Andrew Hunter
Operational Buyer at Quintessential Brands Group- Claim this Profile
Click to upgrade to our gold package
for the full feature experience.
Topline Score
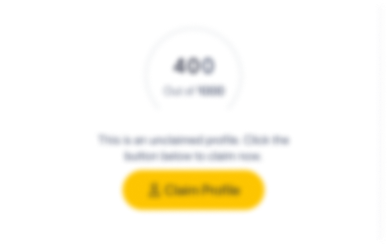
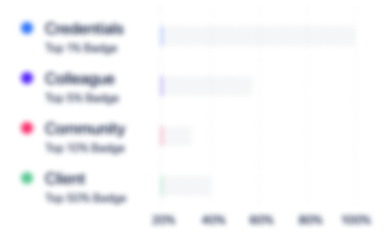
Bio


Credentials
-
5S Workplace Productivity
LinkedInJan, 2021- Sep, 2024 -
TPM Fundamentals - Deployments (Self Paced)
CrossKnowledgeJan, 2021- Sep, 2024
Experience
-
Quintessential Brands Group
-
United Kingdom
-
Wine & Spirits
-
1 - 100 Employee
-
Operational Buyer
-
Dec 2021 - Present
Reporting into the head of procurement, I am responsible for purchasing and managing all flavours and bulk liquid onto site. I am also responsible for liaising and managing our co-packing teams around the country in terms of orders and production, in line with our New Product Development team. I will also provide data analytics to help improve efficiency and important information on production and process throughout the team. Reporting into the head of procurement, I am responsible for purchasing and managing all flavours and bulk liquid onto site. I am also responsible for liaising and managing our co-packing teams around the country in terms of orders and production, in line with our New Product Development team. I will also provide data analytics to help improve efficiency and important information on production and process throughout the team.
-
-
-
Syngenta
-
Switzerland
-
Farming
-
700 & Above Employee
-
Asset Planner
-
Jun 2021 - Dec 2021
Reporting into the Tolling Manager, my role is to create and maintain the overall Formulation, Fill & Pack (FF&P) production plan across a group of Tollers (3rd party manufacturing), providing options to meet variances in demand and supply. I order in SAP on Toller location and schedule and order all required components provided by Syngenta to Toller locations to meet production plan. I am also in charge of the co-ordination along the supply chain to manage the production plan and ex-works shipments over a zero to end current season horizon. Show less
-
-
-
The HEINEKEN Company
-
Netherlands
-
Food and Beverage Services
-
700 & Above Employee
-
Site Scheduling Manager
-
Oct 2017 - Mar 2021
Reporting into the Site Logistics Manager, I am responsible and accountable for the delivery and execution of a beer production plan each week. Working closely with our mid to long term planning team in Edinburgh I will steer and streamline the sites production planning on a short-term basis. I am responsible for the ordering, delivering and organising of our raw materials. I am responsible for the management of our tanking production to external customer and other Heineken breweries. • Plan many areas aspects of beer production through an advance planning tool (A.S.) which includes raw materials, centrifuge beer transfer, filtration, packaging, tanker loading and offloading. • Creating and managing a packaging conformance database and report on a daily basis.• Part of the team the planned the newly accredited Heineken beer production on site.• Working closely with the brewing department in order to meet required production plans.• Introducing a new tanker planning process for the site in order to compensate for the increased tanking requirement for site.• Create standard operational guides and processes. Show less
-
-
Data Analyst
-
Apr 2016 - Oct 2017
• Maintain a bespoke suite of databases called HOPS for the brewery. Control and develop requests for HOPS to help overall brewery processes.• Enter and validate raw data for all elements of site performance for Heineken in a global system called BCS.• Query a large collection of data in the sites SQL server to manipulate information and produce bespoke reports.• Liaise daily with key stakeholders with key information.• Create new reference tables to integrate a SKU performance document and report for site. This has provided accurate run rates for the brewery so that logistics can plan better.• Created a daily control system for logistics and KNDL.• Created a packaging quality inspection database for the brewery to monitor regularly whether there is any damage to stock before it leaves site.• Integrated all staff on site onto our time and attendance database so the site can accurately monitor sickness, holidays and overall attendance• Reconfigure the entire data capture system for Heineken Manchester to fall in line with Heineken standards. Show less
-
-
-
The Christie NHS Foundation Trust
-
United Kingdom
-
Hospitals and Health Care
-
700 & Above Employee
-
Workforce Data Analyst
-
Apr 2014 - Apr 2016
• Produce monthly divisional board reports with the use of ESR and Microsoft Excel • Amending pre-existing Business Intelligence reporting templates to suit the desires of managers within the Christie. • FOI (Freedom of Information) requests on information about The Christie from external sources, such as the Manchester Evening news and National Newspapers. • Assisted in the creation and responsible for ongoing maintenance of a HR People Dashboard covering all movements within the business. • Responsible for a data cleanse and people hub projects to refine and ‘fix’ data anomalies. • Introduced Business Intelligence as a modern reporting platform to replace ESR, using workshops and training session to show how managers and HR staff can access reporting from their own areas to check all manor report requests. • Used the Business Intelligence training course to design reports from scratch to meet the business needs with the use of basic tables, pivot tables, graphs and dashboards. Show less
-
-
Education
-
The Manchester Metropolitan University
BA Honours, English Language and Literature/Letters
Community
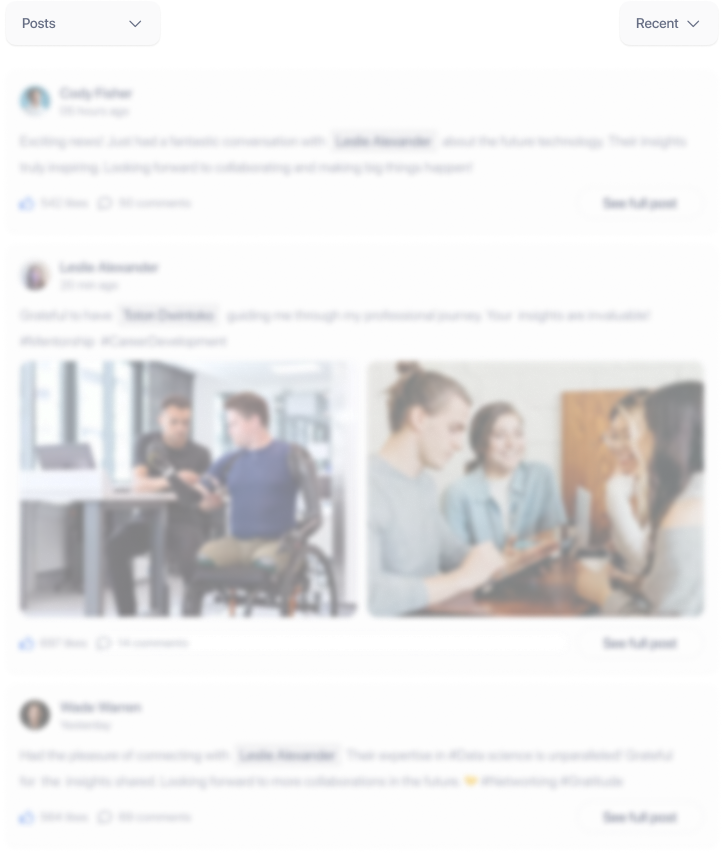