Andrew Dillon
Shift production technician at ALGAL OMEGA 3 LTD- Claim this Profile
Click to upgrade to our gold package
for the full feature experience.
Topline Score
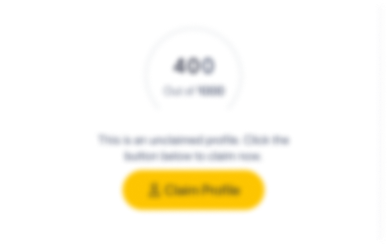
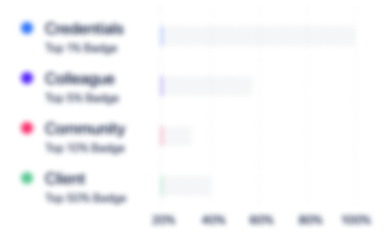
Bio


Experience
-
ALGAL OMEGA 3 LTD
-
Chemical Manufacturing
-
1 - 100 Employee
-
Shift production technician
-
Jan 2020 - Present
A Biotechnology company utilizing fermentation, sterilisation, centrifuges, dryers and packing technology in the production of oil products. Operating in the Nutraceutical, Nutritional, infant formula and animal feed sectors.Operation of the DCS system reviewing data for abnormal conditions, making alterations, inputting data and recommending improvements.To operate as a member of a shift team reporting to the Technical Development Manager.To cover all areas of the production process including Mash, Fermentation and DSP areas.Operation of the Production Process Plant in accordance with the Standard Operating Procedures and in compliance with the Site Environmental , Health and Safety Policies and Quality/Food Safety Procedures.To contribute to Plant and Process improvements, maintain a healthy and safe working environment and to maintain all areas to Good Manufacturing Practice. Laboratory testing of samples in accordance with Operating instructions, i.e. Titration of acid and Caustic, Glucose concentration, Near Infra Red scanning, Karl Fisher determination of moisture content. Also to undertake microbiological testing, i.e. Streak places and examination of fermentation samples using microscopy.To maintain food areas in compliance with the FSSC 2200 and Food Hygiene and Safety act.
-
-
-
-
Senior shift operator
-
Dec 2017 - Dec 2019
REnescience separates household waste into recyclables and turns bio liquid into methane gas to create green energy, running 4 CHP engines generating <6Mw of electricity, most of which is returned to the national grid. Enzymes, mechanical sorting, recycled water and anaerobic digestions are the focus of operations, which uses a fully sustainable pasteurisation, decanting and evaporating process.Responsible for all aspects of health, safety, environment, quality and processing of the waste to biogas facility. Provision of full planning support to the O&M manager, directing and managing operational performance. Leading the team to operate efficiently and compliantly to achieve business objectives and providing a 24-hr contact point for the site. Handover of workload for oncoming 12-hr shift, conducting daily safe start toolbox talks to ensure all staff appraised of safety issues, issuing permit to works, POWRA and isolations to assure a safe working environment. Interacting closely with shift operators to ensure operational effectiveness, maximise gas production and provide high-quality off-take products (RDF, SRF, ferrous and non-ferrous metals). Performing thorough fault-finding utilising TPM tool and techniques (WCM), recording on the SAP system and creating / delegating work instructions to engineering resource.
-
-
-
-
Siemens PCS7 Process Operator
-
Sep 2017 - Dec 2017
Collaborated closely with software engineers during the commissioning state, providing advice and guidance on the operational format. Operated the system following software updates / improvements and feedback of results to the projects management team during daily morning briefings. In conjunction with software engineers, investigated a continuous improvement programme to maximise the sorting hall process while maintaining safety as a priority. Collaborated closely with software engineers during the commissioning state, providing advice and guidance on the operational format. Operated the system following software updates / improvements and feedback of results to the projects management team during daily morning briefings. In conjunction with software engineers, investigated a continuous improvement programme to maximise the sorting hall process while maintaining safety as a priority.
-
-
-
-
Chemical Process Operator
-
Sep 2013 - Aug 2017
Responsible for the consistent achievement of high standards in respect of safety, housekeeping, quality and environmental issues, operating as a one-man team. Ensured all autonomous maintenance tasks were completed daily / weekly and recorded any repairs, safety issues or improvements via the tag database. Performed regular products testing and initiated process adjustments as necessary and undertook daily / weekly stock taking, inputting data via the SAP system. Communicated extensively with colleagues and other departments via completion of electronic log books, activity boards and comprehensive handovers. Maximised any downtime to conduct 5S, maintenance and improvement activities, proactively sharing knowledge and training to promote a culture of continual improvement. Led team decision-making and proactively influenced earlier maintenance activities or changeover to other products as appropriate.
-
-
-
Unilever
-
United Kingdom
-
Manufacturing
-
700 & Above Employee
-
Technical Operator
-
Sep 2008 - Sep 2013
Responsible for equipment operation, repair, continuous maintenance and improvement to support delivery of operational KPIs (Productivity, Quality, Safety, Health & Environment, Cost, Delivery, Morale, Innovation and Sustainability). Understood equipment mechanism and motion principles and conducted changeovers, basic repairs and adjustments (for example cams, slides, bearings, belts and pulleys) and utilised relevant lubrication regimes. Demonstrated an understanding of the principles and application of pneumatics / hydraulics in the sourcing unit and conducted fault-finding and basic repair. Monitored and evaluated equipment, machinery and components conditions, liaising with technicians to eliminate minor stops and sources of contamination. Conducted comprehensive and effective handovers to ensure objectives were achieved in full and on time.
-
-
Process plant operator
-
Sep 2004 - Sep 2008
Operate and maintain through autonomous maintenance a production plant ensuring minimum downtime. Fully utilizing TPM tools and techniques to maximize the effectiveness of all production equipment.During the early equipment management project I was heavily involved in the commissioning of the gel plant.Drove the TPM program within the gel team and ensured KPI targets were met on time in full.
-
-
Shift team leader
-
Sep 1996 - Sep 2004
Delivery of the required production plan with primary regard to safety, time, cost & quality. Actively promote HS&E activities and carried out Du Pont audits. Used Quality and Environmental Management Systems (ISO9001 & 14001) on a daily basis. Effectively run productive and maintenance shifts on regularly changing shift patterns whilst fulfilling site and personal objectives. Ensuring the personal development of all operators to ensure the skills gaps were identified and training allocated were required. Managed the PDR and PDP process annually to identify any skills gaps within the team and implement the relevant training.
-
-
-
Bristol-Myers Squibb
-
United States
-
Pharmaceutical Manufacturing
-
1 - 100 Employee
-
Chemical operator
-
Sep 1988 - Sep 1996
Worked in the manufacturing unit of pharmaceuticals as a Chemical process operator. Worked to the highest quality standards and guidelines (GMP), as set by regulatory bodies including the FDA. Used various methods of process such as blending, granulation, milling and filtration using exact measurements and within a clean room environment. Strict guidelines followed to ensure risk assessments were in place and safety concerns evaluated. Worked in the manufacturing unit of pharmaceuticals as a Chemical process operator. Worked to the highest quality standards and guidelines (GMP), as set by regulatory bodies including the FDA. Used various methods of process such as blending, granulation, milling and filtration using exact measurements and within a clean room environment. Strict guidelines followed to ensure risk assessments were in place and safety concerns evaluated.
-
-
Education
-
Ellesmere Port Catholic High
8 X O levels, C's and above -
Wirral metropolitan college
City and Guilds microcomputer technology, Computer Software Engineering
Community
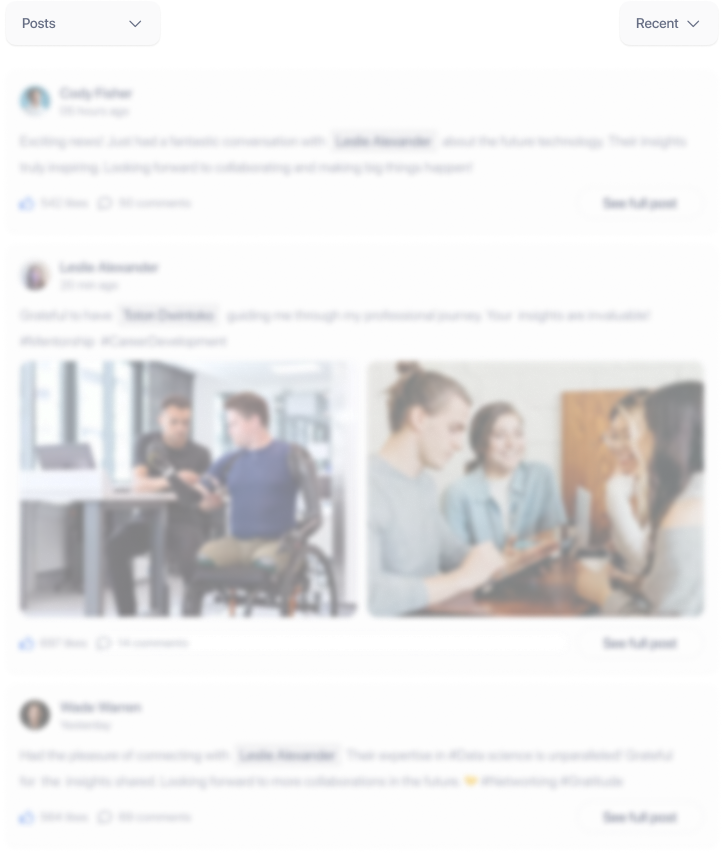