Amr Safwat
Project Control Manager at Contrasteel (HADID CO. FOR INDUSTRY ,TRADING AND CONTRACTING- S.A.E)- Claim this Profile
Click to upgrade to our gold package
for the full feature experience.
-
Arabic Native or bilingual proficiency
-
English Full professional proficiency
Topline Score
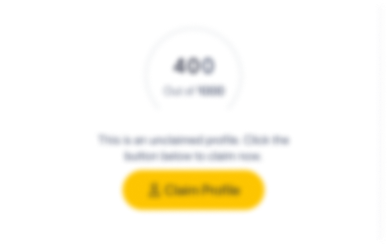
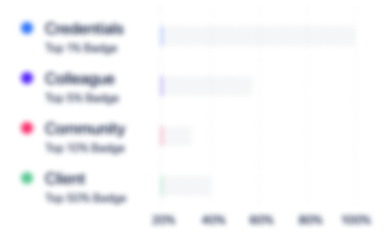
Bio

Ahmed Ihab Ismail
Amr worked with me in two projects and he showed full understanding about all project management requirements. He based his knowledge on his professional projects planning skills that allows him to have an outlook view on the project progress and identify the critical jobs to get all tools for controlling actions when needed. He is mastering MS Projects and Primavera 7 and many other tools for managing large size projects. He works with the team and contributes sincerely to the success of the project I recommend Amr strongly to take a lead position in any organization or project team.

Guenter Schmucker
Reccommendation I had the pleasuer of having Amr Safwat on my Engineers team in operation a large cement plant, He was responsible planning and scheduling any maintenance task in the mechanical department of our O&M operation. He discharged his duties with determination, competence and the required confidence successfully to achieve all set targets at any given time. I highly recommend Amr Saftwat to any employer who is looking for mature, professional and 100% reliable manager. He also possesses an outstanding social competence and has to ability to solve tensions (problems) among the staff. He wil be an masjor asset to any management team not only to O&M project in Cement Plants. I wish him all the best for his future.

Ahmed Ihab Ismail
Amr worked with me in two projects and he showed full understanding about all project management requirements. He based his knowledge on his professional projects planning skills that allows him to have an outlook view on the project progress and identify the critical jobs to get all tools for controlling actions when needed. He is mastering MS Projects and Primavera 7 and many other tools for managing large size projects. He works with the team and contributes sincerely to the success of the project I recommend Amr strongly to take a lead position in any organization or project team.

Guenter Schmucker
Reccommendation I had the pleasuer of having Amr Safwat on my Engineers team in operation a large cement plant, He was responsible planning and scheduling any maintenance task in the mechanical department of our O&M operation. He discharged his duties with determination, competence and the required confidence successfully to achieve all set targets at any given time. I highly recommend Amr Saftwat to any employer who is looking for mature, professional and 100% reliable manager. He also possesses an outstanding social competence and has to ability to solve tensions (problems) among the staff. He wil be an masjor asset to any management team not only to O&M project in Cement Plants. I wish him all the best for his future.

Ahmed Ihab Ismail
Amr worked with me in two projects and he showed full understanding about all project management requirements. He based his knowledge on his professional projects planning skills that allows him to have an outlook view on the project progress and identify the critical jobs to get all tools for controlling actions when needed. He is mastering MS Projects and Primavera 7 and many other tools for managing large size projects. He works with the team and contributes sincerely to the success of the project I recommend Amr strongly to take a lead position in any organization or project team.

Guenter Schmucker
Reccommendation I had the pleasuer of having Amr Safwat on my Engineers team in operation a large cement plant, He was responsible planning and scheduling any maintenance task in the mechanical department of our O&M operation. He discharged his duties with determination, competence and the required confidence successfully to achieve all set targets at any given time. I highly recommend Amr Saftwat to any employer who is looking for mature, professional and 100% reliable manager. He also possesses an outstanding social competence and has to ability to solve tensions (problems) among the staff. He wil be an masjor asset to any management team not only to O&M project in Cement Plants. I wish him all the best for his future.

Ahmed Ihab Ismail
Amr worked with me in two projects and he showed full understanding about all project management requirements. He based his knowledge on his professional projects planning skills that allows him to have an outlook view on the project progress and identify the critical jobs to get all tools for controlling actions when needed. He is mastering MS Projects and Primavera 7 and many other tools for managing large size projects. He works with the team and contributes sincerely to the success of the project I recommend Amr strongly to take a lead position in any organization or project team.

Guenter Schmucker
Reccommendation I had the pleasuer of having Amr Safwat on my Engineers team in operation a large cement plant, He was responsible planning and scheduling any maintenance task in the mechanical department of our O&M operation. He discharged his duties with determination, competence and the required confidence successfully to achieve all set targets at any given time. I highly recommend Amr Saftwat to any employer who is looking for mature, professional and 100% reliable manager. He also possesses an outstanding social competence and has to ability to solve tensions (problems) among the staff. He wil be an masjor asset to any management team not only to O&M project in Cement Plants. I wish him all the best for his future.

Experience
-
Contrasteel (HADID CO. FOR INDUSTRY ,TRADING AND CONTRACTING- S.A.E)
-
Egypt
-
Construction
-
1 - 100 Employee
-
Project Control Manager
-
Jan 2022 - Present
Project planning manager for the Melt-shop Extension Project of Suez – Al EZZ Flat Steel Plant, Ain Sokhna – Suez, Egypt Responsible for: o Creating, updating, or revising the installation and commissioning schedule for the Electro-Mechanical scope linked with the civil works and local and foreign supplies. o Follow up on all the running activities and see the impact on the project schedule and put the suitable corrective actions. o Make the progress reports and highlight the risks, potential delays, and solutions proposal. o Follow up on the procurement process and material supplies. o Assist in site management, material control, and technical office. o Mechanical Installation technical assistance and follow-up. o Project activities cross-function coordination. o Commissioning activities coordination. Show less
-
-
-
Alreefsugar
-
Food and Beverage Manufacturing
-
1 - 100 Employee
-
Project Planning Manager
-
Jan 2021 - Dec 2021
o Determine and define project scope and objectives. o Identify the Work Breakdown Structure (WBS) according to the project scope. o Create projects master / detailed baseline schedules & milestones per the submitted BOQ and organized by the WBS using the Primavera P6 / MS project. o Make resources analysis and allocation on scheduled activities. o Assign a cost to the scheduled activities and make the cash flow curve/ forecasts during the life cycle of the project report. o Update the project time/cost schedule and compare the actual work performed against the baseline program and reporting variances. o Regularly review critical path, cost loading, schedule content, use of relationships and lag, constraints, and milestones. o Use Earned Value Analysis to measure the amount of work performed on the project, forecasting its completion date and final cost. o Track project costs to meet the budget. o Participate in regular project team meetings. o Updating the schedule and comparing the actual work performed against the baseline program and reporting variances. o Review vendor, sub-contractor, and consultant schedule submittals. o Maintain project risk register to ensure that risks are effectively managed to minimize their impact on the schedule, scope, and budget of projects. o Follow up on all stock movements and transactions between warehouses/store yards and workplace to be sure of the work right sequence and no delay in the project activities. o Ensure own actions comply with HSE policies and safe operating practice standards. Show less
-
-
-
BMIC Cement Plant
-
Asyut, Egypt
-
Project Planning and Inventory Control Manager
-
Jan 2017 - Dec 2020
o Make the Detailed Schedule for the new projects in the plant like the coal mill and AF System, follow up on all the project activities, and assist in mechanical installation. o Utilize ERP system to auto‐generate manufacturing work orders o Notify Sales of any schedule impacts to customers. o Coordinate/expedite manufacturing builds to ensure schedules are achieved. o Completes status reports, such as production progress, customer information, and materials inventory. o Detect issues when arise and exercises judgment within defined procedures and practices to determine appropriate action. o Developing a master schedule in consultation with management, overseeing the workflow of the production facility. o Create status and performance reports and present them to managers o Lead production planning reviews and designing business processes; facilitation in formulating recommendations to improve and support business production activities. o Participates in technical reviews and audits to verify change management is carried through phases of production. o Review the stock availability of source material and material and establish a monthly production plan for required materials with sufficient lead time. o Obtain approval from the relevant Department Manager(s) and communicate to concerned parties through e-mail. o Responsible to create process orders for the required material through SAP as per the approved monthly production plan and follow-up production status. Show less
-
-
-
FLSmidth
-
Denmark
-
Industrial Machinery Manufacturing
-
700 & Above Employee
-
Chief Planner/Shutdown Planning.
-
Jan 2011 - Dec 2016
o Enable the safe and efficient execution of shutdown asset strategies maintenance work, by detailed job preparation. o Establish standard job plans for repetitive shutdown maintenance tasks. o Ensure all improvements in the work execution process are clearly communicated and implemented. o Providing detailed job plans that ensure the safe and efficient execution of all Shutdown maintenance jobs. o Follow management of the change process if new materials are required for job completion. o Managing the work notification and work order backlog by: o Returning incomplete or poorly defined work notifications. o Reviewing backlog and planning list. o Grouping notifications together that can be planned and worked as a single order. o Coordinating with production to ensure job plans meet the timing requirements of production. o Developing or copy the work order job plan and clearly documenting required skill crafts, duration, specialty tools, and necessary equipment. o Creating purchase orders for necessary components. o Building the job plan library, including ensuring accurate plans exist for high-frequency jobs. o Continually updating job plans to ensure necessary changes or improvements are incorporated, and efficiencies are captured. Execute planning of work orders by identifying priority identifiers such as Critical equipment, Statutory Inspections, PMs, and Priority assignment. o Ensure all planning functions are completed prior to the assignment of Planned status on an order i.e., operation steps, labor assignment and estimated work, components and procured services, work instructions and other supporting documentation, system condition, maintenance activity type, execution dependencies, and relationships (must start, must finish, etc.), and total planned costs. Show less
-
-
-
ARESCO for Manufacturing and Industrial Projects
-
Egypt
-
Industrial Machinery Manufacturing
-
100 - 200 Employee
-
Project Planning Engineer
-
Jan 2007 - Dec 2010
• Create a Detailed schedule (Level 5 schedule) for the project. • Generate progress, cash flow, look ahead plan, and earned value analysis reports. • Cross-functional coordination. • Maintain risk register and event records • Create a Detailed schedule (Level 5 schedule) for the project. • Generate progress, cash flow, look ahead plan, and earned value analysis reports. • Cross-functional coordination. • Maintain risk register and event records
-
-
Education
-
Cairo University
Bachelor of Mechanical Engineering, Mechanical Engineering
Community
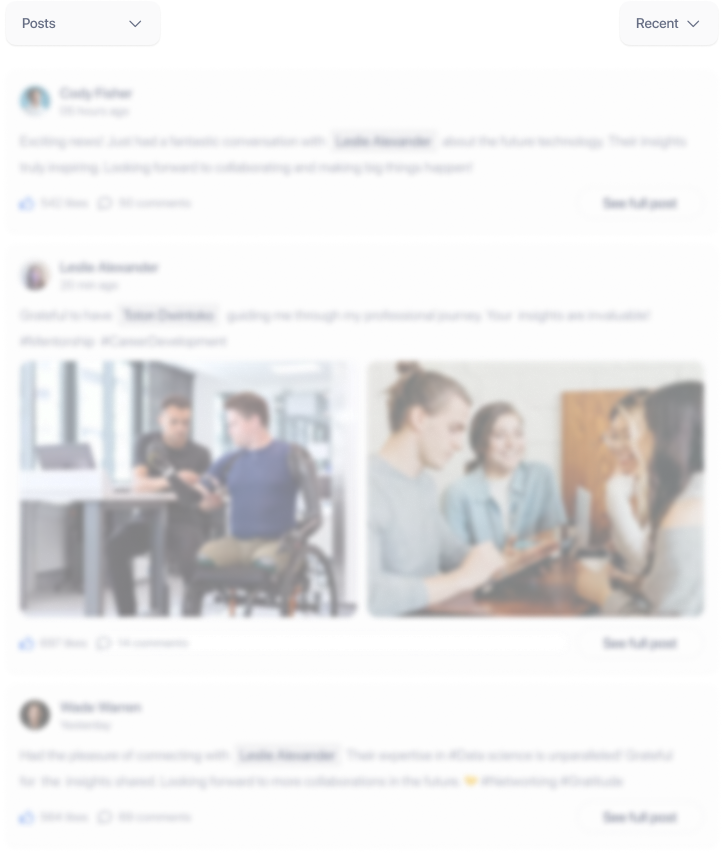