
Andrew Gardner
Manufacturing Manager at Manor Concepts Limited- Claim this Profile
Click to upgrade to our gold package
for the full feature experience.
Topline Score
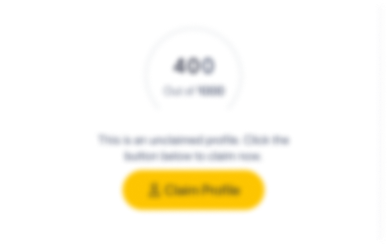
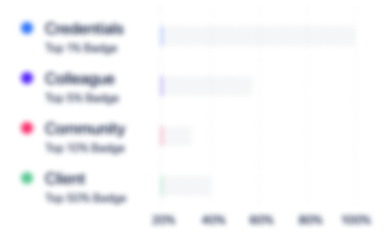
Bio


Experience
-
Manor Concepts Limited
-
United Kingdom
-
Machinery Manufacturing
-
1 - 100 Employee
-
Manufacturing Manager
-
Aug 2021 - Present
-
-
-
Fletcher European Containers Ltd
-
United Kingdom
-
Plastics Manufacturing
-
1 - 100 Employee
-
Factory Manager
-
Jan 2021 - Mar 2021
Managing all Factory and Purchasing Functions• Reviewed all mould tooling and jigs and implemented a plan for refurbishment.• Implemented a ‘What does good look like’ scheme for the facility. Managing all Factory and Purchasing Functions• Reviewed all mould tooling and jigs and implemented a plan for refurbishment.• Implemented a ‘What does good look like’ scheme for the facility.
-
-
-
Oxford Technical Solutions
-
United Kingdom
-
Appliances, Electrical, and Electronics Manufacturing
-
1 - 100 Employee
-
Operations Manager
-
Jan 2020 - Dec 2020
Managing all Operations and Facilities functions• Reducing materials stock holding by £1.4m without affecting OTIF.• Reviewing the Operations teams functions and making appropriate changes to get the best out of the team.• Put in place equipment maintenance system for preventive maintenance and root cause analyses.• Working with Lean principles made modifications to the production facility to get the best out of the available building.• Employ live data dashboards to manage all aspects of the operations side of the business.
-
-
-
-
Independent Process Improvement Consultant
-
Apr 2018 - Jan 2020
Undertaking short term contacts to supporting SME manufacturing companies to troubleshoot, reduce waste and maximise efficiencies.• Provided systemic and comprehensive consulting services that took clients through the process of Value Stream Mapping of their processes to show them a path and journey required to become more efficient.• Assisted clients in developing a culture of Lean Thinking, continuous improvement, problem solving, by training leading to improved productivity and efficiency.• Assessing processes in place in place to implement changes to reduce waste and improve quality, assess people’s skills and implementing training programs.• Implement a plan to overhaul the sites equipment, identify and justify new or alternative equipment.• Increase site efficiencies by identifying root cause and implementing improvement plans.
-
-
-
SupplyPoint
-
United States
-
Manufacturing
-
1 - 100 Employee
-
Global Operations Manager
-
Jul 2014 - Apr 2018
Managing all Operational and Facilities Functions• Introduced Lean techniques, Automation and Design for Manufacturing to increase production capacity and deliver sustainable cost savings.o cut ongoing materials costs by £300K.o cut inventory and work in progress by 19%.o cut manufacturing lead time by 25% without increasing stock values.o increased on time delivery performance of goods from the factory by 33%.o increased on time delivery performance of raw materials to the factory by 34%.• Recommended £1.5m strategic acquisitions of key sheet metal suppliers to secure lower cost capacity, prepared business case, won Board approval, executed acquisition in short timeframe and under budget, integrated into the business, delivered cost savings of £200K annually and cut lead times by three weeks.• Led and mentored a team of 70 (50 in the UK, 20 in the USA) through global introduction of Best Practices, process change, standardisation of systems, practices, procedures and reporting packs.• Consolidated six UK manufacturing facilities into one, on time and to budget.• Specified functional requirements for and implemented a new custom-built ERP system for the manufacturing facilities, automated the legacy paper data display and replaced with a live feed from ERP system.• Drove introduction of KPI scorecards throughout operations and manufacturing, enabling staff as well as management to monitor progress, and through sales function, to report on units sold.• Initiated and led monthly facilities meetings to share information on business progress with the staff and to get feedback and ideas, introduced daily stand-up meetings for production and service teams.
-
-
-
KEMET Electronics Corporation
-
United States
-
Appliances, Electrical, and Electronics Manufacturing
-
700 & Above Employee
-
Operations Manager
-
Jun 2008 - Jul 2014
Managing Divisions Operational Functions• Relocated UK manufacturing facility to Macedonia with minimal interruption to business continuity, completed on time and to budget• Recruited and developed new teams of unskilled, non-English speaking Macedonian staff, taught new manufacturing skills and trained to ISO 9001• Upgraded two manufacturing sites using value stream mapping to improve production planning and processes• Continuously cut costs by re-negotiating contracts with suppliers
-
-
-
-
MANUFACTURING MANAGER
-
Jan 2007 - Jun 2008
Managing Factories Operational Functions• Managed four production lines with a 50-strong staff• Established new facilities to produce new product ranges• Managed offshore sub-contractors in China • Prepared business case for re-location of manufacturing facilities• Oversaw the closure of existing UK manufacturing site including staffing arrangements
-
-
ASSISTANT MANUFACTURING MANAGER
-
Feb 2005 - Jan 2007
Arcotronics Ltd (Part of the KEMET Group), Towcester• Controlled and improved all manufacturing processes and procedures to improve and maintain on-time delivery• Led all Health and Safety and Quality Assurance issues, from Audits and Compliance to internal training and investigations
-
-
-
Custom Design Technologies (CDT)
-
United Kingdom
-
Appliances, Electrical, and Electronics Manufacturing
-
1 - 100 Employee
-
Project Engineer
-
Jan 2003 - Feb 2005
Managing Projects Turning Customer Requirements into Product• Recommended technical design improvements to the product and process improvements for manufacturing• Gathered customer requirements, translated into working specifications, managed project lifecycle from contract through production Managing Projects Turning Customer Requirements into Product• Recommended technical design improvements to the product and process improvements for manufacturing• Gathered customer requirements, translated into working specifications, managed project lifecycle from contract through production
-
-
Education
-
De Montfort University
Community
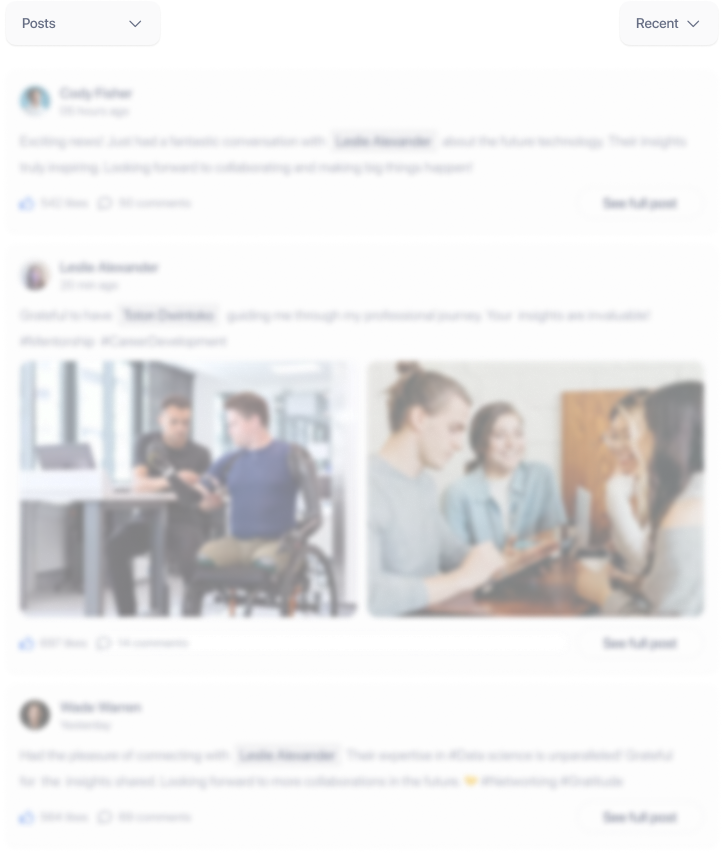