Anantha Krishna
Integrations Leader - Project Management Office at Advantus Health Partners- Claim this Profile
Click to upgrade to our gold package
for the full feature experience.
Topline Score
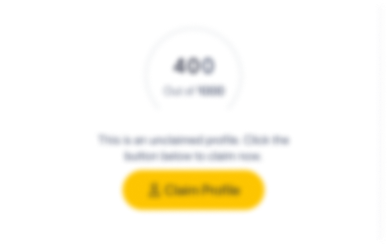
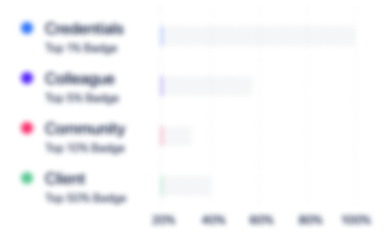
Bio


Experience
-
Advantus Health Partners
-
United States
-
Hospitals and Health Care
-
1 - 100 Employee
-
Integrations Leader - Project Management Office
-
Mar 2022 - Present
• Key leader and adviser within the Advantus Health Partners (AHP) organization. • Develop strategies that are implemented in a timely, effective manner for all relevant initiatives and projects in support of AHP and AHP client priorities • Manage and coordinate system-wide strategies and tactics tied to critical largescale projects and initiatives • Develop and manage comprehensive strategies for communications, including project plans and standing collaboratives • Key leader and adviser within the Advantus Health Partners (AHP) organization. • Develop strategies that are implemented in a timely, effective manner for all relevant initiatives and projects in support of AHP and AHP client priorities • Manage and coordinate system-wide strategies and tactics tied to critical largescale projects and initiatives • Develop and manage comprehensive strategies for communications, including project plans and standing collaboratives
-
-
-
Providence
-
Hospitals and Health Care
-
700 & Above Employee
-
Strategy Consultant - Business Process Improvement
-
Nov 2021 - Mar 2022
Resident expert in Provider/Clinician/ Caregiver onboarding Strategize and Drive end to end process improvements in the onboarding space Product ownership of tools and processes to support new strategies Resident expert in Provider/Clinician/ Caregiver onboarding Strategize and Drive end to end process improvements in the onboarding space Product ownership of tools and processes to support new strategies
-
-
-
Amazon.com
-
United States
-
Retail
-
100 - 200 Employee
-
Sr Program Manager
-
Apr 2017 - Sep 2021
• Owned global undeliverable program, delivered customer experience improvements, reduced undeliverable cost and built a weekly business review deck for undeliverable packages in NA and EU. • Owned and delivered projects in building retrofits and pilots work stream to deliver on Amazon’s sustainability goals • Developed a mid-term (3-5 yrs.) strategy for embodied carbon reduction in buildings and a roadmap to 100% renewable energy within Amazon Transportation. • Launch PM for launch of 20 temporary and 5 permanent reverse logistics operations. • On boarded 3 carriers on an automated refund system, built dashboards to measure goodness of automated refunds improving customer experience, reducing customer service traffic and cost. • Created WW transportation wasted truck policy and managed LED retrofit project for NA sortation center buildings in support of sustainability goals for transportation sustainability. • Onboarded existing tools at Heavy Bulky warehouses to process undeliverable packages reducing transportation cost by $1MM and improving COGS recovery rate of non-sort undeliverable packages by 12%. • Managed direct reports in the undeliverable program and expanded team scope and deliverables. • Supported OKC9 returns grading launch: Program responsibility spanned across system configuration, lane creation, product flow & coordinating with launch team to ensure site readiness. • Supported Transportation concessions program by evaluating ad-hoc concessions requests, deep dive requests evaluating customer experience and concessions impact. • Core launch PM for three 3PL warehouse launches delivering 4.0 M ft3 in North America. • Delivered 1.1M ft3 in capacity expansions at existing 3PL FCs as part of 3.0M ft3 mattress solve required for Prime Day 2018 and Peak 2018. • Managed vendor relationship with 3PL vendors during launch & hand off to 3PL operations. Show less
-
-
-
Markem-Imaje
-
Switzerland
-
Automation Machinery Manufacturing
-
700 & Above Employee
-
Supply Chain Manager
-
Dec 2014 - Apr 2017
• Responsible for distribution of product globally to M-I Distribution centers and the customer base • Propose optimized value chains for the product line based on Value Stream Management methodology to reach the best balance between SLA (lead time), landed cost and risk reduction. Ensure alignment with global supply chain infrastructure development strategy. • Work Package Leader for value stream 'expert' work - Design and implement the new targeted value stream • Supply chain project leader for CPM (current product maintenance) activities & PTM (product to manufacture) projects • Project/Program Management – Phase out projects, Organize project reviews for new product launces • Evaluate and maintain a balance between new and existing business in house to maintain optimal capacity • Value Chain Analysis to identify right sourcing for products based on market dynamics & geographical impact • Value Chain Management – Landed cost analysis, distribution planning, using service level agreement as an input to design the distribution infrastructure and optimize supply chain performance based on needs of the customer Show less
-
-
-
Caterpillar Inc.
-
United States
-
Machinery Manufacturing
-
700 & Above Employee
-
Supply Chain Analyst
-
May 2011 - Nov 2014
• Designed and delivered supply chain solutions by understanding key supply chain performance levers (i.e. on-time delivery, cost, inventory management, feasibility, etc.) and seek solutions to improve these metrics • Capacity expansion–Racking & bin expansion to accommodate higher volume due to new business • Supply chain and Inventory planning for service parts to improve performance (SAP-EWM, SAP SPM) • Service analysis and backorder analysis for regional parts planning /global parts demand • Evaluated Incremental Part Stocking Request and approved/denied dealer requests based on availability Show less
-
-
-
Southwire Company
-
United States
-
Appliances, Electrical, and Electronics Manufacturing
-
700 & Above Employee
-
Project Manager
-
Apr 2008 - May 2011
• Responsible for executing SCR (Southwire Continuous Rod) System contracts - Project kick off, design, manufacturing, installation, commissioning and performance demonstration onsite to ensure completion • Responsible for all deliverables of the project • Maintained project timeline and budget to ensured profitability • Co ordinated field service operations (machinery installation, start up and performance demonstration test) • Maintained the PDQ system with customer complaints and driving the resolution process. Ensured all engineering changes to resolve customer issues are incorporated in future designs • Assisted with technical presentations to prospective customers & supported sales to build global strategic alliances • Coordinated performance guarantee test at customer’s site & responsible for collecting final contract payment • Planning and tracking of field service man hours to optimize cost Show less
-
-
-
Magna International
-
Canada
-
Motor Vehicle Manufacturing
-
700 & Above Employee
-
Product Development Engineer
-
Jan 2006 - Apr 2008
• Launched programs from initial customer concept and design to achieve full production status including design feasibility, design execution, generation of drawings, DVP&R and product tuning loops • Managed tool trials from first shots until process stability with EOAT is achieved at production facility • Established boundary samples and calibrated the inspection process to achieve required quality • Designed and developed packaging solutions for product sequencing • Controlled Product Change Requests/Product Change Orders, technical and part drawing releases • Maintained Customer Scorecards weekly. Customer point of contact for engineering changes & quality issues • Maintained program information sheets, Bill of Materials (BOM), design records and PPAP binders. Updated and maintained Bill of Materials as a living document • Designed and performed process DOE’s for process optimization to achieve dimensional stability of parts Show less
-
-
-
Ventura Manufacturing
-
United States
-
Industrial Machinery Manufacturing
-
1 - 100 Employee
-
Quality Engineer
-
Dec 2004 - Dec 2005
• Lean implementation by optimizing work flow and continuous development of material handling processes • Developed Customer PPAP deliverables such as Process Flow, Q level History, PSW, AAR, Dimensional layout and control plan in accordance with the customer's requirements • Studied “Cost of Quality” by benchmarking company’s quality performance against other automotive suppliers • Developed work standardization concepts as a part of the “Lean Journey” to completely eliminate waste • Resolved corrective action requests from OEM customers (8 Discipline and 5 Why technique) • Measurement System Analysis overview, gauge design, gauge R&R’s, and dimensional layouts • Team oriented problem solving, 8 Discipline technique and corrective actions for non-conformities • Supplier development by periodic supplier performance reviews and supplier scorecards • Maintained Standard work, PFMEA and Control plans • Trained associates on supplier product approval, ISO/TS, capability studies and work instructions Show less
-
-
-
Central Michigan University
-
United States
-
Higher Education
-
700 & Above Employee
-
Research and Teaching Assistant
-
Dec 2002 - May 2004
Analyzed composite materials and lab tested various samples to classify based on manufacturability Researched concurrent engineering and process design as a simultaneous approach and measured against process design following product design in the product development cycle Studied rapid prototyping as a manufacturing method and ways to improve cycle times Analyzed composite materials and lab tested various samples to classify based on manufacturability Researched concurrent engineering and process design as a simultaneous approach and measured against process design following product design in the product development cycle Studied rapid prototyping as a manufacturing method and ways to improve cycle times
-
-
-
Convergys
-
United States
-
Outsourcing and Offshoring Consulting
-
700 & Above Employee
-
Sales Associate
-
Dec 2001 - Aug 2002
-
-
Education
-
Central Michigan University
Master's degree, Engineering/Industrial Management -
Bangalore University
Bachelor of Science, Industrial and Production Engineering
Community
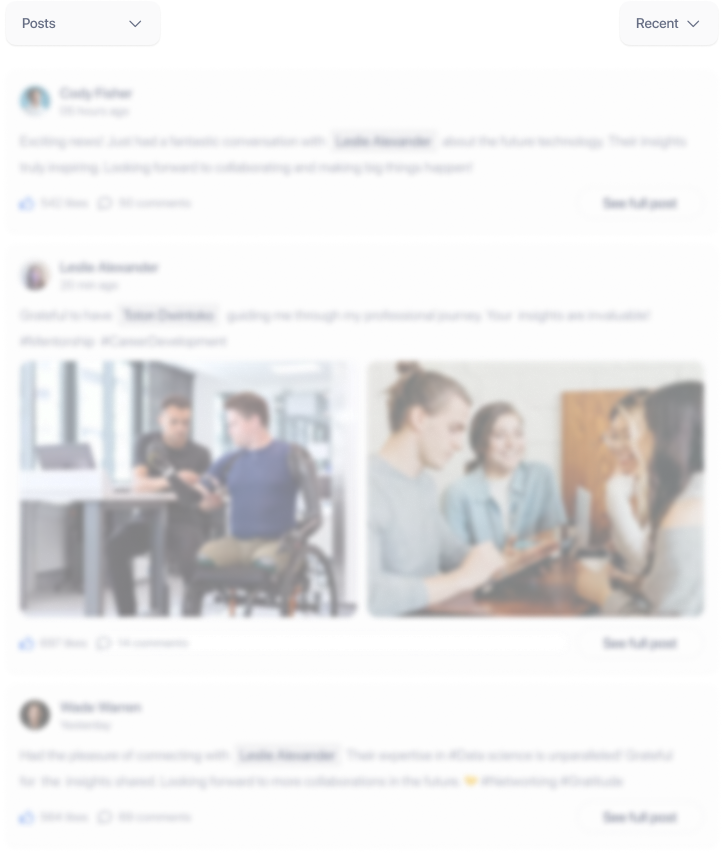