Andrew Manion
Project Engineer at Intier Automotive- Claim this Profile
Click to upgrade to our gold package
for the full feature experience.
Topline Score
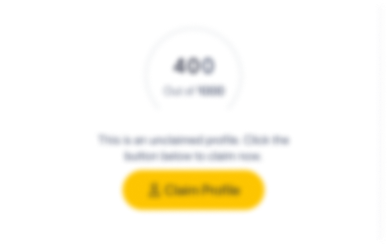
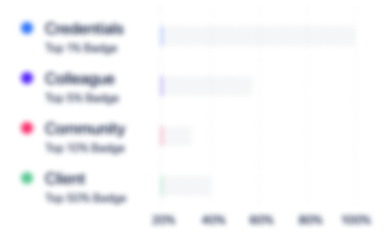
Bio


Experience
-
Intier Automotive
-
Motor Vehicle Manufacturing
-
1 - 100 Employee
-
Project Engineer
-
2009 - Present
• As Project Engineer for current engineering I am responsible for solving issues raised during the assembly of the 'BMW Mini' cockpit, console and doors• Some issues have been around since SOP and are difficult to solve, others are more immediate and require urgent actions and solutions.• Working with all departments from CAD, Tooling, Production and Quality I present solutions to all parties including the customer before managing the change into production.• I am also running an adhesive change program due to EU Legislation.
-
-
-
CABAUTO
-
United Kingdom
-
Motor Vehicle Manufacturing
-
1 - 100 Employee
-
Project Engineer
-
2012 - 2014
-
-
Project Engineer
-
2012 - 2014
-
-
-
-
Project Manager
-
Apr 2007 - Dec 2009
• Project Leader for various interior trim projects including L322 Leather Doors and L359 Door Inserts• All aspects of Project Management and Engineering to internal Project Team and externally to Customer.• Controlling product development, prototyping, DV/PV Testing, production machine specification and production methods.• Required to produce and control timing plans, APQP, Launch Readiness (LRR), PFMEA, Process Flows, Work Instructions, BOM and costs.• Provided input into CRT, Standards Book and customer DFMEA and Feasibility• Manufacturing processes were varied due to complex nature and skill level of leather trimming but include adhesive spraying, manual machines for trim aids and bladder laminating processes
-
-
-
-
Product Engineer
-
Jul 2006 - Mar 2007
Product Engineer for X250 Jaguar Armrests and Top Rolls• Responsible for eight components including injection moulded substrate, PUR cushion and leather wrapping.• Engineering change, BOM and build requirements including material procurement and logistics. Rapid tooling and component investigations and procurement. Running open issues lists with customer and internal manufacturing feasibility studies. Manufacturing processes include adhesives spraying, seam alignment and edge wrapping. CRT creation and documentation using Catia v5 (basic level). Gauge design and procurement.
-
-
-
-
Product Engineer
-
Jan 2004 - Jul 2006
Cockpit Product Engineer on L359 Landrover Freelander II Design responsible for over fifteen components Main components include glove box, driver side lower, column cowl and IMF trim finishers Represented C&A at customer focused Clay Reviews, Optical Quality and Design Reviews Participated in some and chaired other internal Design, DFMEA, Crash/CAE, DVP&R, DVA and feasibility reviews Utilised internal CAD resource and experience where possible and external expertise when required Processes include In Mould Foil (IMF), vibration welding, injection moulding and metal pressings
-
-
-
-
Project Engineer
-
Jul 2001 - Jan 2004
Console Project Engineer for R52 BMW Mini facelift Project managed seven new injection mould tools Chaired design/feasibility reviews at Magna in Germany who were design responsible Reported condition of project to Intier management through Intier ‘PDP’ Gateway System Liaised with quality, production and logistics departments to achieve build deadlines Console was delivered on time and within budget Also involved in cockpit D/PFMEA and prototype build. Processes involved injection moulding, chrome finishing, sand casting (prototype CCB), thermo forming and rapid prototyping using SLA and SLS technology
-
-
-
-
CMS Engineer
-
Jun 1999 - Jul 2001
The Commodity Management Supply (CMS) concept was driven by Ford to reduce the amount of suppliers into the Ford Motor Company by single sourcing commodities. As a power tool Engineer I worked with customer engineers/analysts/buyers to analyse the Ford inventory and monitor the purchasing process Tasked with cost savings against the annual spend on the power tool commodity Represented Atlas Copco in the role of Commodity Manager at all Ford plants within the UK Attended courses regarding assembly-tightening techniques and theories at Atlas Copco in Sweden and in Belgium
-
-
Education
-
University of Wolverhampton
2:1, Product Engineering
Community
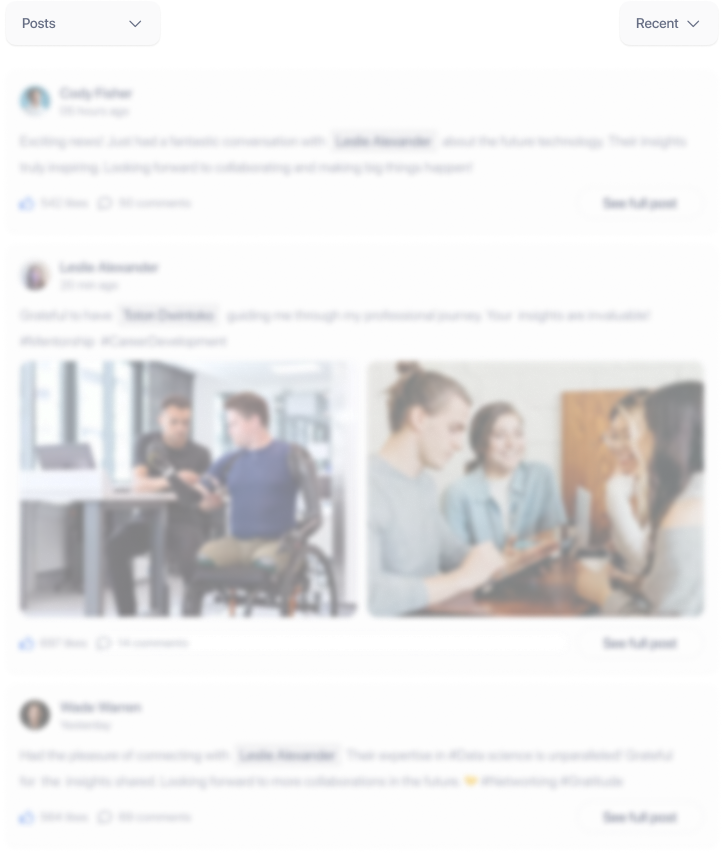