Andree Lukito
Manager at Deloitte Consulting- Claim this Profile
Click to upgrade to our gold package
for the full feature experience.
-
Indonesian -
-
English -
Topline Score
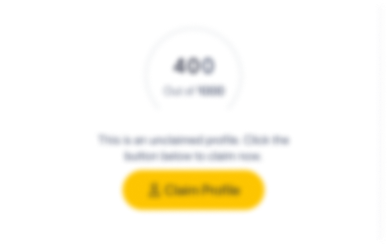
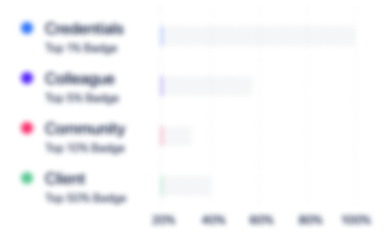
Bio

Boon Wee Phua
Andree is a highly-driven individual and manager. Constantly challenging norms and driving his team and his customers to think out of the box. A collaborator you would want on your team all the time.

Sumarno U.
Andree's working attitudes is excellent and dedicated to ensure products are delivered in compliance with project and industry code. I enjoyed working with Andree as he have the depth and broad knowledge in his area of expertise to solve technically challenging issue.

Boon Wee Phua
Andree is a highly-driven individual and manager. Constantly challenging norms and driving his team and his customers to think out of the box. A collaborator you would want on your team all the time.

Sumarno U.
Andree's working attitudes is excellent and dedicated to ensure products are delivered in compliance with project and industry code. I enjoyed working with Andree as he have the depth and broad knowledge in his area of expertise to solve technically challenging issue.

Boon Wee Phua
Andree is a highly-driven individual and manager. Constantly challenging norms and driving his team and his customers to think out of the box. A collaborator you would want on your team all the time.

Sumarno U.
Andree's working attitudes is excellent and dedicated to ensure products are delivered in compliance with project and industry code. I enjoyed working with Andree as he have the depth and broad knowledge in his area of expertise to solve technically challenging issue.

Boon Wee Phua
Andree is a highly-driven individual and manager. Constantly challenging norms and driving his team and his customers to think out of the box. A collaborator you would want on your team all the time.

Sumarno U.
Andree's working attitudes is excellent and dedicated to ensure products are delivered in compliance with project and industry code. I enjoyed working with Andree as he have the depth and broad knowledge in his area of expertise to solve technically challenging issue.

Credentials
-
Professional Scrum Master™ I (PSM I)
Scrum.orgAug, 2021- Oct, 2024 -
Collaboration Principles and Process
LinkedInMay, 2021- Oct, 2024 -
Strategic Thinking
LinkedInMay, 2021- Oct, 2024 -
Digital Transformation
LinkedInApr, 2021- Oct, 2024 -
Economics for Business Leaders
LinkedInMar, 2021- Oct, 2024 -
Gemba Kaizen: A Commonsense Approach to Continuous Improvement (Blinkist Summary)
LinkedInFeb, 2021- Oct, 2024 -
QMS Lead Auditor ISO 9001:2015
Lloyd's Register FoundationFeb, 2017- Oct, 2024 -
Risk Assessor
Bond International Consultants Pte LtdJun, 2014- Oct, 2024 -
API Q1 practicioner
API - American Petroleum InstituteMar, 2014- Oct, 2024 -
Taproot associate
TapRooT® | System Improvements, Inc.May, 2007- Oct, 2024
Experience
-
Deloitte Consulting
-
Business Consulting and Services
-
700 & Above Employee
-
Manager
-
Jun 2021 - Present
Enthusiastic leader, team focused, client oriented mindset with consistent, robust strategical transformational implementation. Enthusiastic leader, team focused, client oriented mindset with consistent, robust strategical transformational implementation.
-
-
-
-
Leadership Coach
-
Oct 2019 - Present
Providing mentee with the guidance to think critically about her ideas and goals, while sharing key work experiences and learnings development along the way.Utilize Leadership Development curriculum, resources, and team support to discuss valuable leadership topics and opportunities for mentee growth Providing mentee with the guidance to think critically about her ideas and goals, while sharing key work experiences and learnings development along the way.Utilize Leadership Development curriculum, resources, and team support to discuss valuable leadership topics and opportunities for mentee growth
-
-
-
-
Project Quality Energy Consultant
-
Mar 2018 - Jun 2021
Appointed Technical Representatives for Research & Development, Quality and Manufacturing for a 500 personnel facility.Led the team to become the 1st manufacturing facility API certified for Packer in Indonesia. Appointed Technical Representatives for Research & Development, Quality and Manufacturing for a 500 personnel facility.Led the team to become the 1st manufacturing facility API certified for Packer in Indonesia.
-
-
-
OMS Oilfield Services
-
Singapore
-
Oil and Gas
-
1 - 100 Employee
-
Group QA Manager
-
Nov 2013 - Dec 2017
Lead, Developed & Implemented Group Quality Program in accordance to API across 11 Manufacturing locations in 7 Countries for 500 people (Singapore, Malaysia, Brunei, Thailand, Indonesia, Saudi Arabia, and Australia) with KPI of 30% reduction for Cost of Poor Quality per annum and compliance improvement of 25% per annum. Lead, Developed & Implemented Group Quality Program in accordance to API across 11 Manufacturing locations in 7 Countries for 500 people (Singapore, Malaysia, Brunei, Thailand, Indonesia, Saudi Arabia, and Australia) with KPI of 30% reduction for Cost of Poor Quality per annum and compliance improvement of 25% per annum.
-
-
-
FMC Technologies
-
Oil and Gas
-
700 & Above Employee
-
Project QA Manager
-
Jan 2012 - Nov 2013
Lead and Develop a Project Quality Stage Gates flawless execution for CHEVRON Wheatstone Project(s) valued at $525 M USD with compliance & response rate towards complaints with 90% closure within 30 days. Lead and Develop a Project Quality Stage Gates flawless execution for CHEVRON Wheatstone Project(s) valued at $525 M USD with compliance & response rate towards complaints with 90% closure within 30 days.
-
-
-
Halliburton
-
United States
-
Oil and Gas
-
700 & Above Employee
-
Supplier Quality Manager
-
Oct 2011 - Dec 2011
Business ManagementProvide Leadership through strategic business direction for the Quality DepartmentSetting and align Quality vision and strategy to meet company and regional business annual operation planDeveloping knowledge base and training for Quality personnelManage a team of professionals in various Quality functionOrganization structure that includes Quality Systems, Supplier Quality, Process Quality, Quality Engineering, and Customer AuditsSupplier Quality ManagementResponsible for Regional Supply QualityEstablish and manage supplier quality performance matrixProvide Business direction and strategy on supplier developmentQuality Management System - Management RepresentativeEstablish Policies and procedures that governs the Quality Management System to API Q1, ISO/TS29001: 2010 and API 11D1 & 14L requirementsManage product quality standard certification to meet regulatory requirementsCustomer Quality ManagementPoint of contact for customer quality feedbackManage Customer audits within Asia Pacific region - Major Customer: SHELL, TOTAL, ADCO, BP, PETRONAS
-
-
Quality Manager
-
Aug 2009 - Oct 2011
Direct, Create, and control adherence to a company-wide set of quality standards.Supervise Quality Assurance staffWork with various departments to make sure standards are being upheld throughout the company.Ensure that quality control measures are strictly adhered to on tools and productsDevelop and implement quality management strategy and plans, including resource, systems, timescales, financials, to support, contribute to, and integrate within the organization’s annual business plan.Establish and implement necessary communication strategy for the improvement and awareness of quality issues across all departmentsPlan and manage departmental activities in accordance with agreed goals and objectivesReport as necessary on changes in standards and procedures (internally and externally initiated) and on performance against established standardsLiaise and cooperate with quality management and standards bodies (API, Government Departments, HSE, etc.)Liaise with customers and suppliers audits where necessaryContribute to executive policy and strategyLiaise between corporate offices and product development departmentsUtilize broad manufacturing expertise to verify/validate complex manufacturing sequencesInternal trainer for Geometric and Dimensioning Tolerance application
-
-
Quality Auditor Technical Professional
-
Feb 2007 - Sep 2009
• Perform vendor audits/assessments in order to improve incoming supplies,supplier performance and reduce costs• Develop, implement, monitor, and report vendor performance measures• Provide technical support to operations and manufacturing• Liaison between end Customer, Vendor, Manufacturing and Outside Inspection agencies• Interpret and develop quality plans/specifications consistent to customer specified requirements/expectations • Ensure manufacturing of quality products• Conduct and direct Quality training activities • Maintain compliance to safety policies and procedures
-
-
-
State of Wisconsin
-
United States
-
Government Administration
-
700 & Above Employee
-
Analyst / Industrial Engineering
-
Jan 2006 - Dec 2006
- Established a reference manual for CHPP workers to update their maintenance plans - Created a step-by-step procedure of inputting work requests and maintained the quality of all final products - Established a tracking system used to record the details of both the boiler uptimes and downtimes. - Established a reference manual for CHPP workers to update their maintenance plans - Created a step-by-step procedure of inputting work requests and maintained the quality of all final products - Established a tracking system used to record the details of both the boiler uptimes and downtimes.
-
-
-
-
Production Team Leader
-
Jun 2006 - Aug 2006
Developed strong leadership skills while assisting production line management for stainless steel products Designed procedural and management tools for ISO 17025 laboratory certification for calibration Developed strong leadership skills while assisting production line management for stainless steel products Designed procedural and management tools for ISO 17025 laboratory certification for calibration
-
-
-
Greenheck
-
United States
-
Industrial Machinery Manufacturing
-
700 & Above Employee
-
Industrial Engineering Co-op
-
Jun 2005 - Dec 2005
Developed assembly time standards for architechtural products to improve material resource planning and forecast of customer delivery datesImproved special design fabrication through routing allocation steps for architechtural product linesImproved production output for WD line assembly using TAKT rate board and time study. Developed assembly time standards for architechtural products to improve material resource planning and forecast of customer delivery datesImproved special design fabrication through routing allocation steps for architechtural product linesImproved production output for WD line assembly using TAKT rate board and time study.
-
-
-
-
Operation Manager
-
Jul 2003 - Aug 2003
Planned and coordinated schedules of imported cars to maintain safety stock levels.Worked with plant supervisor to identify safety and reduce work hazards Planned and coordinated schedules of imported cars to maintain safety stock levels.Worked with plant supervisor to identify safety and reduce work hazards
-
-
Education
-
Harvard Business School Online
Credential of Readiness (CORe), Business Fundamental, Pass -
University of Wisconsin-Madison
Bachelor, Industrial Engineering -
Kolese Kanisius (Canisius College)
Diploma, Social Science
Community
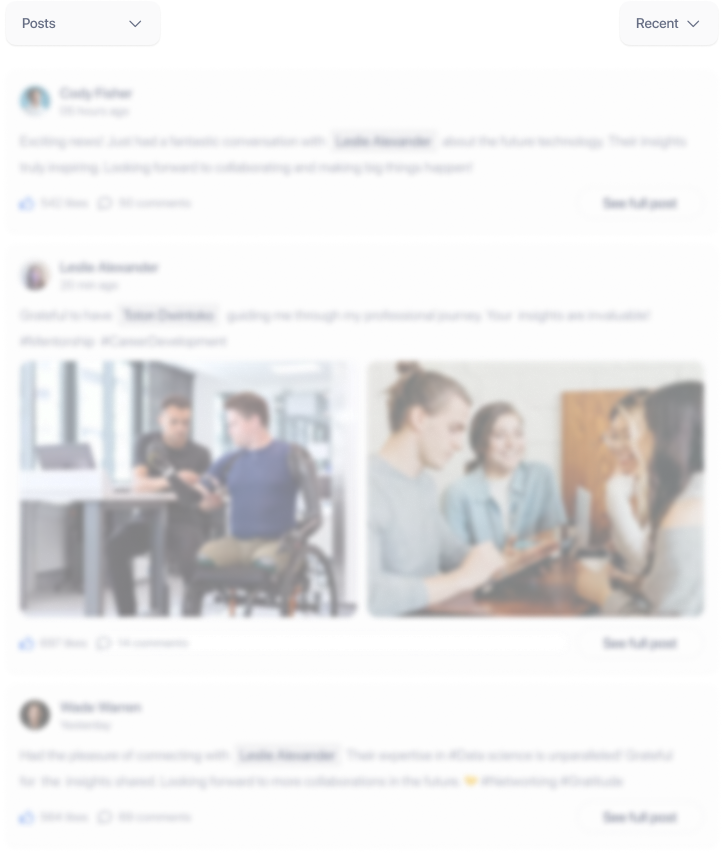