Andrea Pinto
Purchasing Manager at Filthy Food- Claim this Profile
Click to upgrade to our gold package
for the full feature experience.
Topline Score
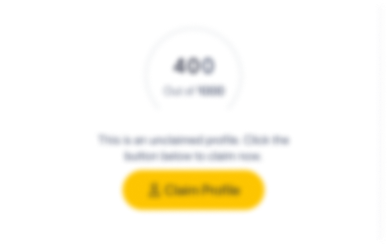
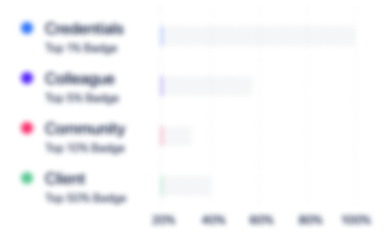
Bio


Experience
-
Filthy Food
-
United States
-
Food & Beverages
-
1 - 100 Employee
-
Purchasing Manager
-
Jun 2021 - Present
Miami, Florida, United States Raw Materials and Packaging Purchasing Manager. Filthy is the leading brand in the premium mixers and garnish space, dedicated to making the drinks people love, better. Our products are enjoyed by the home cocktail maker and experienced mixologist alike and proudly served by the best bars, restaurants, retailers, cruise ships and airlines in the world. https://filthyfood.com/
-
-
-
SUNSOF
-
United States
-
Food and Beverage Manufacturing
-
1 - 100 Employee
-
Purchasing Manager
-
Jun 2020 - Jun 2021
Miami, Florida, United States Food manufacturing facility, that provides a wide variety of handheld pies on a local, regional, and national scale. • Developed and managed sourcing strategies of Direct Materials: food ingredients and packaging. • Defined and monitor processes to drive, generate, and deliver cost/efficiency savings and working capital targets; manage $5M yearly budget. • Maximized company revenue by saving costs in raw material acquisition by 12%. • Negotiated new contracts, price and… Show more Food manufacturing facility, that provides a wide variety of handheld pies on a local, regional, and national scale. • Developed and managed sourcing strategies of Direct Materials: food ingredients and packaging. • Defined and monitor processes to drive, generate, and deliver cost/efficiency savings and working capital targets; manage $5M yearly budget. • Maximized company revenue by saving costs in raw material acquisition by 12%. • Negotiated new contracts, price and terms with suppliers. Achieving 4% saving for 2021 with new IQF products contract. • Created, developed and maintained a manual MRP system to assure all consumables were available when needed. • Managed delivery schedule and status of goods. • Controlled and managed appropriate inventory levels. • Monitored supplier performance to identify improvements and reduced lead time. Show less
-
-
-
Lennox International
-
United States
-
Manufacturing
-
700 & Above Employee
-
Export Operations Analyst
-
Sep 2018 - Apr 2020
Miami, Florida • Managed export and import logistics from China to Latin America and the United States. • Established standard operating procedures for logistics accomplishing revenue increased by 10% due to the streamline of the purchase orders, documentation and lead time. • Implemented a tracking tool for orders improving customer service. • Developed Key Performance Indicators (KPIs) to measure the firm’s international supply chain performance. Resulting in a 28% improvement in schedule… Show more • Managed export and import logistics from China to Latin America and the United States. • Established standard operating procedures for logistics accomplishing revenue increased by 10% due to the streamline of the purchase orders, documentation and lead time. • Implemented a tracking tool for orders improving customer service. • Developed Key Performance Indicators (KPIs) to measure the firm’s international supply chain performance. Resulting in a 28% improvement in schedule compliance, cost, and quality. • Analyzed data from SAP and reported performance metrics for sales representatives; on a weekly basis, including forecast, bookings, back orders, performance against quota, products and market segments. • Coordinated implementation of new demand forecast software by participating in the system development, reporting and migration of data to new system. Show less
-
-
-
Axalta
-
United States
-
Chemical Manufacturing
-
700 & Above Employee
-
Procurement Specialist Direct Material Buyer
-
Sep 2016 - Aug 2018
Valencia, Venezuela • Negotiated rates, terms and conditions with vendors. • Managed inventory of 500 SKUs for the factory plant/distribution center. • Used SAP to conduct forecasting analysis. • Reduced inventory by 5% quarterly by analyzing sales trends. • Introduced new suppliers to the company. • Helped find cost savings by seeking alternative logistics options. • Worked cross-functionally with quality department to ensure specifications were met under the company standards. • Negotiated… Show more • Negotiated rates, terms and conditions with vendors. • Managed inventory of 500 SKUs for the factory plant/distribution center. • Used SAP to conduct forecasting analysis. • Reduced inventory by 5% quarterly by analyzing sales trends. • Introduced new suppliers to the company. • Helped find cost savings by seeking alternative logistics options. • Worked cross-functionally with quality department to ensure specifications were met under the company standards. • Negotiated adjustments for replacement items that failed purchase specifications, thus ensuring Show less
-
-
-
Protinal Proagro
-
Venezuela
-
Food and Beverage Manufacturing
-
200 - 300 Employee
-
Import Purchasing Coordinator
-
Sep 2013 - Sep 2016
Valencia, Venezuela • Planned and negotiated the procurement of imported goods for 4 different food manufacturing plants/distribution centers. • Created a tracking system to improve visibility of open orders; increasing customer satisfaction by 50%. • Reduced the import cycle from 190 days to a maximum of 180 days; resulting in a cost reduction. • Received, studied and analyzed quotes and budgets according to the requisitions. • Reduced cost by implementing a management model reducing 13% of purchase… Show more • Planned and negotiated the procurement of imported goods for 4 different food manufacturing plants/distribution centers. • Created a tracking system to improve visibility of open orders; increasing customer satisfaction by 50%. • Reduced the import cycle from 190 days to a maximum of 180 days; resulting in a cost reduction. • Received, studied and analyzed quotes and budgets according to the requisitions. • Reduced cost by implementing a management model reducing 13% of purchase orders issued and 34% of items purchased. • Reduced 5% of the cost of emergency plant shutdown by decreasing the average days of pending purchase request, lead time and reduction of open orders. • Performed follow-up of dispatch for purchased goods and managed claims. • Ensured the operational continuity of poultry, incubators and frozen foods with the correct and just-in time management of purchases of supplies and equipment Show less
-
-
-
Tienda El Castillo
-
United States
-
Textile Manufacturing
-
1 - 100 Employee
-
Purchasing Analyst
-
Dec 2011 - Sep 2013
• Analyzed sales, inventory and suggested purchases, monitoring and control of quotes and budget. • Cost reduction due to negotiating prices with supplier by approximately 5%. • Managed inventory levels of the distribution center and 26 retail stores across the country. • Reported and updated sales and inventory of new emerging products. • Worked closely with the quality and design department ensuring specs were met.
-
-
Education
-
Universidad de Carabobo
Bachelor of Industrial Engineer, Industrial Engineer -
Universidad Tecnológica del Centro (UNITEC)
Master's degree, Logistics Management
Community
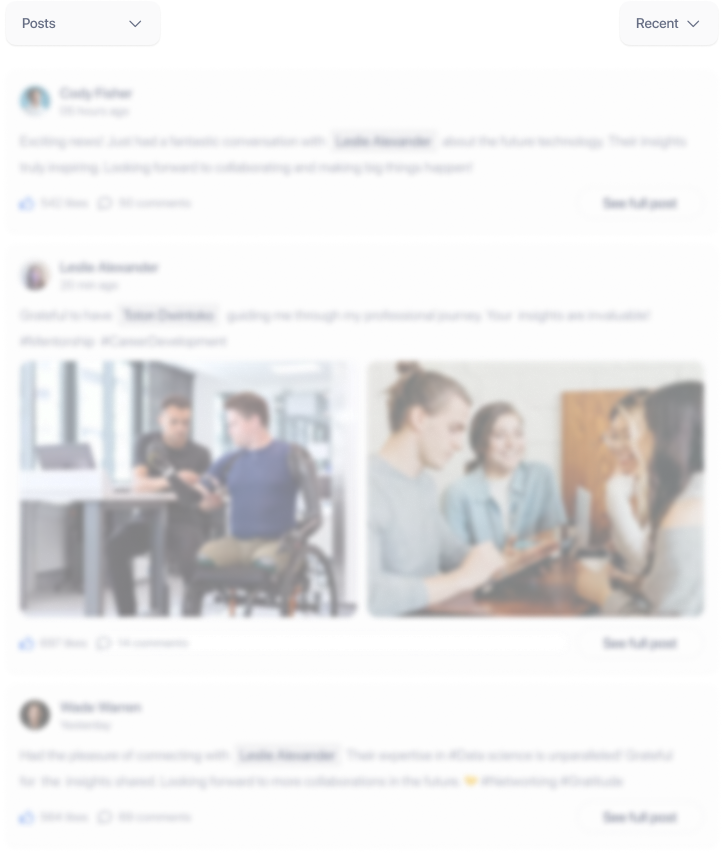