Andres Blanco Siller
Quality Manager at Criotec, S.A. de C.V.- Claim this Profile
Click to upgrade to our gold package
for the full feature experience.
Topline Score
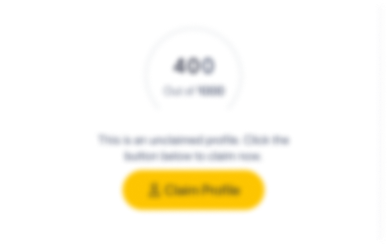
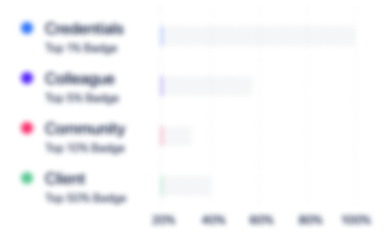
Bio

Alberto Diaz Argüello
Andres has a strong leadership and a very charismatic personality. He is clever, determined, collaborative, multi-task and always focused on results. Willing to help at any level by means of sharing his knowledge. Commonly member of committees with worthy assistance. A proven background. He is highly recommended for any venture or opportunity.

Alberto Diaz Argüello
Andres has a strong leadership and a very charismatic personality. He is clever, determined, collaborative, multi-task and always focused on results. Willing to help at any level by means of sharing his knowledge. Commonly member of committees with worthy assistance. A proven background. He is highly recommended for any venture or opportunity.

Alberto Diaz Argüello
Andres has a strong leadership and a very charismatic personality. He is clever, determined, collaborative, multi-task and always focused on results. Willing to help at any level by means of sharing his knowledge. Commonly member of committees with worthy assistance. A proven background. He is highly recommended for any venture or opportunity.

Alberto Diaz Argüello
Andres has a strong leadership and a very charismatic personality. He is clever, determined, collaborative, multi-task and always focused on results. Willing to help at any level by means of sharing his knowledge. Commonly member of committees with worthy assistance. A proven background. He is highly recommended for any venture or opportunity.

Experience
-
Criotec, S.A. de C.V.
-
Manufacturing
-
1 - 100 Employee
-
Quality Manager
-
Mar 2013 - Present
• Assure Plant's adequacy to the Quality Management System (ISO 9001) and to other International and National Standards such as ISO17025, UL, NOM, and Customer Certifications (ex. Coca-Cola & PepsiCo). • Assure proper Risk and Opportunity Evaluation for every process on the QMS and Laboratory QMS (PFMEAs, DFMEAs, SWOT, Conflict of Interest and Business Continuity Strategy). • Coordinate Business Continuity Management System based on ISO22301. • Develop a Quality Strategy that meets Plant's and Customer needs. • Set Quality Standards and KPIs that will assure quality and continuous improvement for the operation. • Corrective Action Management – Internal, Customer/Field & Supplier, • Supplier Quality – PPAP, Supplier Corrective Actions, Supplier Evaluation/Certification, and Supplier visits. • Metrology- Part Approval, Parts Measurement, Equipment Calibration, Measurement Adequacy Studies, Equipment purchase. • Process Quality (Commercial Coolers and Freezers- Sheet-metal, Plastics, Brazing, Welding, Assembly & Functional/Performance Testing) measuring Criotec Total Quality, Scrap, Cost per Unit, MRB, Deviation(product, process & system),Cost of Poor Quality, Customer PPM (ICQ + Tot Wty) Process PPM, & FPY • Incoming Inspection- Part sampling, measurement, defect containment/sorting/reprocess • Quality Customer Claims- Customer Quality Relations (Field/Customer Visits) Complaint & Warranty Analysis and Product improvement. • Continuous Improvement Projects. • Technical Service- assure proper technical service is provided to the customer, due-diligence on claim investigation, determine root cause and corrective actions to eliminate customer complaint, coordinate technicians to provide service. • Spare parts- coordinate spare part (for warranty and selling) request, warehousing, shipping, setting inventory quantities (according to demand and new technologies) and setting goals to align to company’s budget objective. Show less
-
-
-
Ingersoll Rand
-
United States
-
Industrial Machinery Manufacturing
-
700 & Above Employee
-
Quality Manager
-
Feb 2012 - Feb 2013
Process & Quality Manager, Trane Ingersoll Rand, Compressor & HVAC Plants Monterrey, Feb 2012 to Feb 2013•Assure adequacy of the Plant’s Quality Management System (ISO 9001)•Align with Corporate Quality Guidelines meeting both Sector requirements for Residential and Commercial Divisions Developing a Quality Strategy that meets both as well as the Manufacturing Plant’s particular needs.•Customer Quality Relations•Corrective Action Management – Internal, Customer/Field & Supplier, •Supplier Quality – PPAP, Supplier Corrective Actions, Supplier Certification•Metrology- CMMs, Parts Measurement, Equipment Calibration. •Process & Quality (HVAC, Reciprocating Compressors, Scroll Compressors, Screw Compressors, Assembly, Welding, Brazing, Powder Paint & Coil-shop)•Incoming Inspection- Part sampling, measurement, defect containment/sorting•Quality Indicator Control : Scrap, Cost per Unit, Internal & External PPM / DPU, FPY & COPQ•Quality at the Source Implementation •Complaint & Warranty Analysis•Productivity Projects Show less
-
-
Process Quality Leader Odyssey Split Systems Plant Monterrey
-
Mar 2010 - Feb 2012
•Split Systems (Air Handlers, Condensing Units/Heat Pumps and Electric Heaters) and Support Areas (Coil-shop, Brazing and Sheet metal) Process Implementation and Coordination. •XM Condenser Product “Relaunch” (Residential application with micro-channel coil) Improved DPU performance from 0.346 to 0.02%improvment from baseline•Process Control and Improvement (Standard Work, Method Sheets, FMEAs, Control Plans, Pokayoke development for process CFs, Scrap Reduction, Material Handling Improvement, Line balancing, Quality at the Source, Process Checklists, Operator Certification, Takt attainment, Engineering Changes, VSM, Kaizen Events, VAVEs, etc ) Led to 50% Failure rate Improvement, Internal DPUs from 0.745 to 0.0616 on 2011YTD•Process Quality Indicators Control and Improvement (DPUs, Downtime, Scrap, Operator Certification, Corrective Actions, Daily Process and Quality Action Item follow up) 53% Scrap Reduction from Operations Startup•Quality Escape, Customer Complaint & Warranty Management Reduced from Baseline $163 USD Warranty Cost per unit to $29.6 USD 2011 YTD•Supplier Corrective Action Requests Execution •Supplier On Site Assessments /FAIs/Trial Runs/New product sign off Show less
-
-
Supplier Quality Engineer
-
Sep 2009 - Mar 2010
•Supplier Quality Support (Reciprocating & Screw Compressors and Wire Harness) •Supplier Corrective Action Requests Execution (initiate, follow up and closure)•Supplier On Site Assessments; Supplier Performance Management.•PPAP administration•New Component/Process introduction Execution (Define Quality Plan, Trial runs, lead to closure and approval) Support on change management for purchased components.•Quality Transfer Engineer for Heaters, Condenser and Airhandler lines start up (Quality Plan, Op. Certification, Quality checklists, Control Plans, Supplier Quality, etc) Show less
-
-
-
-
Quality Supervisor
-
Nov 2003 - Aug 2009
Quality Function on Reciprocating, Scroll & Screw Compressors. •Screw compressor line Quality Transfer, Start up Quality Plan, Checks & Audits, R410A Light Commercial and Commercial Line Start up Quality Plan, Checks & Audits. •Production Area Scrap Reduction-50% Waste reduction on assy, machining and welding areas . •Scroll Rotor Reclaim- Cost avoidance process to reclaim rejected compressor’s rotors. •Piston Machining Process Certification in 6 Sigma- Piston Machining Certification on Six Sigma •Redefinition of Compressor line Process Checks for Reciprocating an Scroll Areas (Machining, Solder, Assembly, Chemical, Paint, Final Test & Packout Areas) •Improvement Teams Movement Coordinator -23 teams - •Reaction Plan design & Implementation on Manufacturing Processes •PPAP administration per suppliers •Green Belt Project: 100% Reduction per Client Noise complaints by Tube Misalignment. •Green Belt Project: 30% Reduction per compressor valve discharge leaks •Applying Lean Mfg Tools (Value Stream Mapping, 5S, Pokayoke, etc.) & Industrial Engineering •Green Belt Project Coaching (Champion) •Process Quality Indicators Administration/Monitoring (Process & Product Quality Audits, PPMs, RTY, 5Ss, etc.). •Corrective/Preventive Action Follow up - Client Reciprocating PPM reduction from 781 to 286, Client Scroll PPM reduction from 910 to 462 YTD , Scrap reduction project on Set Up Parts, Process Scrap Reduction •Supplier weekly quality performance reviews, Quality Agreements, Audits, etc.. •ISO 9001:2000 Implementation - Member of the Core team to implement ISO System working the Quality Manual definition, process, formats and system documentation Training Instructor :•ISO 9001:2000 Internal Auditor •New Component / Process Introduction •Operator Certification -180 Certified Operators •OHSAS 18001 Certification Core Team - Member of the Safety Management Team & Internal Auditor •EHS Audits- •Develop/Implement Control Plans, R&R, Cap. Studies, FMEA Show less
-
-
-
Philips
-
Netherlands
-
Hospitals and Health Care
-
700 & Above Employee
-
Continuos Improvement
-
Aug 2003 - Nov 2003
•Green Belt Project Coaching - •6 Sigma Project Admin. for Business Unit. •Green Belt Project: 25% reduction of destructive tests. - per definition of power sample •5S/Ergonimics evaluations - Ergo evals Resulted on Seat and position change per TL-U line • TLU Line Process Flow and Layout redefinition, Glass Tube feeding machine implementation •New Component / Process Introduction •ISO 9001:2000 Internal Auditor •Maintaining IS0 9001/14000 in the Business Unit •System administration per Process (PPM & DPMO) and Product performance Show less
-
-
-
-
Quality Engineer Normal Incandescent Lamps
-
Jul 2001 - Aug 2003
•System administration per Process (PPM & DPMO) and Product performance.- Implementation of Electronic PPM Monitor System •Consumer Complaint/Rejection Management, Analysis and Disposition •Develop/Implement Control Plans, R&R, Cap. Studies, FMEA- Definition and Implementation of Out of Control Action Plans for Normal incandescent process •Redefinition of line Process Checks, life tests, process control. •Quality Team Champion for Business Unit-34 Quality Teams formed •Green Belt Projects: PPM Measurement System Reinforcement, 15% Life improvement on Incandescent Lamps, 50% Al Base Scrap Reduction • ISO 9001:2000 Implementation- Member of the Core team update the ISO System from ISO9001:1994 to ISO9001:2000 Working on the redefinition of process, formats as well as system documentation. •Maintaining IS0 9001/14000 in the Business Unit- Internal instructor for ISO 9001, Corrective Actions Show less
-
-
-
Philips
-
Netherlands
-
Hospitals and Health Care
-
700 & Above Employee
-
Supplier Quality Engineer
-
Jun 1999 - Jul 2001
•Incoming Inspection •Zero Defect Sampling Implementation on Raw Material Incoming Inspection. •Supplier Audit, Development and Certification.- 15 Supplier Certifications, 56 Supplier Evaluations and follow up •Supplier Performance Evaluations, Cost Control, Reject Control, Quality Agreements (MRNs, RMAs, Credit Notes, etc.) •20 % Material Reject Reduction on Raw Material- Handled Supplier Corrective Actions and Follow Up (Al Base Crack 80% defect reduction, Carton legend miss-print 100% reduction, Lead wire poor welding 100% reduction, Brittle coils 40% reduction) Show less
-
-
Education
-
Universidad de Monterrey
MBA -
Universidad de Monterrey
Industrial & Systems Engineer
Community
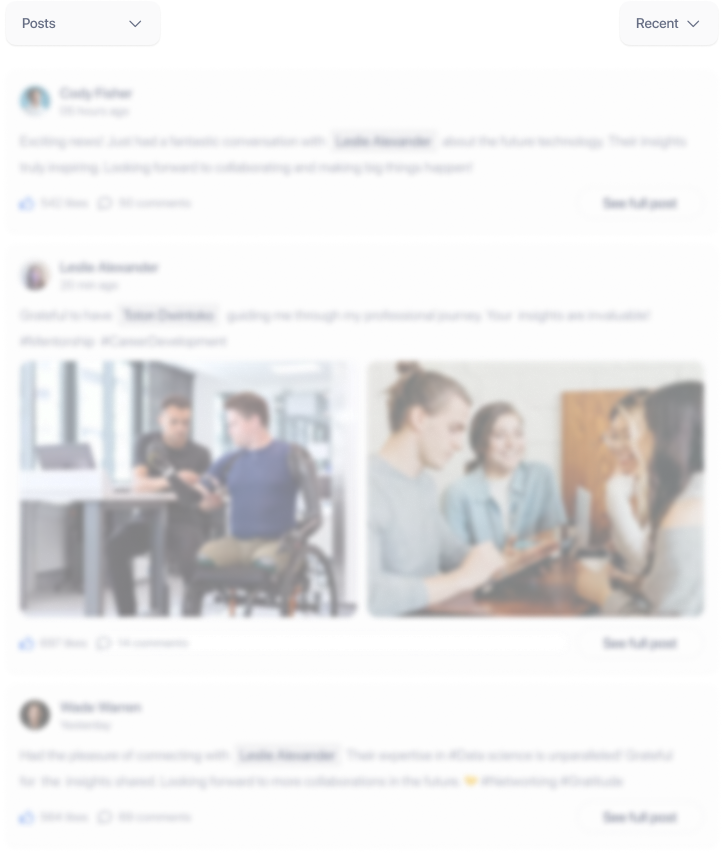