Andrew Nelson
Purchasing Manager at Austofix- Claim this Profile
Click to upgrade to our gold package
for the full feature experience.
Topline Score
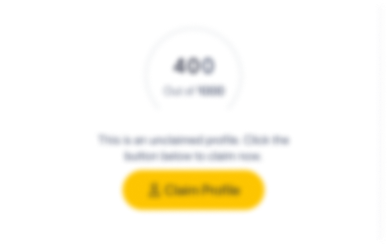
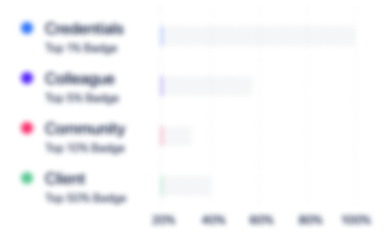
Bio

Darren Bishop
DIFOT Specialist to boot 👍

André Dolphin
Andrew has a strong leadership qualities, many years of experience in the Purchasing and Logistics (Domestically & Internationally) fields, working with large organisations to achieve there outcomes

Darren Bishop
DIFOT Specialist to boot 👍

André Dolphin
Andrew has a strong leadership qualities, many years of experience in the Purchasing and Logistics (Domestically & Internationally) fields, working with large organisations to achieve there outcomes

Darren Bishop
DIFOT Specialist to boot 👍

André Dolphin
Andrew has a strong leadership qualities, many years of experience in the Purchasing and Logistics (Domestically & Internationally) fields, working with large organisations to achieve there outcomes

Darren Bishop
DIFOT Specialist to boot 👍

André Dolphin
Andrew has a strong leadership qualities, many years of experience in the Purchasing and Logistics (Domestically & Internationally) fields, working with large organisations to achieve there outcomes

Experience
-
Austofix
-
Australia
-
Medical Equipment Manufacturing
-
1 - 100 Employee
-
Purchasing Manager
-
May 2022 - Present
Leading and managing purchasing and inventory functions. Developing and maintaining supplier partnerships with local and international suppliers. Conducting evaluations, lead supplier selection, review and management of processes. Leading and managing purchasing and inventory functions. Developing and maintaining supplier partnerships with local and international suppliers. Conducting evaluations, lead supplier selection, review and management of processes.
-
-
-
RPC Pipe Systems Pty Ltd
-
Australia
-
Plastics Manufacturing
-
1 - 100 Employee
-
Purchasing & Logistics Coordinator
-
May 2013 - May 2022
Overseeing purchasing for manufacturing and indirect / adhock procurement. Coordinator for logistics and exporting finished goods. Coordinating Stores/ goods inwards and raw materials including Dangerous Goods. Overseeing purchasing for manufacturing and indirect / adhock procurement. Coordinator for logistics and exporting finished goods. Coordinating Stores/ goods inwards and raw materials including Dangerous Goods.
-
-
-
-
Purchasing Supervisor
-
Oct 2009 - Mar 2013
My role as Purchasing Supervisor in the MSP Group required I manage 5 product groups of locally and imported goods to cater to the building industries sometimes-aggressive demand with a keen eye on inventory levels and safety stocks. This meant having a good relationship with my suppliers and the customer service department responsible for requesting the supervisor’s demands. I was also responsible for administering and enforcing the best purchasing protocol as the teams Supervisor and implementing practices / procedures to make improvements. Key Achievements Improved customer service levels and implemented inventory level reduction projects, during the busiest season of the year (2010/2011) Increase Delivered In Full On Time (DIFOT) to the highest quarterly levels in the company’s history 99.8% Assist implement major purchasing ordering / planning function software. Reduced inventory levels for slow moving and obsolete stock, by over $150K.
-
-
-
Seeley International Pty Ltd
-
Australia
-
Industrial Machinery Manufacturing
-
100 - 200 Employee
-
Purchasing / Procurement
-
Jan 1999 - Oct 2009
I joined the Purchasing and Procurement department in 2004 where I managed over 60 suppliers directly linked to production assembly and 6 indirect such as Material Handling/ Cleaning Contract and Waste Management for our two manufacturing sites in SA. Other tasks included / projects include “Cost down initiatives”, price negotiations, RFQ’s (Request For Quote). Gathering / Analysing data, preparing Tenders and reports Key Achievements Assisted development and implemented RFQ templates and standard Supplier Agreement Terms and Conditions for all market reviews. Reduction in inventory 2006-2009, KPI’s set by Purchasing Manager to reduce inventory to a JIT system where all locally sourced production assembly parts were only held for a week before consumption. Cost Savings 2006-2009, targets set to reduce cost for production related parts and indirect related accounts. Cost savings ranged from Personal Protective Equipment (PPE) of 15k / Material Handing fleet 30k through to electronic components of 60k PA Supplier Quality improvement 2006-2009, liaised QA feedback for suppliers not delivering components to specification. Monitored and logged results in database. Set KPI’s for suppliers. Kaizen / Lean Project 2008, assist research then implementation of a completely paper free electronic Vendor Schedule system. The test pilot for the IT departments’ involvement in implementation and roll out of the new system. Feedback and supplier involvement critical. Electronic Vendor Schedule saving 1.5hrs per Buyer totalling 4.5hrs per week. Paper and print doc centres cost savings also noted. Kaizen / Lean Project 2009, heavily researched and implemented a automated system to reduce repetitive tasks in the Purchasing function of running daily reports for 2 Buyers and the Purchasing Procurement Supervisor. A total saving of 5hrs per week of keystrokes.
-
-
Education
-
Kaizen – Lean Leadership Master Class 2016
-
Enhanced Training Services
Cert IV in Frontline Management BSB40807 -
Apics (The Australasian Production & Inventory Control Society)
Fundamentals of Purchasing and Contract Management, Purchasing, Procurement/Acquisitions and Contracts Management -
Electus
Infuencing & Negotiation (E1528-PLA) -
Major Training Services
Cert IV in Business Purchasing (BSB41404), Purchasing, Procurement/Acquisitions and Contracts Management -
Electus
Excel 2003 Intermediate (E356) -
Electus
Excel 2003 Introduction (E355) -
TAFE SA
Cert in Engineering Production Level 2, Engineering Mechanics -
TAFE SA
Prep education course, Professional, Technical, Business, and Scientific Writing -
Morphett Vale High School
Community
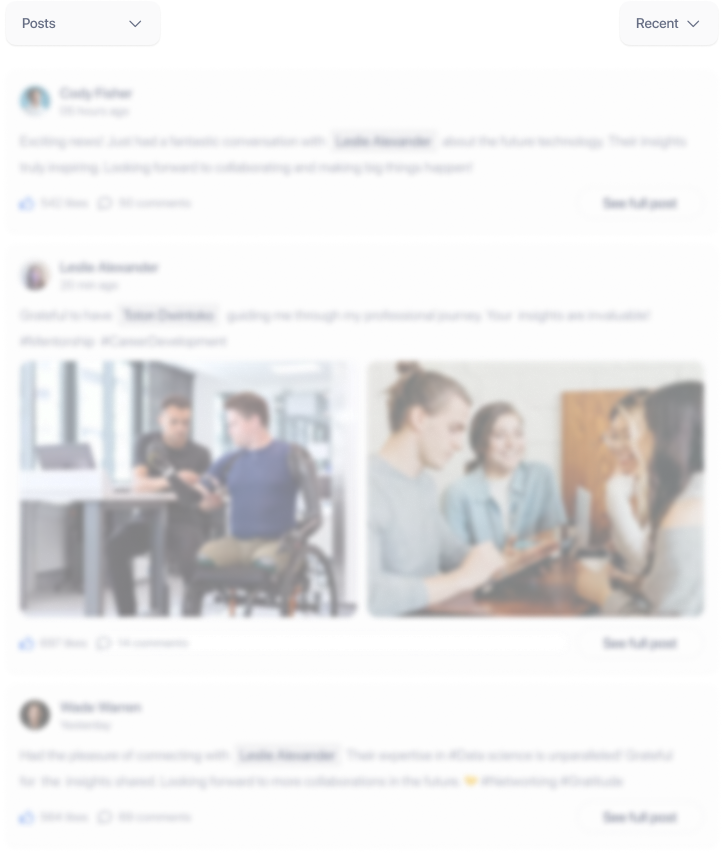