Andrei Cular
Tooling & Prototype Manager at Intrepid Powerboats- Claim this Profile
Click to upgrade to our gold package
for the full feature experience.
-
English -
Topline Score
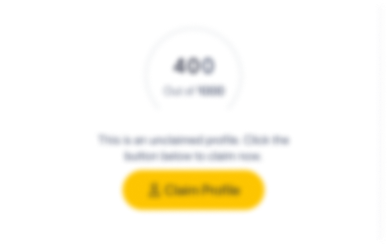
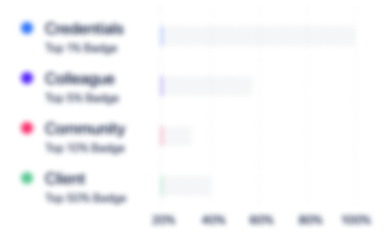
Bio


Credentials
-
USCG OUPV
USCG Merchant Marine Captain - Near Coastal
Experience
-
Intrepid Powerboats
-
United States
-
Maritime Transportation
-
1 - 100 Employee
-
Tooling & Prototype Manager
-
Mar 2018 - Present
-
-
-
ACME Engineering / Odyssey Boat Works
-
Matlacha FL
-
President
-
Jan 2004 - Present
Engineering design and prototype Boat repair and modification New boat construction Composite tooling Engineering design and prototype Boat repair and modification New boat construction Composite tooling
-
-
-
Fort myers travel
-
Fort Myers, Florida Area
-
Co Owner
-
Jan 2000 - Present
Accounting, IT support, Senior transporter Accounting, IT support, Senior transporter
-
-
-
Bertram Yachts
-
Tampa/St. Petersburg, Florida Area
-
Engineer
-
Aug 2016 - Jan 2018
Do whatever needs to be done. Was first engineer at facility to startup production of 35 model. Worked on various systems and areas of facility to get it ready for production. Instructed lamination crew on first infusions of parts. Continued to support lamination on infusion and construction of parts. Provided shop “Build Book” documentation and acted as liaison between Bertram Tampa and Lyman Morse in Maine. Lead in-house engineer on design and development of 60ft model. Responsible for reviewing all tooling files before releasing to for production. Negotiated tooling contracts and over saw production of plugs/molds. Worked with lamination crew to infuse hull, stringers, and deck. Provided shop documents and support to mechanical crews to build prototype. Coordinated with vendors to specify and source material required. Started to establish in-house tooling department. Repaired 1997 PAR 5-axis router. Unit was left in un-useable condition by previous owners. Had to troubleshoot and diagnose multiple failures without the help of the manufacture. Brought Homag 3-axis online for use in creating frame kits for 60 mock-ups. Hired plug and mold builders to start developing capabilities to create and modify tooling for current production and futures projects.
-
-
-
ANDRITZ Iggesund Tools, Inc.
-
United States
-
Industrial Machinery Manufacturing
-
1 - 100 Employee
-
Production Engineer
-
Apr 2014 - Jul 2016
Responsible for overseeing $2.5m renovation and expansion of production shop. Worked with production to create work cells and start optimizing processes. Setup a new work cell for metallic powder hard coating process utilizing an industrial robot and high temperature industrial furnaces. The new process reduced the cost per plate by almost $500 over previous process. Optimized and induction brazing process where carbide cutting tips were joined to a steel base to be used in de-barking machines. The optimization and de-bugging of the process took a product with an 80% field failure rate to just 1%. Created a set of documentation standards for all processes in the production shop. Have started to document and debug all process in production. The end goal of the documentation project is that any employee with minimal one on one training can produce quality products at any work cell by following the manual. Relocated production equipment for production of Pyramo Debarking tips from Sweden to Oldsmar. Coordinated transfers as well as training of production staff. Production started one week ahead of schedule and was under budget. Began implementing Lean manufacturing practices.
-
-
-
Intrepid Powerboats
-
United States
-
Maritime Transportation
-
1 - 100 Employee
-
CNC Manager
-
Apr 2011 - Apr 2014
Responsible for the daily operations of the CNC department which includes 7 employees, 3 5-axis routers (Motion Master, Bulleri, CIS Quintax), 2 3-axis routers (Phoenix, Thermwood), and an Eastman fabric cutter. Responsible for all maintenance / repairs and calibration for all CNC related equipment. Work with designer to develop temporary and permanent composite tooling as well as various plastic components for new models and improve existing ones. Take concepts from sketches, renderings, or hand made parts using Rhino 3D or MasterCAM develop into production ready parts. Worked closely with designer and lead engineer to design and build production friendly components. Modified existing assemblies to be more efficient throughout the process while maintaining initial design intent. Worked with production engineer and assembly management to modify stringer grid for custom one-off modifications per customer requests. Successfully implemented 5S and a modified 6 Sigma program within the CNC department to increase efficiency. Fully integrated department with Made 2 Manage ERP software. Have implemented a rapid tooling process for building custom one off and limited production tooling.
-
-
-
-
Mechanical Engineer
-
Feb 2009 - Mar 2011
Worked with project manager and customers to develop new processes and techniques to build autoclave quality parts without the cost of the autoclave. Developed low cost rapid tooling program for accelerated composite component development program with top tier aerospace company. Was key member of design / production team responsible for several cost reduction programs for the US Army and Navy. Developed method for manufacturing parts containing carbon fiber, fiberglass, spectra, and stainless steel in a moving joint. Produced one off and limited production parts out of various composites and metals. Worked with several chemists to develop environmentally and user friendly material used in various processes of composite tooling manufacturing. Developed high temperature (350F +) temporary tooling material with Sandia National Labs. Developed and implemented new processes to apply bio-based materials used in the manufacturing of composite tooling. Installed and maintained 100ft x 25ft x 10ft CMS Cronus 5-axis CNC mill. Responsible for daily operations of high speed high precision 5-axis machine center (CMS Cronus). Supported semi-production jobs on Flow 5-axis water jet, Haas tool room mill, and Haas GR 510. Worked with Unigraphics, Solidworks, and MasterCAM w/ Verisurf.
-
-
-
Marine Concepts / JRL Ventures Inc.
-
Design Services
-
1 - 100 Employee
-
Project Engineer
-
1999 - 2009
Project engineer responsible for taking back of the envelope mechanical designs through master, mold, and prototype testing stages. Was responsible for the design and fabrication of composite plugs and molds primarily for boat hulls, decks, stringer systems, and miscellaneous fixtures for boats ranging from 10’-70’, including both planning and non-planning hulls. Also responsible for the design and analysis of structural steel mold support and turning fixtures Responsible for tooling design and training customers in the use of light RTM closed molding processes. Engineering duties also included the use of a Faro 3D laser scanner to reverse engineer current products and generate CAD files; in addition to designing and prototyping a robot assistant for handicapped people. Supported operations of the CNC department as well as installation, maintenance of various CNC equipment (PAR MR 5-axis, EEW 5-axis, Motion Master 5-axis, Thermwood 3-axis with auto load, Production Automation 3-axis. Worked with Unigraphics, Rhino, MasterCAM w/ Verisurf, Vector 3D, Bobcad.
-
-
Education
-
Sea School
Captains License -
University of Phoenix
Master of Business Administration (M.B.A.), Marketing -
University of South Florida
Bachelor of Mechanical Engineering, Integrated Systems and Composite Materials
Community
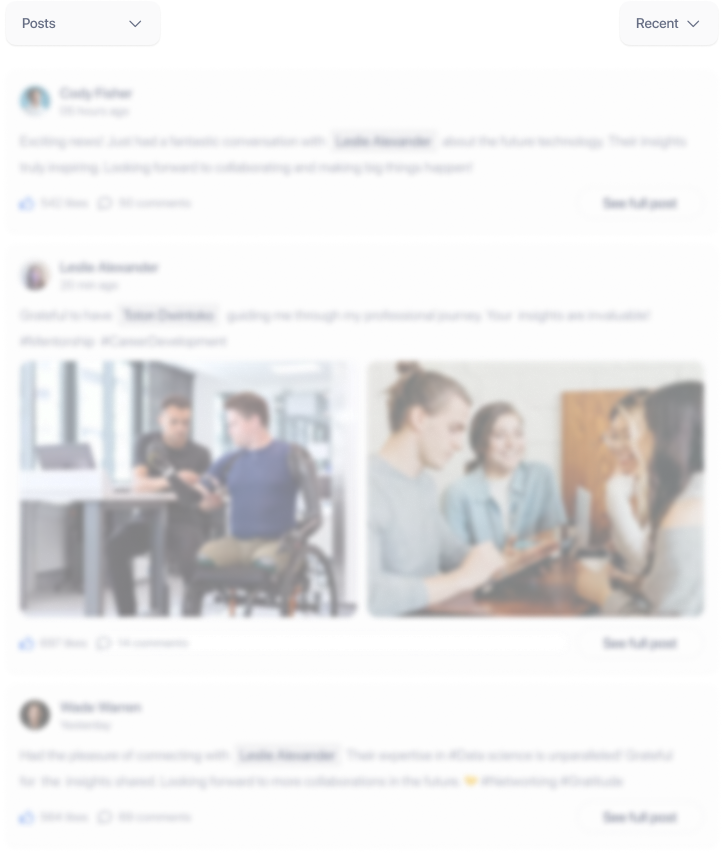