I had the privilege of working with Andrew at Renold Clutches and Coupling. It is rare to find someone of Andrew's ability in lean and process thinking, as well as wisdom in building teams and personal credibility.

Dave Lunn
I had the pleasure of working with Andrew for two years at Cooper Security, part of Cooper Industries. Andrew was responsible for our global operations team and in just two years had totally transitioned manufacturing from Europe to Asia. His drive, tenacity, and attention to detail can only be surpassed by his level integrity in all that he does. In the first year alone, key business metrics vastly improved from which customers and the business started to feel the benefit. Andrew was a valued member of senior management team where his contributions would often provide a good counter balance of opinion. Andrew is also a great coach and mentor from which both his team and I benefited.

Dale Gooding
I had the privilege of working with Andrew at Renold Clutches and Coupling. It is rare to find someone of Andrew's ability in lean and process thinking, as well as wisdom in building teams and personal credibility.

Dave Lunn
I had the pleasure of working with Andrew for two years at Cooper Security, part of Cooper Industries. Andrew was responsible for our global operations team and in just two years had totally transitioned manufacturing from Europe to Asia. His drive, tenacity, and attention to detail can only be surpassed by his level integrity in all that he does. In the first year alone, key business metrics vastly improved from which customers and the business started to feel the benefit. Andrew was a valued member of senior management team where his contributions would often provide a good counter balance of opinion. Andrew is also a great coach and mentor from which both his team and I benefited.

Dale Gooding
I had the privilege of working with Andrew at Renold Clutches and Coupling. It is rare to find someone of Andrew's ability in lean and process thinking, as well as wisdom in building teams and personal credibility.

Dave Lunn
I had the pleasure of working with Andrew for two years at Cooper Security, part of Cooper Industries. Andrew was responsible for our global operations team and in just two years had totally transitioned manufacturing from Europe to Asia. His drive, tenacity, and attention to detail can only be surpassed by his level integrity in all that he does. In the first year alone, key business metrics vastly improved from which customers and the business started to feel the benefit. Andrew was a valued member of senior management team where his contributions would often provide a good counter balance of opinion. Andrew is also a great coach and mentor from which both his team and I benefited.

Dale Gooding
I had the privilege of working with Andrew at Renold Clutches and Coupling. It is rare to find someone of Andrew's ability in lean and process thinking, as well as wisdom in building teams and personal credibility.

Dave Lunn
I had the pleasure of working with Andrew for two years at Cooper Security, part of Cooper Industries. Andrew was responsible for our global operations team and in just two years had totally transitioned manufacturing from Europe to Asia. His drive, tenacity, and attention to detail can only be surpassed by his level integrity in all that he does. In the first year alone, key business metrics vastly improved from which customers and the business started to feel the benefit. Andrew was a valued member of senior management team where his contributions would often provide a good counter balance of opinion. Andrew is also a great coach and mentor from which both his team and I benefited.
0
/5.0 / Based on 0 ratingsFilter reviews by:
Credentials
-
Certified Lean Sigma Master Black Belt
Safran University -
Chartered Engineer
Engineering Council
Experience
-
Sharing In Growth UK Limited
-
United Kingdom
-
Business Consulting and Services
-
1 - 100 Employee
-
Business Transformation Coach
-
Oct 2022 - Present
-
-
-
Rotork
-
United Kingdom
-
Industrial Machinery Manufacturing
-
700 & Above Employee
-
Interim Plant Manager
-
Mar 2022 - Jun 2022
Design and manufacture of valve actuators and gearboxes. Design and manufacture of valve actuators and gearboxes.
-
-
-
Albion Saddlemakers Co. Ltd.
-
United Kingdom
-
Sporting Goods
-
1 - 100 Employee
-
Managing Director
-
2019 - 2021
Design and manufacture of equestrian saddles and accessories. Full business financial and commercial responsibility. • Maintained positive cashflow across the three COVID-19 national lockdowns and Brexit. • Reversed a three-year downward trend in profitability through increased labour productivity and material cost reduction. • Delivered all-time-high customer on-time delivery performance achieving zero arrears. Design and manufacture of equestrian saddles and accessories. Full business financial and commercial responsibility. • Maintained positive cashflow across the three COVID-19 national lockdowns and Brexit. • Reversed a three-year downward trend in profitability through increased labour productivity and material cost reduction. • Delivered all-time-high customer on-time delivery performance achieving zero arrears.
-
-
-
-
Interim Operations Director
-
2016 - 2018
Led the transition of the business into a fully process-based organisation with clear responsibilities and accountability through the introduction of standard work and a data driven governance cycle. Delivered benefits included: • Embedded pro-active employee engagement through effective training, coaching, objective setting and performance reviews. • Elimination of revenue loss through late delivery and customer returns. • 50% reduction in site safety risk rating in first 12 months of management programme implementation. Show less
-
-
-
Renold Couplings
-
Mechanical Or Industrial Engineering
-
Operations Director
-
2015 - 2016
Design and manufacture of power transmission couplings. 70 reporting employees at sites in the UK and China. • Successful transition to M3 Enterprise Resource Planning software platform as the pilot site for Renold. Design and manufacture of power transmission couplings. 70 reporting employees at sites in the UK and China. • Successful transition to M3 Enterprise Resource Planning software platform as the pilot site for Renold.
-
-
-
-
Division Operations Manager
-
2013 - 2015
Design and manufacture of hydraulic actuation and control systems. 200 reporting employees at sites in the UK, Sweden and Czech Republic. • 20% increase in labour productivity achieved through employee engagement in process improvements delivering highest ever levels of business profitability. • Customer returns and cost of poor quality reduced by over 50% year-on-year through the introduction of non-conforming material controls and effective problem solving. • Customer on-time delivery increased to all-time high levels through improved works order and capacity management controls. Show less
-
-
-
Messier-Bugatti-Dowty
-
France
-
Business Consulting and Services
-
1 - 100 Employee
-
Vice President - Improvement Methods & Capabilities
-
2012 - 2012
Design and manufacture of aircraft landing and braking systems.Member of the multi-national team created following the merger of Messier-Dowty, Messier-Bugatti and Messier-Services to establish a single strategy and operational infrastructure for business improvement.
-
-
Vice President Lean-Sigma, UK and North America
-
2011 - 2012
With the VP France & Asia, developed the global business improvement strategy, with direct responsibility for its deployment at 7 sites in the UK, Canada, USA and Mexico.• Improvement Facilitator to 2 Divisional CEOs and 3 Functional Executive VPs.• Developed and implemented a standard Lean-Sigma deployment roadmap establishing common best practices including training, shop-floor control systems and improvement project management.• Achieved total annualised cost savings from improvement activities exceeding €40m during 2011. Show less
-
-
Value Creation & Process Improvement Director
-
2009 - 2011
Responsible for the development of operational and transactional improvement processes and capabilities at Messier-Dowty’s UK landing gear facility. £350m revenue.• Embedded enhanced Lean-Sigma training and improvement project management processes, both subsequently recognised as global benchmarks within the business.• Mentored 5 employees to Black Belt certification who subsequently mentored over 40 employees to Green Belt certification.• Achieved total annualised cost savings from improvement activities exceeding £5m during 2010. Show less
-
-
-
-
Operations Manager
-
2008 - 2009
Design and manufacture of access hardware solutions servicing diverse applications including automotive, aerospace and consumer electronics. Head of stand-alone manufacturing and distribution facility. 150 reporting employees. • Increased employee engagement in Lean activities through enhancement of the daily management system and continuous improvement project management process. • Established effective management information and review infrastructure in expense control, labour capacity planning, overall equipment effectiveness and on-time delivery. • Subsequent achievements included a 75% reduction in soft quality errors, a 20% increase in assembly direct labour productivity and a step change in the facility environment through 5S. Show less
-
-
-
Cooper Security Ltd
-
United Kingdom
-
Advertising Services
-
1 - 100 Employee
-
Operations Director
-
2006 - 2008
Design and manufacture of electronic intruder detection systems serving the domestic, commercial and industrial markets. 90 reporting employees. • Increased customer on-time delivery from 40% to 95% through multiple internal and supply base variance reduction actions. • Exceeded corporate operational cost reduction targets in 2006 and 2007 through the establishment of an effective Continuous Improvement team and enhanced processes for opportunity evaluation, resource allocation and project review. Show less
-
-
-
-
Business Projects Manager
-
2002 - 2006
Design and manufacture of diesel fuel injection systems.Member of corporate team re-aligning diesel capabilities across sites in Europe and the USA.• Developed and delivered the “Centre of Manufacturing Excellence” strategy to integrate and optimise the operational capabilities of Woodward’s UK and German sites within a combined two-site business unit.• Programme manager for the transfer of three fuel system production lines from customer sites in the USA to the UK, increasing annual revenues by 40%. All lines transferred and validated to plan with no disruption to service levels. Show less
-
-
Site & Operations Manager
-
1998 - 2002
Profit and loss responsibility for stand-alone business unit. 250 reporting employees.• Increased return on sales by 15% over 3 years on flat revenue through the on-going development of Lean Enterprise capabilities to drive operational excellence.• Transformed relationships with staff and shop-floor unions from adversarial to mutually supportive, facilitating a step change in employee motivation and engagement.
-
-
Education
-
The University of Reading
Bachelor of Science (B.Sc.), Mechanical Engineering
Community
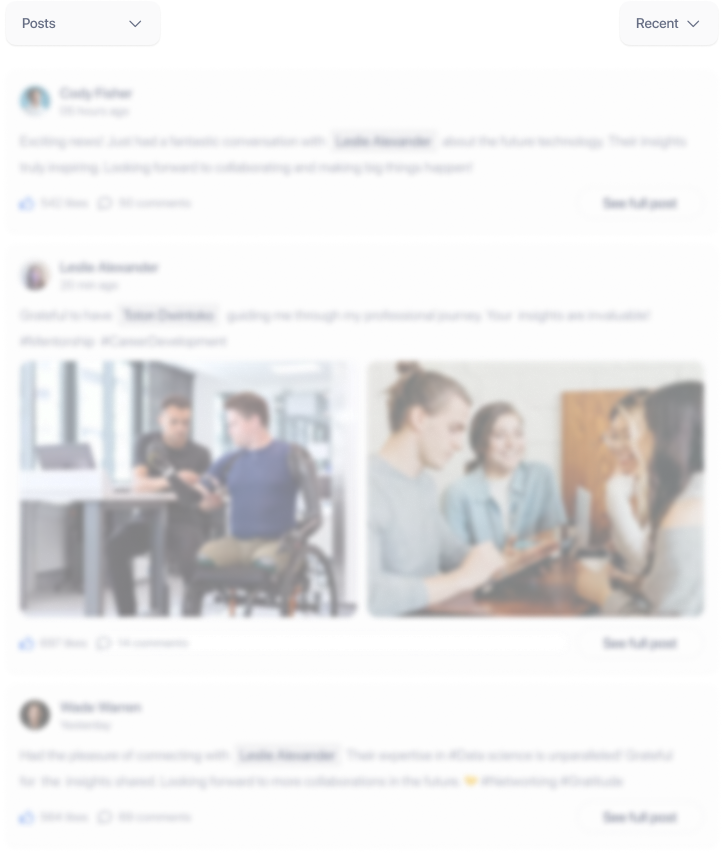